射出成形は、金型に溶融材料を注入して部品を製造する多用途の製造プロセスである。射出成形の様々な種類の中で、最も一般的なものは次の2つです。 熱可塑性射出成形 および ガスアシスト射出成形 .熱可塑性射出成形は、耐久性のある高品質な部品を効率的に生産できることから広く使用されています。一方、ガスアシスト射出成形は、構造的完全性を向上させた複雑な中空部品や軽量部品の製造に適しています。ガスアシスト射出成形は、構造的完全性を向上させた複雑な中空部品や軽量部品を製造するのに適しています。これらの工程は、自動車から消費財まで幅広い産業で不可欠であり、用途や材料の要件に応じて独自の利点を提供します。
キーポイントの説明
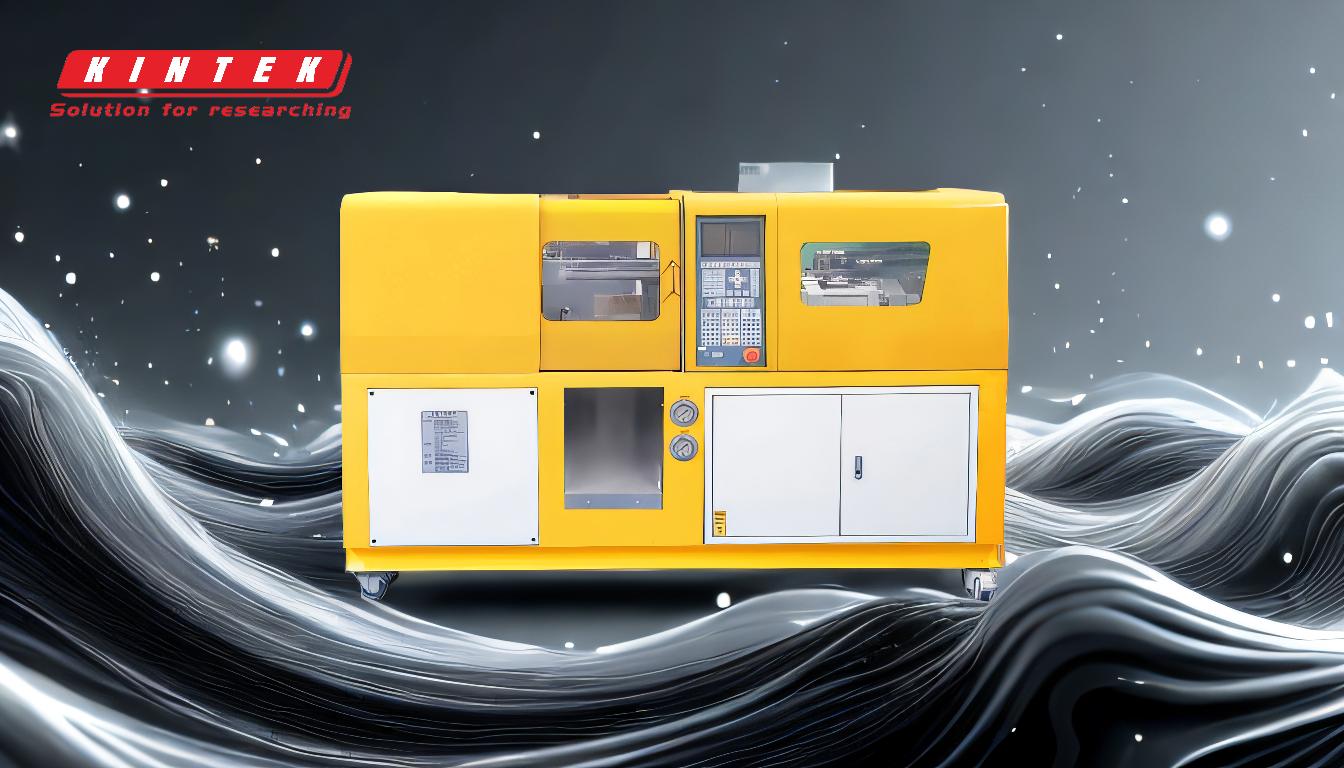
-
熱可塑性射出成形
- 定義:このプロセスでは、溶融した熱可塑性材料をプレス金型に注入する。 プレス金型 キャビティで冷却され、希望の形状に固化する。
-
主な特徴:
- 素材の多様性:ポリエチレン、ポリプロピレン、ABSなどの熱可塑性プラスチックは、大きな劣化を起こすことなく何度でも溶かして形を変えることができるため、一般的に使用されている。
- 高効率:工程は高度に自動化されており、安定した品質で大量の部品を迅速に生産することができます。
- アプリケーション:消費財、自動車部品、医療機器、包装の製造に広く使用されている。
-
利点:
- 大量生産に適したコストパフォーマンス。
- 優れた表面仕上げと寸法精度
- 熱可塑性プラスチックのリサイクル性
-
制限事項:
- 初期金型費が高くつく可能性がある。
- 溶融・冷却プロセスに耐えられる材料に限定される。
-
ガスアシスト射出成形
- 定義:このプロセスでは、溶融材料を金型に注入し、その後、加圧ガス(通常は窒素)を導入して中空部を形成したり、部品の構造を改善したりする。窒素雰囲気炉の使用 窒素雰囲気炉 ガス環境を正確に制御
-
主な特徴:
- 中空断面:ガスが特定の領域で溶融材料を置換し、軽量の中空部品を作り出す。
- 構造的完全性の向上:ガス圧により、ヒケや反りを抑え、より強く均一な部品を作ることができます。
- 用途:自動車パネル、家具、ハンドルなど、大型で複雑な部品の製造に最適。
-
利点:
- 材料使用量と部品重量を削減。
- 部品の強度と表面仕上げを向上
- ヒケや反りなどの欠陥を最小限に抑えます。
-
制限事項:
- ガス圧とタイミングを正確に制御する必要がある。
- 標準的な射出成形に比べて複雑でコストが高い。
-
2つのプロセスの比較
- 材料の使用:熱可塑性射出成形は、一般的に多くの材料を使用しますが、ガスアシスト射出成形は、中空部を形成することによって材料の消費を削減します。
- 部品の複雑さ:ガスアシスト射出成形は、内部に空隙のある複雑で軽量な部品の製造に適しています。
- コスト:熱可塑性射出成形は一般的に、よりシンプルで大量生産が可能な部品に適しており、ガスアシスト射出成形は軽量で強度の高い部品を必要とする特殊な用途に適しています。
-
適切なプロセスの選択
- 標準部品の 標準部品の大量生産 熱可塑性射出成形は、その効率性と操作の複雑さの低さから、しばしば最良の選択となります。
- 複雑で ガスアシスト射出成形は、複雑で、軽量で、構造的に要求の高い部品に適しています。 ガスアシスト射出成形は、より高いコストと複雑さにもかかわらず、優れた結果を提供します。
この2つの一般的な射出成形プロセスを理解することで、メーカーは特定の要件に基づいて最適な方法を選択することができ、最適なパフォーマンス、コスト効率、および製品の品質を確保することができます。
総括表
側面 | 熱可塑性射出成形 | ガスアシスト射出成形 |
---|---|---|
材料の使用 | 材料消費量の増加 | 材料使用量の削減(中空部) |
部品の複雑さ | よりシンプルな部品 | 複雑で軽量な部品 |
コスト | 大量生産に適したコスト効率 | 高コスト、特殊用途 |
用途 | 消費財、自動車、医療機器 | 自動車パネル、家具、ハンドル |
利点 | 高効率、リサイクル性、表面仕上げ | 軽量、強度、欠陥低減 |
制限事項 | 高い初期工具費用 | 精密なガスコントロールが必要 |
適切な射出成形プロセスの選択にお困りですか? 当社の専門家に今すぐご連絡ください オーダーメイドのソリューションを