粉末冶金(P/M)は、高効率、低コスト、最小限の廃棄物など、多くの利点を提供する汎用性の高い製造プロセスである。しかし、他の製造方法と同様、課題がないわけではありません。P/M部品の最も一般的な欠陥には、射出クラック、密度のばらつき、マイクロラミネーション、焼結不良などがある。これらの欠陥は、粉末の準備、成形、焼結など、P/Mプロセスのさまざまな段階で発生する可能性があります。これらの欠陥を理解することは、P/M部品の品質を向上させ、自動車や航空宇宙産業などの重要な用途における信頼性を確保するために極めて重要である。
キーポイントの説明
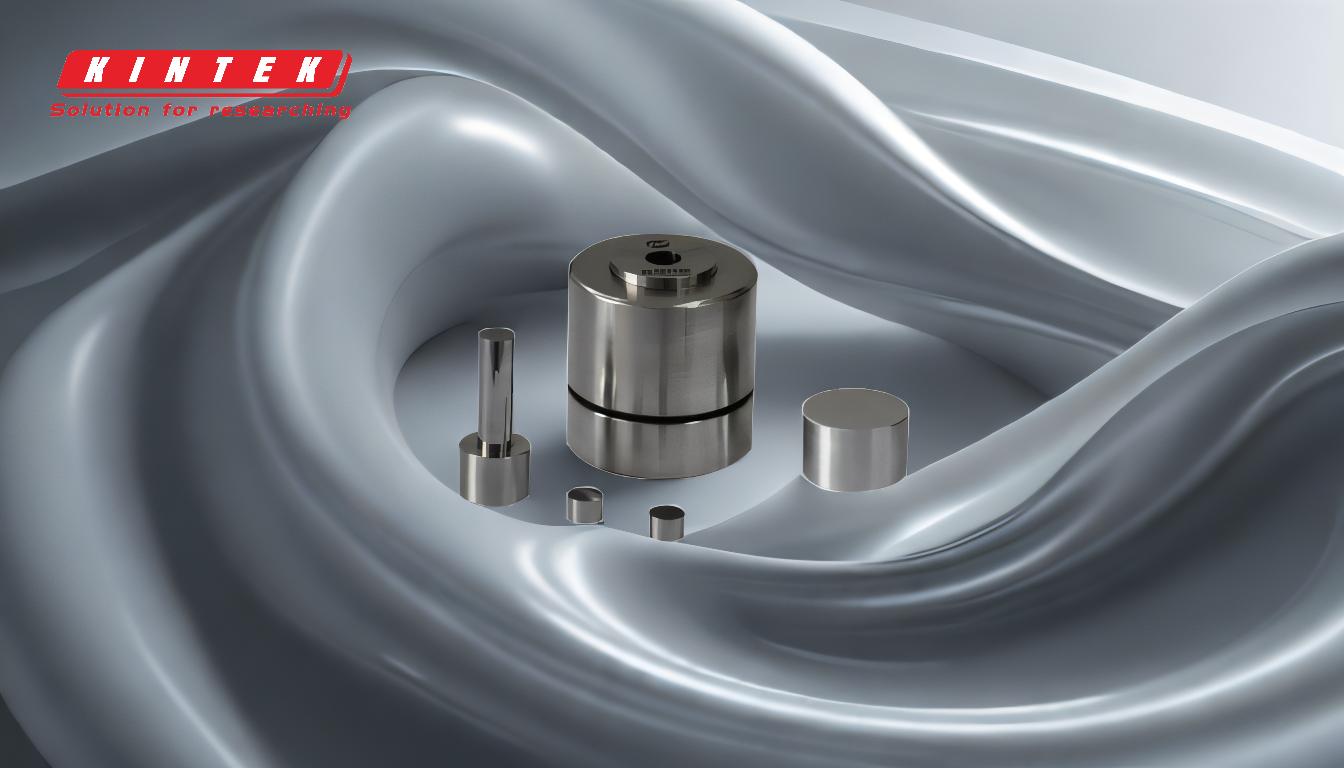
-
放出クラック:
- 原因:排出クラックは、成形された粉末部品が金型から排出される際に発生します。成形品と金型との間の摩擦が、成形プロセスからの残留応力と組み合わさって、亀裂を形成する可能性があります。
- 衝撃:これらの亀裂は、部品の構造的完全性を損ない、応力下での破損につながる可能性がある。
- 予防:適切な金型設計、潤滑、射出力の制御により、射出割れの発生を最小限に抑えることができる。
-
密度のばらつき:
- 原因:密度のばらつきは、成形工程における粉末の不均一な分布によって生じる。これは、金型への不適切な充填、不十分な押圧力、または粉末特性のばらつきが原因となることがあります。
- 衝撃:密度が均一でないと、強度や耐摩耗性などの機械的特性が部品間でばらつく可能性がある。
- 予防:パウダー分布の均一化、プレスパラメーターの最適化、高品質パウダーの使用により、より安定した密度を得ることができます。
-
マイクロラミネーション:
- 原因:マイクロラミネーションは、粉末粒子間の空隙または不完全な結合の薄い層である。成形圧力が不十分であったり、焼結条件が不適切であったりすることで発生する。
- 衝撃:これらの欠陥は応力の集中源となり、部品の疲労寿命と全体的な耐久性を低下させます。
- 予防:マイクロラミネーションを最小限に抑えるには、適切な成形圧力、適切な焼結温度、時間が不可欠である。
-
焼結不良:
- 原因:焼結不良は、焼結工程での加熱が不十分であることに起因する。これは、不適切な温度、不十分な時間、不適切な雰囲気制御によるものである。
- 影響:焼結が不十分だと粒子間の結合が弱くなり、その結果、強度が低く機械的特性の低い部品ができる。
- 予防:焼結温度、時間、雰囲気を正確に制御することは、適切な接合を確保し、望ましい機械的特性を達成するために極めて重要である。
-
プロセスのばらつきと欠陥への影響:
- 従来の方法:従来のP/Mプロセスは、粉末分布や金型設計の制限により、密度のばらつきや射出クラックなどの欠陥が発生しやすい。
- 射出成形:この方法は、密度のばらつきを抑えることができるが、適切に管理されないと、反りや不完全な充填など、他の欠陥を引き起こす可能性がある。
- 静水圧プレス:この技術は、より均一な密度の部品を製造することができ、密度に関連する欠陥の可能性を低減します。
- 金属積層造形:最新の進歩であるこの方法は、精密なレイヤーバイレイヤー構造による欠陥低減の可能性を提供しますが、気孔率や残留応力などの新たな課題も生じます。
-
粉末冶金の利点:
- このような欠点があるにもかかわらず、P/Mは複雑な形状を高精度で製造でき、材料の無駄が少なく、費用対効果に優れているなど、大きな利点があります。
- このプロセスは環境に優しく、使用された材料の97%が最終製品の一部となるため、自動車や航空宇宙などの産業にとって持続可能な選択肢となっている。
結論として、粉末冶金は非常に効率的でコスト効果の高い製造プロセスであるが、高品質の部品を確実に製造するためには、一般的な欠陥を理解し、それに対処することが不可欠である。粉末の調製、成形、焼結といったP/Mプロセスの各段階を最適化することで、メーカーは欠陥を最小限に抑え、重要な用途におけるP/M部品の性能を高めることができる。
総括表
欠陥 | 原因 | 影響 | 予防 |
---|---|---|---|
射出亀裂 | 排出時の摩擦、残留応力 | 構造的完全性の低下、応力下での部品の破損 | 適切な金型設計、潤滑、制御された排出力 |
密度のばらつき | 不均一な粉末分布、不適切な金型充填、不適切なプレス | 機械的特性(強度、耐摩耗性)のばらつき | 均一な粉末分布、最適化されたプレス、高品質の粉末 |
マイクロラミネーション | 成形圧力不足、不適切な焼結条件 | 応力集中、疲労寿命の低下、耐久性の低下 | 適切な成形圧力、適切な焼結温度と時間 |
焼結不良 | 不適切な温度、不十分な時間、不適切な雰囲気制御 | 粒子間の結合が弱い、強度が低い、機械的特性が低い | 焼結温度、時間、雰囲気の正確な制御 |
粉末冶金プロセスの最適化にお困りですか? 当社の専門家に今すぐご連絡ください オーダーメイドのソリューションを