金属レーザー焼結(MLS)は、高出力レーザーを使用して金属粉末粒子を層ごとに融合させ、固体の3次元物体を作成する高度な積層造形プロセスである。このプロセスは、高い精度と材料効率で複雑な形状を製造できることから、航空宇宙、自動車、医療機器などの産業で広く使用されている。このプロセスには、粉末の準備、レーザー焼結、後処理など、いくつかの重要な工程があり、それぞれが最終製品の望ましい特性を実現する上で重要な役割を果たす。
キーポイントの説明
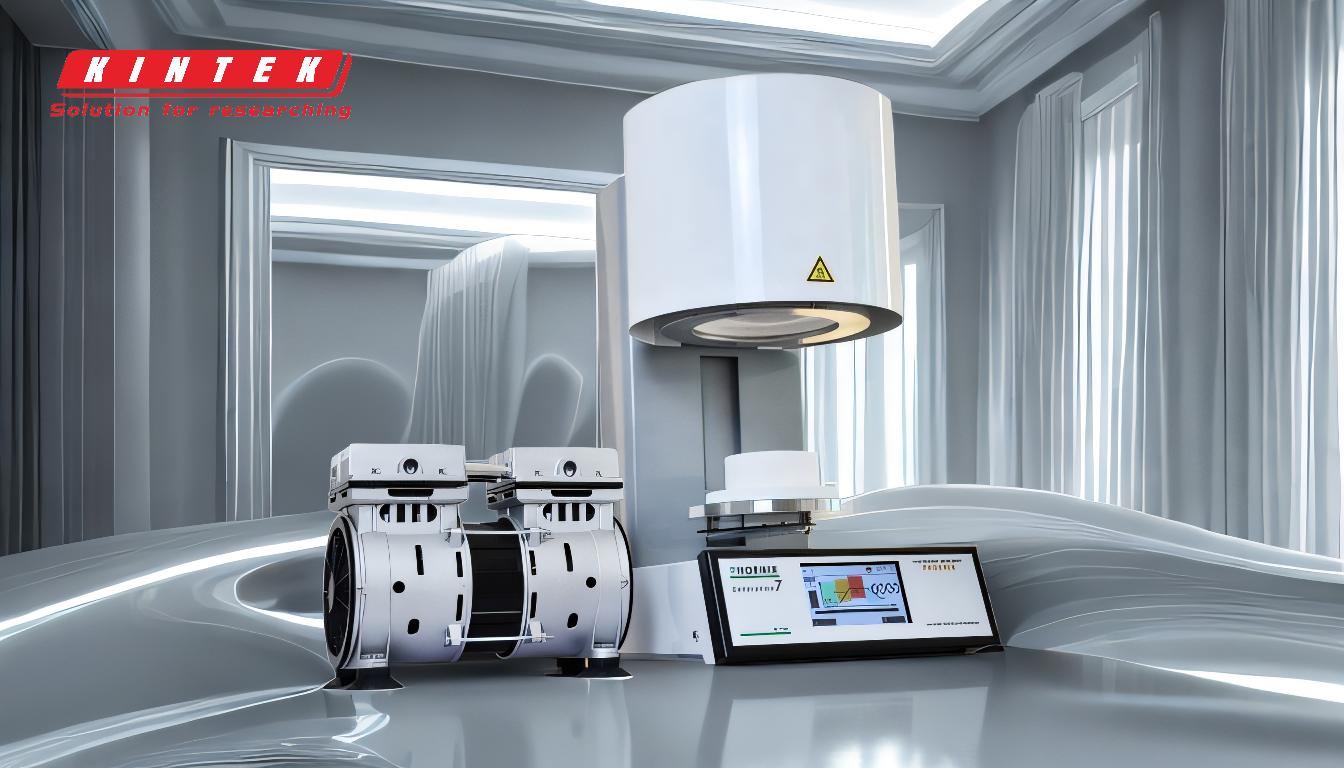
-
パウダーの準備:
- 素材の選択:プロセスは、適切な金属粉末を選択することから始まる。一般的な材料には、チタン、アルミニウム、ステンレス鋼、ニッケル基合金などがある。材料の選択は、強度、耐久性、耐熱性など、最終製品に求められる特性によって決まります。
- パウダーブレンド:金属粉末は、特定の特性を向上させるために、合金元素や添加剤とブレンドされることが多い。このブレンドにより、均一な混合物が得られ、均一な最終製品が得られます。
-
レーザー焼結プロセス:
- レイヤーデポジション:金属粉末の薄い層は、ビルドプラットフォーム上に均一に広げられる。この層の厚さは、要求される解像度や特定の用途にもよりますが、通常20~100ミクロンの範囲です。
- レーザー溶融:高出力のレーザービームをパウダーベッドに照射し、パーツのデジタル3Dモデルに従ってパウダー粒子を選択的に溶融します。レーザーのエネルギーは、金属粒子が過度の熱変形を起こすことなく融合するように正確に制御されます。
- レイヤーボンディング:各層が焼結するにつれて、その下にある以前の焼結層と結合する。この層ごとのアプローチにより、従来の製造方法では困難または不可能であった複雑な形状や内部構造を作り出すことができる。
-
制御された雰囲気:
- 不活性ガス環境:焼結プロセスは通常、アルゴンや窒素のような不活性ガスで満たされた制御された雰囲気の中で行われます。この環境は金属の酸化や汚染を防ぎ、最終製品の完全性と品質を保証します。
- 温度管理:焼結炉は正確な温度、通常は金属の融点ぎりぎりの温度を維持し、完全に溶融させることなく粒子間の原子拡散と結合を促進する。
-
後処理:
- 余分な粉の除去:焼結プロセスが完了した後、レーザーで溶融されなかった余分な粉末が取り除かれます。この粉末は多くの場合、リサイクルされ、その後の造形に再利用される。
- 熱処理:焼結部品は、材料と所望の特性に応じて、その機械的特性を向上させるために、アニールや応力除去などの熱処理工程を追加することができます。
- 表面仕上げ:最終工程では、機械加工、研磨、コーティングなどの表面仕上げ加工を行い、所望の表面品質と寸法精度を達成することが多い。
-
利点と用途:
- 複雑幾何学:MLSは、従来の製造方法では実現不可能な、複雑な内部構造や複雑なディテールを持つパーツの製造を可能にします。
- 材料効率:パーツを作るのに必要な量のパウダーしか使用しないため、無駄を最小限に抑えることができます。
- カスタマイズとプロトタイピング:MLSは、ラピッドプロトタイピングやカスタム製造に特に有効で、設計の迅速な反復やカスタマイズを可能にします。
- 産業用途:この技術は、軽量構造の航空宇宙、カスタムパーツの自動車、患者専用インプラントの医療機器など、高性能部品を必要とする産業で広く使われている。
要約すると、金属レーザー焼結は、レーザーの力を利用して金属粉末を融合させ、複雑で高性能な部品を作る多用途かつ精密な製造プロセスである。このプロセスでは、材料の入念な準備、焼結環境の精密な制御、および所望の特性と仕上げを達成するための徹底的な後処理が必要です。この技術は、従来の方法では不可能だった部品の製造を可能にし、製造業に革命をもたらし続けている。
要約表
主なステップ | 詳細 |
---|---|
パウダーの準備 | - 材料の選択(チタン、アルミニウム、ステンレス鋼など)。 |
- 均一な特性のための粉末混合 | |
レーザー焼結 | - 層堆積(20-100ミクロン)。 |
- レーザー溶融による精密溶融
- 複雑な形状のためのレイヤーボンディング。| | 制御された雰囲気
- | 不活性ガス環境(アルゴンまたは窒素)。 正確な温度制御。| |
- 後処理
- | 後処理 - 余分な粉の除去。 熱処理(焼きなまし、応力除去)。 表面仕上げ(機械加工、研磨)|
- |
- 利点 | 複雑な形状 材料効率。
ラピッドプロトタイピングとカスタマイズ。| | アプリケーション