導入
目次
冷間静水圧プレス (CIP) は、セラミック製造の分野に多くの利点をもたらす魅力的なプロセスです。このプロセスを理解することで、ビジネス運営をどのように改善できるかについて貴重な洞察を得ることができます。 CIP では、高圧ポンプを使用してセラミック材料に等方性の均一な圧力を生成します。結果として生じる均一な圧力分布により、最終製品の密度と高強度が向上します。このブログ投稿では、高品質のセラミック製品の製造を求める企業にとって理想的な選択肢となる CIP のプロセスと利点、およびそのコスト効率について探っていきます。
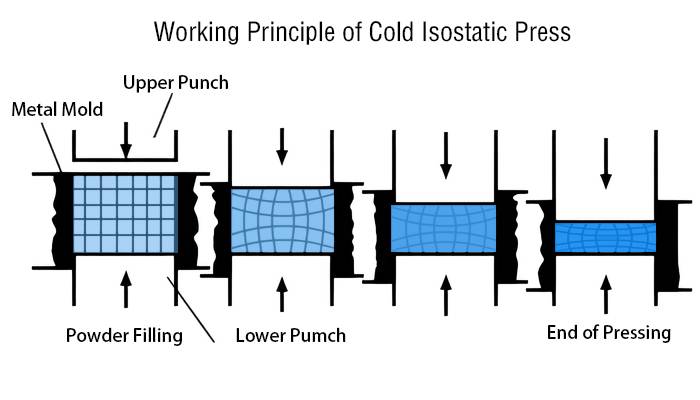
冷間静水圧プレスの説明
静水圧プレス (CIP) のプロセスを理解する
冷間静水圧プレス (CIP) は、粉末をエラストマー型に封入して圧縮する材料の加工方法です。このプロセスは、密閉された流体内に加えられた圧力が大きさを変えることなく全方向に伝達されるというパスカルの法則に基づいています。
流体または気体によって生成される静圧の役割
CIP 中に、金型に圧力を加える媒体として使用される油や水などの流体または気体によって静圧が発生します。圧力が材料全体に均等に分散されるため、歪みが軽減され、精度が向上し、空気の巻き込みや空隙のリスクが最小限に抑えられます。

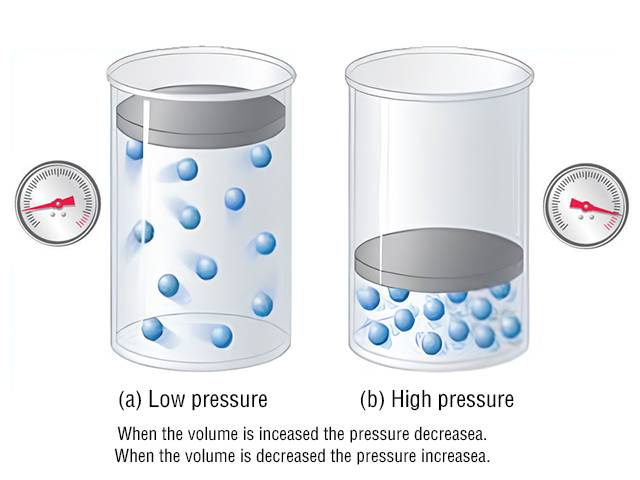
プロセスでの高圧ポンプの使用
CIP に必要な圧力を実現するには、高圧ポンプを使用して必要な流体圧力を生成します。このポンプは、特定の用途に応じて、通常 60,000 ポンド/平方インチ (400 MPa) から 150,000 ポンド/平方インチ (1000 MPa) の範囲の圧力を加えます。
プレス時に等方性の均一な圧力が得られる
CIP 中に流体圧力を加えると、圧力が材料全体の全方向に均一に伝達されます。これにより等方性の均一な圧力が得られ、プロセスの最後に非常に緻密な固体を得るのに役立ちます。
CIP は、プラスチック、グラファイト、粉末冶金、セラミック、スパッタリング ターゲットなど、さまざまな材料に使用できる多用途の方法です。医療、航空宇宙、自動車などの業界で、精度と強度が向上した部品を製造するために広く利用されています。
冷間静水圧プレスは、粉末をさまざまなサイズや形状の部品に成形および圧縮するための効果的な技術です。流体圧力を使用することで均一性が確保され、欠陥のリスクが軽減されます。 CIP は、その多用途性と幅広い用途により、さまざまな業界で貴重なプロセスです。
静水圧プレス技術の応用例
新しい合金製品の製造
静水圧プレス技術を使用すると、従来の鋳造方法では製造が困難な新しい合金製品を製造できます。全方向から均一な圧力を加えることで、凹部や中空、細長い形状などの複雑な形状を成形することができます。均一な圧力分布により、高密度分布が得られ、最終製品の強度が向上します。さらに、静水圧プレスには、他の成形プロセスと比較して金型コストが低いという利点があります。
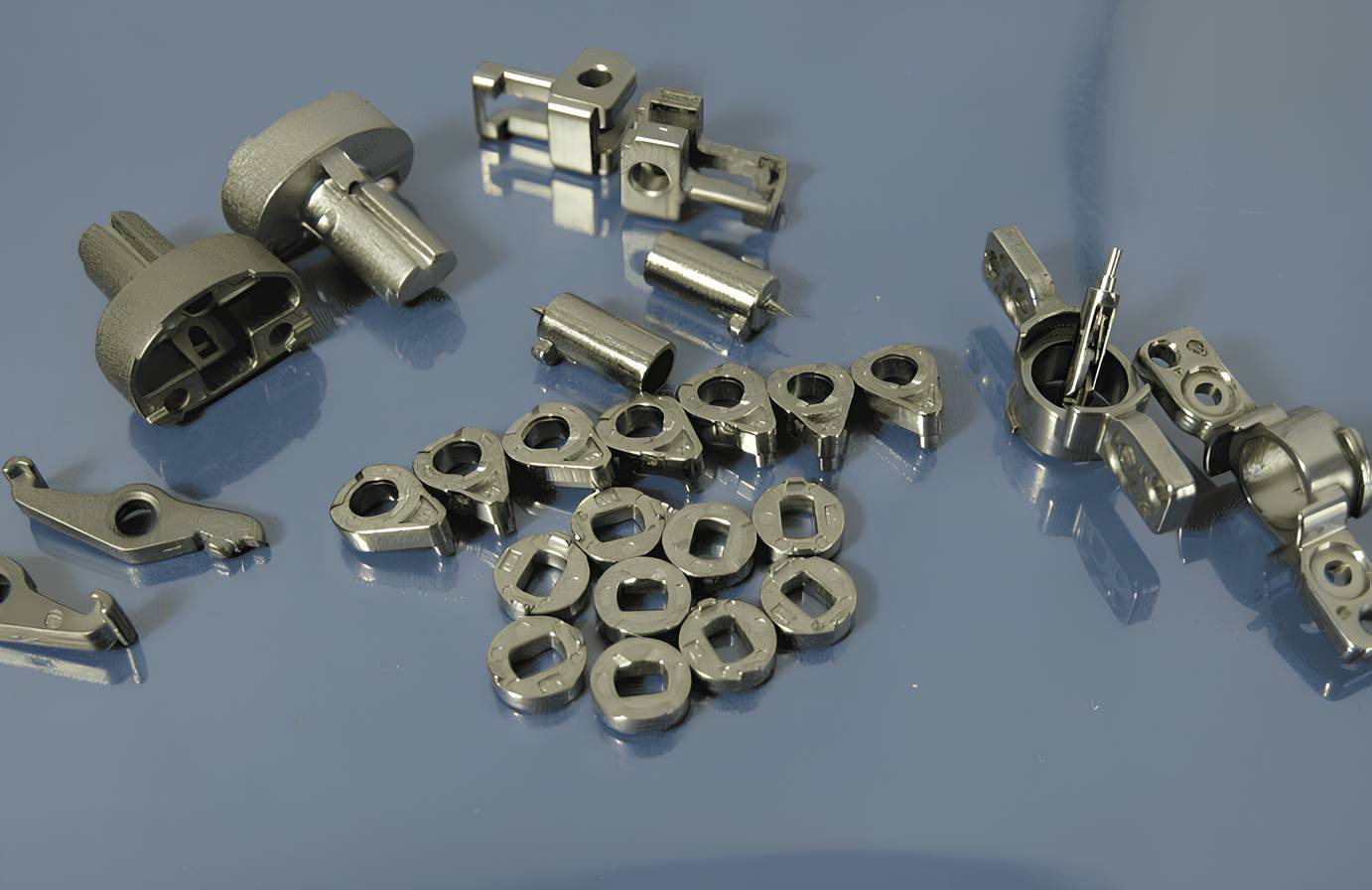
ジルコニアセラミックス、アルミナセラミックス製品の成形工程
静水圧プレスは、高い性能と強度が要求されるジルコニアセラミック製品やアルミナセラミック製品に最適な成形プロセスです。冷間静水圧プレス (CIP) としても知られるこの技術は、流体またはガスを使用して粉末またはブランクに均一な圧力を加えます。これにより、凹面や細長い形状を含む、正確な寸法や複雑な形状の部品の製造が可能になります。静水圧プレスには、摩擦損失が少なく、成形圧力が低いという利点もあります。
静水圧プレスプロセスは、医薬品、爆発物、化学薬品、食品、核燃料製造など、さまざまな業界で広く採用されています。セラミックス、金属、複合材料、プラスチック、カーボンなどの材料に適しています。静水圧プレスは、粉末を固めて鋳物の欠陥を修復するための費用対効果の高いソリューションを提供します。さらに、あらゆる形状やサイズの製品に均一な圧力を加えることができるため、セラミックや耐火物の用途に特に有利であり、コストのかかる機械加工の必要性が軽減されます。
要約すると、静水圧プレス技術は、新しい合金製品の製造やジルコニア セラミック製品やアルミナ セラミック製品の成形に多くの利点をもたらします。全方向から均一な圧力を加えられるため、高密度・高強度を実現し、複雑な形状の形成も可能です。この汎用性の高い技術はさまざまな業界で応用され、貴重な生産ツールとなっています。
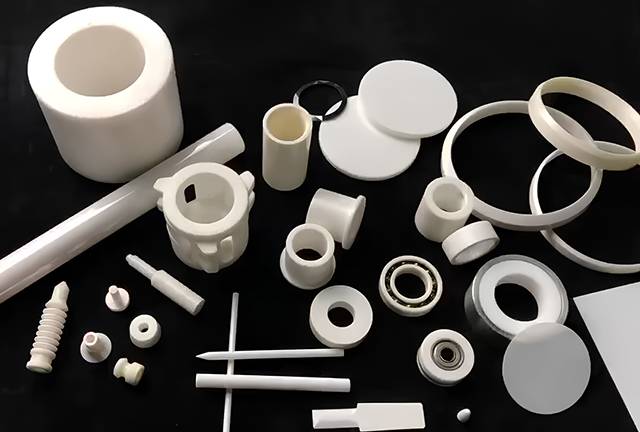
静水圧プレスの利点
静水圧プレスには、ダイ圧縮、押出、スリップキャスティング、射出成形などの他の製造方法に比べていくつかの利点があります。これらの利点には次のようなものがあります。
複雑な形状の部品もプレス可能
静水圧プレスでは、他の方法では実現が困難または不可能でさえある、複雑で複雑な形状の部品の製造が可能になります。この形状の柔軟性により、より多くのデザインの可能性と製品開発の革新が可能になります。
低摩擦損失と低成形圧力
他の成形方法とは異なり、静水圧プレスでは潤滑剤を使用する必要がありません。これにより、プレス加工時の摩擦損失が少なくなります。さらに、静水圧プレスに必要な成形圧力は他の方法に比べて低いため、材料の変形や損傷のリスクが軽減されます。
均一な圧力分布により均一な密度と高いビレット強度が得られます。
静水圧プレスでは、粉末は全方向から同じ圧力で圧縮されます。この均一な圧力分布により、得られる圧縮片の密度が均一になります。この均一な密度により、焼結または熱間静水圧プレス中に一貫した収縮が生じ、反りや歪みが最小限に抑えられます。さらに、静水圧プレスによって得られる高いビレット強度により、最終製品の耐久性と性能が保証されます。
静水圧プレスには、次のような他の利点もあります。
形状の柔軟性: 静水圧プレスでは、他の方法では実現が難しい形状や寸法の製造が可能になります。内部形状、ねじ山、スプライン、セレーション、テーパーを備えた部品の製造が可能になります。
部品サイズ: 静水圧プレスは、大規模なニアネット PM 形状から小さな MIM 部品まで、幅広い部品サイズの製造に使用できます。
低い金型コスト: 静水圧プレスは他の製造方法に比べて金型コストが低いため、短期間の生産ではより経済的です。
合金化の可能性の向上: 静水圧プレスにより、材料に偏析を引き起こすことなく合金元素を強化でき、その結果、材料特性が向上します。
リードタイムの短縮:等方圧プレスにより、プロトタイプから量産まで複雑な形状を経済的に生産できるため、鍛造や機械加工コンポーネントなどの従来の方法と比較してリードタイムが大幅に短縮されます。
材料と機械加工のコスト: 静水圧プレスで製造されるニアネットシェイプ部品は、材料と機械加工のコストを削減し、コスト効率の高い製造オプションとなります。
結論として、静水圧プレスの利点により、均一な密度と高い強度が確保され、複雑な形状の部品の多用途かつ効率的な製造方法となります。その柔軟性、コスト効率、および幅広い材料に対応できる能力により、さまざまな業界にとって魅力的な選択肢となっています。
静水圧プレスのコスト効率
金型コストの削減
静水圧プレスは、高い成形体密度を達成し、一軸プレスでは成形できない形状にアクセスするために一般的に使用される方法です。コスト効率に関して言えば、静水圧プレスの利点の 1 つは、他の方法と比較して金型コストが低いことです。
熱間静水圧プレスでは、一軸プレスよりも工具のコストとプロセスの複雑さが高くなります。ただし、静水圧プレスでは、必要に応じて、ある程度複雑な形状をエラストマー金型に加工することができます。これは、金型のコストが高くても、金型設計の柔軟性により、場合によってはコスト削減につながる可能性があることを意味します。
一方、冷間静水圧プレスでは、摩擦の影響が最小限に抑えられるため、より均一な密度を実現できます。この方法で使用される圧力容器は通常 415 MPa (60 ksi) の圧力に制限されますが、金型コストが低いため、コストを重視する企業にとって魅力的な選択肢となります。さらに、冷間静水圧プレスは自動化できますが、金型プレスに比べて生産率は低くなります。
静水圧プレスのコスト効率は、プロジェクトの特定の要件によって異なる場合があることに注意することが重要です。希望の形状、部品サイズ、生産量などの要因が全体のコストに影響します。したがって、特定のニーズに最も費用対効果の高いアプローチを決定するには、その分野の専門家に相談することをお勧めします。
全体として、静水圧プレスは、特に金型コストの削減という点で、コスト効率に優れています。静水圧プレスの独自の特性を考慮し、他の方法と比較することで、企業は情報に基づいた意思決定を行い、製造プロセスのコスト効率を最適化できます。
結論
結論として、ジルコニア セラミック冷間静水圧プレスのプロセスは、企業に多くの利点と用途を提供します。静水圧プレスのプロセスと静圧の役割を理解することで、企業は新しい合金製品を効果的に製造し、ジルコニア セラミックやアルミナ セラミック製品を成形することができます。複雑な形状の部品をプレスできること、低摩擦損失、均一な圧力分布などの静水圧プレスの利点により、均一な密度と高いビレット強度が得られます。さらに、静水圧プレスは金型コストが低くなり、コスト効率が高いことが証明されています。全体として、静水圧プレス技術を導入することで、さまざまな業界の生産性と品質を大幅に向上させることができます。
無料相談はお問い合わせください
KINTEK LAB SOLUTION の製品とサービスは、世界中のお客様に認められています。弊社スタッフがどんなご質問にも喜んで対応させていただきます。無料相談にお問い合わせいただき、製品スペシャリストにご相談いただき、アプリケーションのニーズに最適なソリューションを見つけてください。