CVD技術の紹介
定義と重要性
化学気相成長法(CVD)は極めて重要な薄膜形成技術であり、半導体製造やその他数多くの産業で重要な役割を果たしている。この技術は、様々な基板上に薄膜を精密かつ制御された形で成膜することを可能にし、電子部品、光学コーティング、保護層の製造に不可欠なものである。
半導体製造では、集積回路の性能と信頼性を高める高品質で均一な膜を作るために、CVDは不可欠である。導電性、絶縁性、光学的透明性など、特定の特性を持つ材料を成膜できるCVDは、最先端のマイクロエレクトロニクスデバイスの製造に欠かせないツールとなっている。
半導体以外にも、CVDはディスプレイ技術に幅広く応用されており、インジウム・スズ酸化物(ITO)膜や銅膜の成膜に使用され、ディスプレイ・デバイスの機能性と耐久性を高めている。さらに、CVDはレンズやミラーの光学コーティング、金属表面の防錆コーティングの製造にも利用されており、多様な分野での汎用性が実証されている。
CVDの意義は、その応用範囲の広さだけでなく、卓越した均一性、密着性、制御性を備えた膜を製造できる点にある。これらの特性により、CVDはさまざまな産業を発展させ、材料科学の革新を推進するために不可欠な技術となっている。
CVDの動作原理
化学反応プロセス
化学気相成長(CVD)プロセスにおいて、薄膜の形成は制御された化学反応に依存している。最初に、目的の薄膜の原料であるガス前駆体が反応室に導入されます。これらの前駆体は通常、気化しやすい揮発性化合物である。一旦チャンバー内に入ると、これらのガスは、特定の前駆体や所望のフィルム特性にもよるが、多くの場合、数百度から数千度の範囲の熱にさらされる。
加熱プロセスは、ガス分子が活性化エネルギーの障壁を乗り越えて反応するのに必要なエネルギーを供給するため、非常に重要である。温度が上昇すると、ガス前駆体は分解し、互いに、あるいは基板表面と反応する。この反応は通常、基材表面で起こり、そこで前駆体が吸着し、さらに分解または結合を受ける。これらの反応から生じる生成物には、基板上に堆積する所望の膜材料と、通常はガス状で系から排出される副生成物がある。
例えば、シリコン膜の蒸着では、一般的な前駆体はシラン(SiH4)である。加熱すると、シランはシリコンと水素ガスに分解する。その後、水素ガスが反応室から排気される間に、シリコン原子が基板上に堆積し、連続膜が形成される。この例は、CVDプロセスの動的な性質を示しており、温度と前駆体の流量を正確に制御することが、所望の膜質と均一性を達成するために不可欠である。
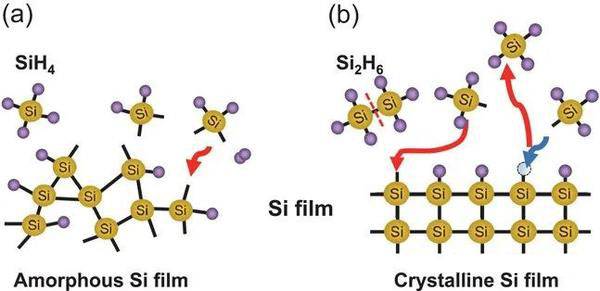
CVDにおける化学反応プロセスは、単純な分解にとどまらず、酸化、窒化、化合物材料の形成などの複雑な反応を伴うこともある。これらの反応は、酸素や窒素などの反応ガスがチャンバー内に導入され、膜の特性を変化させることで促進されることが多い。例えば、二酸化ケイ素(SiO2)膜を成膜する場合、シランを酸素と反応させて酸化膜を形成する。
反応例
化学気相成長法(CVD)では、主要な反応の1つにトリクロロシラン(SiHCl₃)の分解が含まれる。このプロセスは、特に半導体製造における薄膜形成の基本である。SiHCl₃が加熱されると、複雑な化学変化を起こす。シリコンの原料であるSiHCl₃は元素状シリコンに分解され、基板上に析出する。同時に、塩素(Cl₂)と塩酸(HCl)のガスが副産物として放出される。これらのガスは通常、反応チャンバーから排気され、成膜プロセスを妨げないようになっている。
この反応は、前駆体ガスが制御された化学反応によって固体膜に変換されるというCVDの基本原理を例証している。SiHCl₃の分解は、膜形成に必要なシリコンを供給するだけでなく、クリーンで効率的な成膜環境を維持するためのガス管理の重要性を示している。副生ガスであるCl₂とHClは、その存在が蒸着膜の品質と均一性に影響を及ぼす可能性があるため、監視と管理が極めて重要である。
CVDの分類
熱CVD
熱化学気相成長法(CVD)では、反応室内で前駆体ガスを高温(通常700℃以上)に加熱する。この高温は前駆体ガスの分解を促進するのに重要であり、前駆体ガスは基板上に堆積して薄膜を形成する。このプロセスは、膜形成に必要な化学反応を促進する熱エネルギーに依存しており、成膜された膜は、結晶性の向上、密度の向上、成膜速度の向上などの優れた特性を発揮する。
熱CVDでは、多くの場合、ガス状の反応物質は窒素のような不活性ガスによって反応室に運ばれ、制御された環境を維持するのに役立つ。高温は前駆体の分解を促進するだけでなく、低温でなければ不可能な反応を可能にする。しかし、このような高温は、フィルム内での応力形成、基板からフィルムへの元素の拡散速度の上昇、基板自体の劣化の可能性などの欠点につながる可能性がある。
利点 | 欠点 |
---|---|
成膜速度の向上 | 応力形成 |
結晶性の向上 | 拡散速度の向上 |
高い膜密度 | 基板劣化 |
熱CVDは半導体製造において特に有利であり、二酸化ケイ素、窒化ケイ素、ポリシリコンなどの薄膜をシリコンウェハー上に成膜するために使用される。これらの薄膜は、集積回路やその他の電子機器の製造に不可欠である。その利点にもかかわらず、熱CVDでは、成膜プロセスを最適化し、潜在的な欠点を軽減するために、温度と前駆体の供給速度を注意深く管理する必要がある。
プラズマエンハンストCVD (PECVD)
プラズマエンハンスト化学気相成長法(PECVD)は、化学気相成長法(CVD)の特殊な一種であり、プラズマを活用して反応速度を高め、成膜プロセスを綿密に制御する。プリカーサーガスを分解する熱エネルギーだけに依存する従来のCVD法とは異なり、PECVDではプラズマを使用して反応性ガスを活性化するため、通常100~600℃という非常に低い温度での成膜が可能になる。
PECVDでは、プラズマが触媒として働き、反応性前駆体を構成する原子や分子に分解し、それらが反応して基板表面に堆積する。このプラズマアシスト分解により、シリコン(Si)、二酸化シリコン(SiO2)、窒化シリコン、酸窒化シリコン、炭化シリコンなど、さまざまな膜を200~350℃という低い温度で成膜できる。この低い温度範囲は、高温になると基板の完全性が損なわれる可能性があるアルミニウムなど、温度に敏感な材料を使用する用途に特に有利である。
PECVDプロセスは、多くの場合、平行平板型容量結合プラズマ装置で行われる。このセットアップでは、基板は接地された電極上に配置され、プラズマは2つの電極間で生成される。PECVDで使用されるガスは、希望する膜特性によって異なり、一般的なガスとしては、シラン(SiH4)、亜酸化窒素(N2O)、アンモニア(NH3)、ヘリウム(He)、アルゴン(Ar)、三フッ化窒素(NF3)、ホスフィン(PH3)などがある。各ガスは成膜プロセスにおいて特定の役割を果たし、目的の膜の形成に寄与する。
PECVDの主な技術仕様のひとつは、540 °C以下の温度で運転できることで、幅広い基板に適している。プロセスチャンバーは通常、シランチャンバー(A+C)やTEOS(テトラエチルオルソシリケート)チャンバー(B)など複数のガスチャンバーを備え、それぞれが異なる混合ガスや成膜要件に対応できるように設計されている。このモジュール設計により、成膜プロセスの柔軟性と制御性が向上し、正確な特性を持つ高品質の膜を確実に製造することができます。
有機金属CVD (MOCVD)
有機金属化学気相成長法(MOCVD)は、金属および半導体膜の成膜用前駆体ガスとして有機金属化合物を利用する高度なエピタキシャル成長技術です。この方法は、Ⅲ-Ⅴ族およびⅡ-Ⅵ族材料を含む広範囲の化合物半導体、およびそれらの多層固溶体を成長させる能力で特に注目されている。
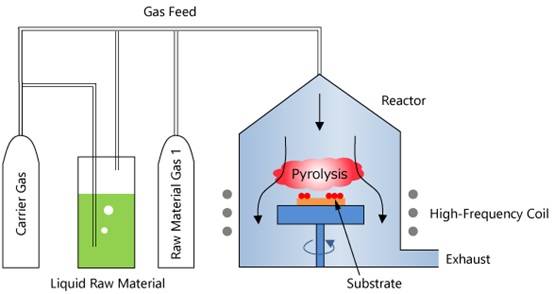
MOCVDの主な特徴
-
ソース材料:MOCVDでは、結晶成長のための主要な原料として、III族およびII族元素の有機化合物、ならびにV族およびVI族元素の水素化物を使用する。これらの材料はガス状で反応室に導入され、熱分解を経て基板上に薄い単結晶層を形成する。
-
精密制御:MOCVDの大きな利点の一つは、蒸着膜の組成とドーパント濃度を精密に制御できることである。この精度は、ガス状前駆体の流量とオン/オフのタイミングを調節することで達成され、薄層および超薄層材料を高精度で成長させることができます。
-
高速スイッチング:反応チャンバー内のガス流量が比較的速いため、複数の化合物の組成やドーパント濃度を素早く変更することができます。この迅速な切り替え機能により、メモリー効果の可能性が低くなり、急峻な界面の形成が容易になり、MOCVDはヘテロ構造、超格子、量子井戸材料の成長に理想的です。
他のエピタキシャル技術と比較した利点
他のエピタキシャル成長法と比較して、MOCVD にはいくつかの明確な利点があります:
利点 | 利点 |
---|---|
成分制御 | 前駆体が気体状態であるため、成分、ドーパント濃度、エピタキシャル層の厚さを正確に制御できます。 |
迅速な調整 | ガス流量の迅速な変更は、化合物組成の迅速な調整を可能にし、メモリー効果を低減し、界面品質を向上させます。 |
汎用性 | Ⅲ-Ⅴ系、Ⅱ-Ⅵ系を含む幅広い化合物半導体に対応し、様々な用途に高い汎用性を発揮します。 |
CVDの用途
半導体製造
半導体製造において、CVD(Chemical Vapor Deposition:化学気相成長)は、デバイスの性能と信頼性を高める高度な材料を作り出す上で極めて重要な役割を果たしています。このプロセスでは、シリサイド、窒化膜、金属膜などさまざまな膜が成膜され、それぞれが半導体産業内の特定の用途に合わせて調整されます。
シリサイド
シリサイドは、シリコンと金属の反応によって形成され、接触抵抗を低減し、半導体デバイスの効率を向上させるために重要です。シリサイドは、ゲート電極、相互接続、コンタクトパッドに一般的に使用されています。例えば、タングステンシリサイド(WSi₂)は、その低い抵抗率と熱安定性により、CMOS技術でしばしば採用されている。
窒化膜
窒化シリコン(Si₃N₄)などの窒化膜は、半導体製造において複数の役割を果たします。拡散バリアとしてドーパントや不純物の移動を防ぎ、パッシベーション層として環境要因からデバイスを保護します。さらに、窒化膜はDRAMデバイスのキャパシタ形成に不可欠であり、高キャパシタンスと低リーク電流を保証します。
金属膜
アルミニウム(Al)や銅(Cu)を含む金属膜は、集積回路内の電気信号の流れを促進する相互接続の形成に不可欠です。特に銅は、抵抗率が低く、消費電力と発熱を抑えることができるため、好まれています。これらの金属膜を成膜する際にCVDを使用することで、均一な被覆と優れた密着性が保証され、半導体デバイスの完全性と性能の維持に不可欠です。
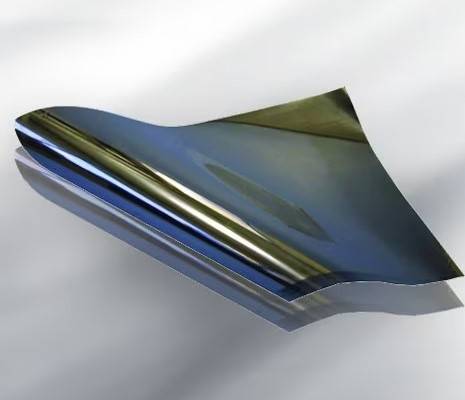
CVD技術を活用することで、半導体メーカーは成膜プロセスを正確に制御することができ、その結果、最新の電子デバイスの厳しい要件を満たす高品質の膜を得ることができます。
ディスプレイ技術
ディスプレイ技術の分野ではインジウム・スズ酸化物(ITO)膜 および銅膜 は極めて重要な役割を果たしている。これらの材料は、さまざまなディスプレイ・デバイスの製造に不可欠であり、その性能と機能を高めています。
酸化インジウムスズ(ITO)膜
ITOフィルムは、その卓越した導電性と光学的透明性で有名です。このユニークな組み合わせにより、以下のような用途に最適です:
- タッチスクリーン:タッチセンサーディスプレイに必要な導電層を提供します。
- エレクトロルミネセントパネル:ディスプレイの発光を促進する。
- 太陽電池:電気を通しながら光を通すことで、太陽電池の効率を高める。
銅薄膜
一方、銅フィルムは高い導電性と機械的強度で知られています。これらの特性は、次のような用途に活用されている:
- フレキシブル・ディスプレイ:耐久性と効率的な信号伝送を提供します。
- 高解像度ディスプレイ:信号ロスを最小限に抑え、高速データ処理を実現。
- 先進のパッケージング:複雑な電子システムの相互接続をサポートします。
ITOと銅の両フィルムは通常、以下の方法で成膜されます。化学気相成長法(CVD) この技術により、膜厚と均一性を精密に制御することができ、ディスプレイ・デバイスの最適な性能を保証します。
その他の分野
化学的気相成長(CVD)技術は、半導体製造やディスプレイ技術にとどまらず、精密で耐久性のあるコーティングを必要とする様々な産業に応用されています。顕著な用途のひとつは光学コーティングCVDは、レンズ、ミラー、その他の光学部品に薄膜を蒸着するために使用される。これらのコーティングは光の透過率を高め、反射を抑え、全体的な光学性能を向上させるため、電気通信、航空宇宙、医療用画像処理などの分野で不可欠なものとなっている。
もうひとつの重要な用途は防錆コーティング.CVD技術は、金属や合金に保護層を形成し、過酷な環境条件から保護し、耐用年数を延ばすために使用される。これは、自動車、航空宇宙、海洋工学など、材料が腐食性要素にさらされる産業において特に重要である。
用途 | 産業への影響 |
---|---|
光学コーティング | 電気通信や医療用画像処理に不可欠な光学機器を強化する。 |
防錆コーティング | 自動車、航空宇宙、海洋分野の金属を保護し、寿命を延ばす。 |
これらの用途は、CVD技術の多用途性と堅牢性を強調するものであり、現代の工業プロセスにおける要となっている。
CVDプロセスの特徴
高温要件
化学気相成長(CVD)プロセスにおける高温要件は、いくつかの理由から極めて重要である。第一に、高温は以下を実現するために不可欠である。反応速度の促進 が不可欠である。加熱されると、これらのガスは分解を受け、基板表面で化学反応が起こり、目的の薄膜が形成される。熱による運動エネルギーは、分子が反応して安定した結合を形成するのに十分なエネルギーを確保する。
さらに、高温は拡散速度の向上 を高めるのに役立つ。この拡散は、表面全体で均一な成膜を達成するために極めて重要である。適切な熱がなければ、拡散プロセスは停滞し、その結果、不均一で欠陥のある膜ができる可能性がある。
さらに、高温は不純物の除去 を除去する役割を果たす。水分や残留ガスなどの不純物は高温で除去されるため、よりクリーンな成膜プロセスが保証される。半導体デバイスに使用される高純度材料の製造において、この浄化の側面は特に重要である。
温度範囲 | 効果 |
---|---|
低温(<400) | 反応速度が遅い、拡散が制限される、膜が不均一になる可能性がある。 |
中温 (400-800°C) | 多くのCVDプロセスに最適、反応速度と拡散速度のバランスがとれている。 |
高 (>800°C) | 反応速度が速く、拡散速度が高いが、基板の温度限界を超える可能性がある。 |
真空環境
CVDプロセスは通常、真空環境下で行われる。この制御された雰囲気は、いくつかの理由から極めて重要である。第一に、真空にすることで、酸素や水蒸気など、化学反応を妨げ、蒸着膜の品質を低下させる可能性のある汚染物質の存在を最小限に抑えることができる。第二に、真空を維持することで、蒸着チャンバー内の圧力を管理することができ、ガス前駆体が最適な速度で流れ、基板表面で効率的に反応することが保証される。
真空中では、ガス分子の平均自由行程が長くなり、分子間の衝突が減少する。この衝突の減少により、ガス前駆体が基板に向かってより指向的に移動し、蒸着プロセスが強化される。さらに、真空環境は、CVDプロセスの重要なパラメーターである温度と圧力条件の制御を容易にします。
利点 | 真空環境 |
---|---|
汚染物質の低減 | 酸素と水蒸気による干渉を最小限に抑えます。 |
圧力管理 | ガス前駆体の最適なフローと反応を確保します。 |
平均自由行程の増加 | 分子の衝突を減らし、成膜を促進します。 |
温度制御 | 重要なパラメーターの制御を容易にします。 |
真空環境は単なる技術要件ではなく、CVDプロセスの効率と精度を支える基本的な側面です。真空を維持することで、メーカーは高品質で均一な膜を所望の特性で成膜することができ、CVD技術に不可欠な要素となっています。
表面処理
コーティング・プロセス、特に化学気相成長法(CVD)では、最適な密着性と膜質を確保するために、基材の表面を厳密に準備する必要があります。このステップは、蒸着された薄膜の性能と寿命に直接影響するため、非常に重要です。
有機残留物、酸化物、水分などの不純物を入念に除去しなければならない。これらの不純物は、膜形成に必要な化学反応を妨げ、ピンホールや不均一なコーティングなどの欠陥につながります。表面処理のテクニックはさまざまですが、一般的な方法には次のようなものがあります。化学洗浄,エッチングプラズマ処理プラズマ処理.
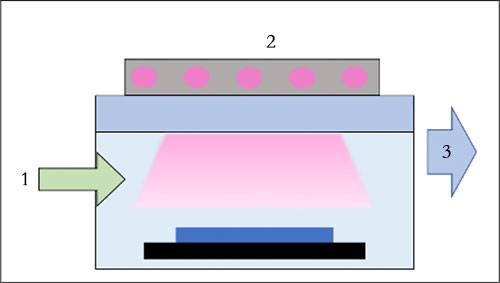
-
化学洗浄:溶剤や酸を使って有機物や無機物の汚れを溶解・除去する方法。例えば、RCA洗浄は過酸化水素と硫酸の混合液を使ってシリコンウエハーを洗浄する標準的な方法である。
-
エッチング:化学反応を利用して表面層を選択的に除去する方法。例えば、フッ化水素酸は、シリコン基板からネイティブな二酸化シリコンを除去するためによく使用されます。
-
プラズマ処理:プラズマを使って表面を活性化し、反応性を高めて残留汚染物質を除去する方法。特に有機残留物の除去や表面エネルギーの改善に効果的である。
これらの方法はいずれも、基板に汚染物質がないことを確認し、高品質の薄膜の成膜を成功させる上で重要な役割を果たす。適切な表面処理は、蒸着膜の密着性を高めるだけでなく、均一性や密度などの膜特性が要求仕様を満たすことを保証する。
基板の制限
温度と反応性の制限は、化学気相成長(CVD)プロセスで使用できる基板の範囲を大幅に制限する重要な要因です。化学反応を起こすのに必要な高温は、基板材料に熱的制約を与える可能性があり、劣化や変形なしにこのような極端な条件に耐えられるものに選択肢が限定される。例えば、ある種の有機材料や低融点金属は、高温で構造的完全性を維持できないため適さない場合がある。
さらに、前駆体ガスの反応性や、その結果生じる基板表面との化学的相互作用によって、適切な材料の選択がさらに狭まる可能性がある。基板によっては、蒸着ガスと不利に反応し、望ましくない副反応や不均一な膜の形成につながることがある。この反応性の制限により、CVDプロセスとの適合性を確保するために、基板の注意深い選択と前処理が必要となる。
カバレッジとマスキング
化学気相成長法(CVD)において、カバレッジとマスキングのプロセスは、成膜された薄膜の最終的な品質と機能を決定する重要な役割を果たします。CVDでは、基板のすべての領域が目的の材料で均一に覆われることが保証されますが、特定の領域を選択的にマスクする能力は、正確なパターンと構造を実現する上で重要な要素となります。
CVDのカバレッジは非常に効果的で、通常、基板表面全体に均一な材料が蒸着される。この均一性は、半導体製造やディスプレイ技術など、均一な膜厚が必要な用途には不可欠である。しかし、基板の特定の領域を蒸着プロセスから保護する必要がある場合には、課題が生じる。そこで登場するのがマスキング技術である。
CVDにおけるマスキングは、物理的なバリアやフォトレジスト層を使用して、特定の領域に材料が蒸着されるのを防ぐものである。この技術は一般的に効果的ですが、限界があります。例えば、マスキング・プロセスの精度は、基板の種類、パターンの複雑さ、使用する特定のCVDパラメータなどの要因に影響される可能性がある。さらに、マスキング材料自体も、成膜ガスと反応したり、CVDプロセスで一般的な高温下で劣化したりしないよう、慎重に選ぶ必要がある。
膜厚の制限
化学気相成長法(CVD)で成膜される薄膜の膜厚は、主にプロセス・パラメーターや材料の物理的状態など、いくつかの要因によって本質的に制約を受ける。これらの制限は、CVD技術の実用的な応用と限界を理解する上で非常に重要です。
プロセス・パラメーター
成膜プロセス自体は、膜厚にいくつかの制約を課す。主な要因は以下の通り:
- 温度と圧力:CVD反応に必要な高温は、蒸着膜厚を制限する可能性がある。極端な温度は、熱劣化や膜の不均一性を引き起こす可能性がある。同様に、プロセスが実施される圧力は、膜の成長速度と均一性に影響を与える可能性がある。
- 反応速度論:前駆体ガスが反応し、目的のフィルムが形成される速度も制限要因となる。反応速度が速いと、プロセスが注意深く制御されない場合、フィルムが薄くなる可能性がある。
材料の状態
前駆物質の物理的・化学的特性も重要な役割を果たします:
- 前駆体の安定性:高温での前駆体ガスの安定性は、膜厚を制限することがある。不安定な前駆体は早期に分解し、不完全な膜や不均一な膜になる可能性がある。
- 基板適合性:基板材料が蒸着条件に耐えられるかどうかは非常に重要である。基板によっては、厚膜蒸着に必要な高温や反応性に耐えられない場合がある。
このような制約は単なる制限ではなく、成膜された膜が高品質で意図された用途に適していることを保証する、プロセスに不可欠なものです。
密着性
優れた接着特性は、化学気相蒸着(CVD)技術の特徴であり、製造される薄膜の耐久性と機能性にとって極めて重要です。これらの薄膜の密着性は、基板の表面処理、前駆体ガスの化学反応性、温度や圧力などのプロセス条件など、いくつかの要因に影響されます。
例えば、適切な表面処理を行うことで、汚染物質が確実に除去され、フィルムと基板との接着性を高めるクリーンで反応性の高い表面が形成される。この工程は半導体製造において特に重要で、わずかな不純物でも性能に大きな問題を引き起こす可能性がある。
前駆体ガスの化学的性質も極めて重要な役割を果たす。前駆体ガスと基板表面との反応は強い化学結合を形成し、これがCVD膜に見られる優れた密着性の基礎となる。この化学結合メカニズムにより、過酷な使用条件下でも、成膜された膜は基板にしっかりと密着する。
CVDに必要な高温などのプロセス条件は、強力な密着性をさらに助長する。これらの高温は、膜形成に必要な化学反応を促進するだけでなく、膜材料の基板への拡散を促進し、より強固な界面を形成します。
CVD技術の利点
均一性
化学気相成長法(CVD)における均一性は、大面積の基板で一貫した膜質を保証する重要な特性です。この均一性は、温度、圧力、前駆体流量を含むプロセスパラメーターの綿密な制御によって達成されます。均一性を維持する能力は、わずかなばらつきでも最終製品に重大な性能問題をもたらす半導体製造において特に重要である。
典型的なCVDセットアップを考えてみよう。基板は、均一な前駆体ガスの流れにさらされる。ガス分子は基板表面で拡散・反応し、薄膜を形成する。これらのガスの分布を正確に管理することで、メーカーは、そのサイズに関係なく、基板全体に均一に蒸着が行われるようにすることができる。これは多くの場合、ガスの均一な分布を促進し、局所的な変動を最小限に抑える高度なリアクター設計によって促進される。
パラメータ | 均一性への影響 |
---|---|
温度 | プレカーサーの均一な分解と成膜を保証する。 |
圧力 | ガスフローと反応速度を一定に保ちます。 |
プリカーサーフロー | 反応種の濃度と分布を制御する。 |
まとめると、CVDプロセスにおける均一性は、単に望ましい特徴ではなく、高品質の薄膜を製造するための基本的な要件である。これは、大きな基板全体で一貫した結果を得るためには、精密なプロセス制御と高度なリアクター技術が重要であることを強調している。
制御性
化学気相成長(CVD)技術の際立った特徴のひとつは、成膜プロセスを高度に制御できることです。この制御性は、半導体製造やディスプレイ技術など、さまざまな用途で重要な正確な膜特性と成膜速度を達成するために不可欠です。
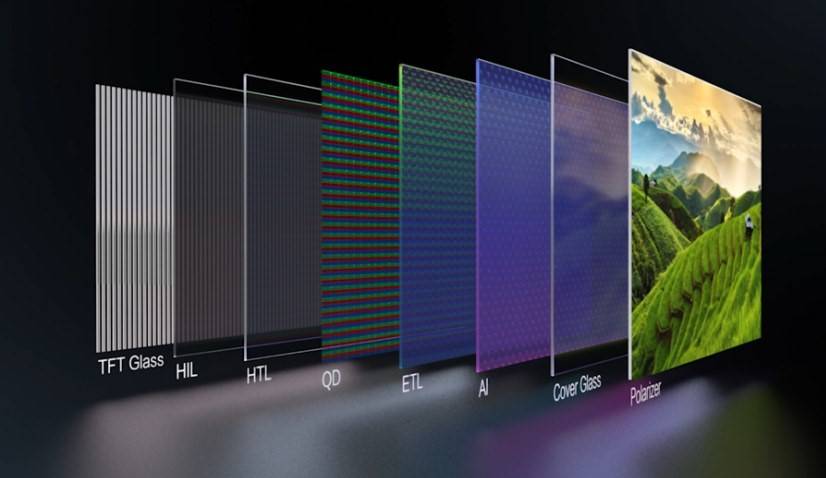
蒸着速度の制御
CVDにおける成膜速度は、いくつかのパラメータを調整することで緻密に制御することができます。以下がその例です:
- 温度:基板と前駆体ガスの温度を変えることで、化学反応の速度を微調整することができる。一般に、温度を高くすると反応速度が加速され、成膜速度が速くなる。
- 圧力:異なる圧力下で操作することで、プリカーサーガスのフローダイナミクスと基板表面への到達速度に影響を与えることができる。
- ガス流量:前駆体ガスの流量を制御することで、基板における反応物の濃度を正確に調整することができ、蒸着速度に影響を与えます。
膜特性のカスタマイズ
成膜速度だけでなく、CVDでは得られる膜の特性も幅広く制御できます。カスタマイズ可能な主な特性は以下の通りです:
- 膜厚:プロセス・パラメーターを注意深く管理することで、蒸着膜の厚さを狭い範囲で制御することができ、大きな基板でも均一性を確保することができます。
- 化学組成:異なるプリカーサーガスや混合ガスを使用することで、特定のアプリケーション要件に合わせた様々な化学組成の成膜が可能です。
- 結晶構造:温度と圧力条件は蒸着膜の結晶性に影響を与え、必要に応じてアモルファスまたは結晶構造を作成することができます。
- ストレス:膜の内部応力を制御することで、欠陥を防ぎ、膜の完全性と基板への密着性を確保することができます。
プロセスの柔軟性
CVDの制御性は、プロセス自体の柔軟性にも及んでいる。熱CVD、プラズマエンハンストCVD(PECVD)、有機金属CVD(MOCVD)など、さまざまなタイプのCVDには、独自の利点と制御メカニズムがあります。例えば、PECVDはプラズマを使用して反応速度を高め、成膜プロセスをさらに制御します。一方、MOCVDでは有機金属化合物を使用して複雑な材料を成膜することができます。
汎用性
化学気相成長(CVD)技術は、その卓越した汎用性で際立っており、さまざまな産業の要となっている。この汎用性は主に、特定の用途に合わせたさまざまな材料を蒸着できる能力に起因しています。高品質の半導体膜を作るにせよ、ディスプレイ技術を強化するにせよ、保護膜を開発するにせよ、CVDはさまざまな材料タイプや機能要件に適応できることを証明している。
材料の多様性
CVDが多様な材料を扱えることは、大きな利点です。シリコンや金属膜から、窒化物や酸化物のような複雑な化合物まで、処理できる材料の範囲は広範囲にわたります。CVDは、マイクロエレクトロニクスから先端光学に至るまで、現代の技術アプリケーションの厳しい要求を確実に満たすことができます。
アプリケーションの柔軟性
材料の多様性だけでなく、CVDの柔軟性はさまざまな分野への応用にも及んでいる。半導体製造では、シリサイド、窒化膜、金属層の形成に不可欠であり、それぞれがデバイスの性能に重要な役割を果たしている。ディスプレイ技術では、CVDは酸化インジウム・スズ(ITO)や銅膜の成膜に使われ、スクリーンの機能と耐久性を高めている。さらにCVDは、光学コーティングや防錆処理など、従来とは異なる分野でも活用されており、その汎用性の高さを物語っている。
プロセスの適応性
CVDプロセスの適応性は、その汎用性のもう一つの側面である。熱CVD、プラズマエンハンストCVD(PECVD)、有機金属CVD(MOCVD)などの技術はそれぞれ独自の利点を持ち、成膜プロセスを正確に制御することができる。この適応性により、CVDはさまざまな基板や環境条件に最適化することができ、研究者やエンジニアの手中にある汎用性の高いツールとなっている。
無料相談はお問い合わせください
KINTEK LAB SOLUTION の製品とサービスは、世界中のお客様に認められています。弊社スタッフがどんなご質問にも喜んで対応させていただきます。無料相談にお問い合わせいただき、製品スペシャリストにご相談いただき、アプリケーションのニーズに最適なソリューションを見つけてください。