薄膜蒸着における真空蒸着は、物理蒸着(PVD)プロセスのひとつで、高真空環境で材料を蒸発させ、基板上に蒸着させて薄膜を形成する。このプロセスでは、蒸発するまで原料を加熱し、蒸気が真空中を移動して基板上に凝縮します。この方法では、ガス分子の衝突や汚染がないため、高純度の薄膜が得られる。エレクトロニクス、光学、コーティングなど、精密で均一な薄膜を必要とする産業で広く使用されている。
キーポイントの説明
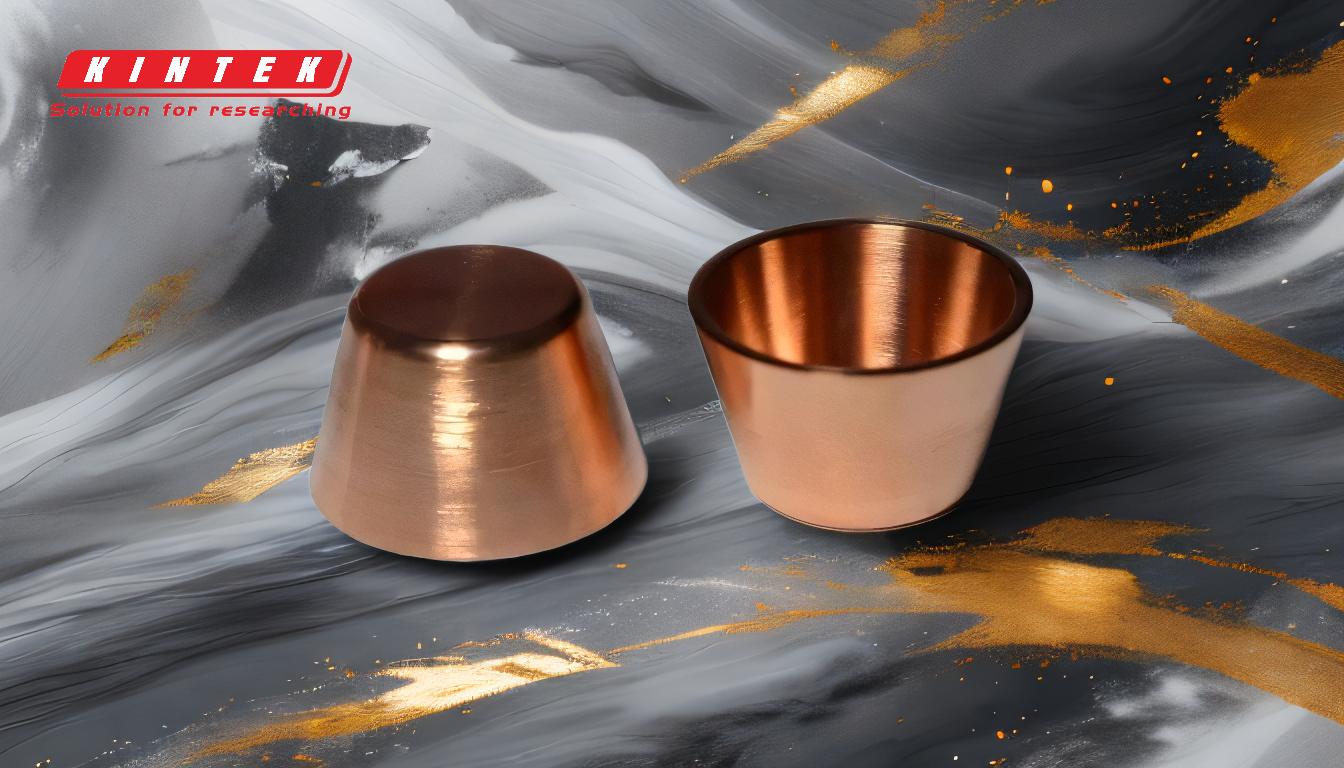
-
真空蒸発の定義と概要:
- 真空蒸着は、基板上に薄膜を蒸着するために使用されるPVD技術である。
- 高真空環境(10^-5~10^-9Torr)で行われ、ガス分子の衝突や汚染を最小限に抑える。
- このプロセスはライン・オブ・サイトであり、気化した材料はソースから基板まで直接移動する。
-
プロセスステップ:
- 蒸発:原料は蒸発するまで加熱される。これは、抵抗加熱ワイヤー、ボート、るつぼ、または電子ビームを使用して達成することができる。
- 輸送:気化した材料は真空チャンバーを通って基板に移動する。
- 凝縮:蒸気が基板上で凝縮し、固体薄膜を形成する。
-
蒸発のための熱源:
- 抵抗加熱:電気的に加熱されたワイヤーまたはルツボを使用して材料を蒸発させる。
- 電子ビーム蒸発:高エネルギーの電子ビームをソース材料に集束させて蒸発させる。
- これらの熱源は高温に耐える必要があり、蒸発させる材料よりもかなり高い融点を持つ。
-
真空蒸発の利点:
- 高純度:真空環境のためコンタミネーションがなく、高純度な膜が得られます。
- 均一な成膜:ライン・オブ・サイトにより、均一な膜厚が得られます。
- 汎用性:金属、半導体、絶縁体など幅広い材料に適しています。
-
用途:
- エレクトロニクス:半導体、太陽電池、ディスプレイの製造に使用される。
- 光学:反射防止膜、ミラー、光学フィルターを成膜。
- コーティング:さまざまな素材に保護・装飾用コーティング剤を提供。
-
課題と考察:
- 材料の制限:材料によっては高温で分解・反応するものがある。
- 設備費用:高真空システムと特殊な熱源は高価な場合がある。
- 基板適合性:基板は真空環境と蒸着条件に耐えなければならない。
-
他のPVD技術との比較:
- スパッタリング:高エネルギーのイオンを使用してターゲット材料から原子を離し、より優れた密着性とステップカバレッジを提供する。
- 化学蒸着(CVD):複雑な形状に適しているが、不純物が混入する可能性がある。
- 真空蒸着は、用途によってはよりシンプルでコスト効率が高いが、スパッタリングと同レベルの密着性やステップカバレッジが得られない場合がある。
これらの重要なポイントを理解することで、薄膜蒸着における真空蒸着の役割と、様々な産業用途におけるその重要性を理解することができる。
総括表
アスペクト | 詳細 |
---|---|
定義 | 材料を真空中で気化させ、基板上に蒸着させるPVDプロセス。 |
プロセスステップ | 蒸発 → 輸送 → 凝縮 |
熱源 | 抵抗加熱、電子ビーム蒸発 |
利点 | 高純度、均一成膜、汎用性 |
用途 | エレクトロニクス、光学、コーティング |
課題 | 材料の制限、高い装置コスト、基板適合性 |
PVDとの比較 | スパッタリングよりシンプルでコスト効率が高いが、密着性/ステップカバレッジは劣る |
真空蒸着がお客様の薄膜プロセスをどのように強化できるかをご覧ください。 今すぐ専門家にお問い合わせください !