真空中での薄膜蒸着は、制御された真空環境内で基板上に超薄膜の材料を塗布する特殊なプロセスである。この技術は、半導体、光学、コーティングなど、精密な材料特性が要求される産業において非常に重要です。真空環境は汚染を最小限に抑え、高純度膜の成膜を可能にする。薄膜蒸着は、物理的または化学的手法によって達成することができ、それぞれ所望の膜特性や用途に応じて独自の利点を提供する。このプロセスは、導電性、耐摩耗性、耐食性、光学特性などの特性を変更することにより、基板の性能を向上させます。
キーポイントの説明
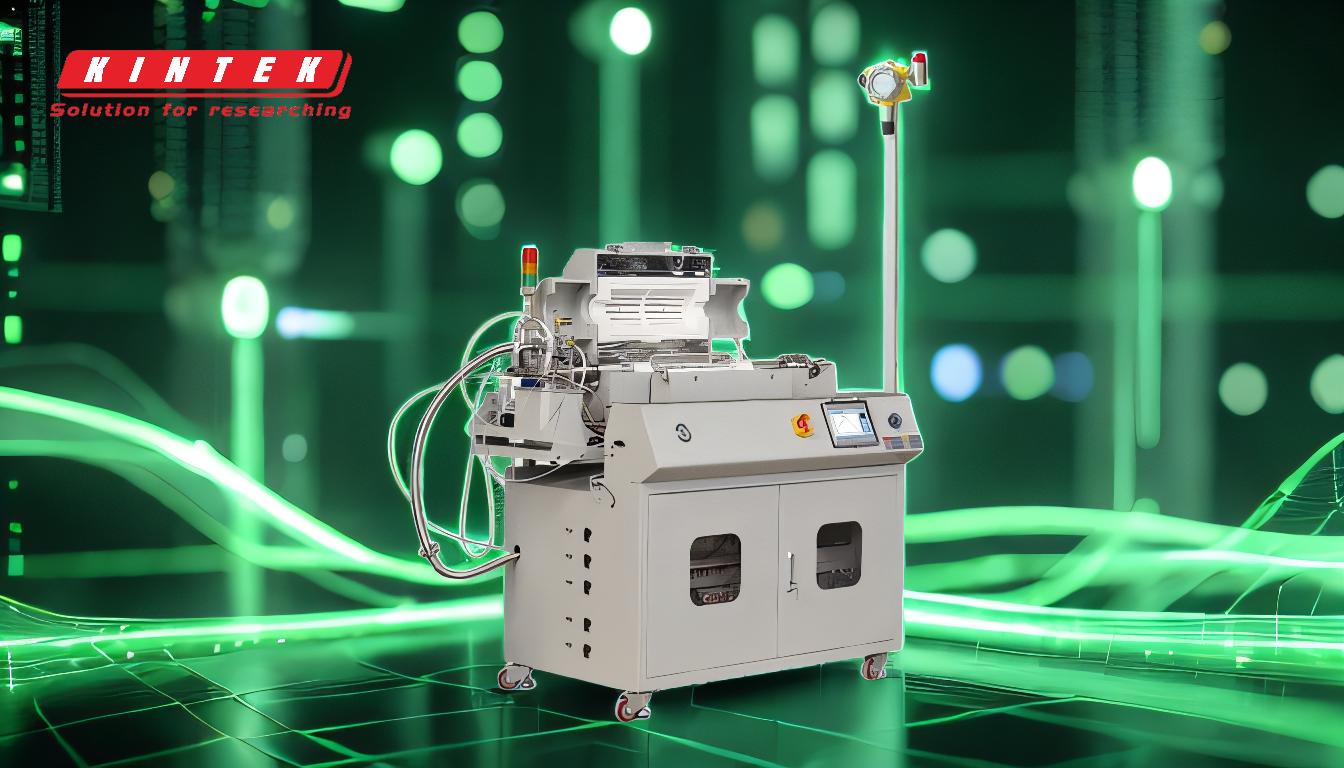
-
真空薄膜蒸着の定義と目的:
- 真空中での薄膜蒸着は、真空チャンバー内で基板上に材料の薄い層(ナノメートルからマイクロメートルの範囲)を塗布する。
- 主な目的は、導電性、硬度、耐食性、光学的または電気的性能など、基板の表面特性を変更または強化することである。
- 真空環境は、空気や他のガスによる汚染を最小限に抑え、高純度で高品質な膜を確保するために非常に重要です。
-
薄膜蒸着の種類:
-
物理的沈殿:
- 機械的、電気機械的、または熱力学的な方法で材料を堆積させる。
-
一般的な手法には次のようなものがある:
- 熱蒸発:真空中で材料を気化点まで加熱し、その蒸気を基板上に凝縮させる。
- スパッタリング:ターゲット材料にイオンを照射して原子を放出させ、基板上に堆積させる。
- イオンビーム蒸着:集束イオンビームを使用して、基板上に材料をスパッタする。
-
化学蒸着:
- 化学反応を利用して薄膜を形成する。
-
一般的な技術には以下のようなものがある:
- 化学気相成長法(CVD):基板表面で気相化学反応が起こり、固体膜が形成される。
- 原子層堆積法(ALD):逐次的、自己限定的な化学プロセスにより、一度に1原子層を蒸着し、精密に制御します。
-
物理的沈殿:
-
薄膜蒸着の主な用途:
- 半導体:マイクロエレクトロニクスの導電層、絶縁層、半導体層の形成に使用される。
- 光学:反射防止コーティングやミラーなど、ガラスの光学特性を向上させる。
- 腐食防止:金属に保護膜を形成し、耐久性を向上させる。
- 耐摩耗性:工具や部品に硬質コーティングを施し、寿命を延ばす。
- エネルギー:太陽電池やバッテリーの効率と性能を向上させるために使用される。
-
真空薄膜蒸着の利点:
- 高純度:真空環境はコンタミネーションを防ぎ、高品質なフィルムを実現します。
- 精密制御:高度な用途に不可欠な、正確な厚みと組成の制御が可能。
- 汎用性:金属、酸化物、化合物を含む幅広い材料を蒸着できる。
- 強化された特性:カスタマイズされた特性を持つ機能層を追加することで、基板の性能を向上させます。
-
課題と考察:
- コスト:真空蒸着装置とプロセスは高価である。
- 複雑さ:望ましい結果を得るためには、専門的な知識と設備が必要。
- 拡張性:方法によっては大量生産に限界がある。
- 材料の制限:気化または反応特性により、すべての材料が真空蒸着に適しているわけではありません。
-
蒸着技術の比較:
-
熱蒸発:
- 長所単純、費用対効果、高い蒸着率。
- 短所:融点の低い材料に限られる、精度が低い。
-
スパッタリング:
- 長所幅広い材料に対応し、密着性が高い。
- 短所:成膜速度が遅い、装置が複雑。
-
CVD:
- 長所高品質のフィルム、複雑な形状のステップカバレッジの良さ。
- 短所:高温を必要とし、有害な副生成物が発生する可能性がある。
-
ALD:
- 長所原子レベルの精度、優れた均一性。
- 短所:蒸着速度が遅い、材料の選択肢が限られている。
-
熱蒸発:
-
薄膜蒸着の今後の動向:
- ナノテクノロジー:ナノスケールデバイスとアプリケーションで増加する薄膜の使用。
- グリーンテクノロジー:環境に優しい成膜方法と材料の開発。
- オートメーション:AIとオートメーションの統合によるプロセス制御と効率の向上。
- ハイブリッド技術:物理的手法と化学的手法の組み合わせによる膜特性の向上
要約すると、真空中での薄膜蒸着は、基板に機能性コーティングを施し、幅広い用途の性能を向上させるために使用される、多用途で精密なプロセスである。純度と制御の面で大きな利点がある一方で、慎重な検討が必要な課題もある。技術の進歩に伴い、薄膜蒸着はエレクトロニクス、光学、エネルギーなどの産業でますます重要な役割を果たすようになると予想される。
総括表
アスペクト | 詳細 |
---|---|
目的 | 導電性、耐食性などの基材特性を改質する。 |
種類 | 物理的(例:熱蒸着、スパッタリング) & 化学的(例:CVD、ALD) |
主な用途 | 半導体、光学、腐食保護、エネルギー、耐摩耗性 |
利点 | 高純度、精密制御、汎用性、特性の向上 |
課題 | 高コスト、複雑性、拡張性の問題、材料の制限 |
薄膜蒸着がお客様のアプリケーションをどのように最適化できるかをご覧ください。 今すぐ専門家にお問い合わせください !