熱蒸着とマグネトロンスパッタリングは、広く使われている2つの薄膜蒸着技術で、それぞれに異なる特徴と用途がある。熱蒸着は、真空中で材料が気化するまで加熱し、基板上に薄膜を形成する。蒸着速度が速く、OLEDや薄膜トランジスタなどの用途に適している。一方、マグネトロンスパッタリングは、高エネルギーのプラズマを使ってターゲット材料から原子を放出し、基板上に堆積させる。この方法は、膜の密着性、均一性、カラーオプションの多様性に優れ、電気および光学用途に理想的である。この2つの選択は、成膜速度、膜質、特定の用途要件などの要因によって決まる。
主なポイントを説明する:
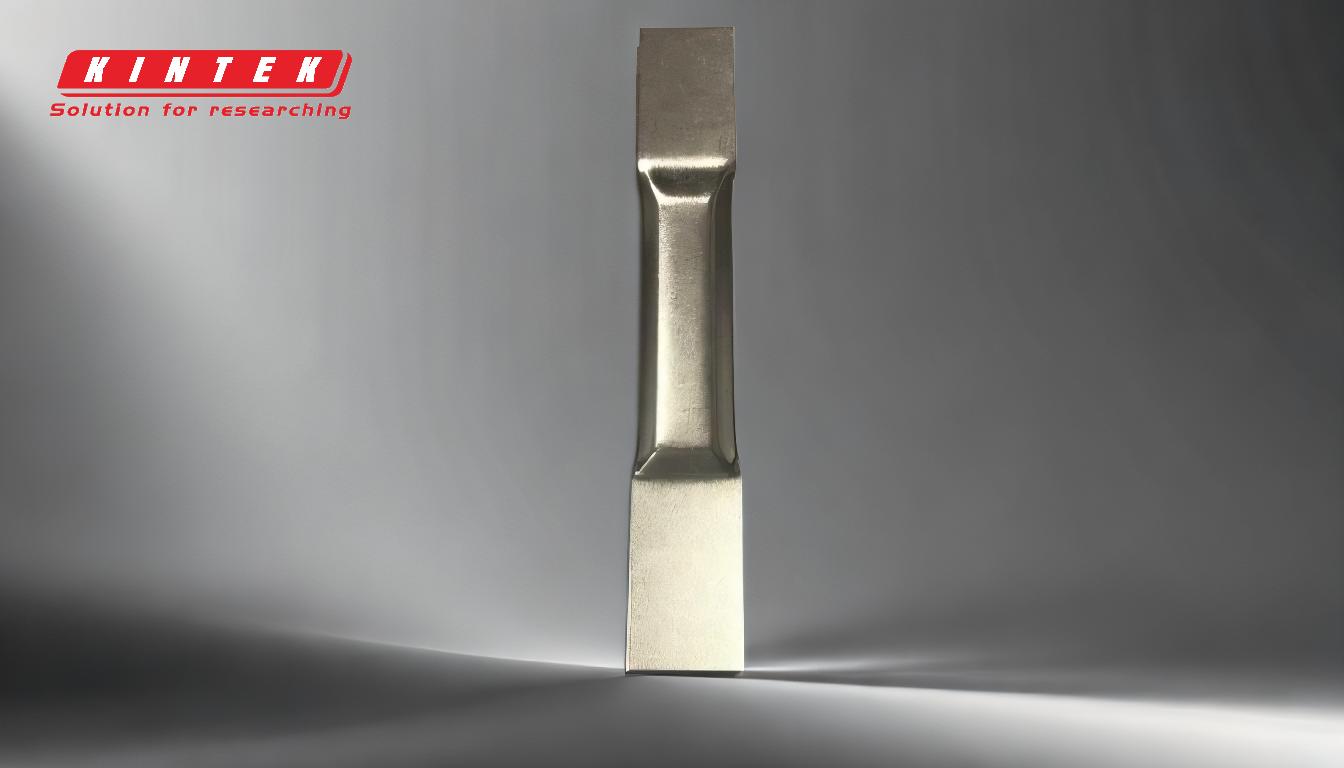
1. 析出のメカニズム
-
熱蒸発:
- 抵抗性熱源を使用し、真空中で固体材料を蒸発させる。
- 強固な蒸気流を生成し、より高い蒸着速度を可能にする。
- 合金やシーケンシャルコーティングの形成に適しています。
-
マグネトロンスパッタリング:
- プラスに帯電したイオンをマイナスに帯電したターゲット材料に衝突させる。
- 単原子またはクラスターを放出するため、膜の均一性と密着性が向上する。
- 閉鎖磁場内で動作するため、高いスケーラビリティと自動化が可能。
2. フィルム特性
-
粘着性:
- 熱蒸着膜は、蒸着エネルギーが低いため、比較的弱い密着性を示す。
- スパッタリング膜は、高エネルギープロセスであるため、基材との密着性が高い。
-
均一性:
- 熱蒸着は膜の均一性に優れています。
- スパッタリングはパーティクルを含む可能性があり、均一性は若干劣りますが、全体的な膜質は向上します。
-
粒径:
- スパッタリングでは粒径が小さくなり、硬度や耐久性などのフィルム特性が向上します。
- 熱蒸発では粒径が大きくなり、フィルムの機械的特性に影響を与える可能性がある。
3. 蒸着速度と蒸着効率
-
熱蒸発:
- 蒸着速度が速く、短時間でのコーティングが必要な用途に適しています。
- 安定した蒸気流により、運転時間が短縮されます。
-
マグネトロンスパッタリング:
- 純金属以外の成膜レートが低い。
- 稼働時間は長いが、膜特性の制御が容易。
4. 色と素材の多様性
-
熱蒸発:
- アルミ本来の色に限ります。
- 他の色をご希望の場合は、別途スプレー塗装が必要です。
-
マグネトロンスパッタリング:
- 変調による色の多様性を提供。
- よりリアルで均一なメタル効果が得られる。
5. 応用例
-
熱蒸発:
- OLEDや薄膜トランジスタの作成によく使用される。
- 高い成膜速度とシンプルなコーティングを必要とする用途に有効。
-
マグネトロンスパッタリング:
- 電気・光学用途に最適。
- 優れた粘着性と均一性を持つ高品質のフィルムを必要とする用途に適している。
6. 真空と環境条件
-
熱蒸発:
- 高真空環境を必要とする。
- 膜中の吸収ガスが少なく、より純度の高いコーティングが可能。
-
マグネトロンスパッタリング:
- より低い真空度で使用可能。
- 吸収ガス量が多く、フィルムの特性に影響を与えるが、密着性も向上する。
7. エネルギーと粒子のダイナミクス
-
熱蒸発:
- 析出種はエネルギーが低いため、膜の密度が低くなる。
- アトマイズされた粒子はより分散しているため、指向性の低い成膜となる。
-
マグネトロンスパッタリング:
- 蒸着種はエネルギーが高いため、より緻密で耐久性の高い膜が得られる。
- アトマイズされた粒子はより方向性があり、膜厚と均一性をよりよく制御できる。
8. スケーラビリティと自動化
-
熱蒸発:
- プロセスの性質上、拡張性が低く、自動化が難しい。
-
マグネトロンスパッタリング:
- 拡張性が高く、多くの用途で自動化できるため、大規模生産に適している。
まとめると、熱蒸着とマグネトロンスパッタリングのどちらを選択するかは、成膜速度、膜質、密着性、色彩の汎用性などの要因を含む、アプリケーションの具体的な要件によって決まる。それぞれの方法には独自の利点と限界があり、さまざまなタイプのプロジェクトや業界に適している。
総括表
特徴 | 熱蒸着 | マグネトロンスパッタリング |
---|---|---|
メカニズム | 真空中での抵抗加熱 | 高エネルギープラズマでターゲットから原子を放出 |
堆積速度 | 高い | 低い(純金属を除く) |
フィルム密着性 | 弱い | 強い |
フィルムの均一性 | 優れている | やや低いが、全体的な品質は良い |
粒度 | 大きい | 小さい |
色の多様性 | アルミニウムに限定 | 豊富なカラーオプション |
アプリケーション | OLED、薄膜トランジスタ | 電気および光学製造 |
真空要件 | 高真空 | 低真空 |
拡張性 | スケーラビリティが低い | 高い拡張性と自動化 |
どの薄膜蒸着技術がお客様のニーズに合うか、まだご不明ですか? 当社の専門家に今すぐご連絡ください にお問い合わせください!