射出成形とインサート成形は、プラスチック部品の製造に使われる2つの異なる製造工程で、それぞれに独自の用途と利点があります。射出成形では、金型のキャビティに溶融プラスチックを注入して部品を成形しますが、インサート成形では、あらかじめ成形されたインサート(多くの場合金属)を金型に入れてから、その周囲にプラスチックを注入します。重要な違いは、通常の射出成形では使用されないインサート成形のインサートの有無にある。関連工程であるオーバーモールドは、2つの材料を射出して基材とオーバーモールドを作りますが、1つの工程で複数の材料を使用する点でインサート成形とは異なります。
キーポイントの説明
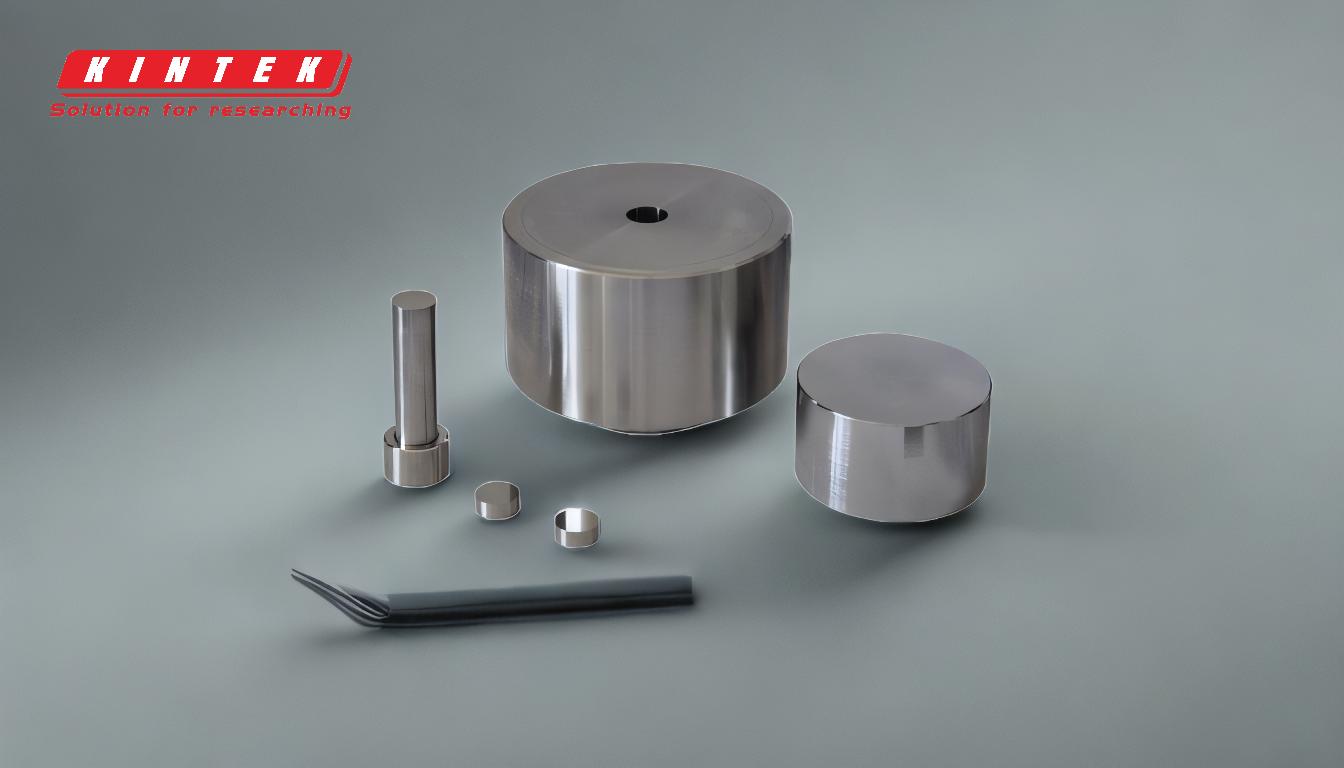
-
定義とプロセス:
- 射出成形:溶融プラスチックを金型のキャビティに高圧で注入する製造工程。プラスチックが冷えて固まると、金型が開き、部品が射出される。これは単一材料のプロセスであり、さまざまなプラスチック部品の製造に広く使用されている。
- インサート成形:この工程では、プラスチックが射出される前に、あらかじめ成形されたインサート(多くの場合金属製)が金型に入れられる。その後、溶融プラスチックがインサートの周りを流れ、冷えるにつれてインサートと結合する。この工程は、ねじ切りされたインサートや電気コネクターなど、プラスチックと金属の特性を組み合わせた部品を作るために使用される。
-
使用材料:
- 射出成形:通常、1種類のプラスチック材料を使用する。材料は、強度、柔軟性、耐熱性など、最終部品に求められる特性に基づいて選択される。
- インサート成形:プラスチックと、金属、セラミック、その他の材料で作られた、あらかじめ形成されたインサートの両方を使用します。プラスチックは、インサートとよく接着するように選択され、最終製品の強度と耐久性を保証します。
-
用途:
- 射出成形:消費財、自動車部品、医療機器など、幅広いプラスチック部品の生産によく使用される。効率と再現性が高く、大量生産に適している。
- インサート成形:電子部品、医療機器、自動車部品の製造など、素材の組み合わせが必要な用途で使用される。特に、金属補強や特定の機械的特性を必要とする部品の製造に有用である。
-
利点:
-
射出成形:
- 高い生産効率と再現性。
- 複雑な形状を高精度で生産可能。
- 大量生産に適したコストパフォーマンス
-
インサート成形:
- プラスチックと金属の利点を組み合わせ、強度と耐久性を向上させた部品を実現。
- インサートが部品に直接成形されるため、二次組立作業の必要性が減少します。
- 異なる材料を一体化することで、部品全体の性能を向上させることができる。
-
射出成形:
-
課題:
-
射出成形:
- 単一素材の部品に限定されるため、用途によっては要件を満たさない場合がある。
- 初期金型費用が高く、少量生産の障害となる可能性がある。
-
インサート成形:
- インサートを正確に配置する必要があり、成形工程が複雑になる可能性がある。
- 適切な結合を確実にするため、インサートはプラスチック材料に適合していなければならない。
- インサートの追加コストや、より複雑な金型設計が必要になる場合があります。
-
射出成形:
-
オーバーモールディングとの比較:
- オーバーモールディング:このプロセスでは、2つの材料を射出して基材とオーバーモールドを作る。異なる材料を組み合わせるという点ではインサート成形に似ているが、1回の工程で別の材料の上に別の材料を成形する。オーバーモールドは、柔らかいグリップを持つ部品、多色の部品、材料特性の異なる部品を作るためによく使用されます。
- インサート成形:オーバーモールドとは異なり、インサート成形では、プラスチック材料とあらかじめ成形されたインサートを1回で成形する。インサートは成形されるのではなく、プラスチックが射出される前に金型に入れられる。このプロセスは、異なるプラスチックを重ねるのではなく、プラスチックと金属などの他の材料を組み合わせることに重点を置いている。
-
デザインへの配慮:
- 射出成形:設計者は、金型への適切な充填と部品の排出を確実にするために、肉厚、ゲートの位置、抜き勾配などの要素を考慮する必要があります。
- インサート成形:さらに考慮すべき点として、インサートの配置や設計、インサートとプラスチック材料の接合などがあります。インサートは、成形プロセスに耐え、望ましい機械的特性を提供するように設計されなければならない。
まとめると、射出成形とインサート成形はどちらもプラスチック部品を作るために使われますが、その目的は異なり、適した用途も異なります。射出成形は、大量に生産される単一素材の部品に最適であり、インサート成形は、プラスチックを金属などの他の材料と組み合わせて性能を向上させた部品を作るために使用されます。これらのプロセスの違いを理解することは、特定の用途に適した製造方法を選択するために非常に重要です。
総括表
側面 | 射出成形 | インサート成形 |
---|---|---|
工程 | 金型のキャビティに溶融プラスチックを注入する。 | あらかじめ成形されたインサートを金型に入れ、その周囲にプラスチックを注入します。 |
材料 | 単一のプラスチック素材。 | プラスチックと予備成形されたインサート(金属など)の組み合わせ。 |
用途 | 消費財、自動車部品、医療機器 | 電子部品、医療機器、金属補強の自動車部品。 |
利点 | 高効率、高精度、大量生産に適したコスト効率。 | プラスチックと金属を組み合わせ、アセンブリを減らし、部品の性能を向上させます。 |
課題 | 単一素材の部品に限定され、金型コストが高い。 | インサートの正確な配置、互換性、追加コスト。 |
お客様のプロジェクトに適した成形プロセスの選択にお困りですか? 今すぐ専門家にお問い合わせください !