CVD(化学的気相成長法)とPVD(物理的気相成長法)は、切削工具のコーティング技術として広く使用されている2つの手法で、それぞれに異なる特性と用途があります。どちらの手法も、基材上に薄く耐久性のある層を蒸着させることで工具の性能を高めることを目的としていますが、そのプロセス、コーティング特性、特定の加工作業への適合性は大きく異なります。PVDでは、固体材料を気化させて基材に蒸着させるため、より薄く滑らかなコーティングが得られ、エッジもシャープで、精密仕上げ加工に最適です。一方、CVDは気体状の前駆体を使用し、化学反応によってより厚く粗い皮膜を形成するため、優れた遮熱性と耐摩耗性を備え、荒加工や連続切削加工に適しています。これらの違いを理解することは、加工要件と加工材料に基づいて適切なコーティング方法を選択するために非常に重要です。
キーポイントの説明
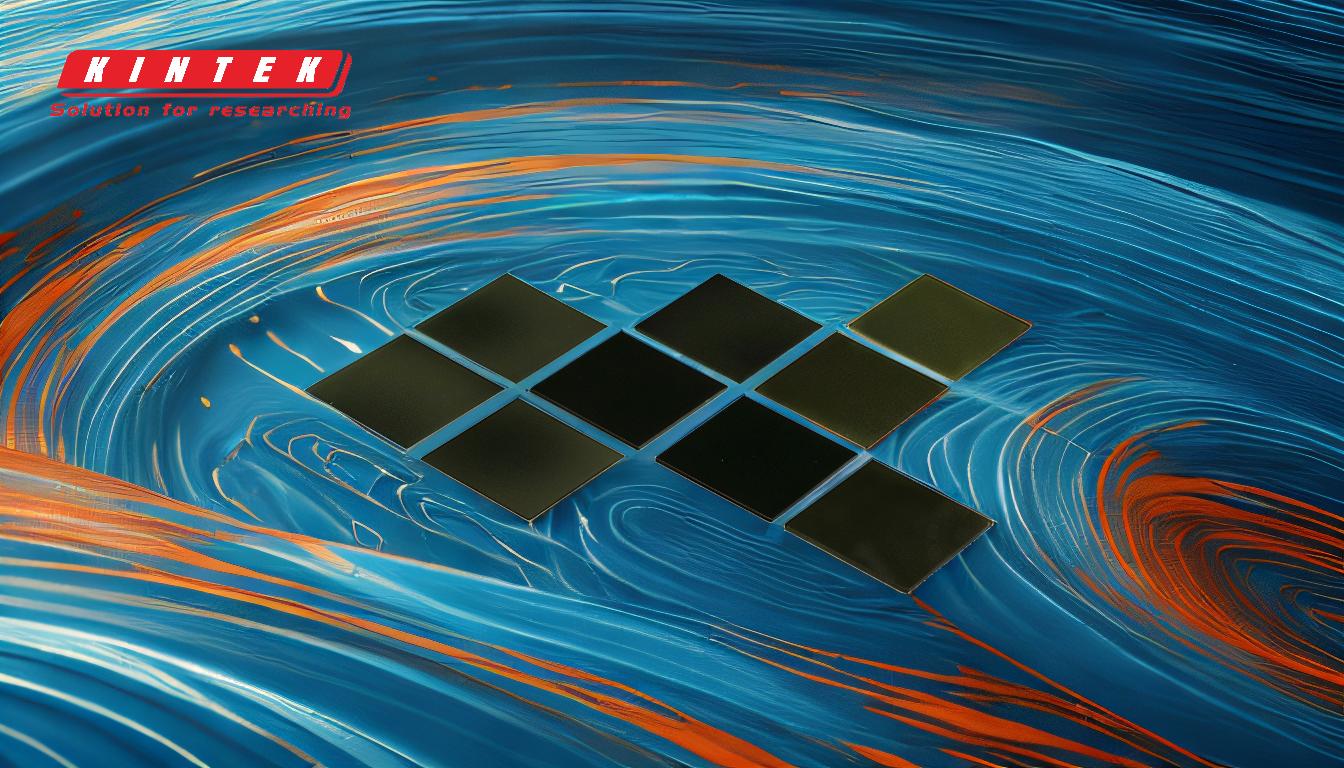
-
プロセスの違い:
-
PVD:
- アーク放電やスパッタリングなどの物理的方法を用いて固体材料(ターゲット)を気化させる。
- 気化した原子は基板上に凝縮し、薄く滑らかなコーティングを形成する。
- 比較的低温(250℃~450℃)で作動するため、熱に弱い材料に適している。
-
CVD:
- 高温(450℃~1050℃)で化学反応するガス状前駆体を使用し、固体皮膜を成膜する。
- 化学反応により、PVDと比較して厚く粗い皮膜が形成される。
- 高温を必要とするため、熱に敏感な基材では使用が制限されることがある。
-
PVD:
-
コーティングの特性:
-
PVD:
- 滑らかな表面で薄い皮膜(3~5μm)を形成し、切れ味を向上させる。
- 冷却時に圧縮応力を形成し、耐久性と耐クラック性を向上。
- 工具刃先が頻繁に衝撃を受けるフライス加工のような断続切削加工に最適。
-
CVD:
- より粗い表面でより厚いコーティング(10~20μm)を生成し、より優れた断熱性と耐摩耗性を提供します。
- 工具が一貫した熱と摩擦に直面する旋盤加工のような連続切削加工に適しています。
-
PVD:
-
機械加工における用途:
-
PVD:
- フライス加工、ドリル加工、ねじ切り加工など、精密さと鋭い切れ味が要求される仕上げ加工に最適。
- ステンレス鋼、チタン、熱処理合金などの加工によく使用される。
-
CVD:
- 荒加工や旋削、中ぐりなどの重切削作業に効果的。
- 鋳鉄、炭素鋼、高温合金のような材料の加工に適している。
-
PVD:
-
環境および操作上の考慮事項:
-
PVD:
- 化学反応を伴わず、有害な副産物を生成しないため、環境に優しい。
- 処理温度が低いため、エネルギー消費を抑え、基板の歪みを最小限に抑えることができる。
-
CVD:
- 化学反応を伴うため汚染物質が発生する可能性があり、適切な廃棄物管理が必要。
- 高温になると基材が変形する可能性があり、素材によっては使用が制限される。
-
PVD:
-
利点と限界:
-
PVD:
- 利点薄くシャープなコーティング、低い加工温度、環境に優しい。
- 制限事項コーティングの厚さに制限があり、遮熱効果に劣る。
-
CVD:
- 利点より厚く耐久性のあるコーティング、優れた耐熱性と耐摩耗性。
- 制限事項加工温度が高い。
-
PVD:
これらの重要な違いを理解することで、購入者やエンジニアは、特定の加工要件、材料特性、および望ましい結果に基づいて、PVDまたはCVDコーティングされた切削工具のどちらを使用するかについて、情報に基づいた意思決定を行うことができます。
まとめ表
側面 | PVD | CVD |
---|---|---|
プロセス | 固体材料を気化、低温 (250°C-450°C) | ガス状前駆体を使用、高温 (450°C-1050°C) |
コーティング厚さ | 薄い (3~5μm), 滑らかな表面 | 厚い(10~20μm)、粗い表面 |
コーティング特性 | シャープなエッジ、圧縮応力、耐久性 | 優れた遮熱性、耐摩耗性 |
用途 | 仕上げ加工(フライス加工、穴あけ加工、ねじ切り加工) | 荒加工と重切削(旋削、中ぐり) |
材質 | ステンレス鋼、チタン、熱処理合金 | 鋳鉄、炭素鋼、高温合金 |
環境への影響 | 環境に優しい、有害な副産物がない | 汚染の可能性があり、廃棄物管理が必要 |
利点 | シャープなコーティング、低い処理温度、環境に優しい | 耐久性のあるコーティング、優れた耐熱性と耐摩耗性 |
制限事項 | 厚みに制限があり、熱バリアとしての効果は低い | 加工温度が高く、基材が変形する可能性がある |
お客様の切削工具に適したコーティングの選択にお困りですか? 今すぐ専門家にお問い合わせください !