冷間加工と熱間加工は、金属を目的の形状やサイズに成形するために使用される2つの基本的な金属加工プロセスである。冷間加工は、金属の再結晶温度以下の温度で行われ、強度と硬度は高まるが延性は低下する。例えば、圧延、延伸、曲げ加工などがある。一方、熱間加工は再結晶温度以上で行われ、金属を著しく硬化させることなく、より容易に成形することができる。例えば、鍛造、押出、熱間圧延などがある。いずれのプロセスにも明確な利点があり、最終製品に求められる特性に応じて選択されます。
キーポイントの説明
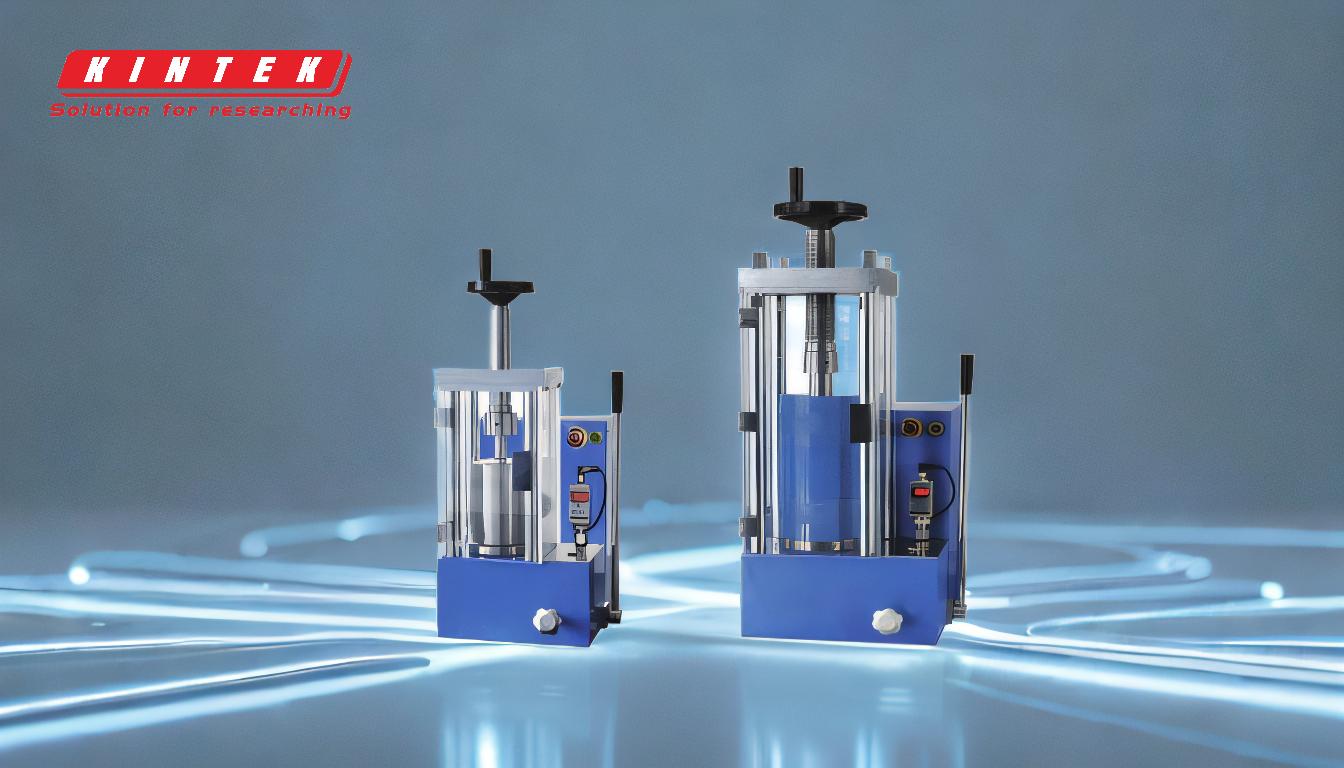
-
コールド・ワーキング:
- 定義:冷間加工とは、金属を再結晶点以下の温度で成形する工程を指す。この加工は金属の強度と硬度を高めるが、延性は低下させる。
-
例:
- ローリング:金属をローラーに通して厚みを減らし、表面の仕上がりを良くすること。
- 図面:金型に金属を通し、ワイヤーやチューブを作ること。
- 曲げ:加熱せずに金属に力を加えて形状を変化させること。
- 利点:強度の向上、表面仕上げの改善、正確な寸法管理。
- デメリット:延性の低下、脆性の増加、変形に対する抵抗の増加によるエネルギー消費の増加。
-
熱間加工:
- 定義:熱間加工では、再結晶点以上の温度で金属を成形する。これにより、金属は著しく硬化することなく、より容易に変形することができる。
-
例:
- 鍛造:ハンマーやプレス機を用いて、局所的な圧縮力を利用して金属を成形すること。
- 押し出し:金属を金型に通し、長尺で均一な形状にすること。
- 熱間圧延:高温で金属を圧延し、厚みを減らして機械的性質を改善すること。
- 利点:変形しやすく、エネルギー消費量を削減し、延性を向上させる。
- デメリット:酸化の可能性、寸法管理の精度の低さ、高温装置の必要性。
-
冷間加工と熱間加工の比較:
- 温度:冷間加工は再結晶温度以下で行い、熱間加工は再結晶温度以上で行う。
- 材料特性:冷間加工は強度と硬度を高めるが延性を低下させるが、熱間加工は延性を維持または向上させる。
- 用途:冷間加工は、高い強度を必要とする精密部品や構成部品によく使用され、熱間加工は、大規模な成形や形成に使用される。
-
冷間加工と熱間加工の選択:
- 素材タイプ:冷間加工に適した素材もあれば、熱間加工を施さなければ望ましい特性が得られない素材もある。
- 最終用途の要件:金属部品の最終的な用途によって、冷間加工と熱間加工のどちらが適切かが決まる。
- 経済的考察:設備のコスト、エネルギー消費量、生産速度は、2つの工程間の選択に影響を与えうる。
冷間加工と熱間加工の違いと用途を理解することで、製造業者は、金属製品に望まれる特性と性能を達成するために、最も適切な工程を選択することができる。
総括表
側面 | 冷間加工 | 熱間加工 |
---|---|---|
加工温度 | 再結晶温度以下 | 再結晶温度以上 |
例 | 圧延、絞り、曲げ | 鍛造、押出、熱間圧延 |
利点 | 強度の向上、表面仕上げの改善 | 変形しやすく、延性が向上する。 |
デメリット | 延性の低下、エネルギー消費量の増加 | 酸化リスク、制御精度の低下 |
用途 | 精密部品、高強度部品 | 大規模な成形と形成 |
冷間加工と熱間加工の選択でお困りですか? 当社の専門家に今すぐご連絡ください にご相談ください!