物理的気相成長法(PVD)は、薄膜で材料をコーティングするために様々な産業で広く使われている技術である。高い蒸着速度、優れた膜質、環境への優しさなど、いくつかの利点がある。しかし、高コスト、複雑さ、真空条件の必要性などの欠点もある。PVDの長所と短所を理解することは、製造から研究まで幅広い用途において、十分な情報に基づいた意思決定を行うために不可欠である。
主なポイントを説明します:
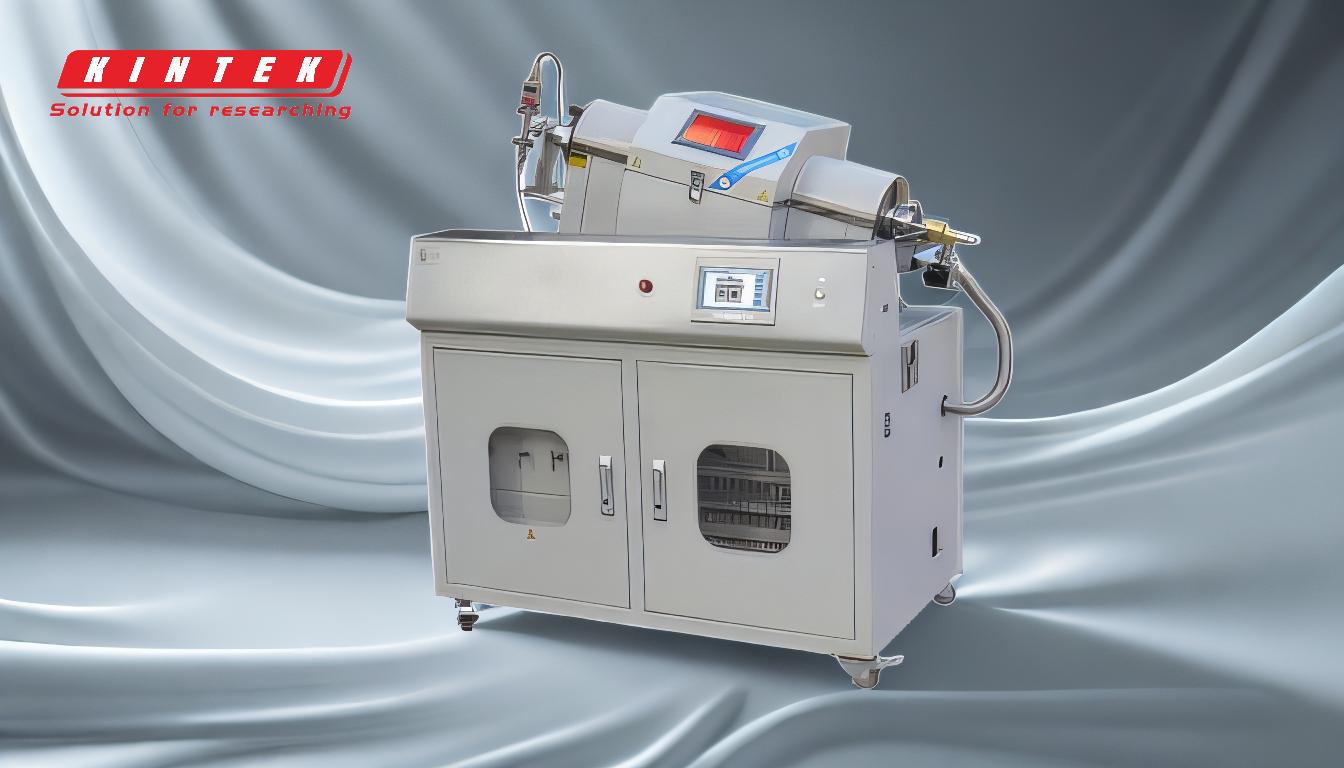
-
PVDの利点:
- 高い成膜速度と試料の有効利用: 蒸着やスパッタリングなどのPVD法は、高い蒸着速度と効率的な材料利用が可能です。そのため、迅速かつ精密なコーティングを必要とする用途に適しています。
- 優れた膜質と均一性: イオンビームスパッタリングのような技術は、優れた品質と均一性を持つ膜を生成し、製造プロセスにおける歩留まりの向上につながります。
- 耐食性と耐摩耗性 PVDコーティングは、製品の耐薬品性と耐摩耗性を高め、耐久性と寿命の延長を実現します。また、カラーバリエーションも豊富で、美的価値を高めます。
- 環境に優しい: PVDは有害な化学薬品を使用せず、廃棄物も最小限に抑えられるため、環境に優しいプロセスと考えられています。
-
PVDの短所
- 高コストと複雑さ: PVDプロセス、特に真空条件を必要とするプロセスは、化学気相成長法(CVD)のような他の成膜方法と比べて高価で複雑である。特殊な装置と熟練したオペレーターが必要なため、全体的なコストがかさむ。
- 時間がかかる: 真空条件が必要なため、PVDには時間がかかり、高スループットの製造環境では欠点となる。
- 基板適合性の制限: PVDは温度に敏感な材料には不向きである。高温になるため、そのような基板にダメージを与える可能性があるからである。
-
CVDとの比較:
- 選択性と適合性: CVDは選択性と適合性に優れ、粗い表面を均一に被覆したり、基板の特定の領域に選択的に蒸着したりすることができる。このため、CVDは特定の用途においてより汎用性が高い。
- 熱的制約: CVDは高温(最高900℃)を必要とするため、温度に敏感な材料への使用が制限される。一方、PVDは、高温に耐えられないものも含め、より幅広い基板に使用できる。
- バッチ処理: CVDは大量の基板を処理できるため、大量生産に効率的である。PVDは大量生産にも少量生産にも適しているが、バッチ処理ではCVDの効率には及ばないかもしれない。
-
運用上の考慮点
- 自動化と制御: PVDコーティング装置はコンピュータ制御されることが多いため、オペレーターは複数の作業をこなすことができ、生産コストとターンアラウンドタイムを削減することができます。この自動化により、PVDプロセスの効率が向上します。
- 材料の無駄: CVDでは、加熱された部分のみがコーティングされるため、一般的に材料の無駄が少ない。PVDは効率的ではあるが、特に選択的加熱が必要な場合、材料の利用という点ではCVDに及ばないかもしれない。
まとめると、PVDは膜質、環境適合性、耐久性の面で大きな利点があり、多くの産業用途で好ましい選択肢となっている。しかし、コストが高く、複雑で、時間がかかるという欠点が目立つ。CVDと比較した場合、PVDはある分野では優れているが、他の分野、特に選択性とバッチ処理効率では劣っている。これらの長所と短所を理解することは、特定のアプリケーション要件に基づいて適切な成膜方法を選択する上で極めて重要である。
要約表
側面 | 長所 | 短所 |
---|---|---|
蒸着率 | 高い蒸着速度と効率的な材料利用 | 真空条件による高コストと複雑さ |
フィルム品質 | 優れたフィルム品質と均一性 | 時間のかかるプロセス |
耐久性 | 耐食性と耐摩耗性の向上 | 温度に敏感な素材との互換性は限定的 |
環境への影響 | 環境に優しく、廃棄物を最小限に | |
自動化 | コンピューター制御により、生産コストと納期を削減 | CVDに比べ、材料廃棄が多い場合がある |
お客様のアプリケーションに適した成膜方法の選択にお困りですか? 当社の専門家に今すぐご連絡ください オーダーメイドのソリューションを