アニーリングプロセスは、金属や合金の特性を改善するために冶金学や材料科学で広く使用されているが、いくつかの制約がある。これには、温度制御、所要時間、材料固有の課題、エネルギー消費、表面酸化の可能性などに関する制約が含まれる。さらに、微細構造が複雑であったり、パラメーターの選択が不適切であったりするために、プロセスが必ずしも望ましい材料特性を達成できるとは限りません。これらの限界を理解することは、アニールプロセスを最適化し、特定の用途で望ましい結果を得るために極めて重要です。
キーポイントの説明
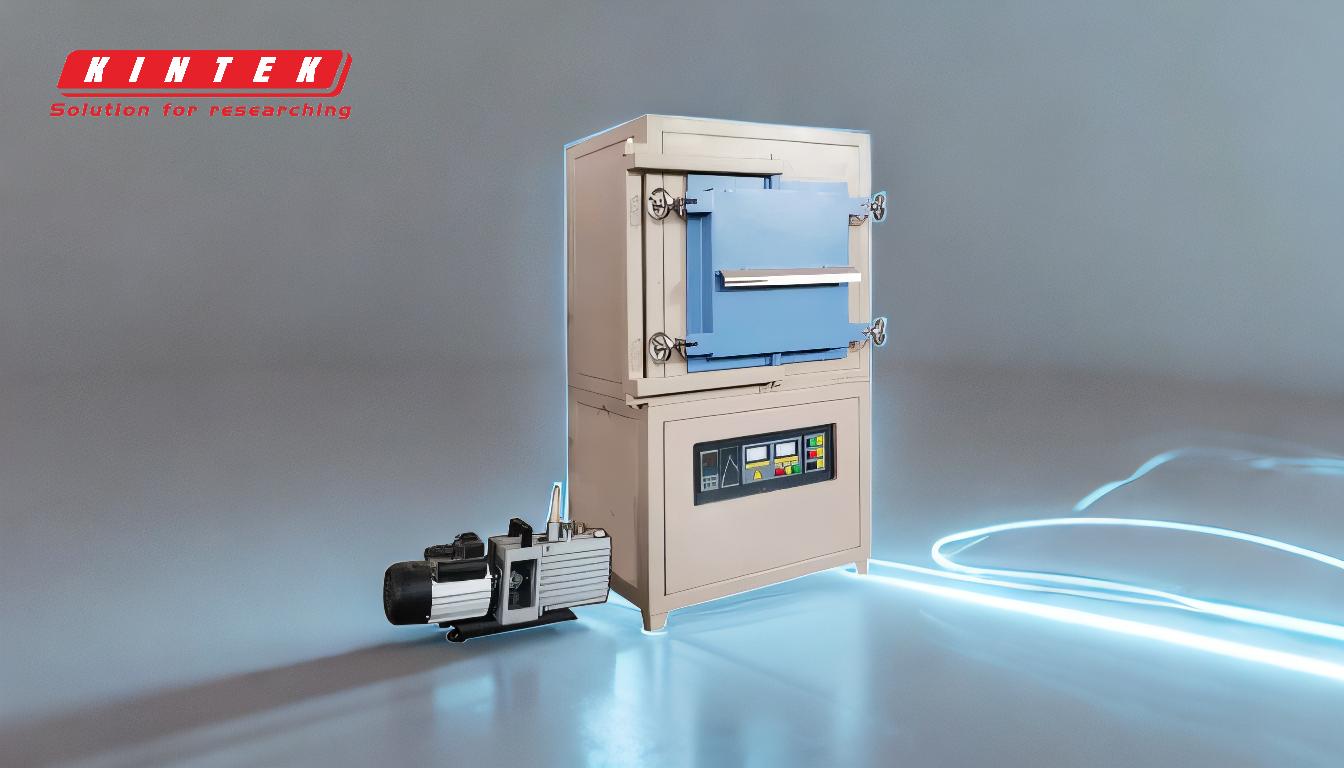
-
温度管理の課題:
- 精度要件:アニーリングは、望ましい材料特性を得るために正確な温度制御が必要です。わずかなずれは、不完全な再結晶や粒成長の問題につながる可能性があります。
- 装置の制限:すべての炉が大型ワークや複雑なワークに対して均一な温度を維持できるわけではないため、結果にばらつきが生じます。
- 材料感度:高炭素鋼や特定の合金のように、効果的な焼きなましを行うための温度範囲が狭い材料もあり、プロセスがより困難になる。
-
時間的制約:
- 長い処理時間:アニールには長時間の加熱・冷却サイクルが必要な場合が多く、大量生産には時間がかかり非効率的である。
- 冷却速度の感度:材料によっては、内部応力を避けるために冷却速度を遅くする必要がありますが、これは処理時間をさらに長くする可能性があります。
-
材料固有の制限:
- 不均一な微細構造:不均質な組成や過去の加工履歴を持つ材料は、焼鈍に均一に反応しない場合がある。
- 粒成長の問題:過度の焼鈍は過度の結晶粒成長を招き、材料の強度と靭性を低下させる。
- 適用範囲の制限:非金属複合材料やセラミックなど、アニールがあまり効かない材料もある。
-
エネルギー消費:
- 高エネルギー必要量:高温を長時間維持することは、多大なエネルギーを消費し、プロセスをコスト高にし、環境にやさしくないものにする。
- バッチ処理の非効率性:バッチ焼鈍は一般的であるが、連続焼鈍に比べエネルギー効率が低い。
-
表面酸化と脱炭:
- 酸化のリスク:酸素の存在下で高温にさらされると、表面が酸化し、材料の品質が低下する。
- 脱炭:鋼の場合、長時間の加熱は表面から炭素を失わせ、硬度と耐摩耗性を低下させる。
-
工程の複雑さと技能要件:
- パラメータ最適化:適切なアニール温度、時間、冷却速度を選択するには、専門知識と実験が必要です。
- アニール後の処理:焼入れや焼戻しなどの追加工程が必要な場合があり、複雑さを増す。
-
経済的・実用的制約:
- 設備費:高品質のアニール炉と温度制御システムは、購入と維持に費用がかかる。
- スペース要件:大規模なアニール処理には大きな床面積が必要であり、小規模な施設では実現不可能な場合がある。
-
一貫性のない結果:
- 材料反応のばらつき:管理されたパラメータを使用しても、材料組成のばらつきや事前の処理により、結果に一貫性がなくなることがある。
- ヒューマンエラー:アニール工程を手動で管理すると、誤った温度設定やタイミングなど、エラーのリスクが高まる。
-
特定の特性に対する限定的な改善:
- 硬さと強さのトレードオフ:焼きなましは、延性を向上させるために硬度と強度を低下させることが多いが、すべての用途に望ましいとは限らない。
- 欠陥への影響は限定的:焼きなましは内部応力を低減できるが、ボイドや介在物などの欠陥をすべて除去できるわけではない。
-
環境と安全への懸念:
- 熱と排出:高温プロセスでは熱と排ガスが発生するため、適切な換気と安全対策が必要となる。
- 労働者の安全:高温材料の取り扱いや高温機器の操作には安全上のリスクが伴う。
これらの限界を理解することで、メーカーとエンジニアは、最適な結果を得るために、アニールプロセスの設計、適切な材料の選択、および補完的な処理の実施を改善することができます。
総括表
限界カテゴリー | 主な課題 |
---|---|
温度管理 | 精度要件、装置の限界、材料の感度 |
時間的制約 | 処理時間が長い、冷却速度に敏感 |
材料特有の問題 | 不均一な微細構造、粒成長、限定された適用性 |
エネルギー消費 | 必要エネルギーが高く、バッチ処理では非効率 |
表面酸化 | 鋼の酸化リスク、脱炭 |
プロセスの複雑性 | パラメータ最適化、ポストアニール処理 |
経済的制約 | 設備コスト、必要スペース |
一貫性のない結果 | 材料反応のばらつき、ヒューマンエラー |
限定的な特性改善 | 硬度と強度のトレードオフ、限られた欠陥の除去 |
環境への懸念 | 熱と排出物、作業員の安全リスク |
アニールプロセスの最適化にお困りですか? 当社の専門家に今すぐご連絡ください オーダーメイドのソリューションを