焼結は材料科学と製造における重要なプロセスであり、熱と場合によっては圧力を加えることによって粉末材料を固体構造に結合させるために使用される。このプロセスにより気孔が減少し、強度、密度、熱伝導性などの材料特性が向上する。焼結プロセスにはいくつかの種類があり、それぞれが特定の材料、用途、望ましい結果に適している。固相焼結、液相焼結、ダイレクトメタルレーザー焼結(DMLS)、スパークプラズマ焼結(SPS)などがある。これらのプロセスを理解することは、セラミックス、金属、プラスチックのいずれであっても、特定の用途に適した方法を選択するために不可欠です。
キーポイントの説明
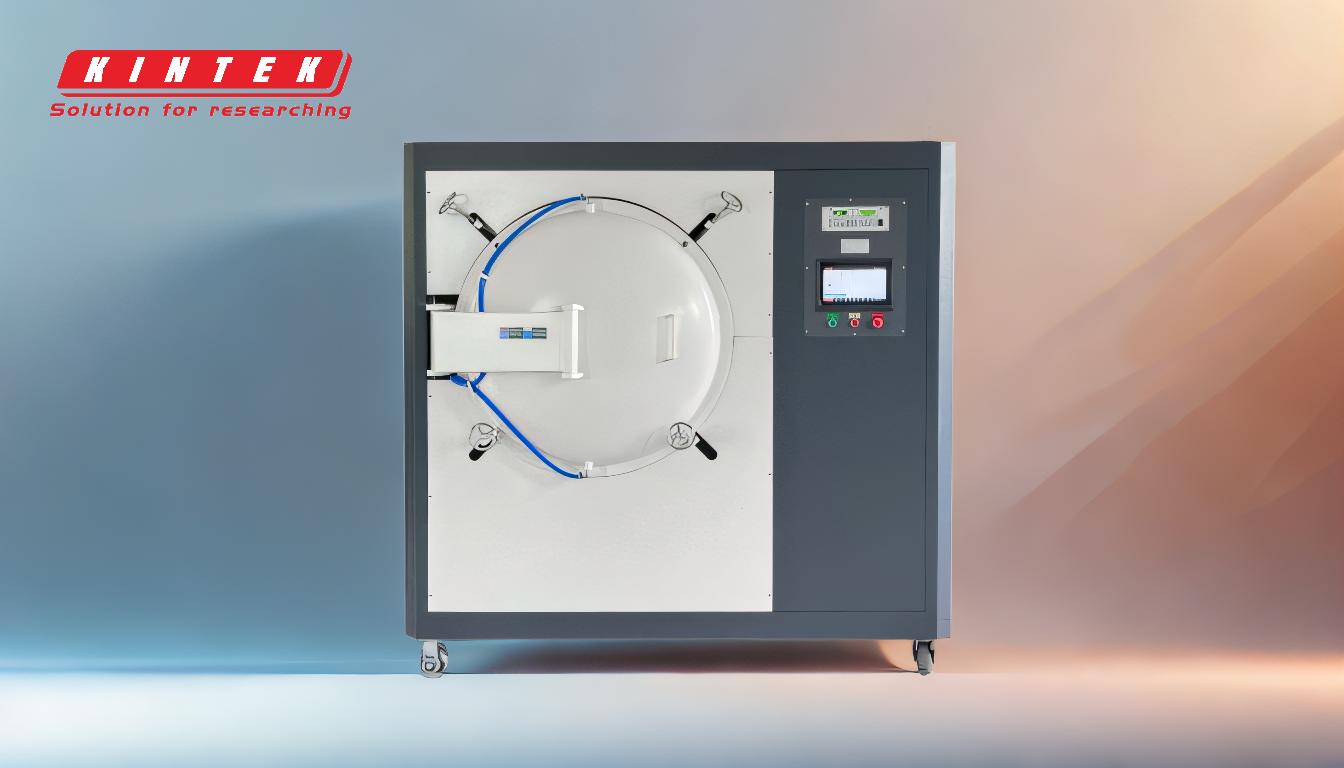
-
従来の焼結
- 説明:焼結の最も基本的な形態で、外圧をかけずに粉末材料を融点以下に加熱する。粒子は原子拡散によって結合し、気孔率が減少して密度が増加する。
- アプリケーション:セラミック、金属、プラスチックのフィルター、ベアリング、構造部品などの製造によく使用される。
- メリット:シンプルでコストパフォーマンスに優れ、さまざまな素材に適している。
- 制限事項:加圧焼結法に比べて密度や機械的特性が低くなる可能性がある。
-
高温焼結
- 説明:このプロセスでは、表面の酸化を抑え、機械的特性を向上させるために、従来の焼結よりも高温で材料を加熱することが多い。
- アプリケーション:アドバンストセラミックスや高性能金属など、高い強度と耐久性を必要とする素材に最適。
- メリット:より高い密度と強度を含む材料特性の向上。
- 制限事項:エネルギー消費量が多く、注意深く管理しないと材料が劣化する可能性がある。
-
ダイレクトメタルレーザー焼結(DMLS)
- 説明:3Dプリンティングの一種で、レーザーが粉末状の金属を選択的に焼結し、層ごとに複雑な金属部品を作る。
- アプリケーション:航空宇宙、自動車、医療産業で、複雑で高強度な金属部品の製造に使用される。
- メリット:高精度、複雑な形状の作成能力、材料の無駄の削減。
- 制限事項:従来の焼結に比べ、高価な装置と限られた材料オプション。
-
液相焼結 (LPS)
- 説明:焼結中に液相が存在し、緻密化と粒子結合を促進する。液相には永久的なものと一時的なものがある。
- アプリケーション:炭化タングステン、セラミック、一部の金属合金の製造に一般的。
- メリット:高密度化と材料特性の向上。
- 制限事項:欠陥を避けるため、液相を注意深く管理する必要がある。
-
スパークプラズマ焼結(SPS)
- 説明:通電と物理的圧縮を利用し、従来法より低温・短時間で粉末原料を急速焼結する方法。
- アプリケーション:先端セラミックス、ナノ材料、複合材料に適している。
- メリット:迅速な加工、高密度、材料特性の向上。
- 制限事項:設備コストが高く、大量生産には限界がある。
-
マイクロ波焼結
- 説明:マイクロ波エネルギーで材料を加熱・焼結するため、加熱速度が速く、温度分布が均一。
- アプリケーション:主にセラミックや一部の金属に使用される。
- メリット:エネルギー効率が高く、処理が速く、熱ストレスが少ない。
- 制限事項:マイクロ波エネルギーを効果的に吸収できる材料に限る。
-
熱間静水圧プレス(HIP)
- 説明:高温と等方加圧(あらゆる方向から均一に加圧)を組み合わせ、粉末材料を高密度化・接着する。
- アプリケーション:航空宇宙、医療用インプラント、高性能合金に使用。
- メリット:高密度で優れた機械的特性を持つニアネットシェイプ部品を製造。
- 制限事項:高い設備コストと運用コスト。
-
反応焼結
- 説明:焼結過程で粉末粒子間の化学反応が起こり、新しい化合物や相が形成されること。
- アプリケーション:先端セラミックス、金属間化合物、複合材料の製造に使用。
- メリット:ユニークな材料特性と複雑な微細構造を作り出すことができる。
- 制限事項:反応速度論と温度を正確に制御する必要がある。
-
粘性焼結
- 説明:粘性のある液相が粒子の緻密化と結合を助けるプロセスで、通常は低温で行われる。
- アプリケーション:ガラスやセラミック加工で一般的。
- メリット:処理温度を下げ、エネルギー消費量を削減。
- 制限事項:粘性相を形成しうる材料に限る。
-
真空焼結
- 説明:酸化や汚染を防ぐために真空環境で行われ、高純度材料によく使用される。
- アプリケーション:耐火金属、先端セラミックス、高性能合金に適している。
- メリット:高い材料純度と改善された機械的特性。
- 制限事項:真空装置が必要なため高価。
-
ホットプレス焼結
- 説明:熱と一軸加圧を組み合わせて粉末材料を高密度化する。従来の方法では焼結が困難な材料によく用いられる。
- アプリケーション:先端セラミックスや複合材料の製造に一般的。
- メリット:高密度で機械的特性が向上。
- 制限事項:一軸加圧のため、単純な形状に限定される。
各焼結方法にはそれぞれ独自の利点と限界があり、材料、所望の特性、アプリケーションの要件に基づいて適切なプロセスを選択することが不可欠です。これらのプロセスを理解することは、製造ワークフローを最適化し、所望の材料性能を達成するのに役立ちます。
総括表:
焼結プロセス | アプリケーション | メリット | 制限事項 |
---|---|---|---|
従来の焼結 | セラミック、金属、プラスチック | シンプルで費用対効果が高く、幅広い材料に対応 | 加圧方式に比べて密度と機械的特性が低い |
高温焼結 | アドバンスト・セラミックス、高性能金属 | 強度と密度の向上 | エネルギー消費量の増加、材料劣化のリスク |
ダイレクトメタルレーザー焼結(DMLS) | 航空宇宙、自動車、医療 | 高精度、複雑な形状、廃棄物の削減 | 高価な設備、限られた材料オプション |
液相焼結 (LPS) | タングステンカーバイド、セラミックス、金属合金 | 高密度化、特性の向上 | 液相の慎重なコントロールが必要 |
スパークプラズマ焼結(SPS) | 先端セラミックス、ナノ材料 | 迅速な加工、高密度、特性の向上 | 設備コストが高く、拡張性に限界がある |
マイクロ波焼結 | セラミック、一部の金属 | エネルギー効率、処理速度、熱応力の低減 | マイクロ波を吸収する素材に限る |
熱間静水圧プレス(HIP) | 航空宇宙、医療用インプラント | 高密度、優れた機械的特性 | 高い設備投資と運営コスト |
反応焼結 | アドバンスト・セラミックス、金属間化合物 | ユニークな材料特性、複雑な微細構造 | 反応速度論と温度の正確な制御が必要 |
粘性焼結 | ガラス、セラミック | 処理温度を下げ、エネルギー消費を削減 | 粘性相を形成する材料に限る |
真空焼結 | 耐火金属、先端セラミックス | 高い材料純度、機械的特性の向上 | 真空装置のため高価 |
ホットプレス焼結 | 先端セラミックス、複合材料 | 高密度、機械的特性の向上 | 一軸圧力のため単純な形状に限定される |
お客様のアプリケーションに適した焼結プロセスの選択にお困りですか? 専門家にご相談ください オーダーメイドのソリューションのために!