焼結は材料科学と製造における重要なプロセスであり、材料全体を溶融させることなく粉末材料を固体構造に結合させるために使用される。このプロセスでは、材料を融点以下の温度に加熱し、原子拡散によって粒子を結合させる。焼結法にはいくつかの方法があり、それぞれ特定の材料、用途、所望の特性に適している。これらの方法は、熱、圧力、電流、化学反応の使用に基づいて大別することができる。さまざまな焼結方法を理解することは、セラミック、金属、プラスチック、高度な3Dプリンティングなど、用途に応じて適切な技術を選択するために不可欠です。
キーポイントの説明
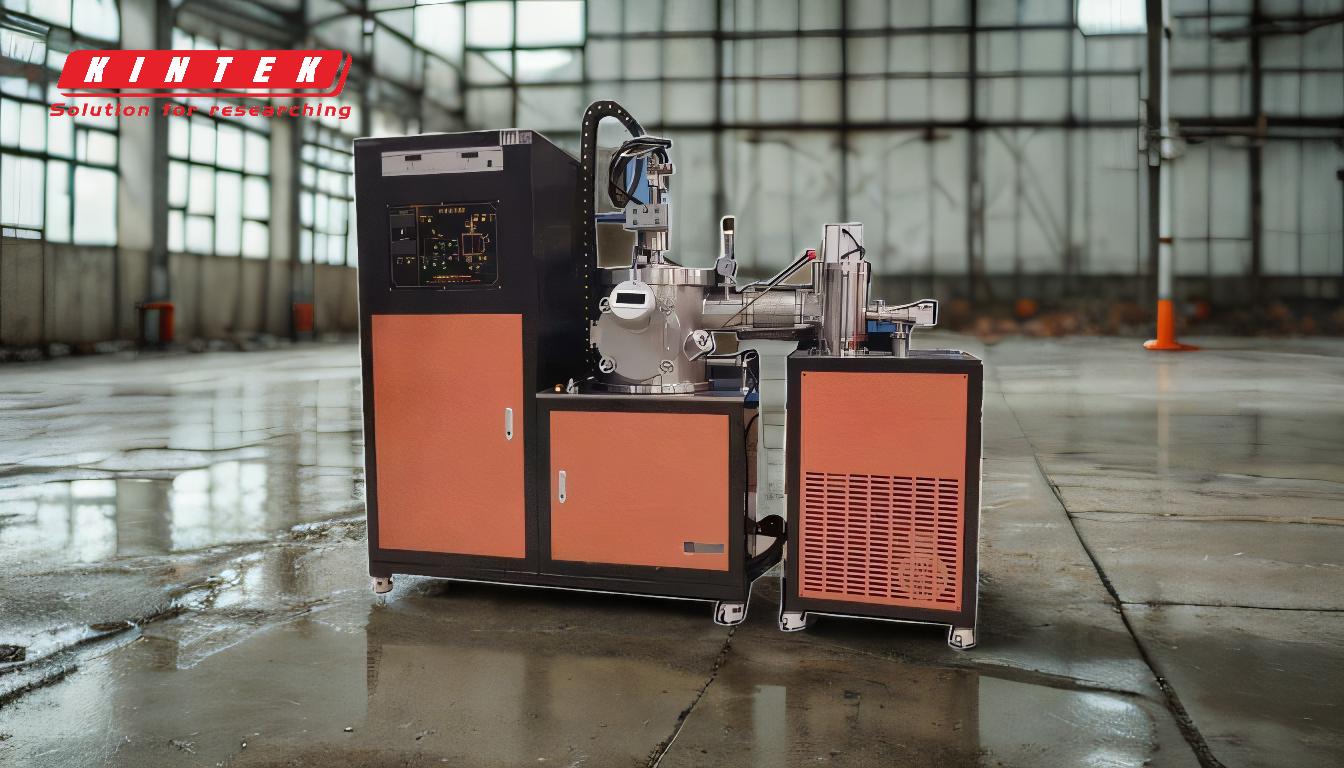
-
固体焼結
- プロセス:粉末材料を融点ぎりぎりに加熱し、原子拡散によって粒子を結合させる。
- アプリケーション:高純度、気孔率制御が要求されるセラミックスや金属によく使用される。
- メリット:液相を使用しないため、コンタミネーションのリスクを低減し、材料の完全性を保つことができる。
- 制限事項:液相や外圧を用いる方法に比べ、プロセスが遅い。
-
液相焼結 (LPS)
- プロセス:粉末材料に液相を導入し、緻密化と結合を促進する。液相は後に加熱により除去される。
-
種類:
- 永久液相焼結:最終製品に液体が残る。
- 過渡液相焼結 (TLPS):液相は一時的なもので、工程中に消失する。
- アプリケーション:炭化タングステン、セラミック、特定の金属合金の製造に使用される。
- メリット:固体焼結に比べ、緻密化が速く、接合性が向上。
- 制限事項:欠陥を避けるため、液相を注意深く管理する必要がある。
-
反応焼結
- プロセス:加熱中の粉末粒子間の化学反応に関与し、結合と緻密化をもたらす。
- アプリケーション:金属間化合物や複合材料など、その場での化学反応が必要な材料に適している。
- メリット:制御された化学反応によってユニークな材料特性を生み出すことができる。
- 制限事項:不要な相や欠陥を避けるため、反応条件を正確にコントロールする必要がある。
-
マイクロ波焼結
- プロセス:マイクロ波エネルギーを利用して粉末原料を加熱するため、従来の方法よりも高速で均一な加熱が可能。
- アプリケーション:セラミックスや先端材料に特に有効。
- メリット:急速加熱、エネルギー効率、処理時間の短縮。
- 制限事項:マイクロ波エネルギーを効果的に吸収できる材料に限る。
-
スパークプラズマ焼結(SPS)
- プロセス:通電と物理的圧縮を組み合わせ、粉末材料を急速に加熱・高密度化する。
- アプリケーション:ナノ構造セラミックスや複合材料を含む先端材料に使用。
- メリット:非常に高速なプロセスで、微細構造と特性の優れた制御が可能。
- 制限事項:高い設備コストと複雑さ。
-
熱間静水圧プレス(HIP)
- プロセス:高圧と高温を同時に加え、粉末材料を高密度化・接着する。
- アプリケーション:航空宇宙部品や医療用インプラントなどの高性能材料に使用される。
- メリット:気孔率を最小限に抑えた、完全に緻密な素材を生産。
- 制限事項:高価で特殊な装置が必要。
-
ダイレクトメタルレーザー焼結(DMLS)
- プロセス:レーザーを使って粉末状の金属を層ごとに焼結させ、複雑な形状を作り出す3Dプリンティング技術。
- アプリケーション:アディティブ・マニュファクチャリングでは、プロトタイピングや金属部品の製造に広く使用されている。
- メリット:複雑なデザインを可能にし、材料の無駄を省く。
- 制限事項:特定の金属粉末に限られ、後処理が必要。
-
従来の焼結
- プロセス:外部圧力をかけずに粉末成形体を加熱し、熱エネルギーだけで接合する。
- アプリケーション:セラミック、金属、プラスチックなど幅広い素材に使用。
- メリット:シンプルでコストパフォーマンスに優れ、様々な用途に使用できる。
- 制限事項:完全な高密度化が必要な高性能素材には、速度が遅く、効果も低い。
-
高温焼結
- プロセス:表面の酸化を抑え、機械的特性を向上させるために高温で実施。
- アプリケーション:耐火金属のような高い強度と耐久性を必要とする材料に適している。
- メリット:材料特性を向上させ、気孔率を減少させる。
- 制限事項:特殊な炉とエネルギー集約的なプロセスを必要とする。
-
水素保護と真空焼結
- プロセス:酸化や汚染を防ぐため、制御された雰囲気(水素または真空)で実施。
- アプリケーション:チタンや特定の合金など、デリケートな素材に使用される。
- メリット:材料の純度を維持し、機械的特性を向上させる。
- 制限事項:特殊な設備と管理された環境を必要とする。
各焼結方法にはそれぞれ独自の利点と限界があり、材料、所望の特性、用途要件に基づいて適切な技術を選択することが不可欠です。例えば、スパークプラズマ焼結は、急速な高密度化を必要とする先端材料に理想的であり、液相焼結は、接合の促進が有効な材料に適している。これらの方法を理解することで、メーカーや研究者はプロセスを最適化し、材料製造において望ましい結果を得ることができる。
総括表:
焼結方法 | プロセス | アプリケーション | メリット | 制限事項 |
---|---|---|---|---|
固体焼結 | 原子拡散のための融点以下の加熱 | セラミックス、高純度を必要とする金属 | 液相がないためコンタミネーションが少ない | より遅いプロセス |
液相焼結 (LPS) | 液相を導入し、迅速な接着を実現 | タングステンカーバイド、セラミックス、金属合金 | より速い高密度化と接着 | 慎重な液相制御が必要 |
反応焼結 | 加熱時の化学反応 | 金属間化合物、複合材料 | ユニークな素材特性 | 正確な反応制御が必要 |
マイクロ波焼結 | マイクロ波エネルギーによる急速加熱 | セラミックス、先端材料 | エネルギー効率の高い均一な暖房 | マイクロ波を吸収する素材に限る |
スパークプラズマ焼結(SPS) | 電流と圧縮の組み合わせ | ナノ構造セラミックス、複合材料 | 極めて高速で精密な微細構造制御 | 高い設備コスト |
熱間静水圧プレス(HIP) | 高温高圧による高密度化 | 航空宇宙部品、医療用インプラント | 完全高密度素材 | 高価な専用機器 |
ダイレクトメタルレーザー焼結(DMLS) | レーザーによる金属部品の3Dプリント | 積層造形、プロトタイピング | 複雑なデザイン、廃棄物の削減 | 特定の金属に限定、後処理が必要 |
従来の焼結 | 外圧なしの加熱 | セラミック、金属、プラスチック | シンプルでコストパフォーマンスが高い | 高性能素材には遅くて効果的でない |
高温焼結 | 酸化を抑えるための高温化 | 耐火金属 | 材料特性の向上 | エネルギー集約型の特殊炉 |
水素/真空焼結 | 酸化を防ぐために管理された雰囲気 | チタン、高感度合金 | 純度の維持、機械的特性の向上 | 専用機材が必要 |
プロジェクトに適した焼結方法の選択にお困りですか? 専門家にご相談ください !