PVD (物理蒸着) コーティング プロセスは、主に金属などのさまざまな材料に薄く耐久性のあるコーティングを施すために使用される高度な技術です。プロセスの所要時間は、必要なコーティングの厚さ、ワークピースのサイズ、使用する特定の種類の PVD プロセスなどの要因に応じて、通常は 30 分から 2 時間の範囲で大きく異なります。コーティングの厚さは通常 0.25 ミクロンから 5 ミクロンの範囲であり、プロセスには蒸発、反応、堆積といういくつかの重要なステップが含まれます。各ステップは、硬度、色、耐腐食性や酸化性などのコーティングの最終特性を決定する上で重要な役割を果たします。
重要なポイントの説明:
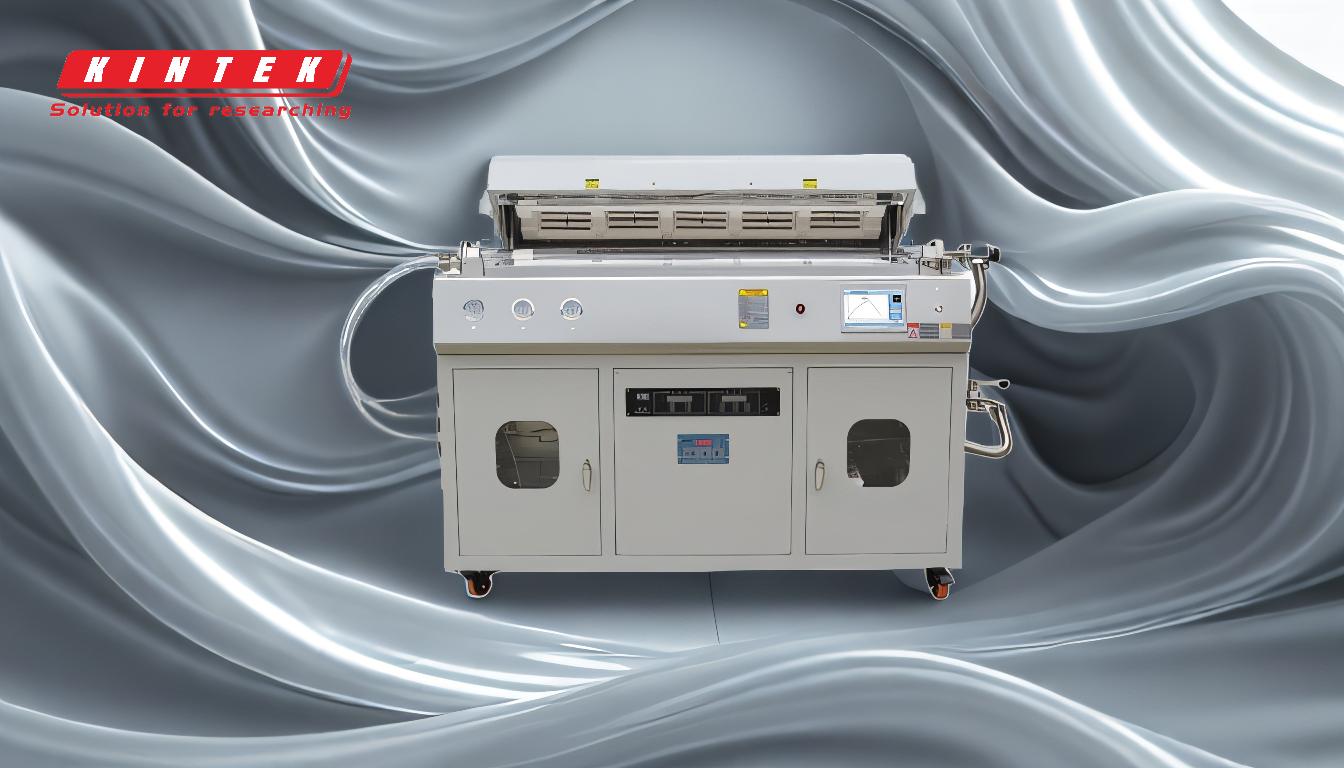
-
PVD コーティングプロセスの期間:
- PVD コーティング プロセスには通常 30 分から 2 時間かかります。小さいまたは単純なアイテムの場合は所要時間は短くなりますが、大きいまたはより複雑なアイテムの場合は時間がかかる場合があります。
- 必要な時間は希望するコーティングの厚さによっても異なりますが、コーティングが厚いほど処理時間は長くなります。
-
コーティングの厚さ:
- PVD コーティングは通常、0.25 ミクロンから 5 ミクロンの範囲で非常に薄いです。この薄い層は、硬度、耐食性、美的外観などの特性を大幅に向上させるのに十分です。
- コーティングの厚さは、コーティングされた材料の全体的な耐久性と性能を決定する重要な要素です。
-
PVD コーティングプロセスの種類:
- スパッタコーティング: 高エネルギーイオンをターゲット材料に衝突させて原子を放出し、その原子を基板上に堆積させます。
- 熱蒸発: 熱を使用してコーティング材料を蒸発させ、基板上に凝縮させます。
- 電子ビーム蒸着: 電子ビームを利用してコーティング材料を加熱し、蒸発させます。
- イオンプレーティング: 蒸発とイオン衝撃を組み合わせて、コーティングの密着性と密度を高めます。
- 各プロセスには独自の特徴と利点があり、さまざまな用途や材料に適しています。
-
PVD コーティングプロセスの手順:
- 気化: ターゲット物質は、スパッタリングや蒸着などのさまざまな方法によって蒸気に変換されます。
- 反応: 蒸発した材料はチャンバー内のガスと反応して、硬度や色などのコーティングの特性を決定する化合物を形成します。
- 堆積: 気化して反応した材料が基板上に堆積し、薄く均一なコーティングが形成されます。
-
特性と用途:
- PVD コーティングは耐腐食性と酸化性に優れているため、過酷な環境での使用に最適です。
- コーティングの硬度は耐久性において重要な要素であり、TiN (窒化チタン) などの材料は基材の疲労限界と耐久性を大幅に向上させます。
- PVD コーティングは一般的にステンレス鋼に適用され、表面処理に応じて、研磨、ブラッシュ仕上げ、サテン、マットなどのさまざまな仕上げを提供します。
-
表面の準備:
- 下地の表面状態は、希望の仕上がりを実現するために不可欠です。研磨または鏡面は研磨 PVD 仕上げに使用され、ブラッシュまたはサテン表面はサテンまたはマット仕上げに使用されます。
- PVD コーティングは表面の欠陥を平らにしたり埋めたりしないため、コーティングプロセスの前に基板を適切に準備する必要があります。
これらの重要なポイントを理解することは、特定の用途に適切な PVD コーティング プロセスとパラメータを選択し、コーティングされた材料の最適な性能と寿命を保証するのに役立ちます。
概要表:
側面 | 詳細 |
---|---|
間隔 | ワークピースのサイズとコーティングの厚さに応じて、30 分から 2 時間。 |
コーティングの厚さ | 0.25 ミクロンから 5 ミクロンで、硬度、耐食性などを提供します。 |
プロセスの種類 | スパッタコーティング、熱蒸着、電子ビーム蒸着、イオンプレーティング。 |
主要なステップ | 蒸発、反応、堆積。 |
アプリケーション | 金属の耐食性、硬度の向上、美しい仕上げ。 |
PVD コーティングで材料を最適化します— 今すぐ専門家にお問い合わせください カスタマイズされたソリューションを実現します。