スパッタリング・プロセスは、基板上に材料の薄膜を堆積させるために広く使われている技術である。反応室内を真空にし、アルゴンのような不活性ガスを導入し、ガスをイオン化してプラズマを形成する。プラズマからの高エネルギーイオンがターゲット材料に衝突し、原子が放出されて基板上に堆積し、薄膜が形成される。このプロセスは高度に制御可能で、さまざまな材料を正確な厚みと均一性で成膜することができる。主な手順には、真空を作り、ガスを導入してイオン化し、プラズマを発生させ、イオンを加速してターゲット原子を基板上にスパッタすることが含まれる。
キーポイントの説明
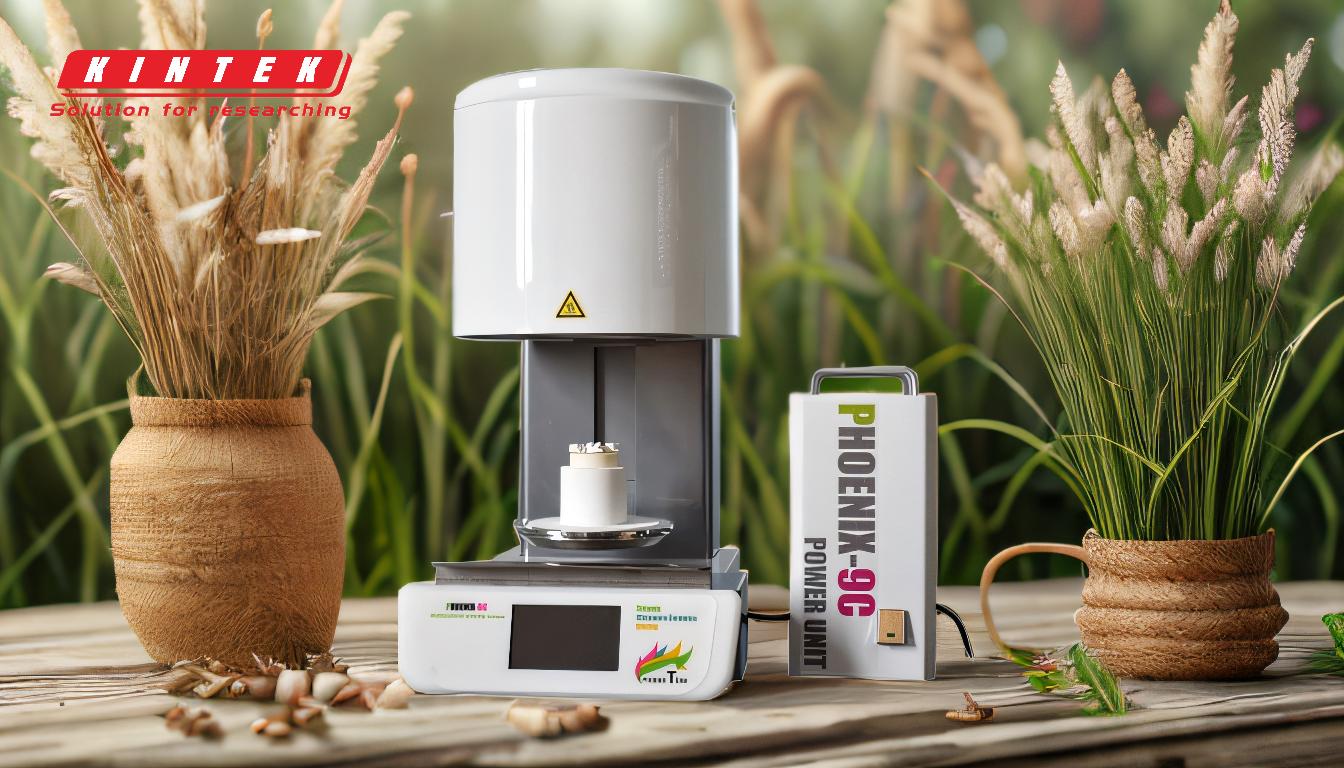
-
室内を真空にする:
- スパッタプロセスの最初のステップは、反応チャンバー内を真空にすることである。これは内圧を1Pa(0.0000145psi)程度まで下げ、水分や不純物を排除するものである。真空環境は、残留ガスによる汚染を防ぎ、成膜表面を清浄に保つために極めて重要である。また、真空にすることで、不要な反応を最小限に抑え、スパッタリングプロセスをより適切に制御することができます。
-
不活性ガスの導入:
- 真空が確立されると、不活性ガス(通常はアルゴン)がチャンバー内に導入される。アルゴンが選ばれるのは、化学的に不活性であり、ターゲット材料や基板と反応しないからである。ガスは、通常10-1~10-3mbarの範囲に制御された圧力で導入される。この低圧環境は、次のステップで生成されるプラズマの安定性を維持するために不可欠である。
-
プラズマの生成:
- チャンバー全体に高電圧(通常3~5kV)を印加してアルゴンガスをイオン化し、プラズマを発生させる。プラズマは正電荷を帯びたアルゴンイオンと自由電子で構成される。プラズマを閉じ込め、イオンの密度を高めるのに役立つ磁場が存在すると、イオン化プロセスが促進されることが多い。プラズマはターゲット材料をスパッタリングするために使用される高エネルギーイオンの供給源であるため、このステップは非常に重要である。
-
ターゲットに向かってイオンを加速する:
- 蒸着される原子の供給源であるターゲット材料は負に帯電している(陰極)。プラズマ中のプラスに帯電したアルゴンイオンは、マイナスに帯電したターゲットに引き寄せられる。これらのイオンがターゲットと衝突すると、その運動エネルギーがターゲット原子に伝達される。このエネルギー伝達は、ターゲット表面から原子を外すのに十分であり、スパッタリングとして知られるプロセスである。
-
ターゲット原子の放出と堆積:
- スパッタされた原子は、中性粒子の形でターゲット表面から放出される。これらの粒子は真空チャンバーを横切り、基板に運ばれる。基板は通常ターゲットに対向して配置され、スパッタされた原子はその表面に凝縮して薄膜を形成する。成膜プロセスは高度に制御されており、正確な膜厚と均一性が得られる。
-
薄膜の形成:
- 基板に到達したスパッタ原子は基板表面に付着し、薄膜を形成する。薄膜の厚み、均一性、密着性などの特性は、スパッタ原子のエネルギー、基板温度、チャンバー内の圧力など、さまざまな要因に影響される。基材は、コーティングの所望の特性に応じて、150℃から750℃の範囲の温度に加熱することができる。この加熱は、蒸着膜の密着性と品質を向上させるのに役立つ。
-
磁場の役割:
- 一部のスパッタリング装置では、磁場を用いてイオン化プロセスを促進し、プラズマをターゲットの周囲に閉じ込める。これはマグネトロンスパッタリングとして知られている。磁場はプラズマの密度を高め、ターゲットへのイオン衝突率を高める。その結果、より効率的なスパッタリングプロセスが実現し、より高い成膜速度が可能になる。
-
制御と最適化:
- スパッタプロセスは高度に制御可能であり、成膜を最適化するためにさまざまなパラメーターを調整できる。これらのパラメーターには、印加電圧、不活性ガスの圧力、磁場の強さ、基板温度などが含まれる。これらの変数を注意深く制御することで、導電性、光学的透明性、機械的強度など、特定の特性を持つ薄膜を成膜することができる。
-
スパッタリングの応用:
- スパッタリングは、半導体、光学コーティング、薄膜太陽電池の製造など、幅広い用途で使用されている。また、工具用の硬質コーティングや消費者製品の装飾用コーティングの製造にも使用されている。多種多様な材料を精密に制御しながら成膜できるスパッタリングは、現代の製造および研究において多用途かつ貴重な技術となっている。
要約すると、スパッタリング・プロセスは、複雑だが高度に制御された方法で、基板上に材料の薄膜を堆積させる。真空を作り、不活性ガスを導入し、プラズマを発生させ、高エネルギーイオンを使ってターゲット材料から基板上に原子をスパッタリングする。このプロセスは、電圧、圧力、磁場、基板温度など、さまざまなパラメータに影響され、所望の膜特性を得るために調整することができる。スパッタリングは、エレクトロニクスから光学まで幅広い産業で広く利用されており、現代の製造業において重要な技術となっている。
総括表
ステップ | 説明 |
---|---|
1.真空を作る | 不純物を排除し、クリーンな成膜を確実にするため、チャンバー圧力を~1Paに下げる。 |
2.不活性ガスの導入 | プラズマの安定性を維持するため、10-1~10-3mbarのアルゴンガスを加える。 |
3.プラズマの生成 | 3~5kVを印加してアルゴンガスをイオン化し、イオンと電子のプラズマを生成する。 |
4.イオンを加速する | プラスに帯電したイオンがマイナスに帯電したターゲット物質に衝突する。 |
5.ターゲット原子の放出 | ターゲット原子をスパッタし、基板上に堆積させる。 |
6.薄膜の形成 | スパッタされた原子が基板上に凝縮し、均一な薄膜が形成される。 |
7.磁場を利用する | 磁場はプラズマ密度を高め、スパッタリング効率を向上させる(マグネトロンスパッタリング)。 |
8.パラメータの最適化 | 電圧、圧力、磁場、基板温度を調整し、望ましい膜特性を得る。 |
9.用途 | 半導体、光学コーティング、太陽電池、ハードコーティングに使用されます。 |
スパッタリングが薄膜アプリケーションにどのような革命をもたらすかをご覧ください。 今すぐ専門家にお問い合わせください !