焼結は材料科学における重要なプロセスであり、粉末材料を融点以下の温度まで加熱して固体塊を形成する。圧力は、気孔率を減らし、焼結時間を短縮し、最終製品の機械的特性を向上させることにより、焼結プロセスを強化する上で重要な役割を果たします。圧力を加えることで、粒子はより効率的に再配列され、より良い緻密化と粒子間のより強い結合につながります。これは、通常の条件では焼結が困難な材料に特に有効である。圧力、温度、および粒子径や組成などの他の要因の相互作用が、焼結プロセスの全体的な有効性を決定します。
キーポイントの説明
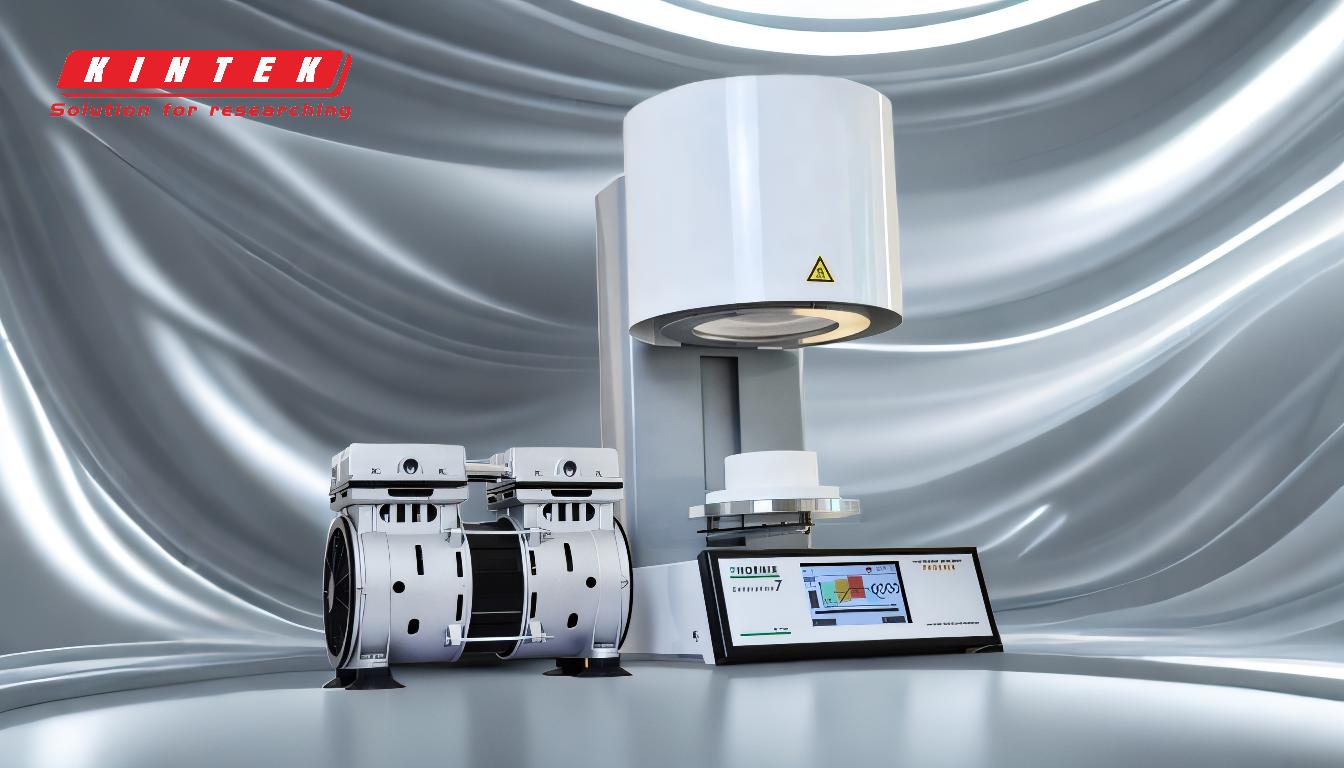
-
焼結における圧力の役割:
- 融合の原動力:圧力は、特にホットプレスのような技術では、焼結中の追加的な駆動力として作用します。これは、標準的な条件では焼結が困難な材料に特に有益です。
- 気孔率の低減:圧力を加えることで、材料内のボイドや気孔をなくし、より緻密でコンパクトな最終製品に仕上げることができます。
- 焼結時間の短縮:圧力は、粒子の再配列と結合を促進することによって焼結プロセスを加速し、所望の材料特性を達成するために必要な全体的な時間を短縮します。
-
圧力と温度の相互作用:
- 高密度化:より高い温度と加圧を組み合わせると、材料の圧縮を著しく高めることができる。これは、圧力が粒子の再配列を助け、温度が焼結に必要な拡散プロセスを促進するためである。
- 液相の制御:焼結プロセスによっては、液相が形成されることがあります。圧力は、この液相の量と分布を制御するのに役立ち、これは所望の材料特性を達成するために極めて重要である。
-
機械的特性への影響:
- 引張強度の向上:焼結中に圧力を加えることで、より均質な微細構造が得られ、その結果、材料の引張強度が向上する。
- 曲げ疲労強度の向上:加圧焼結された材料は、繰り返し荷重に対してより優れた耐性を示し、高い耐久性が要求される用途に適しています。
- より高い衝撃エネルギー:圧力印加によって達成される緻密化により、より高い衝撃エネルギーを持つ材料となり、破壊に対する耐性が高くなる。
-
プロセスパラメーターとその最適化:
- 焼結温度:温度は、材料が溶融しないように注意深く制御する必要があるが、粒子の結合を可能にするために十分に加熱される。加圧することで必要な焼結温度を下げることができ、エネルギー効率に優れたプロセスになります。
- 加熱速度:熱応力を回避し、均一な緻密化を確保するためには、加熱速度の制御が不可欠である。圧力は、均一な粒子の再配列を促進することにより、一定の加熱速度を維持するのに役立ちます。
- 粒子径と組成:小さな粒子と均質な組成物は、表面積が高く欠陥が少ないため、加圧下でより効果的に焼結し、より優れた緻密化につながる。
-
圧力を利用する技術:
- ホットプレス:圧力と熱を同時に加える技術で、特に焼結が困難な材料に有効。機械的特性に優れた高密度製品が得られる。
- スパークプラズマ焼結(SPS):SPSは電流と圧力を利用して急速焼結を実現する。これらの要素が組み合わさることで、微細な組織と強化された特性を持つ材料の製造が可能になります。
-
工業焼結における実際的考察:
- 風量と真空制御:産業環境では、効果的な焼結のために空気量と真空レベルの制御が重要です。圧力印加は、特に大規模な操業において、焼結に最適な条件を維持するのに役立ちます。
- 層厚と機械速度:材料が均一に焼結されるように、材料層の厚さと焼結機の速度を最適化する必要があります。圧力は安定した層厚と速度を達成するのに役立ち、より良い品質の製品につながります。
要約すると、圧力は焼結プロセスにおける重要な要素であり、緻密化、機械的特性、およびプロセス全体の効率に影響を与えます。圧力、温度、その他のパラメータ間の相互作用を理解し最適化することで、メーカーは特定の用途に合わせた高品質の焼結材料を製造することができます。
総括表
側面 | 圧力の影響 |
---|---|
気孔率の減少 | ボイドや気孔をなくし、より緻密な材料を実現します。 |
焼結時間 | 粒子の再配列を促進し、全体的な処理時間を短縮します。 |
機械的特性 | 引張強度、曲げ疲労強度、衝撃エネルギーを向上させる。 |
温度効率 | 必要な焼結温度を下げ、エネルギーを節約します。 |
技術 | ホットプレスとスパークプラズマ焼結(SPS)は、優れた結果を得るために圧力を利用します。 |
圧力がどのように焼結プロセスを最適化するかをご覧ください。 今すぐ専門家にお問い合わせください !