マグネトロンスパッタリングは物理的気相成長(PVD)技術の一つで、基板上に薄膜材料を堆積させるために広く使用されている。真空環境で作動し、ターゲット材料(陰極)に高エネルギーイオンが照射され、ターゲット表面から原子が放出される。放出された原子は真空中を移動し、基板上に堆積して薄膜を形成する。このプロセスは、強力な磁場と電場を発生させて電子をターゲット表面付近に閉じ込め、イオン化とプラズマ密度を高めるマグネトロンを使用することで強化される。その結果、効率的なスパッタリングと高品質な成膜が可能になり、光学、エレクトロニクス、工業用コーティングなどの用途に適している。
ポイントを解説
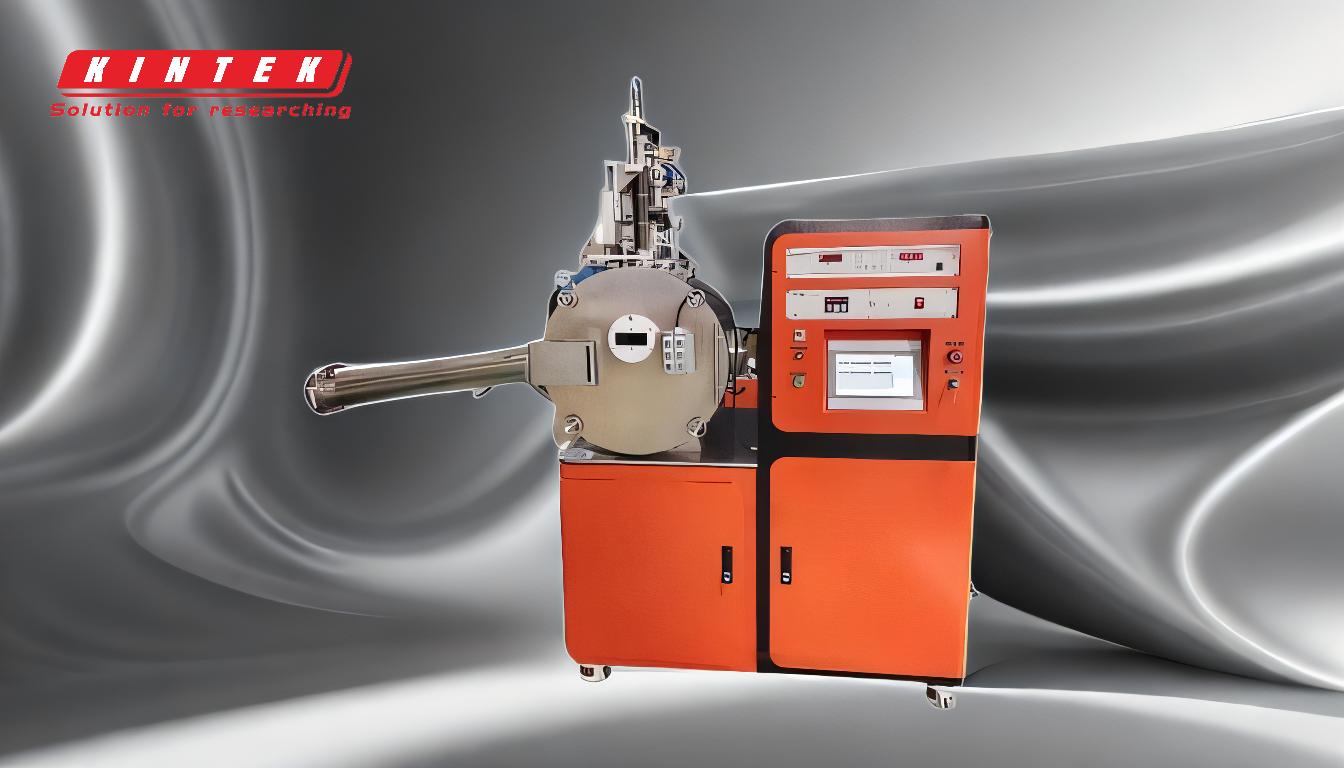
-
スパッタリングの基本メカニズム:
- マグネトロンスパッタリングでは、通常アルゴンのような不活性ガスから発生する高エネルギーイオンをターゲット材料に照射する。
- イオンは、ターゲット(カソード)に印加される負電圧によってターゲットに向かって加速される。
- イオンはターゲットに衝突すると、運動エネルギーをターゲット原子に伝え、原子を表面から放出させる(スパッタリング)。
-
マグネトロンの役割:
- マグネトロンはターゲット表面付近に磁場を発生させ、電子を円軌道に閉じ込める。
- この閉じ込めにより、プラズマ中の電子の滞留時間が長くなり、ガス原子との衝突が増え、イオン化率が高くなる。
- イオン化が進むと、スパッタリングに利用できるイオンの密度が高まり、プロセスの効率が向上する。
-
プラズマの形成と維持:
- スパッタリングプロセスは、不活性ガス(アルゴンなど)で満たされた真空チャンバー内で行われる。
- 電気エネルギーを用いてガスをイオン化し、イオン、電子、中性原子からなるプラズマを生成する。
- スパッタリング中にターゲットから放出された二次電子はガス原子と衝突し、プラズマの持続を助ける。
-
薄膜の成膜:
- ターゲットから放出された原子(スパッタ原子)は真空中を移動し、基板上に堆積する。
- 蒸着された原子は、高密度、密着性、制御された厚みなどの特性を持つ、薄く均一な膜を形成する。
- このプロセスは、金属、合金、絶縁体など幅広い材料の成膜に適しています。
-
マグネトロンスパッタリングの利点:
- 低い蒸着温度:温度に敏感な基板に適しています。
- 高品質フィルム:緻密で均一、欠陥のないコーティングが可能。
- 汎用性:金属、セラミックス、ポリマーなど、さまざまな材料を蒸着できる。
- 拡張性:大面積の基材を均一な厚みでコーティングできる。
-
用途:
- 光学コーティング:反射防止膜、反射膜、透明導電膜に使用。
- エレクトロニクス:半導体、センサー、ディスプレイ用薄膜の成膜。
- 工業用コーティング:耐摩耗性、耐食性、装飾性コーティングを提供。
-
プロセス制御:
- ガス圧、ターゲット電圧、磁場強度、基板温度などのパラメーターを調整し、膜特性を最適化できる。
- このプロセスは高度に制御可能で、膜厚、組成、微細構造を精密に調整できる。
-
課題と考察:
- イオンボンバードメントの局所的な性質により、ターゲットの利用率が不均一になる可能性がある。
- このプロセスには高真空環境が必要であり、その維持にはコストがかかる。
- 望ましい膜特性を得るためには、ターゲット材料とプロセスパラメーターを慎重に選択する必要がある。
これらの重要なポイントを理解することで、コーティング技術としてのマグネトロンスパッタリングの複雑さと多様性を理解することができ、様々な工業的および科学的応用において貴重なツールとなる。
総括表:
アスペクト | 詳細 |
---|---|
メカニズム | 高エネルギーのイオンをターゲットに衝突させ、原子を放出させて成膜する。 |
マグネトロンの役割 | 電子をターゲットの近くに閉じ込め、イオン化と効率を高める。 |
プラズマ形成 | 不活性ガスをイオン化してプラズマを生成し、スパッタリングプロセスを維持する。 |
利点 | 低温成膜、高品質フィルム、汎用性、スケーラビリティ。 |
用途 | 光学コーティング、エレクトロニクス、工業用コーティング |
プロセス制御 | 正確なフィルム特性のための調整可能なパラメータ。 |
課題 | 不均一なターゲット使用率、高い真空コスト、材料選択。 |
マグネトロンスパッタリングの活用にご興味がおありですか? 今すぐご連絡ください までご連絡ください!