はじめに
目次
冷間等方圧加圧(CIP)は、セラミック、金属加工、医薬品など、さまざまな産業で広く使用されている製造プロセスです。これは、フレキシブルな金型や袋の中に入れた材料に、あらゆる方向から均等な圧力を加えるものである。このプロセスは、均一な密度を達成し、複雑な形状の部品を成形するのに役立ちます。CIPは、より複雑な形状の成形が可能で、均一な粒子充填による歪みや亀裂の発生を抑えるなど、従来の一軸ダイプレスに比べていくつかの利点があります。このブログ記事では、冷間等方圧プレスの用途、利点、限界について掘り下げていきます。
冷間静水圧プレスの概要
冷間等方圧加圧の説明
冷間等方圧加圧(CIP)は、粉末材料にあらゆる方向から均等な圧力を加える材料加工技術です。この工程は、粉末を圧縮して固体塊にし、ハンドリングや更なる加工に十分な強度を持つ生の部品を作るために使用されます。
ウェットバッグ静水圧プレスとドライバッグ静水圧プレスの違い
冷間等方圧加圧のバリエーションの1つに、ウェットバッグ技術があります。このプロセスでは、粉末は金型に充填され、圧力容器の外でしっかりと密閉されます。その後、金型を容器内の高圧流体に浸し、静水圧を加えて粉末を形状に圧縮します。ウェットバッグ技術は、多品種少量生産に適している。
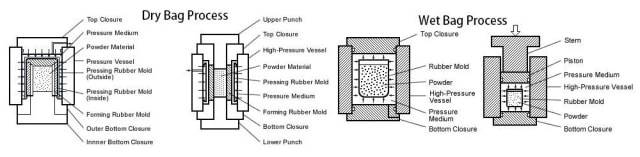
一方、ドライバッグ等方圧加圧では、圧力容器内に一体化した金型を作ります。パウダーを金型に入れ、金型を密閉し、圧力を加えてパウダーを圧縮します。このプロセスでは、金型を別の液体に浸す必要がないため、自動化が容易になる。
工程における粉末の品質と金型設計の役割
冷間静水圧プレスで使用するパウダーの品質は、最終製品に重要な役割を果たします。パウダーは、効率的で均一な圧縮を保証するために、適切な粒度分布、流動性、密度を持つ必要があります。さらに、使用する金型やバッグを含む金型設計は、パウダー材料と希望する形状の特定の要件に対応するよう慎重に設計する必要があります。
適切な金型設計と粉末の品質は、最終製品で望ましい密度と強度を達成するために不可欠です。これは、高品質で信頼性の高い部品が重要な航空宇宙、自動車、医療などの産業で特に重要です。
要約すると、冷間等方圧加圧は、粉末材料を圧縮して固体部品にすることができる汎用性の高い材料加工技術です。ウェットバッグ技術とドライバッグ技術のどちらを選択するかは、具体的な生産要件によって決まります。さらに、粉末の品質と金型設計は、最終製品で望ましい結果を確保する上で重要な役割を果たします。
冷間静水圧プレスの種類
ウェットバッグ技術の詳細
冷間静水圧プレスのウェットバッグ法では、粉末材料を金型に充填し、圧力容器の外に密閉します。充填された金型は、圧力容器内の圧力流体中に浸漬されます。金型の外面に静水圧をかけ、粉末を圧縮して固体の塊にする。
この方法は他の冷間静水圧プレスほど一般的ではありませんが、世界中で3000以上のウェットバッグプレスが使用されています。湿式バッグには様々なサイズがあり、直径50mmから2000mmまである。
ウェットバッグ・テクノロジーを使って材料を加工する場合、5分から30分かかることがあり、比較的時間のかかるプロセスである。しかし、大容量ポンプや改良されたローディング機構を使用することで、プロセスをスピードアップすることができる。
ドライバッグ・プレス技術の説明
一方、ドライバッグ・プレス法では、圧力容器と一体化した金型を作る。この工程では、粉末を金型に入れ、密閉します。圧力が加えられ、出来上がった部品が排出される。
ウェットバッグ技術と比べ、ドライバッグプロセスは自動化に適しており、高い生産率で長時間の成形品をプレスするのに適している。金型が圧力容器に組み込まれているため、浸漬工程が不要となり、より効率的な方法となる。
両工法の用途比較
ウェットバッグ技術とドライバッグ技術のどちらを選択するかは、アプリケーションの具体的な要件によって決まります。ウェットバッグ技術は、多品種少量生産、大型製品のプレスに最適です。複雑な形状の作成が可能で、高いグリーン密度を実現します。
一方、ドライバッグプレスは自動化や高生産量に適している。製造工程への組み込みが容易で、浸漬工程が不要なため、生産時間が短縮される。
まとめると、ウェットバッグとドライバッグのどちらの技術にも利点があり、異なる用途で使用されている。この2つのどちらを選択するかは、希望する形状、生産量、必要な自動化のレベルなどの要因によって決まります。
一軸ダイプレスに対する冷間等方圧プレスの利点
より複雑な形状の成形が可能
冷間等方圧プレス(CIP)には、一軸ダイプレスと比較して、より複雑な形状を成形できるという利点があります。CIPでは、金型の表面全体に均一に圧力がかかるため、複雑で細かい形状の成形が可能です。特に、一軸ダイプレスでは困難な複雑な形状やデザインの部品を製造する場合に有効です。

均一な粒子充填による歪みや割れの低減
冷間等方圧加圧の一軸ダイプレスに対する大きな利点の一つは、最終製品の歪みと割れの低減である。CIPでは、圧力が均一にかかるため、粒子充填がより均一になり、圧力勾配が減少します。これは、より均一な密度分布につながり、完成部品の歪みや割れの可能性を低減します。この利点は、複雑な形状の部品を扱う場合に特に重要である。
技術的な考察によると、CIPは所定の成形圧力でより均一な密度が得られるため、脆い粉末や微細な粉末に特に適しています。さらに、CIPでは金型壁の摩擦がないため、潤滑油の除去に伴う問題がなく、より高い圧粉密度が可能になります。
さらに、CIPではグリーン密度が均一なため、焼結中の収縮がより均一になるという利点があります。これは、良好な形状制御を維持し、最終製品で均一な特性を達成するために不可欠です。さらに、CIPは一軸ダイプレスのようなワックスバインダーを必要としないため、脱ワックス作業が不要になります。
まとめると、一軸ダイプレスを上回る冷間等方圧加圧の利点には、より複雑な形状の成形が可能なこと、均一な粒子充填による歪みやクラックの減少などがあります。これらの利点により、CIPは複雑な形状の部品を製造し、高品質で均質な製品を実現するのに適した方法となっています。
複雑な形状の部品製造における冷間等方圧加圧法
大量生産におけるCIPと射出成形の比較
一軸ダイプレスの形状能力を超える複雑な形状の部品が必要とされ、大量生産のスループットが必要とされる場合、CIPと射出成形の2つが主な選択肢となります。CIPは、1934年にDaubenmeyerによって、アルミナ・セラミックスを製造するための文献で報告された最初のハイテク方法です。実際、スパークプラグ絶縁体は、おそらく世界最大の生産量を誇るCIPセラミック部品です。年間30億個製造されるスパークプラグ絶縁体のかなりの割合がCIP処理されています。一軸ダイスプレスと同様、CIPの原料は一般的に、単純な粉砕されたバイエルアルミナ、粉砕され噴霧乾燥されたバイエルアルミナ、まれに噴霧乾燥されたハイテクSolGelナノ粉末である。しかし、一般的にCIPは、工業的には射出成形ほど一般的ではありません。CIPは一般的に、非常に複雑な形状が要求され、何らかの理由で射出成形が実用的でない場合にのみ使用される。
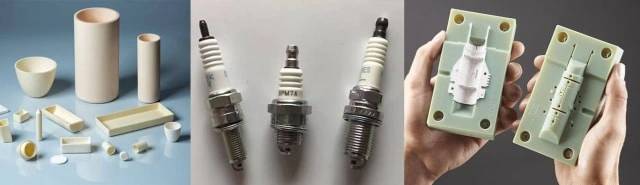
アルミナ・セラミックス製造におけるCIP使用の歴史的概観
冷間静水圧プレス(CIP)は、金属やセラミック部品を製造するための、粉末ベースのニアネットシェイプ技術である。CIPは、セラミックスの加工には一般的に使用されていますが、金属にはあまり広く使用されていません。しかし、プロセス能力と粉末冶金における最近の発展により、高性能金属部品の製造にCIPがますます使用されるようになっています。固体処理、均一な微細構造、形状の複雑さ、低工具コスト、プロセスの拡張性などの利点により、CIPは金属にとって実行可能な処理ルートとなっている。さらに、材料の無駄を最小限に抑えてネットシェイプに近い部品を製造できる可能性があるため、航空宇宙や自動車などのニッチな用途で、このプロセスがより広く受け入れられるようになりました。
スパークプラグ絶縁体製造におけるCIPの利用
何十年もの間、冷間等方圧プレス(CIP)は世界中のメーカーに利用され、成功を収めてきました。CIPは、金属粉末やセラミック粉末を圧密し、圧延、機械加工、焼結などの処理を施した「グリーン」な部品を製造するために使用されます。
一般的な圧力は1,035~4,138bar(15,000~60,000psi)、周囲温度は93℃までで、CIPはセラミックの理論密度の95%を達成できます。
高性能部品のための実証済みのプロセス 冷間静水圧プレスの一般的な用途には、セラミック粉末の圧密、黒鉛の圧縮、耐火物や電気絶縁体、歯科用や医療用のその他のファインセラミックなどがあります。
この技術は、スパッタリングターゲットのプレス、シリンダーヘッドの摩耗を最小限に抑えるためのエンジンバルブ部品のコーティング、電気通信、電子機器、航空宇宙、自動車などの新しい用途に拡大しています。
冷間等方圧プレス
EPSIの冷間等方圧プレス(CIP)は、圧延、機械加工、焼結の前の予備的な緻密化ステップで、未焼結またはグリーン染料成形の金属粉末コンポーネントを製造するために使用されます。当社のCIPシステムは、航空宇宙、軍事、工業、医療産業向けの完璧な部品を効率的に生産するために、世界中の企業で使用されています。当社の冷間等方圧プレスは、さらなるハンドリングや焼結に必要な十分なグリーン強度を保ちながら、部品を容易に取り外すことができるように設計されていることを、世界中の技術リーダーが知っています。
冷間等方圧プレス
冷間等方圧プレスは、プレス金型の高いイニシャルコストを正当化できない部品や、非常に大きい、または複雑な成形品が必要な部品の製造に有利です。金属、セラミック、プラスチック、複合材料など、さまざまな粉末を商業規模で静水圧プレスすることができます。成形に必要な圧力は、5,000 psi未満から100,000 psi(34.5~690 MPa)以上の範囲です。粉末は、ウェットバッグまたはドライバッグプロセスのいずれかでエラストマー金型内で圧縮されます。
冷間等方圧加圧サービスを選択する際には、材料の能力を考慮することが重要です。アルミニウム合金やマグネシウム合金、炭化物や切削工具、カーボンやグラファイト、セラミック、複合材料は、CIPで製造される材料や部品のほんの一部です。コーティングや溶射皮膜、銅合金、ダイヤモンドやダイヤモンドに似た材料を専門とする冷間等方圧加圧サービスもあります。また、電子材料や電気材料、火薬や火工品、特殊材料や専有材料を扱うところもあります。
冷間静水圧プレスとは
冷間静水圧プレス(CIP)は、粉末を様々なサイズや形状の部品に成形し、圧縮するために使用されるプロセスです。湿式バッグ冷間等方圧加圧(CIP)では、材料は予備成形された後、フレキシブルバッグまたは金型に密封されます。バッグは圧力容器内の作動流体(油や水など)の中に入れられます。流体には通常10,000~60,000psiの圧力が加えられ、材料全体に均等に分散されます。この方法は、歪みを減らし、精度を向上させ、空気の巻き込みや空洞のリスクを減らすのに役立ちます。医療用、航空宇宙用、自動車用部品の製造に広く使用されています。
CIPでは、一軸プレスよりも寸法管理が難しくなります。例えば、上記の例で、直径5mmが正確に必要な場合、そこに到達するために、事前に金型と充填手順で試行錯誤と計算が必要でしょう。しかし、一旦それを乗り越えれば、それは非常に再現性の高いプロセスであり、いくつかの明確な利点をもたらします。非常に長いアスペクト比のペレットをプレスすることもできます。スパークプラグは、工業規模で冷間等方圧プレスを行う一般的な製品の一例です。
冷間静水圧プレス
冷間等方圧プレス(CIP)は室温で行われ、ウレタン、ゴム、ポリ塩化ビニルなどのエラストマー材料で作られた金型を使用します。冷間静水圧プレスの流体は通常、油または水である。作業中の流体圧力は、通常60,000 lbs/in2 (400 MPa)から150,000 lbs/in2 (1000MPa)である。この製造工程の欠点は、金型が柔軟なため幾何学的精度が低いことである。まず、粉末は冷間静水圧プレスによって非常に均一な密度に圧縮される。その後、この成形体を通常通り焼結し、目的の部品を製造します。
冷間静水圧プレスの工程
CIPプロセスの説明
冷間等方圧加圧法(CIP)は、エラストマー製の金型に粉末を封入して成形する材料加工法です。金型は、ウレタン、ゴム、ポリ塩化ビニルなど、変形しにくい材料で作られます。その後、型に液圧を均一にかけ、圧縮する。このプロセスはパスカルの法則に基づいており、密閉された流体に加えられた圧力は、大きさが変化することなく全方向に伝達されるというものです。
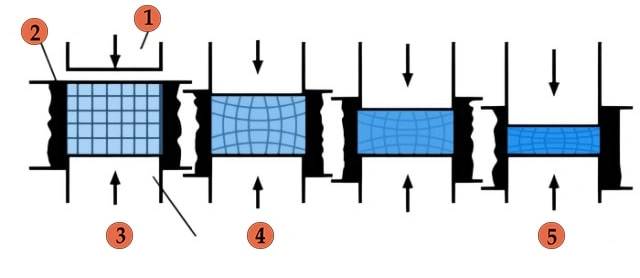
CIPは、プラスチック、グラファイト、粉末冶金、セラミックス、スパッタリングターゲットなど様々な材料に使用できます。一般的には、ハンドリングや加工に十分な強度を持つ「生」部品を得るために使用され、その後、さらに焼結して最終的な強度を得ることができます。
CIP工程の自動化
CIP工程は、専用の装置を用いて自動化することができる。加工する材料をエラストマー金型に密封し、圧力チャンバーに入れます。水や油のような液体媒体がチャンバー内に送り込まれ、金型は四方から均一に高圧を受けます。この自動化により、一貫性のある正確な圧力印加が保証され、高品質の完成品が得られます。
CIP工程の自動化には、いくつかの利点があります。手作業を減らして効率を高め、生産率を上げることができます。また、一貫した圧力印加が保証されるため、完成品の全体的な品質と信頼性が向上します。さらに、自動化によってプロセスパラメーターの制御と監視が改善され、プロセスの最適化とコスト削減につながります。
CIPにおける加圧と減圧のサイクル
CIPプロセスでは、加圧と減圧のサイクルを行い、粉体の望ましい圧縮を実現します。加圧サイクルでは、液体媒体が圧力室に送り込まれ、エラストマー金型に均一な圧力をかけます。この圧力によってパウダーが圧縮され、非常にコンパクトな固体が形成されます。
所望の圧縮が達成されると、減圧サイクルが始まります。チャンバー内の圧力が徐々に解放され、金型が弛緩し、圧縮された材料が取り出される。このサイクルにより、成形された材料が変形や損傷することなく、金型から容易に取り出せるようになります。
加圧と減圧のサイクルは、成形材料の所望の密度と強度を達成するために慎重に制御されます。圧力の大きさ、持続時間、変化率などのパラメータは、処理される材料の特定の要件に基づいて調整することができます。
結論として、冷間静水圧プレス(CIP)は、粉末を圧縮して材料を成形するための汎用性の高い方法です。粉末をエラストマー金型に封入し、均一な圧力を加えることで、CIPは様々な用途に使用できる非常にコンパクトな固形物を製造することができます。CIPプロセスの自動化により、効率と制御が向上し、加圧と減圧のサイクルにより、圧縮された材料の所望の密度と強度が保証されます。
アルミナセラミックスの冷間静水圧プレスの利点
CIPと一軸ダイスプレスおよび他のセラミック成形方法の比較
冷間静水圧プレス (CIP) は、金属およびセラミック部品を製造するための、粉末ベースのニアネットシェイプ技術です。CIPは、セラミックの加工には一般的に使用されていますが、金属にはそれほど広く使用されていません。しかし、プロセス能力と粉末冶金における最近の発展により、高性能金属部品の製造にCIPがますます使用されるようになっています。固体処理、均一な微細構造、形状の複雑さ、低い金型費用、プロセスの拡張性などの利点により、CIPは金属にとって実行可能な処理ルートとなっている。
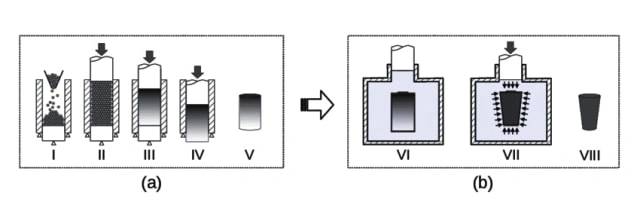
アルミナ・セラミックスにおけるCIPの主な利点は、一軸ダイ・プレスと比較して以下の通りである:
-
より複雑な形状が可能: CIPでは、一軸ダイスプレスと比較して、より複雑な形状の製造が可能です。これは、CIPが複雑なデザインや形状に対応できる柔軟な金型を使用しているためです。
-
プレス圧力勾配を大幅に低減 CIPでは、プレス圧力の勾配が大幅に減少するため、成形工程での歪みや割れを最小限に抑えることができます。これにより、最終的なセラミック部品の寸法精度と構造的完全性が向上します。
少量生産の複雑な部品におけるCIPの利点
CIPは、少量生産の複雑な部品の生産にいくつかの利点をもたらします。これらの利点には以下が含まれます:
-
低い金型コスト: CIPは金型コストを低く抑えることができるため、少量生産の複雑な部品の生産に最適です。他のセラミック成形法とは異なり、CIPは高価な金型を必要としないため、製造コストの削減に役立ちます。
-
CIP後の金型費用は不要です: 金型コストが低いことに加え、CIPではCIP後の工程で金型が不要になります。これにより、製造コストがさらに削減され、複雑な部品の製造にも柔軟に対応できます。
-
サイズ制限なし: CIPには、プレスチャンバーの制限を除き、サイズ制限がありません。このため、非常に大きな部品、特に複雑な形状の部品の製造に適しています。実際、1トンを超える部品もCIPで製造されています。
-
短い加工サイクルタイム CIPは、乾燥やバインダーのバーンアウトを必要としないため、処理サイクル時間が短い。つまり、成形されたセラミック部品は、他の方法よりも速く焼結することができ、生産効率の向上につながります。
CIPはアルミナセラミックに数多くの利点をもたらしますが、いくつかの限界に注意することも重要です。これには、寸法制御の制限、粉末射出成形 (PIM) に劣る形状の複雑さ、優れた流動性を持つ粉末の要件などがあります。
全体として、冷間静水圧プレスは、複雑な形状で少量生産のアルミナセラミックスを製造するための、汎用性が高く費用対効果の高い方法です。形状の複雑さ、圧力勾配の低減、低い金型コスト、処理時間の短縮といった利点があるため、自動車、航空宇宙、電気通信など、さまざまな産業で広く採用されています。
セラミック冷間等方圧加圧の短所
寸法制御と形状の複雑さが課題
冷間等方圧プレス (CIP) は、焼結に適した部品を得るために使用される粉末成形プロセスです。しかし、セラミックスにCIPを使用する場合、寸法制御と形状の複雑さに関連するいくつかの課題があります。
フレキシブル・バッグに隣接するプレス面の精度が、機械的なプレスや押し出しに比べて低いため、多くの場合、その後の機械加工が必要になります。つまり、セラミック部品の所望の寸法や形状を実現するために、追加の工程が必要になる場合があります。
CIPに使用される粉末の要件
冷間等方圧加圧の欠点の一つは、全自動ドライバッグプレスでは通常、比較的高価な噴霧乾燥粉末が必要になることです。特殊な粉末を使用する必要があるため、プロセス全体のコストが高くなる可能性があります。
さらに、CIPの生産速度は、押出成形やダイコンパクションに比べて低い。つまり、大量生産という点では、このプロセスはあまり効率的ではないかもしれません。
まとめると、冷間等方圧加圧には、大型の成形体や複雑な成形体を製造できる、様々な粉末を使用できるなどの利点がある一方で、いくつかの欠点もあります。例えば、寸法制御や形状の複雑さに課題があること、特殊な粉末が必要なこと、他の成形法に比べて生産速度が低いことなどが挙げられます。
冷間静水圧プレスの用途
先端セラミックの大量生産における CIP の一般的な使用例
冷間静水圧プレス (CIP) は、セラミックの加工に一般的に使用される、粉末ベースのニアネットシェイプ技術です。プレス金型の高い初期コストを正当化できない部品や、非常に大きい、または複雑な成形体が必要な部品を製造できるという利点があります。

金属、セラミック、プラスチック、複合材料など、さまざまな粉末を商業規模で静水圧プレスすることができます。圧縮に必要な圧力は、5,000 psi未満から100,000 psi以上の範囲です。粉末は、湿式または乾式バッグプロセスで、エラストマー金型内で圧縮されます。
CIPは、セラミック粉末、グラファイト、耐火物、電気絶縁体、先端セラミックの圧縮に広く使用されています。窒化ケイ素、炭化ケイ素、窒化ホウ素、炭化ホウ素、ホウ化チタン、スピネルなどの材料は、CIPを使って処理できる。
この技術は、スパッタリングターゲットの圧縮、エンジンのシリンダー摩耗を減らすために使用されるバルブ部品のコーティング、電気通信、電子機器、航空宇宙、自動車産業における様々な用途など、新しい用途に拡大しています。
CIPで製造される部品の例
CIPは一般的に、セラミック粉末の圧密、黒鉛、耐火物、電気絶縁体の圧縮、歯科用および医療用のその他のファインセラミックに使用されています。また、スパッタリングターゲットのプレス、シリンダーヘッドの摩耗を最小限に抑えるためのエンジンバルブ部品のコーティング、電気通信、電子機器、航空宇宙、自動車産業における様々な用途にも使用されています。
CIP装置は、生産コストを圧縮するために使用され、原材料から最終製品を作るために不可欠である。このプロセスでは、エラストマー金型に粉体を閉じ込め、金型を圧力室に入れ、液体媒体を送り込み、金型の四方から均一に高圧をかけます。CIPは、粉末冶金、超硬合金、耐火物、グラファイト、セラミック、プラスチック、その他の材料に利用できます。
冷間等方圧加圧サービスを選択する際には、材料の能力を考慮することが重要です。アルミニウム合金やマグネシウム合金、超硬合金や切削工具、カーボンやグラファイト、セラミックス、複合材料、その他の材料をCIPで製造することができます。コーティングや溶射、銅合金、ダイヤモンドやダイヤモンドに似た材料、電子材料や電気材料、火薬や火工品、特殊材料や独自の材料に特化した冷間静水圧プレスサービスもあります。
冷間静水圧プレスは室温で行われ、ウレタン、ゴム、ポリ塩化ビニルなどのエラストマー材料で作られた金型を使用します。冷間静水圧プレスで使用される流体は通常、油または水であり、作業中の流体圧力は通常、60,000 lbs/in2から150,000 lbs/in2の範囲である。この製造方法の欠点は、柔軟な金型による幾何学的精度の低さである。
要約すると、冷間静水圧プレス(CIP)は、先端セラミックやその他の材料を大量生産するための貴重な技術です。固体加工、均一な微細構造、形状の複雑さ、低い金型費用、プロセスの拡張性などの利点がある。CIPは様々な産業で広く利用されており、新たな用途への拡大が続いています。
代替圧縮技術
その他の圧縮技術の概要
材料加工の分野では、強力な圧縮技術がいくつかあります。そのうちの2つの技術、冷間静水圧プレス(CIP)と熱間静水圧プレス(HIP)は、さまざまな産業で広く利用されています。どちらの手法も材料特性を向上させることを目的としていますが、操作条件が異なり、独自の利点があります。
代替手段としての衝撃波成形の導入
CIPとHIPは効果的な圧縮技術ですが、特定の課題に対処するために代替技術が開発されています。そのひとつが、衝撃圧縮としても知られる衝撃波圧縮である。
衝撃波圧縮は、短時間の高圧衝撃波を発生させるもので、粒子を大きく変形させたり、局所的な溶融を引き起こしたりします。このプロセスにより、材料は粒成長することなく、完全に緻密で圧縮された状態になります。衝撃波の特徴は、非常に高い圧力、中程度の温度、非常に短い反応時間、非常に高いひずみ速度である。
以前はミクロンサイズの粉末の圧縮に使用されていたエアガンや爆発性衝撃波などの様々な方法が、現在ではナノ粉末の圧縮に使用されている。加熱時間が非常に短いこれらの代替圧縮技術は、ナノ粒子を粗大化させることなく、完全に緻密でコンパクトな材料を実現することに成功している。
衝撃波圧縮の一例は、エアガンを備えた平面衝撃波圧縮装置の使用である。この装置は短い高圧衝撃波を発生させ、粒子を変形させ、完全な密度と圧縮を達成することができる。これらの代替圧縮技術は、粒成長を最小限に抑え、材料特性を向上させた効率的な加工方法を提供する。
ゴム産業では、効率的なゴム加硫のために高度な圧縮プレスが使用されています。ゴム材料に制御された圧力力を加えることで、これらの機械は、強度、弾力性、耐久性などのゴム製品の物理的特性を試験し、ASTM規格に適合し、高品質であることを保証します。
全体として、衝撃波圧縮のような代替圧縮技術は、改善された特性を持つ、完全に密でコンパクトな材料を達成するための革新的なソリューションを提供します。これらの技術はユニークな利点を提供し、材料加工能力を強化するために様々な産業で利用することができる。
結論
結論として冷間静水圧プレス(CIP) は、特にアドバンスト・セラミックスの製造において、複雑な形状の部品を製造するための汎用性が高く効率的な技術である。従来の一軸ダイスプレスとは異なり、CIPはより複雑な形状の形成を可能にし、均一な粒子充填により歪みやクラックのリスクを低減します。寸法制御と粉末要件に課題がある一方で、CIPは少量生産に大きな利点を提供し、先端セラミックスの大量生産に広く使用されています。CIPに代わるものとして、特定の圧縮用途には衝撃波圧縮も検討に値する。
無料相談はお問い合わせください
KINTEK LAB SOLUTION の製品とサービスは、世界中のお客様に認められています。弊社スタッフがどんなご質問にも喜んで対応させていただきます。無料相談にお問い合わせいただき、製品スペシャリストにご相談いただき、アプリケーションのニーズに最適なソリューションを見つけてください。