真空熱成形は、熱と圧力と金型を使ってプラスチックシートを特定の形状に成形する製造工程である。プラスチックシートがしなやかになるまで加熱し、真空圧を利用してシートを金型に引き寄せ、そこで冷却して固化させることで目的の形状に成形する。この製法は、食品や電子機器の包装など、片面だけの精密な成形が必要な部品を作るのに特に有効である。真空熱成形はコスト効率が高く、汎用性があり、迅速な試作や軽量で耐久性のある製品の生産が可能です。
キーポイントの説明
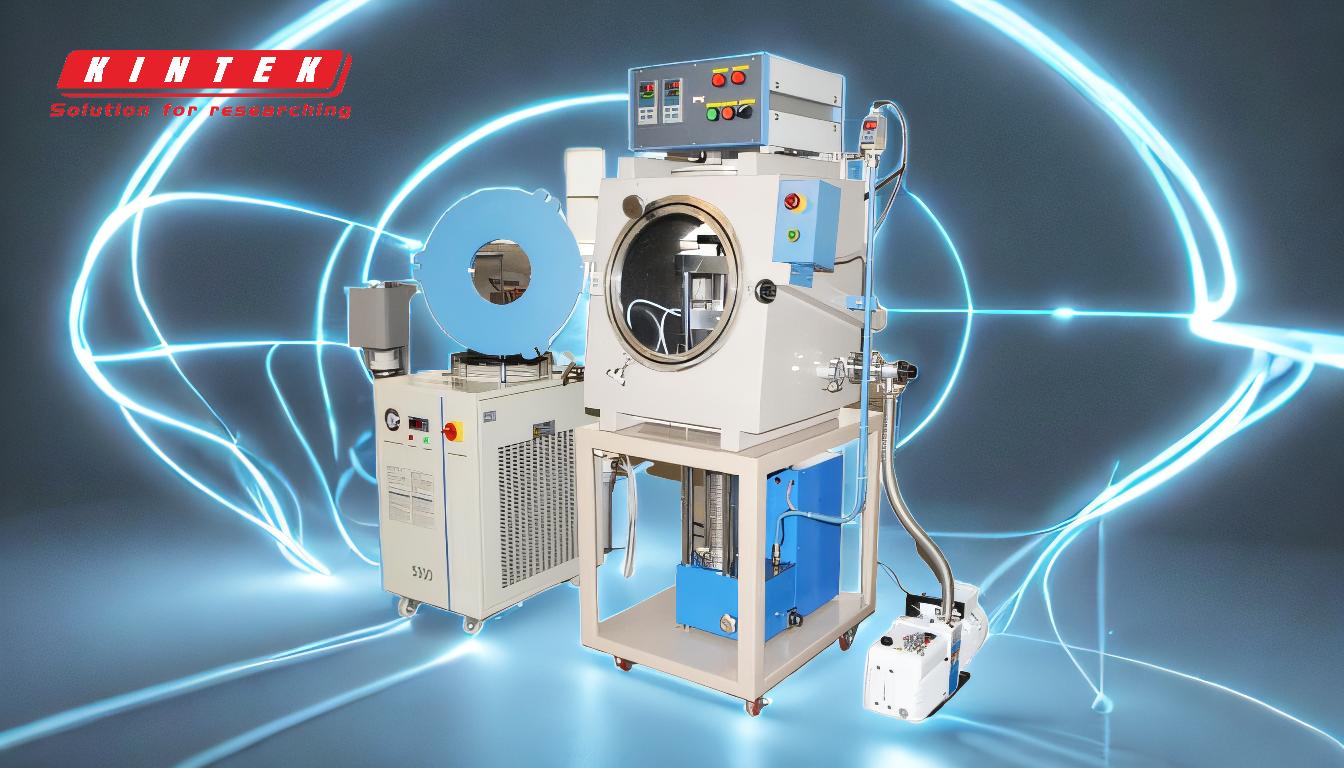
-
真空熱成形の定義:
- 真空熱成形はプラスチック熱成形の一種で、加熱したプラスチックシートを金型と真空圧で成形する。
- 熱成形の最も単純な形態であり、片面の精密な成形が必要な部品に最適です。
-
プロセスの仕組み:
- 暖房:プラスチックシートが柔らかくしなやかになるまで加熱する。
- 成形:加熱したシートを金型にかぶせ、真空圧をかけてシートを金型の表面に引きつける。
- 冷却と固化:プラスチックは冷えて固まり、型の形を保つ。
- トリミング:余分な材料を取り除き、最終製品に仕上げます。
-
真空熱成形の利点:
- コストパフォーマンス:他の成形プロセスと比較して、金型コストが低い。
- 汎用性:包装、自動車部品、医療機器など幅広い用途に適しています。
- ラピッドプロトタイピング:迅速な設計の繰り返しと試作品の製造を可能にします。
- 軽量で耐久性が高い:軽量かつ強靭な製品を生産
-
用途:
- パッケージング:食品、電子機器、消費財の輪郭包装によく使用される。
- 自動車:ダッシュボードやドアパネルなどの内装部品に使用。
- メディカル:トレイ、筐体、その他医療機器部品の製造。
- 小売ディスプレイ:魅力的で機能的な商品陳列を実現。
-
使用材料:
- 一般的な材料には、ABS、PVC、PET、ポリカーボネートなどがあり、柔軟性、耐久性、成形のしやすさから選ばれている。
-
制限事項:
- 片面の精密な成形が必要な部品に限られる。
- 厚い材料では、より高度な技術や機械が必要になる場合があります。
-
他の熱成形法との比較:
- 圧力成形やツインシート成形と異なり、真空熱成形は真空圧のみを使用するため、特定の用途ではよりシンプルで経済的です。
これらの重要なポイントを理解することで、購入者は、コスト、材料、アプリケーション要件などの要因を考慮しながら、真空熱成形が特定のニーズに適したプロセスであるかどうかを評価することができる。
総括表
アスペクト | 詳細 |
---|---|
定義 | 熱、真空圧、金型を使用してプラスチックシートを成形するプロセス。 |
工程 | 加熱→成形→冷却→トリミング |
利点 | コスト効率、汎用性、ラピッドプロトタイピング、軽量、耐久性。 |
用途 | 包装、自動車、医療、小売ディスプレイ |
素材 | ABS、PVC、PET、ポリカーボネート |
制限事項 | 片面成形に限定される。厚い材料には高度なツールが必要な場合がある。 |
あなたのプロジェクトに真空熱成形を検討する準備はできていますか? 今すぐご連絡ください までご連絡ください!