スパークプラズマ焼結(SPS)は、電界支援焼結技術(FAST)としても知られ、圧力、電流、急速加熱を組み合わせることで、従来の焼結に比べて低温・短時間で高密度材料を実現する先進の粉末冶金プロセスである。このプロセスでは、グラファイト製の金型に粉末を入れ、一軸の圧力をかけ、高強度の電気パルスを金型と粉末に通す。これにより、局所的な高温、プラズマ、表面活性化が発生し、粒子の結合と高密度化が促進される。その結果、ジュール加熱、放電プラズマ、塑性変形などのメカニズムにより、99%以上の密度を持つ材料が得られる。
キーポイントの説明
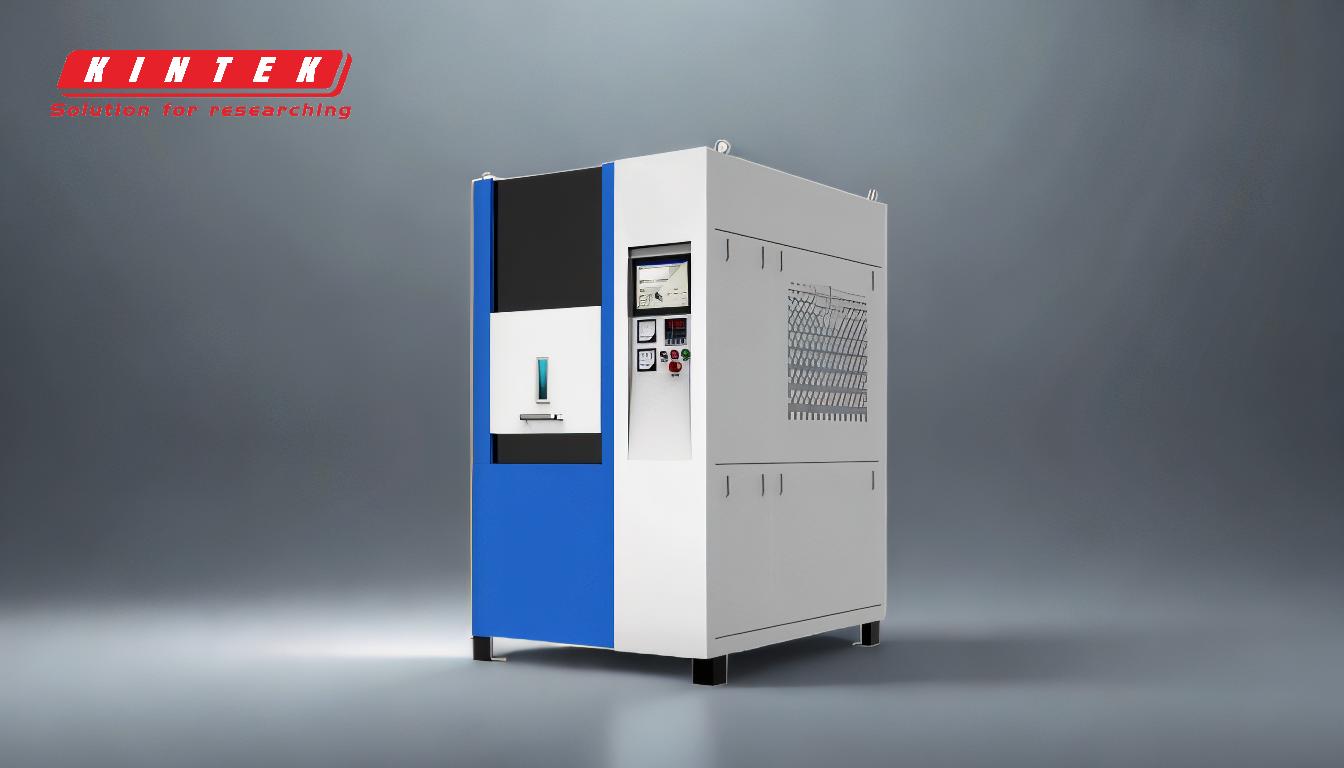
-
セットアップと初期条件:
- グラファイト金型:粉末を黒鉛製の金型に入れ、金型と熱源の両方の役割を果たす。
- 一軸圧力:粉末成形体に約200MPaの圧力をかけ、粒子間の密着を確保する。
- 電流:パルス状の直流電流を金型に流し、導電性の場合は粉体そのものに流す。
-
加熱メカニズム:
- パルス状直流電流:高エネルギーパルス電流により、粒子間に局所的な高温(最大10,000℃)を発生させ、火花放電とプラズマ形成を引き起こす。
- ジュール加熱:粉体と金型の通電抵抗がジュール熱を発生させ、急速加熱に貢献します。
- 急速加熱速度:加熱速度は毎分1,000℃まで達することができ、従来の焼結方法よりも大幅に速い。
-
粒子の結合と高密度化:
- 表面活性化:放電が粒子表面を活性化し、表面酸化物や汚染物質を減少させる。
- ネック形成:高温により粒子表面が溶けて融合し、粒子間にネックが形成される。
- 塑性変形:加えられた圧力と局所的な加熱が塑性変形を誘発し、粒子間の隙間をさらに塞ぐ。
-
温度と時間のコントロール:
- 高温:金型とサンプルの温度は最大2,400℃に達するが、焼結は従来の方法より低温で行われることが多い。
- 短い保持時間:このプロセスでは通常、ピーク温度での保持時間が非常に短く、エネルギー消費と処理時間を削減できる。
-
高密度化と最終特性:
- 高密度:圧力、電流、急速加熱の複合効果により、99%を超える密度の材料が得られる。
- 微細構造制御:急速な加熱と冷却速度により、微細構造の制御が可能になり、多くの場合、結晶粒が微細になり、機械的特性が向上する。
-
システム構成:
- 軸圧装置:焼結時に一軸加圧を付与・維持する。
- 水冷パンチ電極:プロセス中の安定した電気的接触と冷却を確保。
- 真空チャンバー:酸化を防ぐため、真空または不活性ガス下で制御された雰囲気を提供する。
- 雰囲気制御システム:チャンバー内の環境を管理し、最適な焼結条件を確保します。
- DCパルスと冷却水:パルス電流を供給し、放熱を管理します。
- 変位と温度測定:高密度化の進行と温度制御を監視します。
- 安全制御ユニット:特に高温・高圧が要求されるシステムの安全な運転を保証します。
-
従来の焼結を超える利点:
- より低い焼結温度:SPSは通常、従来の焼結よりも数百度低い温度を必要とする。
- 処理時間の短縮:急速加熱と短い保持時間により、全体の処理時間を大幅に短縮。
- 材料特性の向上:微細構造と高密度が達成されることにより、優れた機械的、熱的、電気的特性が得られることが多い。
-
用途:
- セラミックスと金属:SPSは、炭化物、窒化物、複合材料のような先端材料を含むセラミックおよび金属粉末の焼結に広く使用されています。
- ナノマテリアル:このプロセスは、従来の方法では過剰な結晶粒成長を引き起こす可能性のあるナノ材料の焼結に特に効果的である。
- 複雑な形状:焼結中に圧力を加えることができるため、寸法精度の高い複雑な形状の製造が可能です。
要約すると、スパークプラズマ焼結は、電流、圧力、急速加熱を活用して、微細構造を持つ緻密で高品質な材料を製造する、高効率で汎用性の高い焼結技術である。従来の焼結法よりも優れているため、材料特性の精密な制御を必要とする先端材料や用途に特に適している。
要約表
主な側面 | 詳細 |
---|---|
セットアップ | グラファイトモールド、一軸加圧(200MPa)、パルス直流電流 |
加熱機構 | パルス直流電流、ジュール加熱、急速加熱(最大1,000℃/分) |
粒子接合 | 表面活性化、ネック形成、塑性変形 |
温度制御 | 高温(最高2,400℃)、短時間保持 |
最終特性 | >密度99%以上、微細構造、機械的特性の向上 |
利点 | 低い焼結温度、処理時間の短縮、優れた特性 |
用途 | セラミックス、金属、ナノ材料、複雑形状 |
スパークプラズマ焼結で材料加工を変革しましょう。 私たちの専門家に今すぐご連絡ください までご連絡ください!