焼きなましと焼き入れは、金属の物理的および機械的特性を変えるために使用される2つの基本的な熱処理工程である。焼きなましは、金属を特定の温度まで加熱した後、徐冷することで延性を高め、硬度を下げ、内部応力を緩和する。一方、焼き入れは、加熱後に金属を急速に冷却することで、高い硬度と強度を得るが、多くの場合、延性が犠牲になる。焼きなましが材料を軟化させ加工性を向上させることを目的としているのに対し、焼き入れは材料を硬化させることを目的としており、耐摩耗性や耐久性が要求される用途に適している。
キーポイントの説明
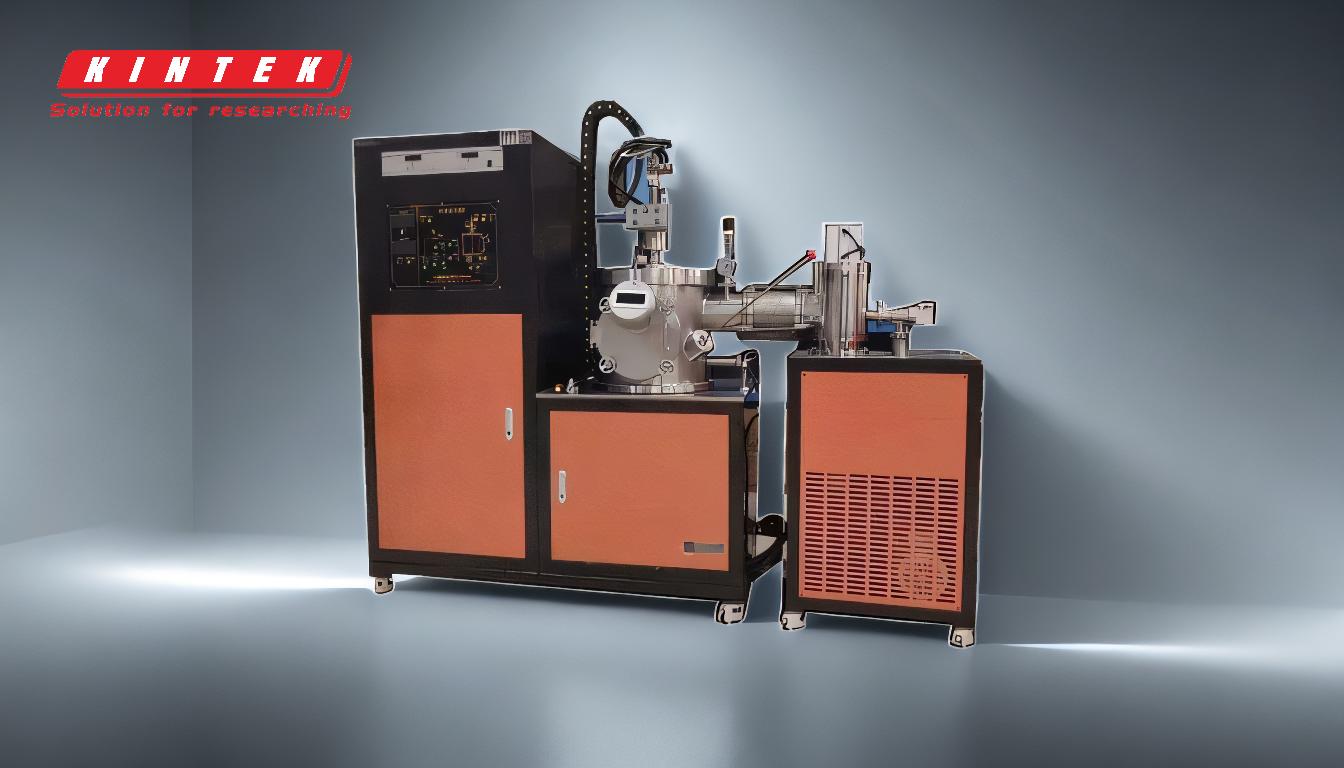
-
目的と目標:
- アニーリング:焼きなましの主な目的は、金属を軟化させ、延性を向上させ、内部応力を緩和することである。この工程を経ることで、その後の製造工程で材料を機械加工、成形、加工しやすくする。
- 焼き入れ:焼き入れは、金属の硬度と強度を高めることを目的としている。これは、加熱された金属を急速に冷却することによって達成され、微細構造を硬化状態に固定し、多くの場合、材料をより脆くする。
-
温度と加熱:
- アニーリング:金属は、再結晶温度以上融点未満の温度に加熱される。この温度は金属の種類や求める結果によって異なる。
- 焼き入れ:また、金属を高温(通常は臨界温度以上)に加熱し、ミクロ組織をオーステナイト相に変化させる。オーステナイト相は、急冷することでその後の硬化を可能にする相である。
-
冷却プロセス:
- アニーリング:加熱後、金属は炉の中や断熱材の中に埋めるなどしてゆっくりと冷却される。この徐冷によって、金属はより安定した、より柔らかい微細構造を形成することができる。
- 焼き入れ:加熱された金属は、通常、水、油、空気などの急冷媒体に浸して急冷される。この急冷により、より軟らかい相の形成が妨げられ、代わりにマルテンサイトのような硬い組織の形成が促進される。
-
微細構造の変化:
- アニーリング:焼きなましの徐冷プロセスにより、より大きく均一な結晶粒が形成され、延性の向上と硬度の低下に寄与する。金属が均一に冷却されるため、内部応力も緩和される。
- 焼き入れ:焼入れにおける急冷は、硬くて脆い微細構造、典型的なマルテンサイトの形成をもたらす。この相は高応力格子構造を特徴とし、材料の硬度上昇と延性低下の一因となる。
-
用途:
- アニーリング:ワイヤー、シート、鍛造品の製造など、金属の成形、形成、機械加工が必要な工程でよく使用される。また、さらなる熱処理工程のために金属を準備するためにも使用される。
- 焼き入れ:歯車、切削工具、自動車部品など、高い表面硬度と耐摩耗性が要求される用途でよく使用される。焼入れの後、脆性を減らすために焼戻しが行われるのが一般的である。
-
機械的性質への影響:
- アニーリング:硬度と強度を下げる一方で、延性と靭性を高める。これにより金属はより柔軟になり、加工しやすくなる。
- 焼き入れ:硬度と強度は増すが、延性と靭性は低下する。このため、金属は摩耗に強くなるが、衝撃で割れたり折れたりしやすくなる。
-
後処理工程:
- アニーリング:単独のプロセスとして、あるいは他のトリートメントの準備段階として使用されることが多い。通常、追加の後処理は必要ない。
- 焼入れ:通常、焼入れの後に焼戻しを行い、焼入れによって生じた脆さを減少させる。焼戻しとは、焼入れした金属を低温に再加熱して内部応力を緩和し、靭性を向上させることである。
要約すると、焼きなましと焼き入れは、金属の熱処理において異なる目的を果たす補完的なプロセスである。焼きなましは、金属を軟化させ、さらに加工するための準備をするために使用され、焼き入れは、高強度および耐摩耗性を必要とする用途のために金属を硬化させるために使用されます。これらのプロセスの違いを理解することは、所望の材料特性と用途要件に基づいて適切な熱処理方法を選択する上で極めて重要です。
総括表
側面 | アニーリング | クエンチング |
---|---|---|
目的 | 金属の軟化、延性の向上、内部応力の緩和 | 硬度と強度を高め、耐摩耗性を向上させる |
温度 | 再結晶温度以上、融点以下で加熱。 | 臨界温度以上に加熱し、オーステナイトを形成させる。 |
冷却プロセス | 徐冷(炉または断熱材) | 急速冷却(水、油、空気) |
微細構造の変化 | より大きく均一な結晶粒を形成し、延性を高める。 | 硬度を高めるため、硬くて脆いマルテンサイトを形成する。 |
用途 | 成形、形成、機械加工(例:ワイヤー、シート、鍛造品) | 高耐摩耗性用途(例:ギア、切削工具) |
機械的特性 | 延性を高め、硬度を下げる | 硬度を上げ、延性を下げる |
後処理 | 単独または準備段階 | 焼戻しによる脆性低減 |
お客様の金属に適した熱処理プロセスの選択にお困りですか? 今すぐ当社の専門家にお問い合わせください!