SPS(スパークプラズマ焼結)は、電流を利用して粉末材料を急速に加熱し緻密化する先進の焼結法です。従来の焼結とは異なり、SPSは導電性グラファイトダイと、場合によっては材料そのものを通過するパルス直流電流(DC)を使用します。この技術は、従来の方法と比較して、極めて速い加熱・冷却速度、短い保持時間、大幅に低い温度での緻密化を可能にする。このプロセスでは粒子表面にプラズマが発生し、拡散と結合が促進されるため、微細構造を持つ高密度材料が得られる。SPSはセラミックス、金属、複合材料に特に有効で、材料特性を精密に制御することができる。
キーポイントの説明
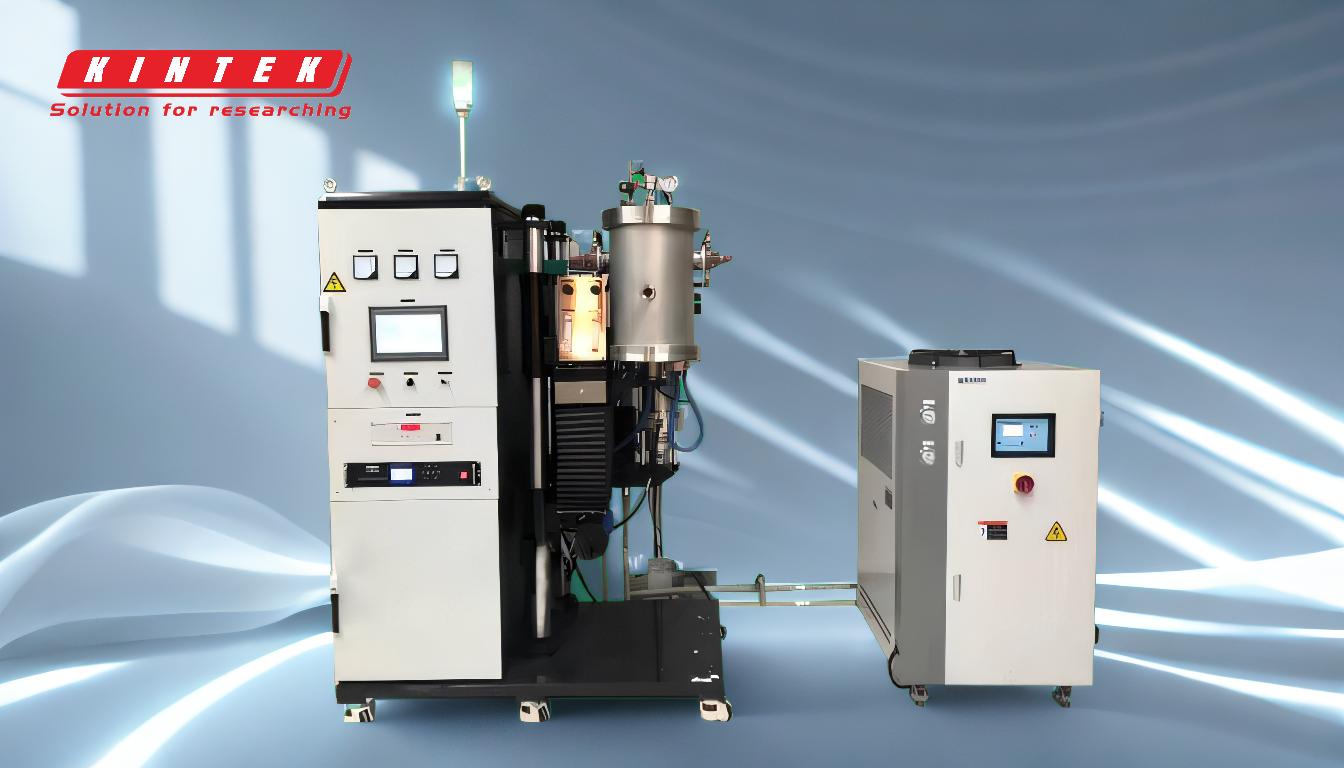
-
SPS焼結の原理:
- SPSは、導電性グラファイトダイと、場合によっては素材そのものに電流(パルスDC)を流す。この電流は内部および外部の熱源として働き、急速な加熱と冷却を可能にする。
- このプロセスは粒子表面にプラズマを発生させ、粒子間の原子拡散と結合を促進する。これにより、従来の焼結法よりもはるかに低い温度で高密度化が実現する。
-
装置とセットアップ:
- SPSシステムは、上部電極と下部電極の間にグラファイトモールドを配置。モールドは油圧システムで加圧され、キャビティは真空になるように排気される。
- 目的の真空度が達成されると、パルス電流が金型とサンプルに直接印加される。このセットアップにより、温度、圧力、焼結時間を正確に制御することができます。
-
SPSの利点:
- 高速加工:SPSは高い加熱・冷却速度を実現し、処理時間を大幅に短縮します。
- より低い焼結温度:従来の方法よりも数百度低い温度で高密度化が行われるため、材料特性が維持される。
- 強化された材料特性:このプロセスにより、高密度、微細構造、改善された機械的特性を持つ材料が得られる。
- 汎用性:SPSはセラミックス、金属、複合材料など幅広い材料に適している。
-
高密度化のメカニズム:
- パルス電流が粉末粒子の表面を活性化し、細孔間で部分放電を起こす。これによりプラズマが発生し、粒子が加熱されて拡散が促進される。
- 同時に、グラファイトモールドが試料に熱を伝え、試料を収縮させ密度を増加させる。このプロセスは、所望の焼結温度と最大密度が達成されるまで続けられる。
-
SPSの用途:
- SPSは、高密度で微細な粒径を実現できることから、アルミナ、ジルコニア、炭化ケイ素などの先端セラミックスの製造に広く使用されている。
- また、微細構造と特性の精密な制御が重要な金属基複合材料、ナノ結晶材料、機能性傾斜材料の製造にも採用されている。
-
従来の焼結との比較:
- 従来の焼結は炉での外部加熱に頼っており、加熱速度は遅く、温度は高くなる。このため、結晶粒が成長し、材料の性能が低下する可能性がある。
- 一方、SPSは電流による内部加熱を利用するため、より迅速な加工が可能であり、材料特性の制御も容易である。そのため、高度な材料製造に最適です。
急速加熱、プラズマ発生、精密制御を組み合わせることで、SPSは焼結にユニークで効率的なアプローチを提供し、高性能材料を製造するための貴重な技術となっている。
要約表
アスペクト | 詳細 |
---|---|
原理 | パルス直流電流でプラズマを発生させ、拡散と接合を促進する。 |
使用装置 | 黒鉛鋳型、電極、真空システム、パルス電流発生器。 |
利点 | 迅速な処理、低い焼結温度、材料特性の向上。 |
用途 | アドバンストセラミックス、金属基複合材料、ナノ結晶材料。 |
比較 | 従来の焼結よりも高速、低温、優れた制御。 |
SPSがお客様の材料製造プロセスをどのように変革できるかをご覧ください。 今すぐお問い合わせください !