SPS(スパークプラズマ焼結)プロセスは、ホットプレスとパルス電流の原理を組み合わせ、材料の迅速かつ効率的な焼結を実現する高度な材料製造技術である。このプロセスの特徴は、温度、圧力、加熱速度を正確に制御することにより、ユニークな微細構造と特性を持つ材料を製造できることです。SPSは、酸化を防ぎ、材料の純度を確保するために、真空または制御された雰囲気の中で作動する。このプロセスには、ガス除去と真空の形成、圧力の印加、抵抗加熱、冷却という4つの主な段階がある。パルス電流によって発生するスパークプラズマ効果は、粒子の成長を抑制し、組成や特性を調整した材料の創出を可能にする。SPSは、特に超高温セラミックスのような先端材料の合成に、研究および産業用途で広く使用されている。
主なポイントを説明します:
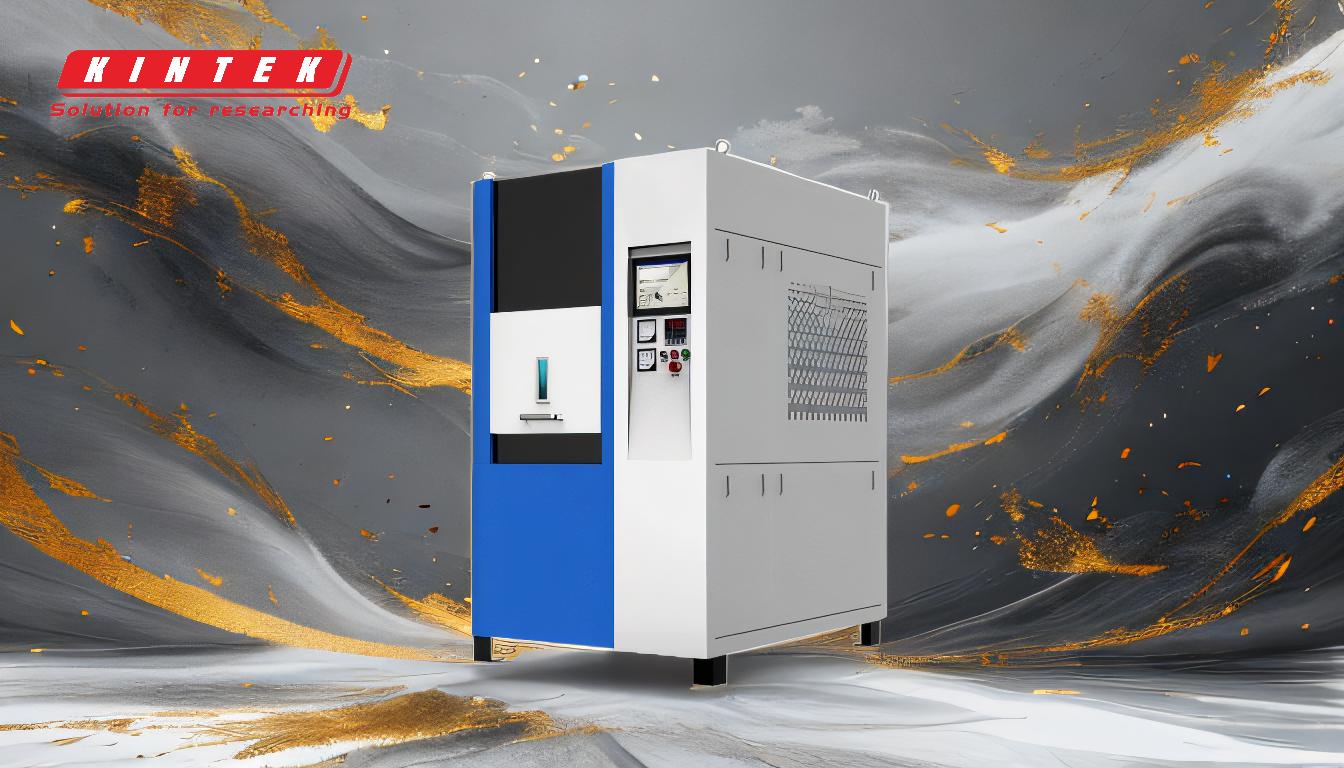
-
SPS加工の定義と目的:
- SPS(スパークプラズマ焼結)は、ホットプレスとパルス電流を組み合わせて効率的に材料を焼結させる材料製造技術である。
- 高密度セラミックス、ナノ材料、複合材料など、従来の方法では実現が困難なユニークな微細構造や特性を持つ材料を製造するために設計されている。
-
核となるメカニズムスパークプラズマ効果:
- このプロセスは、パルス電流が粒子表面に局所的な高温を発生させる「火花プラズマ効果」に依存しています。
- この効果は、蒸発、溶融、粒子間のネックの形成を引き起こし、急速な緻密化と焼結をもたらします。
- また、スパークプラズマ効果により粒子の成長が抑制されるため、機械的・熱的特性が向上した微細な材料の製造が可能になります。
-
SPSプロセスの主要段階:
-
ステージ1:ガス抜きと真空引き:
- チャンバーを排気してガスを除去し、真空状態にすることで、酸化を防ぎ、材料の純度を確保する。
-
第2段階:圧力印加:
- 粒子の再配列と高密度化を促進するために、粉末成形体に一軸圧力を加える。
-
第3段階:抵抗加熱:
- グラファイトダイと試料にパルス電流を流し、抵抗加熱により発熱させる。
-
第4段階:冷却:
- 焼結後、目的の微細構造と特性を維持するために、制御された条件下で試料を冷却します。
-
ステージ1:ガス抜きと真空引き:
-
SPS処理の利点:
-
高い加熱率と短い処理時間:
- SPSは1分間に数百度の加熱速度を達成し、従来の焼結方法に比べて処理時間を大幅に短縮します。
-
低い焼結温度:
- このプロセスは従来の焼結よりも低温で行われるため、結晶粒の成長が最小限に抑えられ、微細構造が維持されます。
-
精密制御:
- 温度、圧力、加熱速度を精密に制御できるため、特性に合わせた材料を製造できる。
-
汎用性:
- SPSはセラミックス、金属、複合材料、ナノ材料など幅広い材料に適しています。
-
高い加熱率と短い処理時間:
-
SPS技術の応用:
-
先端材料の合成:
- SPSは、超高温セラミックス(ZrCなど)、ナノ材料、機能性傾斜材料の製造に使用されています。
-
研究開発:
- この技術は、新しい組成と特性を探求する材料科学研究に広く使用されています。
-
工業生産:
- SPSは、航空宇宙、自動車、電子機器など、高性能材料を必要とする産業で採用されている。
-
先端材料の合成:
-
装置とプロセス制御:
-
黒鉛ダイス:
- 熱伝導率、電気伝導率が高いため、プレス金型には一般的にグラファイトが使用される。
-
タッチスクリーンインターフェース:
- プロセスはタッチスクリーンで制御・プログラムされ、パラメーターの正確な調整とリアルタイムのモニタリングが可能です。
-
真空または制御雰囲気:
- このプロセスは、汚染を防ぎ、材料の純度を確保するために、真空または不活性ガス環境で実施される。
-
黒鉛ダイス:
-
従来法との比較:
- SPSは、処理時間の短縮、エネルギー消費量の削減、ユニークな特性を持つ材料の製造能力など、従来の焼結法に比べて大きな利点を提供します。
- 従来の方法では、高温で長い処理時間が必要な場合が多く、結晶粒の成長や材料性能の低下につながる。
要約すると、SPS処理は、先端材料の迅速かつ精密な製造を可能にする最先端技術である。パルス電流、制御された圧力、高い加熱速度というユニークな組み合わせにより、材料科学者やエンジニアにとって強力なツールとなる。研究用であれ産業用であれ、SPSは比類のない制御性と多用途性を提供し、次世代材料開発のキーテクノロジーとなっている。
総括表
アスペクト | 詳細 |
---|---|
定義 | ホットプレスとパルス電流を組み合わせ、効率的な焼結を行う。 |
コアメカニズム | スパークプラズマ効果により、迅速な高密度化と微細化が可能。 |
主要段階 | ガス除去、圧力印加、抵抗加熱、制御冷却。 |
利点 | 高い加熱速度、低い焼結温度、正確な制御、多用途性。 |
用途 | セラミックス、ナノ材料、工業用高性能材料の合成 |
設備 | グラファイトダイ、タッチスクリーンインターフェース、真空/制御雰囲気。 |
比較 | 従来の方法に比べ、より速く、より少ないエネルギー消費で、より優れた材料特性を実現。 |
SPS技術で先端材料の可能性を解き放つ。 私たちの専門家に今すぐご連絡ください までご連絡ください!