プラズマ支援物理的気相成長法(PAPVD)は、物理的気相成長法(PVD)の原理とプラズマ活性化を組み合わせた高度な薄膜コーティング技術である。この方法は、プラズマを使用して気化材料をイオン化・励起することで蒸着プロセスを強化し、密着性、均一性、膜質を向上させます。PAPVDは、比較的低温で耐久性、耐食性、耐熱性に優れた膜を形成できるため、航空宇宙、自動車、電子機器など、高性能コーティングを必要とする業界で広く使用されている。
キーポイントの説明
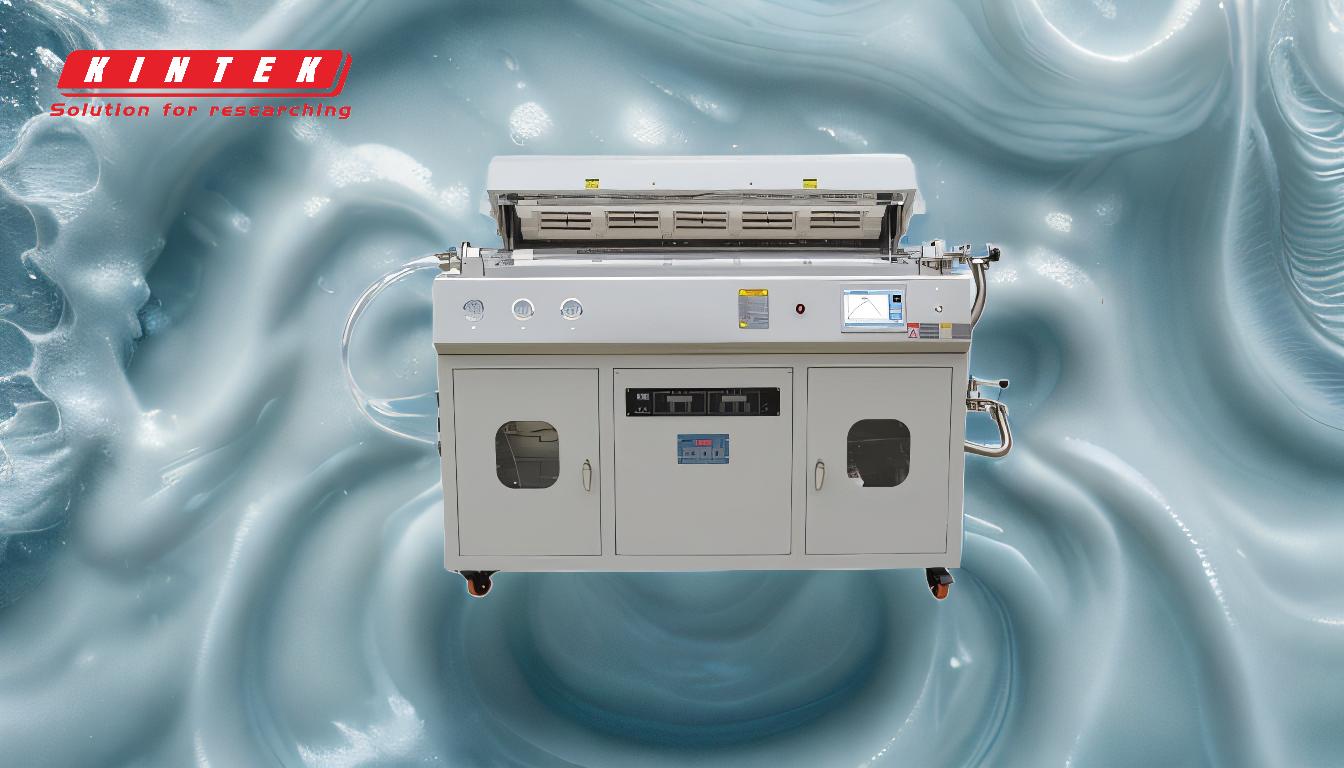
-
プラズマ支援物理蒸着(PAPVD)の定義:
- PAPVDは、プラズマ活性化と従来のPVD法を統合したハイブリッドコーティング技術である。
- 固体前駆体材料(金属やセラミックなど)を気化させ、プラズマで蒸気をイオン化して成膜プロセスを向上させます。
-
PAPVDの基本原理
- 気化: スパッタリング、熱蒸発、レーザーアブレーションなどの高エネルギー法を用いて、固体前駆材料をガス化する。
- プラズマ活性化: プラズマ放電(パルスグローや高周波など)により、気化した物質をイオン化・励起し、反応性とエネルギーを高める。
- 蒸着: イオン化された蒸気は基板に運ばれ、そこで凝縮して薄く均一な膜を形成する。
-
PAPVDの利点
- 低い蒸着温度: プラズマ活性化により、200 °Cという低い温度での成膜が可能になり、温度に敏感な基板に適しています。
- 膜質の向上: プラズマは蒸着膜の密着性、密度、均一性を向上させます。
- 汎用性: PAPVDは、金属、セラミック、複合材料など、さまざまな材料を成膜できます。
- 耐久性: 得られるコーティングは、耐久性、耐食性、高温耐性に優れている。
-
従来のPVDとの比較:
- エネルギー源: 従来のPVDは、材料を気化させるための物理的手段(スパッタリングや蒸発など)のみに頼っていたが、PAPVDはプラズマを使ってプロセスを強化する。
- フィルム特性: PAPVDは従来のPVDに比べ、密着性と均一性に優れた膜が得られる。
- 温度範囲: PAPVDは低温で動作するため、基板への熱損傷のリスクが低減される。
-
PAPVDの用途
- 航空宇宙: 耐摩耗性と熱安定性を向上させるため、タービンブレードなどのコーティングに使用。
- 自動車用 エンジン部品や工具に使用し、耐久性の向上や摩擦の低減を図る。
- エレクトロニクス 半導体や光学部品への薄膜形成に使用。
- 医療機器: 生体適合性と耐食性を向上させるために、インプラントや手術器具をコーティングする。
-
PAPVDのプロセスステップ
- 準備: 基板を洗浄し、真空チャンバーに入れる。
- 気化: スパッタリング、蒸発、レーザーアブレーションなどを用いて固体前駆材料を気化させる。
- プラズマ活性化: プラズマ放電でイオン化し、気化した材料を励起する。
- 蒸着: イオン化された蒸気は基板に運ばれ、そこで凝縮して薄膜を形成する。
- 後処理: コーティングされた基板は、フィルム特性を最適化するために追加処理(アニールなど)を受けることがある。
-
主な設備と消耗品
- 真空チャンバー: 蒸着プロセスのための低圧環境を維持する。
- プラズマソース: プラズマ放電を発生させる(パルスグローや高周波など)。
- ターゲット材料: 気化される固体前駆体材料(金属、セラミックなど)。
- 基板ホルダー: 蒸着中に基板を所定の位置に保持します。
- ポンプシステム: フィルムの汚染を防ぐため、バックグランドガスを低減する。
-
課題と考察
- 複雑さ: PAPVDでは、最適な結果を得るためにプラズマパラメータ(出力、周波数など)を正確に制御する必要がある。
- コスト: PAPVD の装置や消耗品は、従来の PVD に比べて高価な場合がある。
- 拡張性: 大規模生産のためにプロセスをスケールアップすることは困難である。
-
PAPVDの今後の動向:
- ナノ構造コーティング: 性能を向上させるナノスケールの特徴を持つ高度なコーティングの開発。
- ハイブリッドプロセス: PAPVDを他の技術(化学気相成長法など)と統合し、その能力を拡大する。
- 持続可能性: 環境に優しい材料とプロセスを使用し、PAPVDによる環境への影響を低減する。
PVDの物理的原理とプラズマの反応能力を組み合わせることで、PAPVDは高性能薄膜を製造するための強力で汎用性の高いソリューションを提供します。より低い温度で作動し、優れたコーティングを製造するその能力は、現代の製造と材料科学における貴重なツールとなっている。
総括表
アスペクト | 詳細 |
---|---|
定義 | PVDとプラズマ活性化を組み合わせたハイブリッドコーティング技術。 |
基本原理 | 気化、プラズマ活性化、蒸着。 |
利点 | 成膜温度の低減、膜質の向上、汎用性、耐久性 |
用途 | 航空宇宙、自動車、電子機器、医療機器 |
プロセスステップ | 準備、気化、プラズマ活性化、蒸着、後処理。 |
主要設備 | 真空チャンバー、プラズマソース、ターゲット材料、基板ホルダー、排気システム。 |
課題 | 複雑さ、コスト、拡張性 |
将来のトレンド | ナノ構造コーティング、ハイブリッドプロセス、持続可能性。 |
高性能コーティングのニーズにPAPVDをご検討ですか? 今すぐお問い合わせください までご連絡ください!