熱成形は、特に少量生産の場合、射出成形に代わるコスト効率の高い方法です。その手頃な価格の主な理由は、大幅に低い金型費用にあります。熱成形金型は通常、以下のような安価な材料で作られている。 アルミナ・セラミック 射出成形に必要な硬化鋼の金型に比べ、製造が容易で安価である。さらに、熱成形金型は設計と製造工程が単純なため、初期投資とリードタイムが短縮され、特定の用途ではより経済的な選択肢となります。
キーポイントの説明
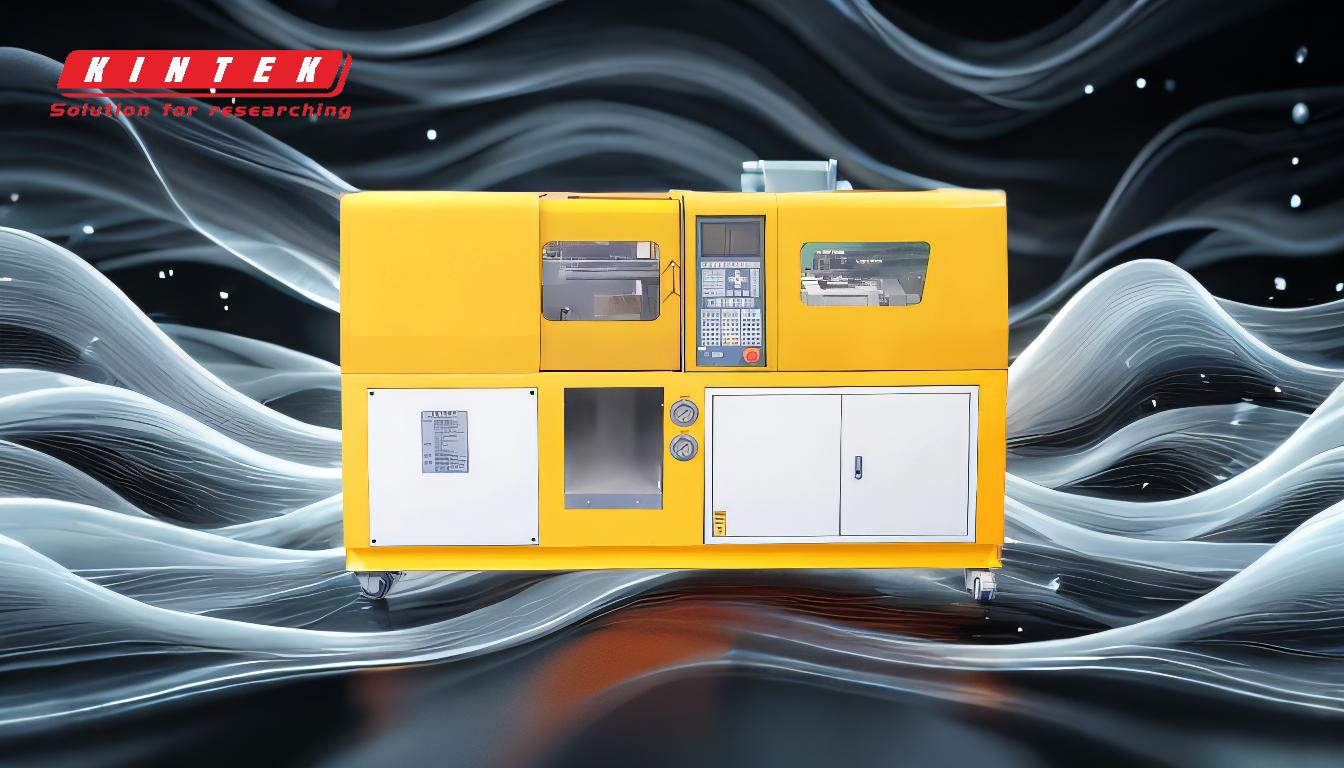
-
金型コストの低減:
- 材料費:熱成形用金型は、射出成形に使われる硬化鋼よりも安価なアルミニウムで作られることが多い。アルミニウムは機械加工が容易で、製造に必要な時間と労力も少なくて済むため、さらにコストを削減できる。
- 設計の複雑さ:熱成形金型は射出成形金型に比べ、一般的に設計が単純です。このシンプルさは、設計および製造コストの削減につながります。
-
初期投資の削減:
- 金型製作時間:熱成形金型の製作に要する時間は、射出成形金型の製作に要する時間に比べて大幅に短縮されます。特に納期の厳しいプロジェクトでは、この短納期がコスト削減につながります。
- セットアップ費用:熱成形の初期設定はそれほど複雑ではなく、コストも低い。これには機械代も含まれ、射出成形機に比べて熱成形機は一般的に安価である。
-
少量生産には経済的:
- ボリュームの柔軟性:熱成形は、特に少量生産において費用対効果が高い。金型への初期投資が少ないため、大量生産を必要としない企業にとって実行可能な選択肢となります。
- プロトタイピング:プロトタイプや少量生産の場合、熱成形はより経済的なソリューションを提供します。金型を迅速かつ安価に製造できるため、設計の反復やテストが迅速に行えます。
-
材料効率:
- 廃棄物削減:熱成形は、特に大きな部品の場合、材料効率が高くなります。このプロセスは、射出成形に比べてスクラップが少なく、原材料のコスト削減につながります。
- 薄肉化:熱成形部品は多くの場合、薄肉で作ることができるため、強度や機能性を損なうことなく材料の使用量を減らすことができます。
-
運用コスト:
- エネルギー消費:熱成形は一般的に、射出成形に比べて少ないエネルギーしか必要としません。エネルギー消費の低減は、特に大規模なオペレーションにおいて、全体的なコスト削減に貢献します。
- メンテナンス:熱成形設備のメンテナンスコストは一般的に低い。機械が単純で、金型の磨耗が少ないため、長期的なメンテナンス費用が削減される。
まとめると、熱成形は射出成形よりも経済的な選択肢を提供し、特に少量生産、試作、材料効率と初期投資の削減が重要な用途に適している。より低い金型費用、よりシンプルな設計、より迅速な生産時間により、熱成形は多くのメーカーにとって費用対効果の高い選択肢となっている。
総括表
側面 | 熱成形 | 射出成形 |
---|---|---|
金型コスト | 低い(アルミ金型) | 高い(硬化鋼金型) |
初期投資 | 削減(シンプルなセットアップ、安価な機械) | 高い(複雑なセットアップ、高価な機械) |
生産時間 | より速い(金型製作時間が短い) | 遅い(金型製作時間が長い) |
量産適性 | 少量生産と試作に最適 | 大量生産に最適 |
材料効率 | 高い(廃棄物が少なく、壁が薄い) | 低い(廃棄物が多い、壁が厚い) |
運転コスト | 低い(エネルギー消費量が少ない、メンテナンスが少ない) | 高い(エネルギー消費量が多い、メンテナンスが多い) |
費用対効果の高い熱成形ソリューションにご興味をお持ちですか? 今すぐお問い合わせください までご連絡ください!