蒸着は、気化した材料を基板表面に蒸着させることで、基板上に薄膜やコーティングを形成するプロセスである。この技術は、半導体、光学、保護膜などの産業で広く使用されている。このプロセスでは、固体または液体の材料を蒸気に変換し、それが基板上に凝縮して薄く均一な層を形成する。蒸着には主に物理蒸着(PVD)と化学蒸着(CVD)の2種類がある。PVDは材料を物理的に気化させるのに対し、CVDは化学反応によって材料を蒸着させる。どちらの方法も、真空チャンバー、精密な温度調節、特定のガス圧など、制御された環境を必要とすることが多い。その結果、耐久性、耐食性、温度耐性に優れたコーティングが実現する。
キーポイントの説明
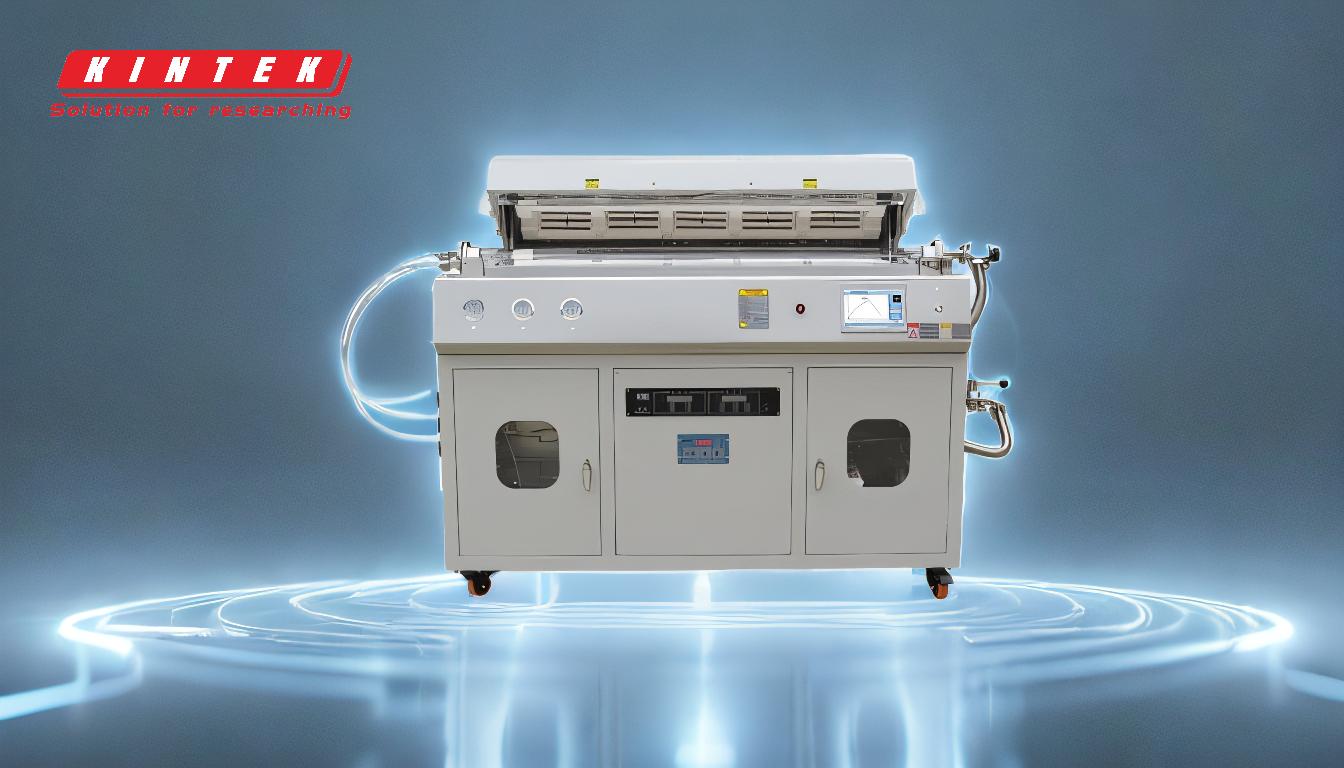
-
蒸着法の概要:
- 蒸着は、材料を薄膜の形で基板上に蒸着させるプロセスである。
- 材料はまず気化され、次に基板上に凝縮され、均一な層が形成される。
- この技術は、半導体、光学、保護膜などの産業で不可欠です。
-
蒸着法の種類:
-
物理蒸着(PVD):
- 多くの場合、熱または高エネルギーイオンを使用して、ターゲット材料を物理的に気化させる。
- 気化した材料は基板上に蒸着される。
- 一般的なPVD法には、スパッタリングや熱蒸着がある。
- PVDは、高温に耐える耐久性のある耐腐食性コーティングを作ることで知られています。
-
化学気相成長法(CVD):
- 化学反応を利用して基材に材料を蒸着させる。
- 基材は、気体状のコーティング材料で満たされた反応チャンバー内に置かれる。
- 気体は基板と反応するか、分解して固体のコーティングを形成する。
- CVDは非常に均一でコンフォーマルなコーティングが可能で、複雑な形状に最適です。
-
物理蒸着(PVD):
-
蒸着における主要プロセス:
-
低圧化学蒸着 (LPCVD):
- CVDの一種で、膜の均一性を向上させ、不純物を減らすために減圧で作動する。
- 半導体製造によく用いられる。
-
低圧プラズマ溶射(LPPS):
- プラズマを使って反応性ガスを活性化し、材料を堆積させる。
- 多くの場合、特定の機械的または電気的特性を持つコーティングを作成するために使用される。
-
熱蒸着:
- 高真空チャンバー内で固体材料を加熱し、蒸気圧を発生させる。
- 気化した材料は基板上に凝縮し、薄膜を形成する。
- 通常、摂氏250度から350度の温度で作動する。
-
低圧化学蒸着 (LPCVD):
-
蒸着システムの構成要素:
-
熱源:
- PVDではターゲット材料を気化させるために、CVDでは化学反応を活性化させるために使用される。
-
真空チャンバー:
- コンタミネーションを防止し、均一な成膜を保証するために、低圧で制御された環境を提供する。
-
ターゲット材料:
- 金属、半導体、その他の固体である。
-
基板:
- 材料が蒸着される表面。多くの場合、ガラス、シリコン、その他の材料でできている。
-
ガス供給:
- CVDでは、成膜プロセスを促進するために反応性ガスをチャンバー内に導入する。
-
温度制御:
- 基板温度とチャンバー温度の正確な調節は、所望のフィルム特性を達成するために非常に重要です。
-
熱源:
-
蒸着アプリケーション:
-
半導体:
- シリコン、二酸化シリコン、金属などの薄膜を半導体ウェハーに成膜するために使用される。
-
光学:
- 反射防止コーティング、ミラー、その他の光学部品に適用される。
-
保護膜:
- 工具、航空宇宙部品、医療機器向けの耐摩耗性、耐食性、遮熱コーティングを提供。
-
コーティング:
- 自動車産業や宝飾品産業で使用され、美しい仕上げを実現。
-
半導体:
-
蒸着法の利点:
-
高精度:
- 極めて薄く均一な膜を、しばしばナノスケールで成膜できる。
-
汎用性:
- 金属、セラミック、ポリマーを含む幅広い材料の蒸着が可能。
-
耐久性:
- 耐摩耗性、耐腐食性、高温耐性に優れたコーティングを実現。
-
拡張性:
- 小規模な実験室研究と大規模な工業生産の両方に適しています。
-
高精度:
-
課題と考察:
-
コスト:
- 特にCVDのような高度な技術では、設備コストや運用コストが高くつくことがある。
-
複雑さ:
- 温度、圧力、ガス流量などのパラメータを正確に制御する必要がある。
-
材料の制限:
- すべての材料がこれらの方法で簡単に気化または蒸着できるわけではない。
-
環境への懸念:
- プロセスによっては、危険なガスや高いエネルギー消費を伴うため、慎重な取り扱いと廃棄が必要となる。
-
コスト:
まとめると、蒸着は薄膜やコーティングを作成するための多用途で精密な方法であり、その応用範囲は広い。さまざまなタイプの蒸着、主要なプロセス、システム構成要素を理解することで、現代の製造と材料科学におけるこの技術の役割を理解することができる。
要約表
アスペクト | 詳細 |
---|---|
タイプ | - 物理蒸着 (PVD) |
- 化学蒸着 (CVD) | |
主要プロセス | - 低圧化学蒸着 (LPCVD) |
- 低圧プラズマ溶射 (LPPS)
- 熱気相成長法 | アプリケーション
- | 半導体
- 光学
- 保護膜 装飾用コーティング |
- メリット
- | 高精度
- 汎用性 耐久性 スケーラビリティ
- |
- 課題
- | 高コスト
複雑さ 素材の限界 環境への配慮