共押出しは、異なる材料特性を持つ多層製品の製造を可能にすることで、製造に大きな利点をもたらします。この製法は、異なる材料を組み合わせてひとつの製品にすることで、機能性、コスト効率、耐久性を高めることができる。共押出成形は、材料特性の調整が不可欠な建築や食品包装などの業界で広く利用されている。様々な剛性、改善されたバリア特性、最適化された性能を持つ製品を作ることができるため、共押出成形は多用途でコスト効率の高いソリューションとなっている。
キーポイントの説明
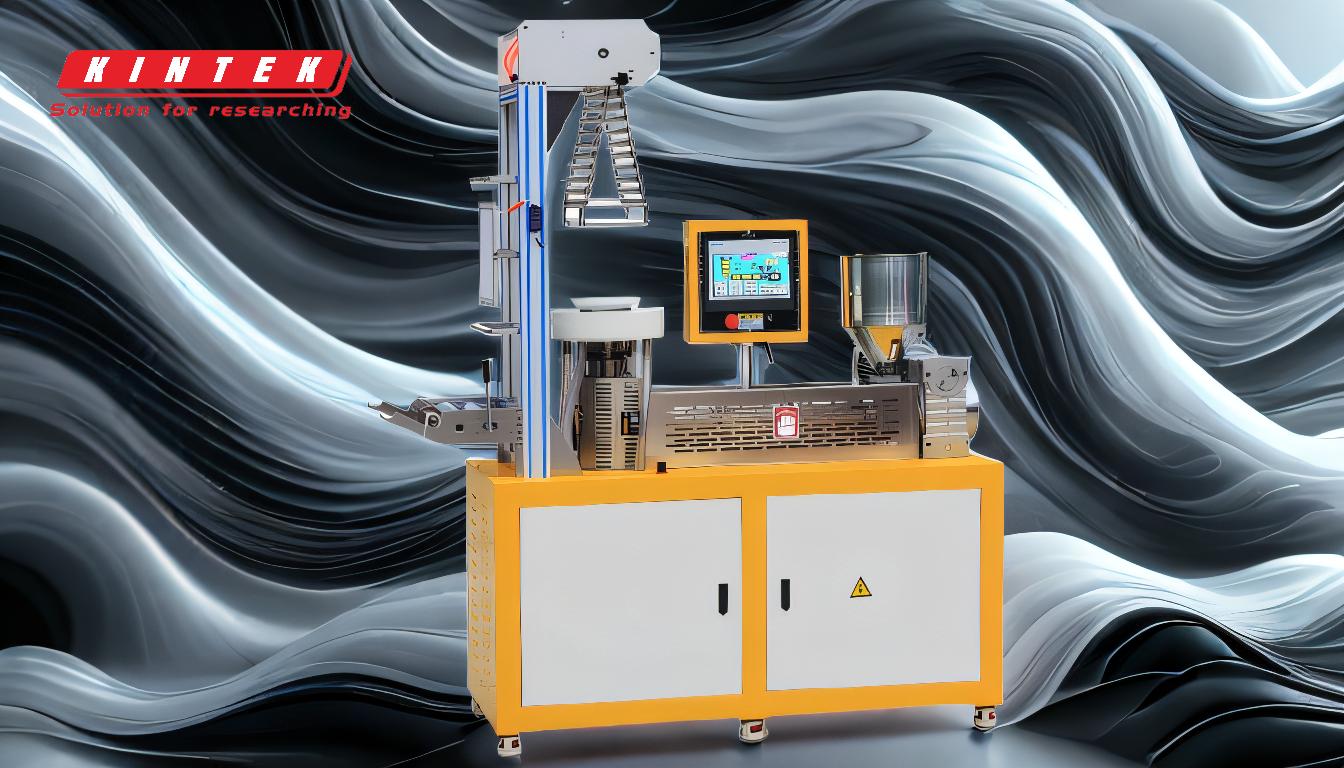
-
強化された素材特性:
- 共押出成形は、剛性の違いなど、性質の異なる素材を組み合わせて1つの製品にすることができます。これにより、ある部分には柔軟性を、別の部分には剛性を持たせるなど、特定の機能要件を満たす製品を作ることができる。
- 例えば、建築分野では、共押出材を使用することで、設置のための柔軟性を維持しながら構造強度を確保することができる。
-
コスト効率:
- 1つの工程で材料を組み合わせることにより、共押出成形は複数の製造工程の必要性を減らし、時間と資源を節約します。
- また、必要な層のみが使用されるため、材料の無駄が最小限に抑えられ、製造コストの削減にもつながります。
-
耐久性と寿命:
- 共押出製品は、互いの特性を高める素材の組み合わせにより、耐久性が向上することが多い。例えば、高い耐摩耗性を持つ材料と紫外線保護機能を持つ材料を組み合わせることで、より長持ちする製品を作ることができます。
- これは、食品包装のような、バリア性が賞味期限を延ばすような用途では特に有益である。
-
業界を超えた汎用性:
- 共押出成形は、建築、食品包装、自動車、医療機器など幅広い産業に適応します。各業界は、特定のニーズに合わせて材料特性を調整できる利点がある。
- 例えば、食品包装では、共押出成形によって酸素バリア性、耐湿性、美観を備えた層を作ることができる。
-
バリア特性の向上:
- 共押出しは、ガス、湿気、化学薬品に対する耐性など、バリア性を高めた製品を作るのに理想的です。これは、製品の鮮度維持が重要な食品包装では特に重要です。
- 補完的なバリア特性を持つ材料を組み合わせることで、共押出成形は単一材料のソリューションと比較して優れた性能を保証します。
-
設計の柔軟性:
- このプロセスは、複雑な設計やカスタマイズを可能にし、メーカーはユニークな形状、質感、機能性を備えた製品を作ることができる。
- このような柔軟性は、軽量でありながら耐久性のある素材が特定の部品に求められる自動車のような業界では貴重である。
-
サステナビリティ:
- 共押出しは、材料の使用量と廃棄物を削減することで、持続可能な製造をサポートします。また、特定の層でリサイクル材料を使用することができるため、環境面での利点がさらに高まります。
- 例えば、共押出し製品では、高性能の外層を維持しながら、再生コア層を使用することができる。
-
一貫した品質:
- 共押出工程は、材料の均一な分配を保証し、一貫した製品品質をもたらします。これは、医療機器のような精度と信頼性が最重要視される産業にとって極めて重要である。
まとめると、共押出成形は、用途が広く、コスト効率が高く、効率的な方法で、特性を調整した多層製品を製造することができる。材料性能を向上させ、コストを削減し、持続可能性をサポートするその能力は、様々な産業で好まれる選択肢となっている。
総括表
利点 | 特徴 |
---|---|
強化された素材特性 | 異なる特性を持つ材料を組み合わせることで、ニーズに合わせた機能性を実現します。 |
コスト効率 | 製造工程と材料の無駄を減らし、製造コストを削減します。 |
耐久性と寿命 | 補完的な材料特性により、製品の寿命を向上させます。 |
業界を超えた汎用性 | 建築、食品包装、自動車、医療用途に適応。 |
バリア特性の向上 | ガス、湿気、化学薬品に対する耐性を強化し、より優れた性能を実現。 |
設計の柔軟性 | 複雑な設計やユニークな製品機能のカスタマイズが可能です。 |
持続可能性 | 材料の使用量を削減し、環境に優しいソリューションのためにリサイクル材料をサポートします。 |
一貫した品質 | 均一な材料分布を確保し、信頼性の高い精密な結果を実現します。 |
お客様の製造ニーズに共押出しの可能性をお届けします。 今すぐご連絡ください !