化学蒸着 (CVD) は、高品質の薄膜やコーティングを作成するために広く使用されている方法です。高い汎用性、材料特性の正確な制御、さまざまな基板上に極薄層を堆積できる機能など、多くの利点があります。ただし、高い動作温度、広い表面のコーティングの制限、特殊な装置の必要性など、いくつかの欠点もあります。以下では、CVD 法の主な利点と欠点を詳しく説明します。
重要なポイントの説明:
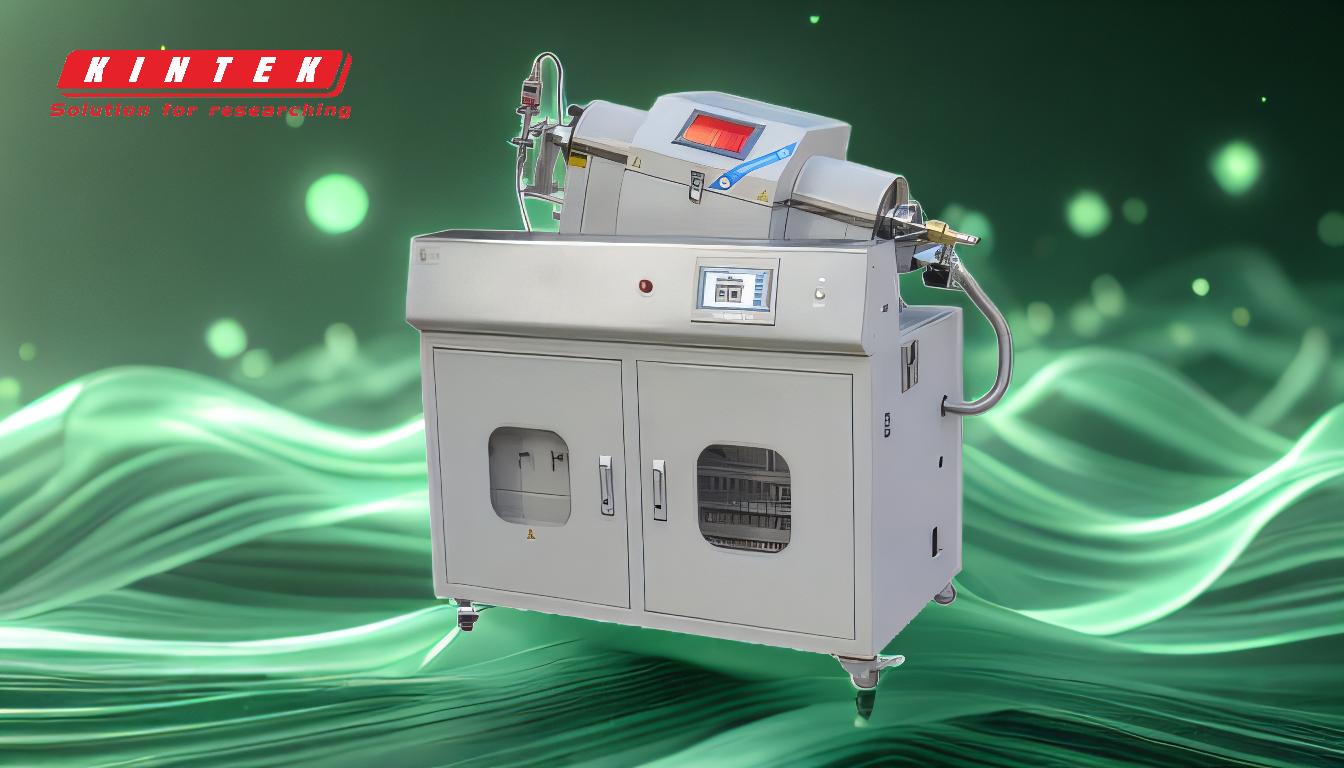
-
化学蒸着の利点:
-
高い汎用性と材料互換性:
- CVD は、セラミック、金属、ガラスなどの幅広い材料の堆積に使用できます。これにより、エレクトロニクスから航空宇宙まで、さまざまな用途に適しています。
- このプロセスにより、純粋な材料と複雑な材料の両方の合成が可能になり、耐食性、耐摩耗性、高純度などの特性をカスタマイズすることが可能になります。
-
精度と制御:
- CVD では、温度、圧力、ガス流量、ガス濃度などの堆積パラメータを完全に制御できます。これにより、堆積膜の化学的および物理的特性を正確に調整できます。
- 電気回路や半導体製造などの用途に不可欠な超薄層の作成に最適です。
-
高品質のコーティング:
- CVD によって生成される膜は通常、高純度、緻密かつ均一で、残留応力が低く、結晶性が良好です。
- この方法は優れた巻き付き特性を備えているため、複雑で精密な表面のコーティングに適しています。
-
耐久性とパフォーマンス:
- CVD コーティングは耐久性が高く、高ストレス環境、極端な温度、温度変化に耐えることができます。
- 他の堆積方法と比較して、CVD はより滑らかな表面、より優れた厚さ制御、および改善された電気伝導性と熱伝導性を実現します。
-
環境上の利点:
- CVD は、多くの場合、ピッチ コーティングなどの代替技術と比較して CO2 排出量の削減につながります。
-
高い汎用性と材料互換性:
-
化学蒸着の欠点:
-
高い動作温度:
- CVD では通常、高温が必要ですが、温度に敏感な材料や基板では問題が発生する可能性があります。
-
広い表面のコーティングの制限:
- CVD で使用される真空チャンバーのサイズには制限があるため、大型またはかさばるコンポーネントをコーティングするのは困難です。
-
複雑なセットアップとプロセスの要件:
- CVD は現場で実行できないため、多くの場合、専門のコーティング センターが必要になります。これにより、物流上の課題とコストが増加します。
- コーティングするにはすべての部品を個別のコンポーネントに分解する必要があり、これには時間と労力がかかる場合があります。
-
全か無かのプロセス:
- CVDは部分的なコーティングには使用が困難です。このプロセスでは、表面全体をコーティングするか、まったくコーティングしないため、特定の用途では柔軟性が制限されます。
-
設備とメンテナンスの費用:
- この装置は操作が比較的簡単ですが、特に高温および真空ベースのシステムの場合、購入と維持に費用がかかる場合があります。
-
高い動作温度:
要約すると、化学蒸着は、高品質のコーティングや薄膜を作成するための非常に多用途かつ正確な方法です。幅広い材料を堆積し、膜特性を制御できるため、エレクトロニクス、航空宇宙、製造などの業界で非常に価値があります。ただし、動作温度が高いこと、広い表面をコーティングする際の制限、物流上の問題が顕著な欠点です。これらの長所と短所を理解することは、特定の用途に適した堆積方法を選択するために非常に重要です。詳細については、以下を参照してください。 化学蒸着 。
概要表:
側面 | 利点 | 短所 |
---|---|---|
多用途性 | セラミックス、金属、ガラスを堆積します。エレクトロニクス、航空宇宙などに適しています。 | 動作温度が高いと、温度に敏感な材料の使用が制限される場合があります。 |
精度と制御 | 蒸着パラメータを完全に制御。極薄層に最適です。 | チャンバーのサイズにより、小型または中型のコンポーネントのコーティングに限定されます。 |
コーティング品質 | 優れた包み込み特性を備えた高純度で緻密で均一なフィルム。 | 特殊な機器が必要であり、現場で実行することはできません。 |
耐久性 | 高いストレス、極端な温度、温度変化に耐えます。 | 全か無かのプロセス。部分的な塗装は出来ません。 |
環境への影響 | ピッチコーティングなどの代替品と比較して CO2 排出量が削減されます。 | 設備費やメンテナンス費が高額。 |
プロジェクトに適した蒸着方法の選択にサポートが必要ですか? 今すぐ専門家にお問い合わせください 個別指導に!