プラスチック金型は、多種多様な製品を作ることができる、製造業には欠かせない道具である。プラスチック成形の最も効果的で一般的な5つのタイプは、押出成形、圧縮成形、ブロー成形、射出成形、回転成形です。それぞれのタイプにはユニークな特徴、用途、利点があり、異なる製造ニーズに適している。以下では、装置や消耗品の購入者がそれぞれの違いや用途を理解するのに役立つよう、これらのタイプについて詳しく説明する。
キーポイントの説明
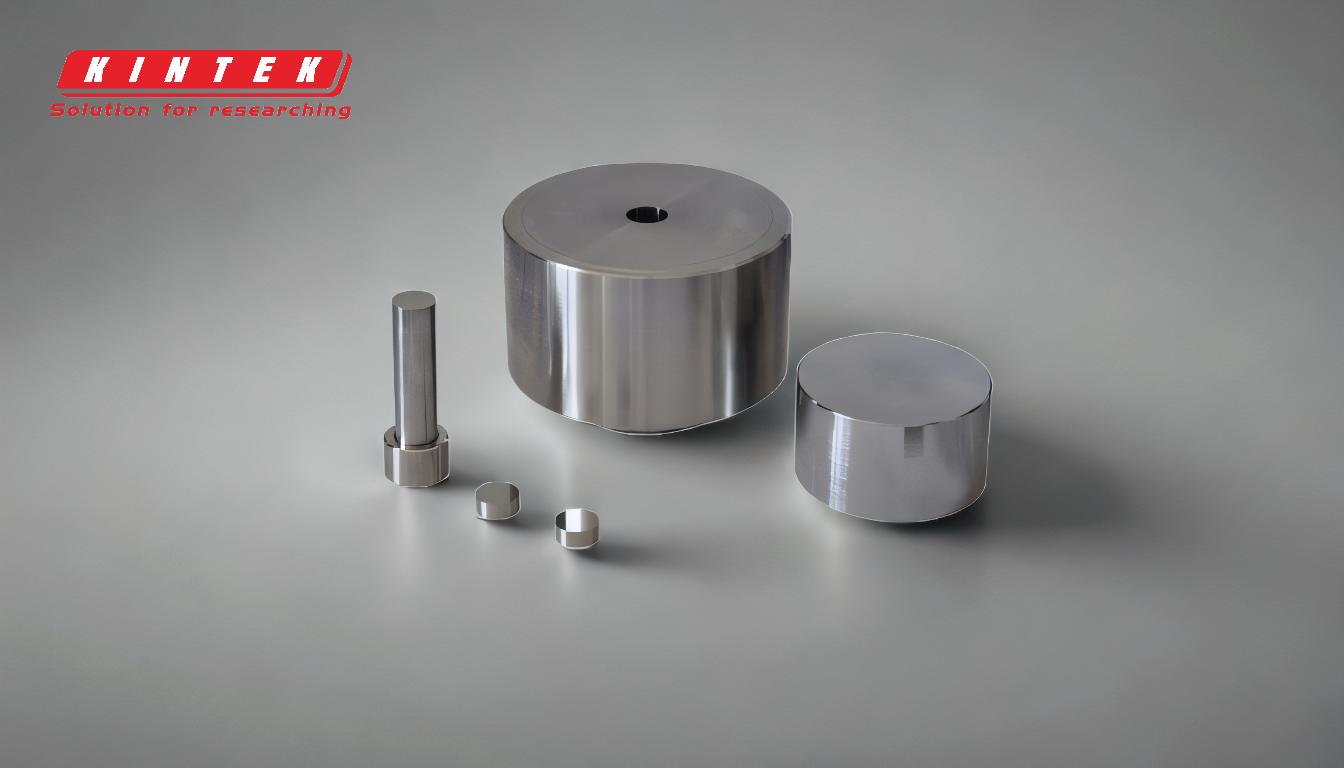
-
押出成形:
- プロセス:押し出し成形では、プラスチック材料を溶かし、ダイに押し込んで連続した形状を作り、それを冷却して希望の長さに切断します。
- 用途:一定の断面を持つパイプ、チューブ、シート、プロファイルの製造によく使用される。
- 利点:生産率が高く、大量生産に適したコスト効率、長尺で均一な形状を作る汎用性。
- 考慮事項:断面が均一な製品に限られ、複雑な形状には適さない。
-
圧縮成形:
- プロセス:加熱された金型のキャビティに、あらかじめ計量されたプラスチック材料を入れ、圧力を加えて材料を目的の形状に成形します。
- 用途:自動車部品、電気筐体、電化製品部品など、大型で平坦な、または中程度に複雑な部品の製造に最適。
- 利点:高強度部品に適し、材料の無駄が少なく、中・大量生産で費用対効果が高い。
- 考慮事項:他の成形法に比べサイクルタイムが長く、複雑なデザインには向かない。
-
ブロー成形:
- プロセス:パリソン(溶融プラスチックの中空管)を金型に入れ、そこに空気を吹き込んで材料を金型壁に対して膨張させ、目的の形状を形成する。
- 用途:主にボトル、コンテナ、タンクなどの中空物を作るのに使われる。
- 利点:軽量で中空製品の製造に優れ、生産効率が高い。
- 考慮事項:中空形状に限定される。少量生産の場合、金型が高価になることがある。
-
射出成形:
- プロセス:溶融プラスチックを高圧で金型に注入し、冷却固化させて目的の形状に成形する。
- 用途:歯車、医療機器、家電製品などの複雑で高精度な部品の製造に広く使用されている。
- 利点:高精度、複雑なデザインが可能、大量生産に適している。
- 考慮事項:初期金型費用が高く、大量生産に最適。
-
回転成形:
- プロセス:プラスチック粉末を金型に入れ、回転させながら加熱して内部を均一にコーティングし、中空部品を形成する。
- 用途:タンク、遊具、貯蔵容器などの大型中空製品によく使用される。
- 利点:低い金型費用、大型部品の製造能力、均一な肉厚。
- 考慮事項:サイクルタイムが遅く、中空で複雑でない形状に限定される。
これらの5つのタイプのプラスチック成形を理解することで、購入者は、生産ニーズ、材料要件、および予算の制約に最適な方法を決定するための情報に基づいた意思決定を行うことができます。それぞれの成形法には明確な利点と限界があるため、適切な成形法を選択する前に、プロジェクトの具体的な要求を評価することが非常に重要である。
総括表
タイプ | プロセス | アプリケーション | 利点 | 留意点 |
---|---|---|---|---|
押出成形 | プラスチックを溶かして金型に通し、冷却して切断する。 | パイプ、チューブ、シート、断面が一定のプロファイル。 | 生産性が高く、大量生産でコスト効率が高い。 | 均一な断面に限定され、複雑な形状には適さない。 |
圧縮成形 | プラスチックを加熱した金型に入れ、圧力をかけて成形する。 | 自動車部品のような大型、平坦、または中程度に複雑な部品。 | 高強度部品、最小限の廃棄物、中規模から大規模の生産ではコスト効率が高い。 | サイクルタイムが長く、複雑な設計には不向き。 |
ブロー成形 | 金型内で溶融プラスチックを空気で膨張させ、中空の形状を成形する。 | ボトル、容器、タンク | 軽量、中空製品、高い生産効率。 | 中空形状に限定される。小ロット用の高価な金型が必要。 |
射出成形 | 溶かしたプラスチックを高圧で金型に射出する。 | 歯車、医療機器、電子機器などの複雑で高精度な部品。 | 高精度で複雑な設計、大量生産に適している。 | 金型費用が高く、大量生産に最適。 |
回転成形 | プラスチック粉末を回転する金型に塗布し、中空部品を成形する。 | タンク、遊具、貯蔵容器。 | 金型費が安い、部品が大きい、肉厚が均一。 | サイクルタイムが遅い。中空で複雑でない形状に限られる。 |
お客様のプロジェクトに適したプラスチック成形方法を選択する準備はできていますか? 今すぐ私たちの専門家にご連絡ください にお問い合わせください!