薄膜蒸着は、エレクトロニクス、光学、エネルギーなど様々な産業において重要なプロセスであり、特定の機能特性を実現するために精密な材料層を基板に塗布する。このプロセスにはいくつかの方法があり、化学的蒸着法と物理的蒸着法に大別される。化学的蒸着法(CVD)や原子層蒸着法(ALD)のような化学的方法は、薄膜を形成するための化学反応に依存し、物理的蒸着法(PVD)のような物理的方法は、ソースから基板への材料の物理的移動を伴う。どちらの方法も、蒸着膜の純度と均一性を確保するために、制御された環境(多くの場合、真空中)を必要とする。どちらの方法を選択するかは、特定の用途に合わせた光学的、電子的、機械的、化学的特性など、希望する膜特性によって決まる。
キーポイントの説明
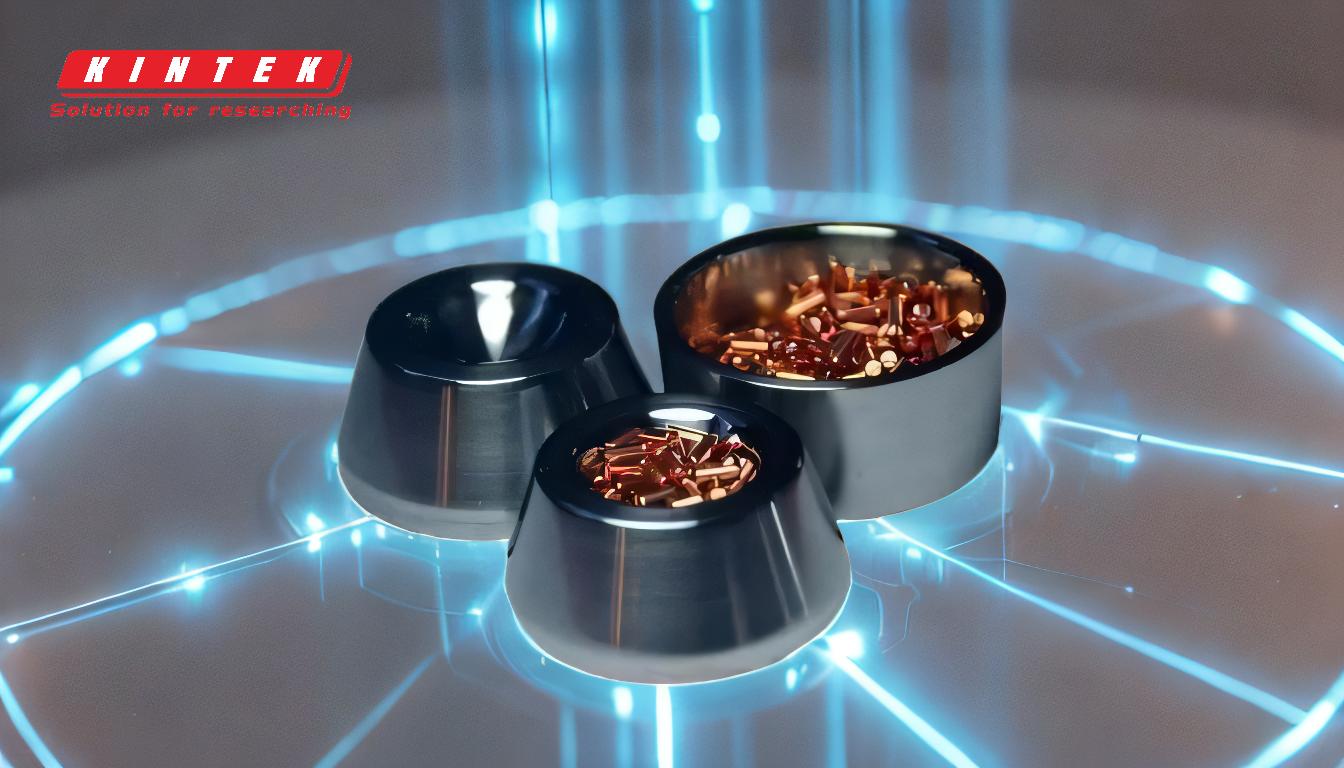
-
薄膜形成法の分類:
- 化学的方法 化学気相成長法(CVD)、プラズマエンハンスドCVD(PECVD)、原子層堆積法(ALD)、電気めっき、ゾル-ゲル、ディップコーティング、スピンコーティングなどの技術がある。これらの方法は、化学反応を利用して薄膜を成膜する。物理的方法
- : 主にスパッタリング、熱蒸着、カーボンコーティング、電子ビーム蒸着、分子線エピタキシー(MBE)、パルスレーザー蒸着(PLD)などの物理蒸着(PVD)技術を用いる。これらの方法は、材料をソースから基板に移動させるために物理的プロセスを使用する。薄膜蒸着の基本ステップ
-
: 準備
- : 基板を洗浄し、薄膜が適切に接着するように準備する。蒸着
- : 実際に薄膜を塗布する工程。使用する方法によって、蒸着、スパッタリング、化学反応などがある。凝縮
- : 気化または化学反応した材料が基板上で凝縮し、固体膜を形成する。蒸着後処理
- : 所望の膜特性を得るために、アニール、エッチング、その他のプロセスが含まれる。化学気相成長(CVD)
-
: プロセス
- : 反応性ガスをチャンバー内に導入し、基材表面で化学反応を起こし、固体膜を形成する。応用例
- : CVDは、二酸化ケイ素や窒化ケイ素などの高純度薄膜を成膜するために、半導体産業で広く使用されている。物理的気相成長法(PVD)
-
: プロセス
- : 材料は真空中で固体ソースから気化され、基板上で凝縮して薄膜を形成する。技術
- : ターゲット材料から原子を放出させるスパッタリングや、材料が蒸発するまで加熱する熱蒸発などの方法がある。応用例
- : PVD : PVDは、マイクロエレクトロニクスから装飾用コーティングに至るまで、金属、合金、化合物の蒸着に使用される。薄膜蒸着における蒸発プロセス
-
: 原則
- : 原料の蒸発と、それに続く基板上への凝縮を伴う。このプロセスは、汚染を防ぎ、均一な成膜を確実にするため、真空中で行わなければならない。熱源
- : 抵抗加熱や電子ビームなど、さまざまな熱源を用いて蒸発させる。用途と要件
-
: フォトニック&オプティカル
- : 薄膜は、反射防止コーティング、ミラー、光学フィルターなどの用途に使用される。電子
- : 半導体デバイス、集積回路、センサーに使用される。メカニカル
- : 耐摩耗性コーティングおよび潤滑剤に適用。化学物質
- : 保護膜や触媒層に使用。先端技術と材料
-
: 原子層堆積法(ALD)
- : 原子レベルでの成膜を可能にし、膜厚と均一性の卓越した制御を実現。フレキシブルエレクトロニクス
- : 新しい方法では、フレキシブル太陽電池や有機発光ダイオード(OLED)などの用途向けに、高分子化合物の微細な層を形成する。環境とプロセス制御
-
: 真空条件
- :コンタミネーションを防止し、高品質な膜を確保するため、ほとんどの蒸着法に不可欠。 温度と圧力の制御
- :所望の薄膜特性を達成するために精密に制御されなければならない重要なパラメーター。 これらの重要なポイントを理解することで、幅広い用途に合わせた特定の機能特性を持つ材料を製造するために不可欠な薄膜蒸着プロセスに求められる複雑さと精度を理解することができる。
総括表:
カテゴリー
方法 | アプリケーション | 化学的方法 |
---|---|---|
CVD、PECVD、ALD、電気めっき、ゾル-ゲル、ディップコーティング、スピンコーティング | 高純度膜、半導体、保護膜 | 物理的方法 |
スパッタリング, 熱蒸着, 電子ビーム蒸着, MBE, PLD | 金属、合金、装飾コーティング、マイクロエレクトロニクス | 主要工程 |
準備、蒸着、凝縮、蒸着後処理 | 適切な密着性、均一性、所望のフィルム特性を確保する。 | 先端技術 |
ALD、フレキシブルエレクトロニクス(OLED、フレキシブル太陽電池など) | 原子レベルの精度、フレキシブルアプリケーション | 環境制御 |
真空状態、温度、圧力のコントロール | コンタミネーションを防ぎ、高品質な膜を実現 | 薄膜蒸着がお客様のプロジェクトをどのように向上させるかをご覧ください。 |
今すぐ専門家にお問い合わせください ! !