DC マグネトロン スパッタリングは、磁場を利用してスパッタリング プロセスの効率を高める、広く使用されている薄膜堆積技術です。これには、真空チャンバー内でプラズマを生成することが含まれ、そこで高エネルギーのイオンがターゲット材料 (陰極) に衝突し、原子が放出されて基板上に堆積します。磁場は電子を捕捉し、ガス原子との衝突確率を高め、プラズマを維持して堆積速度を向上させます。この方法は、比較的低温で高品質で均一なコーティングを堆積できることで知られており、金属、合金、化合物などの幅広い材料に適しています。
重要なポイントの説明:
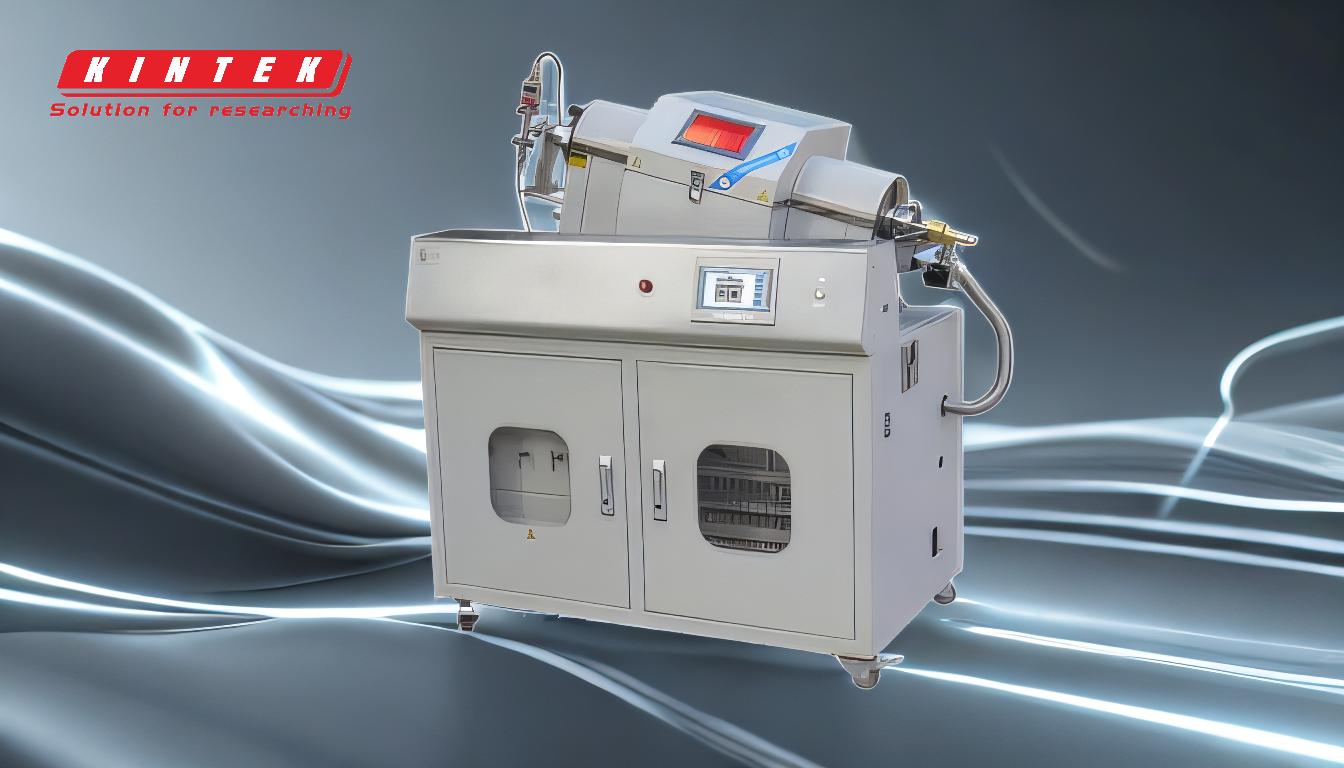
-
プラズマの生成:
- 真空チャンバーには不活性ガス、通常はアルゴンが充填されています。
- 高電圧 DC 電源がターゲット材料 (カソード) に印加され、負の電位が生成されます。
- この負の電位は、ガスから正に帯電したアルゴン イオンを引き付け、プラズマを形成します。
-
磁場の役割:
- 磁石はターゲットの後ろに配置され、閉じた磁場を作成します。
- この磁場は電子を捕らえ、ターゲット表面近くで電子をらせん状の軌道に押し込みます。
- トラップされた電子はアルゴン原子との衝突の可能性を高め、より多くのイオンを生成してプラズマを維持します。
-
スパッタリングプロセス:
- 高エネルギーのアルゴンイオンがターゲット表面に衝突し、運動エネルギーをターゲット原子に伝達します。
- エネルギーが十分であれば、ターゲット原子が表面から弾き出されます(スパッタリングされます)。
- これらの放出された原子は真空中を移動し、基板上に堆積して薄膜を形成します。
-
マグネトロンスパッタリングのメリット:
- 高い成膜速度: 磁場によりプラズマ密度が高まり、より高速なスパッタリングが可能になります。
- 低温動作: このプロセスではターゲット材料を溶解または蒸発させる必要がないため、熱に弱い基板に適しています。
- 材料の多様性 :金属、合金、化合物などの幅広い材料に、その組成を維持したまま適合します。
- 均一なコーティング: 制御されたプラズマと磁場により均一な蒸着が保証され、高品質で均一な薄膜が得られます。
-
パルスDCマグネトロンスパッタリング:
- この変形例では、電力がパルスで印加され、負の電圧と正の電圧が交互に切り替わります。
- 「オン時間」の間、負の電圧が印加され、イオンがターゲットに引き寄せられ、スパッタリングが開始されます。
- 「反転時間」中は、ターゲット表面に蓄積された電荷を放電するために正の電圧が印加され、アーク発生が防止されます。
- この方法は、電荷の蓄積とアーク放電を最小限に抑えるため、誘電体材料を堆積する場合に特に役立ちます。
-
アプリケーション:
- 半導体産業: 集積回路の導電層と絶縁層を堆積するために使用されます。
- 光学コーティング: レンズやミラーの反射防止、反射、保護コーティングの作成に最適です。
- 装飾コーティング: 電子機器の金属仕上げなど、美観を目的として消費者製品に適用されます。
- 耐摩耗性コーティング: 工具やコンポーネントの耐久性を高めるために産業用途で使用されます。
-
プロセス制御と最適化:
- 電源: 安定したプラズマ状態を維持するには、DC 電源を注意深く制御する必要があります。
- ガス圧 :最適なガス圧力により、効率的なイオン化とスパッタリングが保証されます。
- 磁場の構成: 磁場の強さと形状を調整して、電子トラップとプラズマ密度を最適化できます。
- 基板の位置決め: ターゲットに対して基板を適切に配置すると、均一な膜の堆積が保証されます。
要約すると、DC マグネトロン スパッタリングは、磁場を利用してプラズマの生成とスパッタリング レートを向上させ、薄膜を堆積する多用途かつ効率的な方法です。幅広い材料に対応し、高品質のコーティングを生成できるため、さまざまな業界の基礎技術となっています。
概要表:
重要な側面 | 説明 |
---|---|
プラズマ生成 | 不活性ガス (アルゴンなど) は、高電圧 DC 電源を使用して真空チャンバー内でイオン化されます。 |
磁場の役割 | 磁石は電子を捕捉し、ガス原子との衝突を増加させてプラズマを維持し、効率を高めます。 |
スパッタリングプロセス | 高エネルギーイオンがターゲットに衝突し、原子が放出され、基板上に薄膜として堆積します。 |
利点 | 高い蒸着速度、低温動作、材料の多様性、および均一なコーティング。 |
アプリケーション | 半導体、光学、装飾、耐摩耗性コーティング。 |
プロセス制御 | 最良の結果を得るために、電源、ガス圧力、磁場、および基板の位置を最適化します。 |
DC マグネトロン スパッタリングが薄膜堆積プロセスをどのように向上させるかをご覧ください。 今すぐ専門家にお問い合わせください !