スパッタリング・プロセスは、半導体製造、光学、表面工学などの産業で広く使われているプラズマ・ベースの薄膜蒸着技術である。このプロセスでは、高エネルギーのイオン(通常はアルゴンなどの希ガス)による砲撃を通じて、固体のターゲット材料から原子を放出させる。放出された原子は真空中を移動し、基板上に堆積して薄膜を形成する。このプロセスは高度に制御可能で、特定の特性を持つ材料を正確に蒸着することができる。主な手順としては、真空を作り、不活性ガスを導入し、ガスをイオン化してプラズマを形成し、磁場を用いてイオンをターゲットに向ける。スパッタされた原子は基板上に凝縮し、均一で密着性の高い薄膜を形成する。
キーポイントの説明
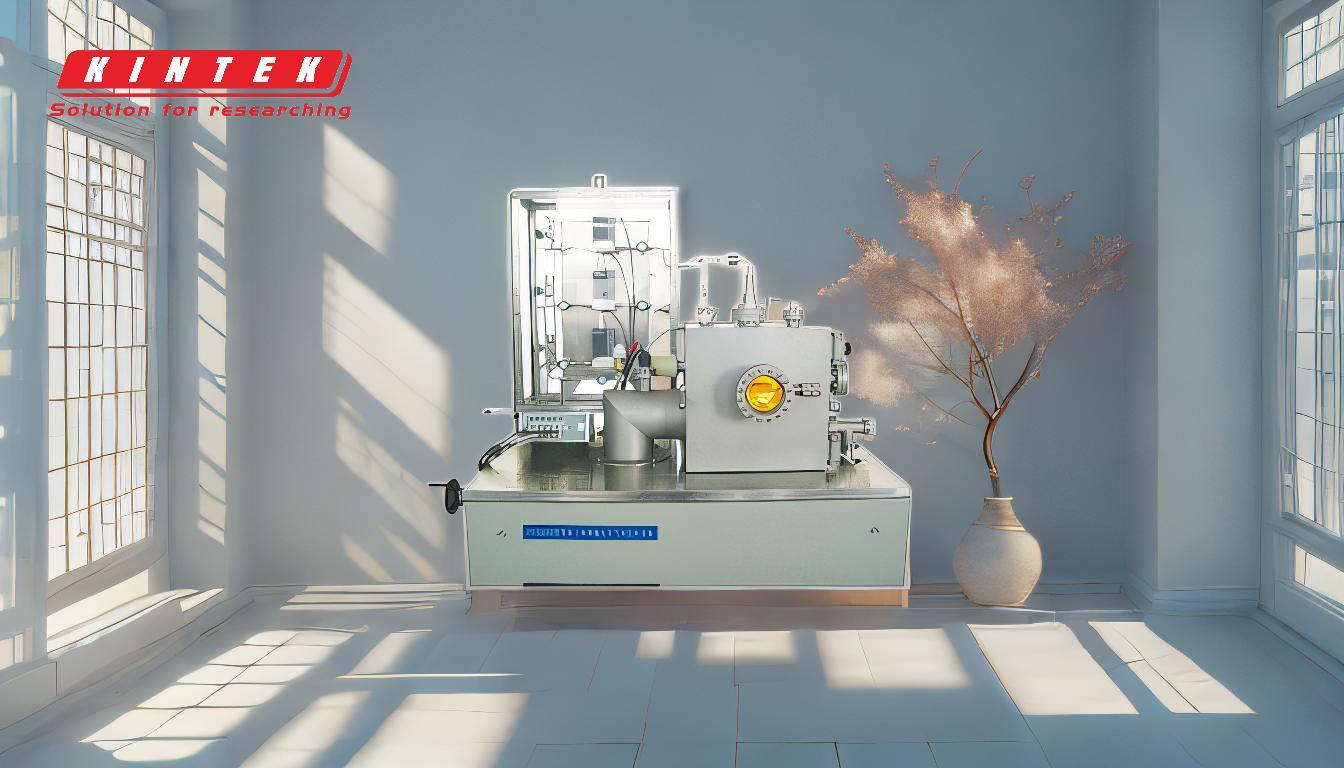
-
プラズマの生成とイオン化:
- 希ガス(通常はアルゴン)を真空チャンバーに導入する。
- このガスは高電圧または電磁励起によってイオン化され、正電荷を帯びたアルゴンイオン(Ar+)からなるプラズマが生成される。
- このプラズマは、ターゲット材料から原子をスパッタするのに必要な高エネルギーイオンを生成するのに不可欠である。
-
真空環境:
- プロセスは、水分や不純物を除去するためにチャンバー内を低圧(約1Paまたは0.0000145psi)に排気することから始まる。
- 真空にすることで、コンタミネーションを最小限に抑え、蒸着プロセスを正確に制御することができる。
-
ターゲットボンバードメント:
- 正電荷を帯びたアルゴンイオンは、通常固体の金属または化合物であるターゲット材料に向かって加速される。
- 衝突すると、イオンはそのエネルギーをターゲットに伝え、スパッタリングとして知られるプロセスでその表面から原子を放出する。
-
磁場閉じ込め:
- 磁場はプラズマを閉じ込め、スパッタリングプロセスの効率を高めるためによく使用される。
- この磁場は、イオンをターゲットに向かわせ、原子の排出率を高めるのに役立つ。
-
スパッタされた原子の輸送:
- 放出された原子は真空チャンバー内を移動し、基板上に堆積する。
- 低圧環境は、原子が弾道的に移動し、衝突を最小限に抑え、均一な成膜を保証します。
-
成膜:
- スパッタされた原子は基板上に凝縮し、薄膜を形成する。
- 膜は層ごとに成長し、膜の厚さと特性はスパッタリング・プロセスの時間とイオンのエネルギーによって制御される。
-
プロセスパラメーター:
- 圧力:チャンバー圧力は、スパッタリングプロセスを最適化するために、通常10^-1~10^-3mbarの範囲で慎重に制御される。
- 温度:基板は、蒸着される材料に応じて、150℃から750℃の範囲で加熱することができる。
- 電圧:高電圧(3~5kV)を印加してアルゴンガスをイオン化し、ターゲットに向けてイオンを加速する。
-
応用例:
- スパッタリングは、半導体、光学コーティング、保護層用の薄膜の成膜など、幅広い用途で使用されている。
- また、反射膜、太陽電池、装飾仕上げの製造にも使用されている。
-
歴史的背景:
- スパッタリング・プロセスは20世紀初頭から商業的に利用されており、トーマス・エジソンは蓄音機録音の大量複製にスパッタリング・プロセスを応用した最初の一人である。
- 陽極酸化のようなスパッタリングのバリエーションは、アルミニウムのような素材に均一で耐久性のある表面を形成するために使用される。
-
利点:
- 精密:このプロセスでは、膜厚と組成を精密に制御することができます。
- 均一性:スパッタリングにより、複雑な形状でも均一性の高い膜が得られます。
- 汎用性:金属、合金、化合物など、さまざまな材料をスパッタリングで成膜することができる。
要約すると、スパッタリング・プロセスは、薄膜を成膜するための多用途で高度に制御可能な方法である。プラズマを発生させ、ターゲット材料に高エネルギーのイオンを照射し、放出された原子を基板上に堆積させる。このプロセスは、その特性を正確に制御しながら均一で高品質な膜を製造できるため、さまざまな産業で広く利用されている。
総括表
主な側面 | 詳細 |
---|---|
プラズマ生成 | 希ガス(アルゴンなど)をイオン化してプラズマを形成し、高エネルギーイオンを発生させる。 |
真空環境 | コンタミネーションを最小限に抑えるため、チャンバーは1Paまで真空排気されている。 |
ターゲット照射 | アルゴンイオンが固体ターゲット材料から原子を放出する。 |
磁場 | プラズマを閉じ込め、スパッタリング効率を高める。 |
薄膜形成 | スパッタされた原子は基板上に凝縮し、均一な薄膜を形成します。 |
用途 | 半導体、光学コーティング、太陽電池、装飾仕上げ。 |
利点 | 高精度、均一性、多様な材料蒸着。 |
スパッタリングの活用にご興味がおありですか? 今すぐご連絡ください までご連絡ください!