熱間鍛造プロセスは、優れた機械的特性を持つ高強度で耐久性のある金属部品を製造する能力で広く認知されています。このプロセスでは、金属を再結晶点以上の温度に加熱し、より可鍛性にし、成形しやすくします。熱間鍛造の主な利点は、金属の結晶粒組織を微細化し、強度、靭性、耐摩耗性、耐疲労性を高めることができる点にある。さらに、熱間鍛造は、材料の無駄を最小限に抑えながら複雑な形状を作り出すことができるため、自動車、航空宇宙、重機などの産業にとって、費用対効果が高く効率的な製造方法となっている。
キーポイントの説明
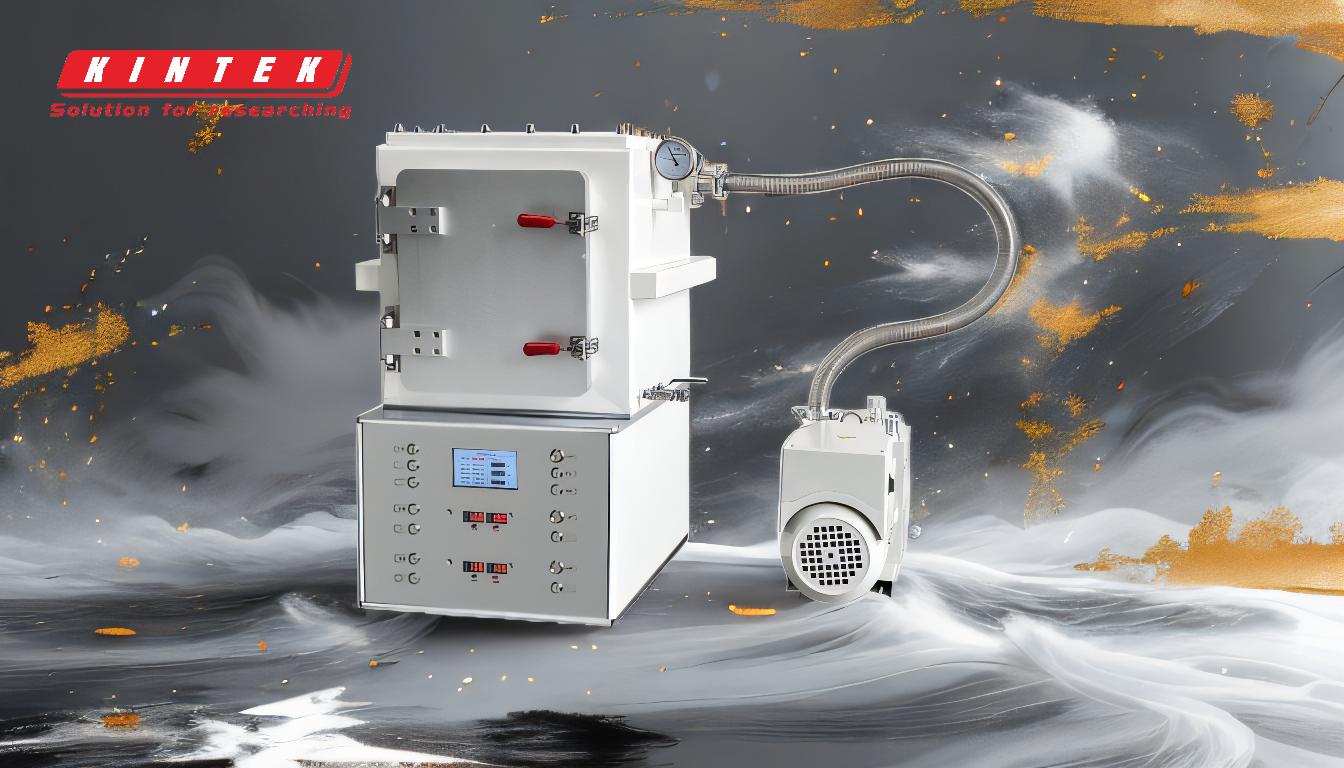
-
機械的特性の向上:
- 熱間鍛造は金属の機械的特性を著しく向上させる。金属を再結晶温度以上に加熱することにより、金属の結晶粒構造の再配列を可能にします。その結果、より微細で均一な粒径が得られ、材料の強度、靭性、衝撃や疲労に対する耐性が向上する。これらの特性の向上は、高い応力や厳しい使用条件にさらされる部品にとって極めて重要である。
-
複雑な形状形成:
- 熱間鍛造プロセスにおける加熱された金属の可鍛性は、冷間鍛造や機械加工では困難または不可能な複雑で複雑な形状の作成を可能にする。この能力は、航空宇宙や自動車製造のように、部品が精密な仕様や厳しい公差を満たす必要がある産業で特に価値があります。
-
材料効率と費用対効果:
- 熱間鍛造は、メーカーが高精度で金属を成形できるようにすることで、材料の無駄を最小限に抑えます。このプロセスでは、しばしばネットシェイプに近い部品が製造されるため、大規模な機械加工や仕上げの必要性が減少します。この効率は、材料費の削減と生産時間の短縮につながり、熱間鍛造を大規模製造のための経済的に魅力的な選択肢にしています。
-
改善されたフローと均一性:
- 熱間鍛造で使用される高温は、成形プロセス中に金属がより均一に流れることを保証します。この均一性により、最終製品の完全性を損なう可能性のある亀裂、空隙、介在物などの欠陥が発生する可能性が低くなります。その結果、熱間鍛造部品はその信頼性と一貫性で知られています。
-
材料を問わない汎用性:
- 熱間鍛造は、鉄、アルミニウム、チタン、銅など幅広い金属や合金に適用できます。この汎用性により、自動車部品から重機械や工具に至るまで、様々な産業の部品を製造するのに適した方法となっています。
-
残留応力の低減:
- 熱間鍛造に使用される高温は、金属内の内部応力を緩和し、より安定した耐久性のある最終製品をもたらします。この残留応力の低減は、繰り返し荷重や過酷な条件にさらされる部品にとって特に重要です。
要約すると、熱間鍛造プロセスは、優れた機械的特性、複雑な形状を作成する能力、材料効率、および汎用性の組み合わせを提供し、高性能金属部品を製造するための非常に有利な製造方法です。
まとめ表
主な利点 | 特徴 |
---|---|
強化された機械的特性 | 結晶粒組織を微細化し、優れた強度、靭性、耐疲労性を実現。 |
複雑な形状の形成 | 高精度と厳しい公差で複雑な設計を可能にします。 |
材料効率 | 無駄を最小限に抑え、機械加工の必要性を減らし、コストを削減します。 |
フローと均一性の向上 | 欠陥のない、信頼性の高い、一貫したコンポーネントを保証します。 |
あらゆる材料に対応する汎用性 | スチール、アルミニウム、チタン、銅合金に最適。 |
残留応力の低減 | 過酷な条件下でも安定した耐久性のある部品を生産。 |
お客様の製造ニーズに熱間鍛造の可能性を。 今すぐ専門家にお問い合わせください !