真空注型と射出成形は、プラスチックまたは樹脂部品を製造するために使用される2つの異なる製造プロセスであり、それぞれ独自の利点、制限、およびアプリケーションを持っています。真空注型は、プロトタイピングや少量生産に理想的な低圧プロセスであり、高いディテールと材料の多様性を提供します。一方、射出成形は大量生産に適した高圧プロセスで、高い精度、再現性、コスト効率を規模に応じて提供します。両者の選択は、生産量、材料要件、予算、希望する部品品質などの要因によって異なります。以下では、これらのプロセスの主な違いについて詳しく説明する。
ポイントを解説
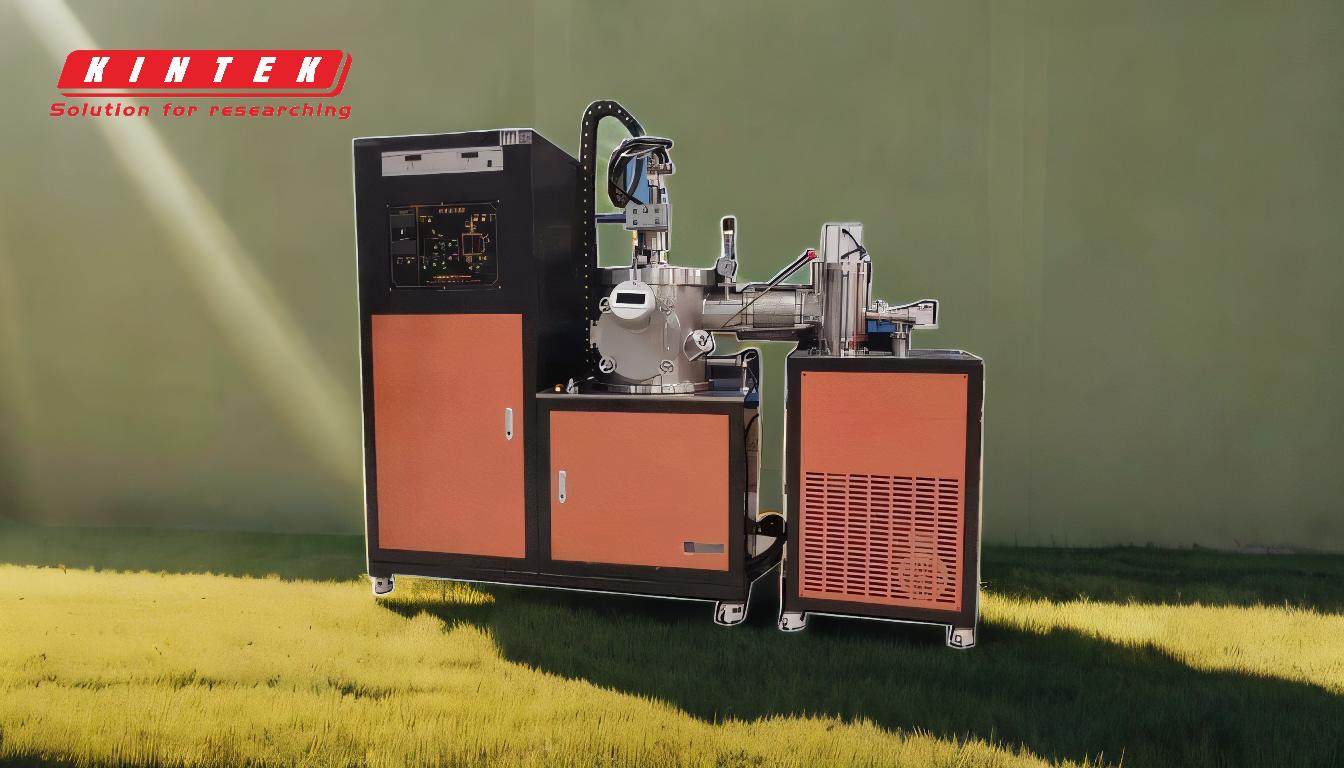
-
プロセスのメカニズム:
-
真空鋳造:
- マスターパターン(多くの場合3Dプリント)から作成したシリコン型を使用。
- 型に液状の樹脂を流し込み、真空状態にして気泡を取り除き、滑らかで細部まで仕上げる。
- その後、金型をオーブンで硬化させ、樹脂を固めます。
-
射出成形:
- 溶かしたプラスチックや樹脂を高圧で鉄やアルミの金型に注入する。
- 材料は金型内で冷えて固まり、その後部品が射出される。
- この工程は高度に自動化されており、繰り返し可能である。
-
真空鋳造:
-
生産量:
-
真空鋳造:
- 低~中程度の生産量(通常、1つの金型につき10~50部品)に最適。
- シリコーン金型は時間の経過とともに劣化するため、生産できる部品数が制限される。
-
射出成形:
- 大量生産(数千から数百万個の部品)用に設計されています。
- 金属金型は耐久性に優れ、大きな摩耗を伴わずに数多くのサイクルに耐えることができます。
-
真空鋳造:
-
材料オプション:
-
真空鋳造:
- 様々なエンジニアリング・プラスチック(例:ABS、PP、PC)を模倣できる幅広いポリウレタン樹脂を提供。
- 比較的低温で硬化可能な材料に限る。
-
射出成形:
- 多様な熱可塑性プラスチックと一部の熱硬化性材料に対応。
- PEEK、ナイロン、ポリカーボネートなどの高機能素材に対応。
-
真空鋳造:
-
コスト:
-
真空鋳造:
- 安価なシリコーン金型によりイニシャルコストが低い。
- 金型の劣化や手作業のため、生産量が多くなると単価が高くなる。
-
射出成形:
- 金型の初期費用が高い。
- 自動化と材料の効率化により、大量生産では単位当たりのコストが低くなる。
-
真空鋳造:
-
部品の品質と精度:
-
真空鋳造:
- 優れた表面仕上げと微細なディテールを持つ部品を生産。
- 手作業の工程や金型の柔軟性により、若干のばらつきが生じることがある。
-
射出成形:
- すべての部品で高精度と一貫性を実現。
- 複雑な形状や厳しい公差に最適です。
-
真空鋳造:
-
リードタイム:
-
真空鋳造:
- 金型製作のリードタイムを短縮(通常1~2週間)。
- ラピッドプロトタイピングや短納期のプロジェクトに適しています。
-
射出成形:
- 金型設計と製作のリードタイムが長い(数週間から数ヶ月)。
- 大規模生産でのみ経済的。
-
真空鋳造:
-
用途:
-
真空鋳造:
- プロトタイピング、機能テスト、少量生産に最適。
- 自動車、家電、医療機器などの業界でよく使用される。
-
射出成形:
- 消費財、自動車部品、工業部品の大量生産に最適。
- 大量かつ安定した生産量を必要とする産業で広く使用されている。
-
真空鋳造:
-
環境への影響:
-
真空鋳造:
- 射出成形に比べて廃棄物が少ない。
- シリコーン金型はリサイクルできませんが、工程で使用するエネルギーは少なくて済みます。
-
射出成形:
- 材料廃棄が多い(スプルーやランナーなど)。
- 高圧機械と加熱が必要なため、エネルギー集約型である。
-
真空鋳造:
これらの重要な違いを理解することで、製造業者や設計者は、コスト、量、材料、部品の品質などの要素をバランスさせながら、特定のニーズに最も適したプロセスを、十分な情報を得た上で決定することができる。
要約表
側面 | 真空鋳造 | 射出成形 |
---|---|---|
プロセスの仕組み | シリコン型を使用し、真空で気泡を除去し、オーブンで樹脂を硬化させる。 | 溶融プラスチックを高圧で金型に注入。 |
生産量 | 低~中量(金型あたり10~50部品)。 | 大量生産(数千から数百万の部品)。 |
材料オプション | エンジニアリングプラスチックを模倣したポリウレタン樹脂 | 幅広い熱可塑性プラスチックと高性能材料(PEEKなど)。 |
コスト | 初期コストは低いが、大量生産では単価が高くなる。 | 初期金型費用が高く、大量生産では単価が低くなる。 |
部品品質 | 優れた表面仕上げ、手作業によるわずかなばらつき。 | 高精度、一貫性、厳格な公差。 |
リードタイム | 短い(金型製作に1~2週間)。 | 長い(金型製作に数週間から数ヶ月)。 |
用途 | プロトタイピング、機能テスト、少量生産 | 消費財、自動車、工業部品の大量生産。 |
環境への影響 | 廃棄物が少なく、エネルギー消費が少ない。 | 材料の無駄が多く、エネルギー集約型のプロセス。 |
どのプロセスがお客様のプロジェクトに最適か、まだご不明ですか? 私たちの専門家に今すぐご連絡ください をご利用ください!