物理的気相成長法(PVD)と化学的気相成長法(CVD)は、薄膜を成長させるために広く使われている2つの技術であり、それぞれ異なるプロセス、メカニズム、用途を持つ。PVDは、一般的にスパッタリングや蒸発などのプロセスを通じて、ソースから基板へ材料を物理的に移動させるもので、低温で作動する。一方、CVDは気体状の前駆物質と基板との化学反応に依存し、多くの場合、高温を必要とし、より厚く粗い膜になる。PVDとCVDのどちらを選択するかは、希望する膜特性、基板との適合性、アプリケーションの要件などの要因によって決まります。
キーポイントの説明
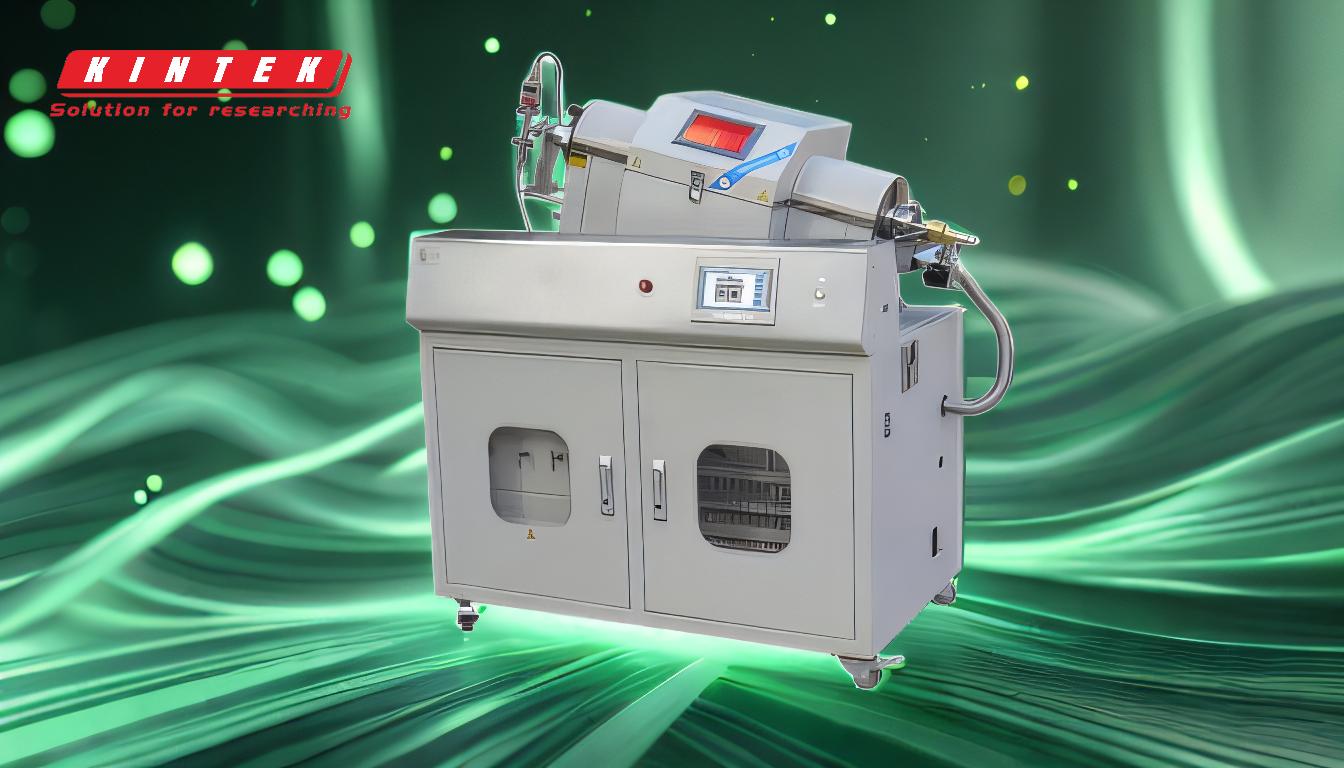
-
成膜のメカニズム:
- PVD:材料が固体または液体のソースから気化され、基板上に蒸着される物理的プロセス。スパッタリングや蒸着などの技術が含まれる。
- CVD:ガス状の前駆体が基板表面で反応し、固体膜を形成する化学プロセス。化学反応を伴うため、高温を必要とすることが多い。
-
使用温度:
- PVD:一般的に低温で動作するため、温度に敏感な基板に適している。
- CVD:高温(500°~1100°C)を必要とするため、使用できる材料や基板の種類が制限されることがある。
-
蒸着方向性:
- PVD:ライン・オブ・サイト・プロセス。つまり、蒸着はソースから基板に直接行われる。このため、複雑な形状の基板では、被覆が不均一になることがある。
- CVD:多方向プロセスにより、複雑な形状や高アスペクト比の構造でも均一な被覆が可能。
-
フィルム特性:
- PVD:高精度で、薄く、滑らかで、耐久性のあるコーティングができる。一般的に膜厚が薄く、密着性に優れる。
- CVD:厚く粗い膜を作ることができるが、適合性に優れ、さまざまな素材にコーティングできる。
-
用途:
- PVD:光学コーティング、装飾仕上げ、耐摩耗コーティングによく使用される。また、高い精度と平滑性が要求される用途にも好まれる。
- CVD:半導体製造(集積回路用多結晶シリコン膜など)や、特定の電気的、熱的、機械的特性を持つコーティングに広く使用されている。
-
材料の利用と効率:
- PVD:一般的に成膜速度は低いが、材料利用効率は高い。電子ビームPVD(EBPVD)のような技術は、低い基板温度で高い蒸着速度(0.1~100μm/分)を達成できる。
- CVD:成膜速度が速く、汎用性が高いが、腐食性の副生成物や不純物が発生する可能性がある。
-
利点と限界:
- PVDの利点:蒸着温度が低く、腐食性の副生成物がなく、高品質で平滑な膜が得られる。
- PVDの限界:成膜速度が低く、複雑な形状を均一にコーティングすることが難しい。
- CVDの利点:優れた適合性、幅広い材料へのコーティング能力、高い成膜速度。
- CVDの限界:高温は基板との適合性を制限し、腐食性ガスを発生させる可能性がある。
まとめると、PVDとCVDは相補的な技術であり、それぞれに独自の強みと限界がある。PVDは、より低温で精密かつ平滑、耐久性のある皮膜を必要とする用途に最適であり、CVDは、高温ではあるが、様々な材料上にコンフォーマルな高品質皮膜を形成するのに優れている。この2つの選択は、希望する膜特性、基材、運用上の制約など、アプリケーションの具体的な要件によって決まる。
総括表
側面 | PVD | CVD |
---|---|---|
メカニズム | 材料の物理的移動(スパッタリング、蒸発など)。 | ガス状前駆体と基板間の化学反応。 |
温度 | 低温、敏感な基材に適する。 | 高温(500°~1100°C)では、基板適合性が制限される。 |
方向性 | 視線処理、複雑な形状では不均一。 | 多方向性、複雑な形状でも均一。 |
皮膜特性 | 高精度で、薄く、滑らかで、耐久性のあるコーティング。 | 適合性に優れた、より厚く粗い皮膜。 |
用途 | 光学コーティング、装飾仕上げ、耐摩耗コーティング | 半導体製造、特殊特性を持つコーティング |
材料効率 | 蒸着率が低く、材料利用率が高い。 | 蒸着速度が速く、汎用性が高いが、腐食性の副生成物が発生する可能性がある。 |
利点 | 低温、腐食性副生成物なし、平滑な膜。 | 優れた適合性、幅広い材料適合性、高い成膜速度。 |
制限事項 | 成膜速度の低下、複雑な形状の課題。 | 高温、腐食性ガス、膜中の不純物。 |
PVDとCVDの選択でお困りですか? 今すぐ当社の専門家にお問い合わせください!