スパーク プラズマ焼結 (SPS) は、圧力とパルス電流の適用を組み合わせて、従来の焼結方法と比較して比較的低い温度で材料の急速な緻密化を達成する高度な焼結技術です。このプロセスは、機械的特性が向上した高密度で微細な材料を製造するのに特に効果的です。 SPS の主な利点は、急速な加熱および冷却速度を達成できることにあり、これにより粒子の成長が最小限に抑えられ、ナノ構造の保存が可能になります。そのため、セラミック、金属、複合材料などの先端材料に非常に適しています。
重要なポイントの説明:
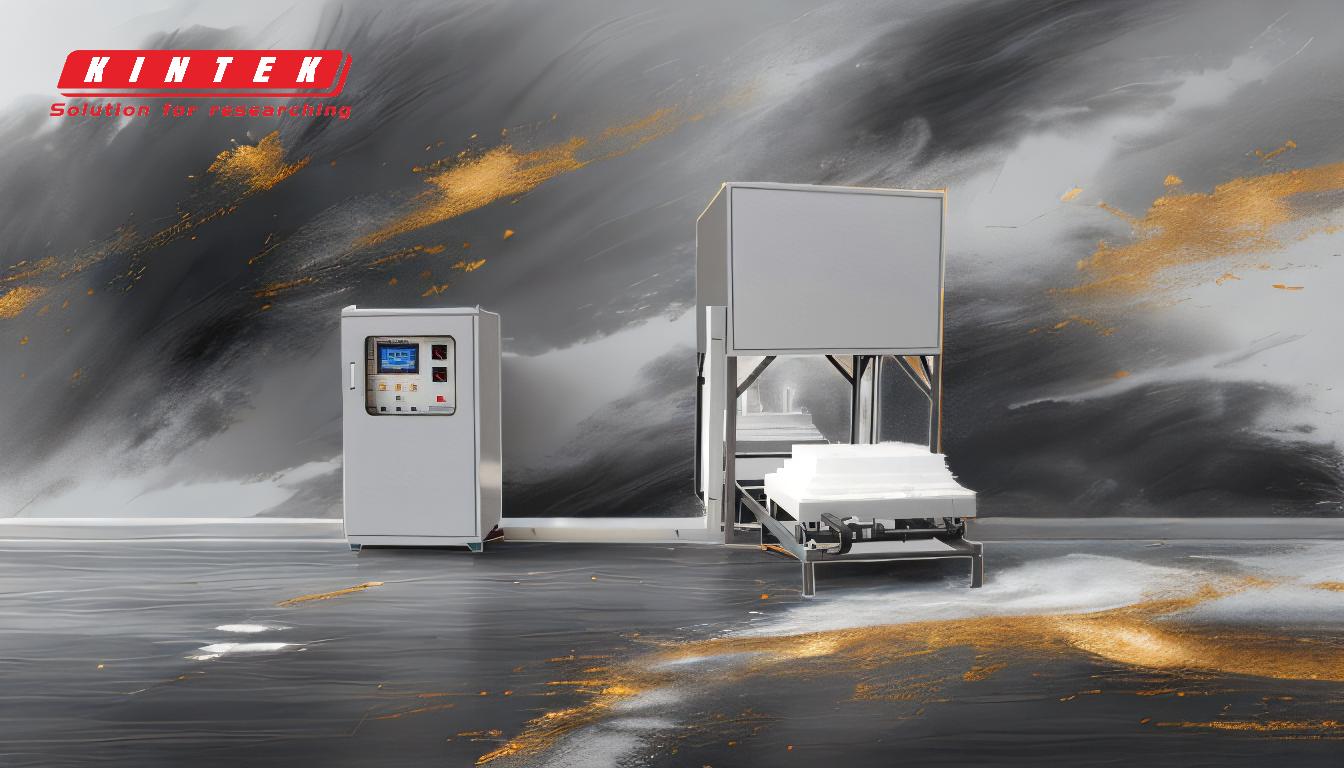
-
放電プラズマ焼結の基本原理:
- SPS は、材料とダイを通過するパルス直流 (DC) を利用し、ジュール加熱とスパーク プラズマ放電を通じて局所的な加熱を生成します。
- 一軸の圧力と電流を同時に加えることで、粒子の迅速な結合と緻密化が促進されます。
- 従来の焼結とは異なり、SPS はより低い温度とより短い処理時間で緻密化を実現し、材料の微細構造の完全性を維持するのに役立ちます。
-
SPS プロセスの段階:
- 粉末の調製: 原料は微粉末の形で準備され、グラファイトダイスに充填されます。
- 圧縮 :粉末は適度な圧力下で圧縮され、均一な分布を確保し、空隙を排除します。
- 加熱と焼結: パルス状の DC 電流が印加され、材料内部で熱が発生します。この急速な加熱により、粒子の結合と緻密化が促進されます。
- 冷却: 焼結後、材料は急速に冷却され、微細粒子構造の維持に役立ち、粒子の成長を防ぎます。
-
放電プラズマ焼結の利点:
- 迅速な処理: 従来の焼結方法では数時間、場合によっては数日かかるのに対し、SPS は数分で完全な緻密化を達成できます。
- より低い焼結温度: このプロセスは材料の融点よりも大幅に低い温度で行われるため、熱劣化のリスクが軽減されます。
- 強化された材料特性: SPS は、高密度、微細な粒子サイズ、および硬度、強度、耐摩耗性などの機械的特性が向上した材料を生成します。
- 多用途性: SPS は、セラミック、金属、複合材料、さらにはナノマテリアルを含む幅広い材料に適用できます。
-
放電プラズマ焼結の応用例:
- アドバンストセラミックス: SPS は、優れた機械的特性と熱的特性を備えた高性能セラミックスの製造に広く使用されています。
- 金属および合金: このプロセスは、金属や合金、特に従来の方法では緻密化が困難な金属や合金の焼結に効果的です。
- ナノマテリアル: SPS は、エレクトロニクス、触媒、エネルギー貯蔵の用途に不可欠なナノ構造を維持しながらナノマテリアルを強化するのに理想的です。
- 複合材料: SPS は、単一の焼結ステップで異なる材料を組み合わせることで、目的に合わせた特性を備えた複合材料の製造を可能にします。
-
従来の焼結との比較:
- 従来の焼結は外部加熱源と長時間の処理時間に依存するため、粒子の成長や材料特性の低下につながる可能性があります。
- 一方、SPS は電流による内部加熱を利用するため、より高速な高密度化と微細構造のより適切な制御が可能になります。
- SPS での焼結中に圧力を加える機能により、緻密化がさらに強化され、気孔率が減少します。
要約すると、スパーク プラズマ焼結は、従来の方法に比べて大きな利点をもたらす、非常に効率的で多用途な焼結技術です。特性が強化された高密度で微細な材料を製造できるため、先進的な材料製造において貴重なツールとなります。
概要表:
側面 | 詳細 |
---|---|
プロセス | 圧力とパルス電流を組み合わせて急速な高密度化を実現します。 |
主な利点 | 迅速な処理、より低い焼結温度、強化された材料特性。 |
アプリケーション | 先進的なセラミックス、金属、合金、ナノマテリアル、複合材料。 |
比較 | 従来の焼結方法よりも高速かつ効率的です。 |
スパーク プラズマ焼結がどのように材料生産に革命をもたらすかを学びましょう。 今すぐ専門家にお問い合わせください !