射出成形は、金型に溶融材料を注入して同じ部品を大量に生産する製造プロセスである。材料が冷えて固まると金型が開き、完成部品が射出される。この方法は、高い精度と再現性で複雑な形状を作ることができるため、大量生産には非常に効率的である。一般的に使用される材料には、プラスチック、金属、ガラスなどがあるが、汎用性とコストパフォーマンスの高さから、プラスチックが最も普及している。
主なポイントを説明します:
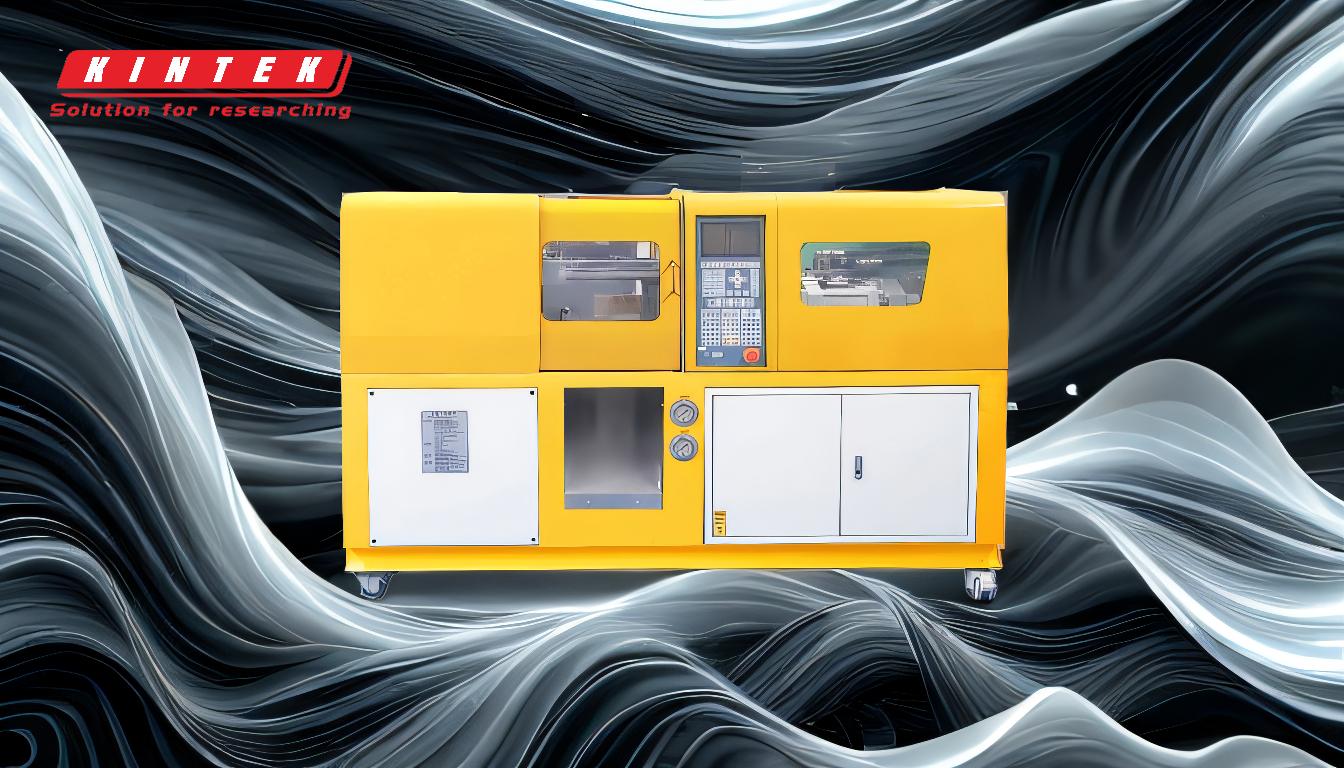
-
射出成形の定義
- 射出成形は、溶融した材料を金型に注入して部品を作る製造技術である。この製法は、同じものを素早く効率的に大量生産できるため、大量生産に広く用いられています。
-
どのように機能するか
- 材料の準備: 原料はペレット状で、射出成形機に投入される。
- 溶融: 材料が溶けるまで加熱する。
- 射出: 溶融した材料を高圧で金型に注入する。
- 冷却: 材料が金型内で冷えて固まり、その形になる。
- 射出: 固化後、金型が開き、完成品が排出される。
-
使用される材料
- プラスチック: 汎用性、費用対効果、成形のしやすさから、最も一般的な素材。例えば、ポリエチレン、ポリプロピレン、ポリスチレンなど。
- 金属: 小型で複雑な金属部品を製造するための金属射出成形(MIM)に使用される。
- ガラス: あまり一般的ではないが、高い透明度や耐熱性を必要とする特殊な用途に使用される。 光学ガラスシート は、そのような特殊材料の一例です。
-
射出成形の利点
- 高効率: 短時間で数千個の部品を生産できる。
- 高精度: 複雑で詳細な形状を高い精度で作成できます。
- 繰り返し精度: 各パーツが同一であることを保証し、大量生産に不可欠です。
- 材料の多様性: さまざまな材料に使用でき、それぞれ異なる特性を持つ。
-
用途
- 消費財: ボトルキャップ、玩具、容器など。
- 自動車: ダッシュボード、バンパー、内装トリムなどの部品。
- 医療用 注射器、手術器具、診断機器。
- 電子機器 デバイス用ハウジング、コネクター、絶縁体
-
購入者への配慮
- 金型設計: 金型設計と製作の初期費用は高くつくが、大量生産で償却できる。 プレス金型 の設計は、特定の用途のためにしばしば考慮されます。
- 材料の選択: 部品の性能と耐久性のためには、適切な材料を選択することが重要です。
- 生産量: 射出成形は、大量生産に最も費用対効果が高い。少量生産やカスタム部品の場合は、他の製造方法の方が適している場合があります。
- 品質管理: 安定した品質を確保するには、成形機や金型の定期的なメンテナンスと、完成した部品の厳密な検査が必要です。
射出成形は現代の製造業の要であり、私たちが日常的に使用する膨大な製品の生産を可能にしている。その効率性、精密さ、多用途性により、消費財から医療機器に至るまで、さまざまな産業で不可欠なプロセスとなっている。
総括表
アスペクト | 詳細 |
---|---|
定義 | 同一の部品を大量に生産する製造工程。 |
仕組み | 材料を溶かし、金型に注入し、冷却し、完成品を射出する。 |
使用材料 | プラスチック(最も一般的)、金属、ガラス。 |
利点 | 高効率、高精度、高再現性、材料の多様性。 |
用途 | 消費財、自動車、医療、エレクトロニクス産業 |
考慮事項 | 金型設計、材料選択、生産量、品質管理。 |
射出成形がお客様の生産工程にどのような革命をもたらすかをご覧ください。 今すぐご連絡ください までご連絡ください!