射出成形機は、主に射出成形プロセスを通じてプラスチック製品を製造するために使用される汎用性の高い製造ツールです。これらの機械は、プラスチック材料を溶融し、プレス金型に射出する。 プレス金型 を作り、冷却固化させて目的の形状にする。このプロセスは、ボトルキャップのような小さな部品から、自動車部品や家電製品のような大きな部品まで、さまざまな製品を製造するために産業界で広く使用されている。この技術は、その効率性、精密さ、そして無駄を最小限に抑えて同一の部品を大量に生産する能力が評価されている。
キーポイントの説明
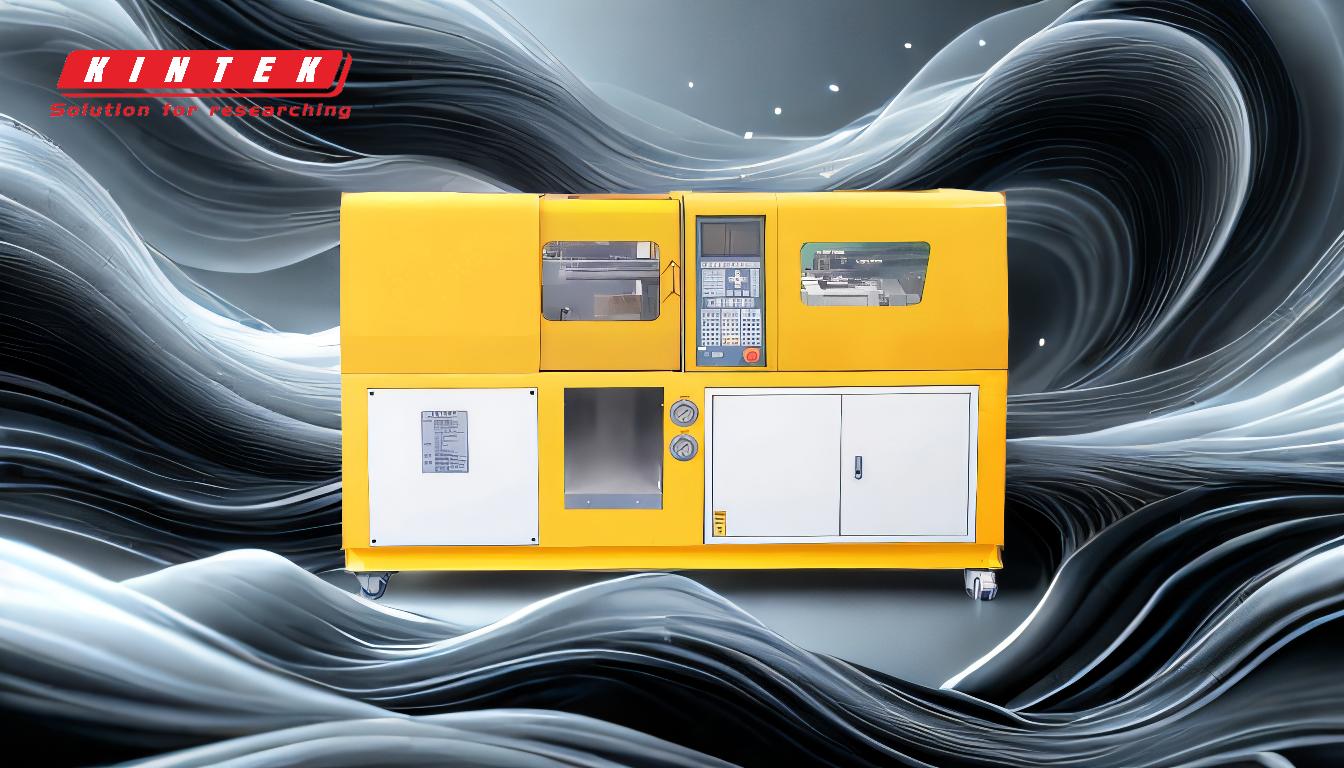
-
射出成形機の主な機能:
- 射出成形機は、金型に溶融プラスチックを射出することによってプラスチック製品を製造するように設計されています。プラスチックペレットが溶けるまで加熱し、溶けた材料を金型の空洞に押し込んで冷やし固め、目的の形状に成形します。この方法は、安定した品質のプラスチック部品を大量生産するのに非常に効率的である。
-
製品の種類:
-
射出成形機は、次のような多種多様なプラスチック製品を生産することができます:
- 小型部品:ボトルキャップ、ボタン、小さな歯車など。
- 消費財:玩具、台所用品、容器などの製品。
- 自動車部品:ダッシュボード、バンパー、内装トリムなどの部品。
- 医療機器:注射器、点滴部品、手術器具など。
- 工業用部品:工具、ハウジング、機械部品
- 包装:ペットボトル、蓋、トレイなど。
-
射出成形機は、次のような多種多様なプラスチック製品を生産することができます:
-
射出成形を利用する産業:
-
射出成形は、以下のような多くの産業で製造の要となっている:
- 自動車:軽量で耐久性のある部品に。
- コンシューマー・エレクトロニクス:ケーシング、コネクター、その他の部品用。
- メディカル:無菌精密部品用
- 包装:容器やクロージャーの作成に。
- 構造:継手、パイプ、断熱材など。
-
射出成形は、以下のような多くの産業で製造の要となっている:
-
射出成形の利点:
- 高効率:大量の部品を迅速に生産できる。
- 精度と一貫性:製品の寸法と品質の均一性を確保します。
- 材料の多様性:幅広い熱可塑性プラスチックと一部の熱硬化性プラスチックを処理できる。
- 最小限の廃棄物:余分な材料はリサイクルして再利用できることが多い。
- 複雑な形状:複雑なデザインや細かな特徴を可能にする。
-
工程概要:
-
射出成形プロセスには、いくつかの重要なステップがあります:
- 材料の準備:プラスチックペレットを機械のホッパーに投入する。
- 溶融:ペレットは機械のバレル内で加熱・溶解される。
- 射出:溶融プラスチックを高圧で金型に注入する。
- 冷却:プラスチックは金型内で冷却固化する。
- 射出:完成した部品は金型から排出され、このサイクルを繰り返す。
-
射出成形プロセスには、いくつかの重要なステップがあります:
-
使用材料:
-
射出成形機は、以下のような様々な材料を加工することができます:
- 熱可塑性プラスチック:ポリエチレン(PE)、ポリプロピレン(PP)、ポリスチレン(PS)、ポリカーボネート(PC)など。
- 熱硬化性プラスチック:エポキシ樹脂、フェノール樹脂など。
- エラストマー:フレキシブルパーツ用
- 複合材料:繊維やフィラーで強化されたプラスチックは、より優れた特性を発揮します。
-
射出成形機は、以下のような様々な材料を加工することができます:
-
カスタマイズと柔軟性:
-
射出成形機にはカスタマイズのオプションがあり、メーカーは特定の形状、サイズ、特性の部品を製造することができます。この柔軟性は、以下のような方法で実現されます:
- 金型設計:カスタム金型は、ユニークな形状や機能を製造するために作成することができます。
- 材料の選択:最終製品に求められる特性に応じて、さまざまなプラスチックを選択することができる。
- プロセスパラメーター:温度、圧力、冷却時間を調整することで、成形プロセスを最適化できる。
-
射出成形機にはカスタマイズのオプションがあり、メーカーは特定の形状、サイズ、特性の部品を製造することができます。この柔軟性は、以下のような方法で実現されます:
-
経済と環境への配慮:
- 射出成形は、生産率が高く、単位あたりのコストが低いため、大規模生産において費用対効果が高い。また、廃棄物が少なく、プラスチック材料のリサイクルが可能なため、比較的環境に優しいプロセスです。
まとめると、射出成形機は現代の製造業において不可欠なツールであり、高い精度と効率でさまざまなプラスチック製品を生産することができる。その汎用性は、金型や材料をカスタマイズする能力と相まって、様々な産業において不可欠なものとなっている。
総括表
主な側面 | 詳細 |
---|---|
主な機能 | 溶融プラスチックを金型に注入し、プラスチック製品を製造する。 |
製品の種類 | 小型部品、消費財、自動車部品、医療機器など |
対象業界 | 自動車、家電、医療、包装、建築 |
利点 | 高効率、高精度、材料の多様性、最小限の廃棄物。 |
プロセスステップ | 材料の準備、溶解、射出、冷却、射出。 |
使用材料 | 熱可塑性プラスチック、熱硬化性プラスチック、エラストマー、複合材料 |
カスタマイズ | 金型設計、材料選択、プロセスパラメータ調整。 |
経済性と環境性 | 大規模生産に適した費用対効果、リサイクル可能な素材。 |
製造工程を強化する準備はできていますか? 今すぐご連絡ください 射出成形ソリューションの詳細について