薄膜蒸着は、材料科学と工学における重要なプロセスであり、エレクトロニクス、光学、コーティングなど、さまざまな用途の基板上に薄膜を作成するために使用される。薄膜形成技術には、物理的気相成長法(PVD)と化学的気相成長法(CVD)がある。PVDは、一般的に蒸着やスパッタリングなどのプロセスを通じて、材料をソースから基板に物理的に移動させることを含み、CVDは化学反応に依存して薄膜を堆積させる。これらの他にも、原子層堆積法(ALD)やスプレー熱分解法などの方法が、特定の用途向けに独自の利点を提供している。各手法には、それぞれ異なるプロセス、利点、用途があり、薄膜製造におけるさまざまな要件に適しています。
主なポイントの説明
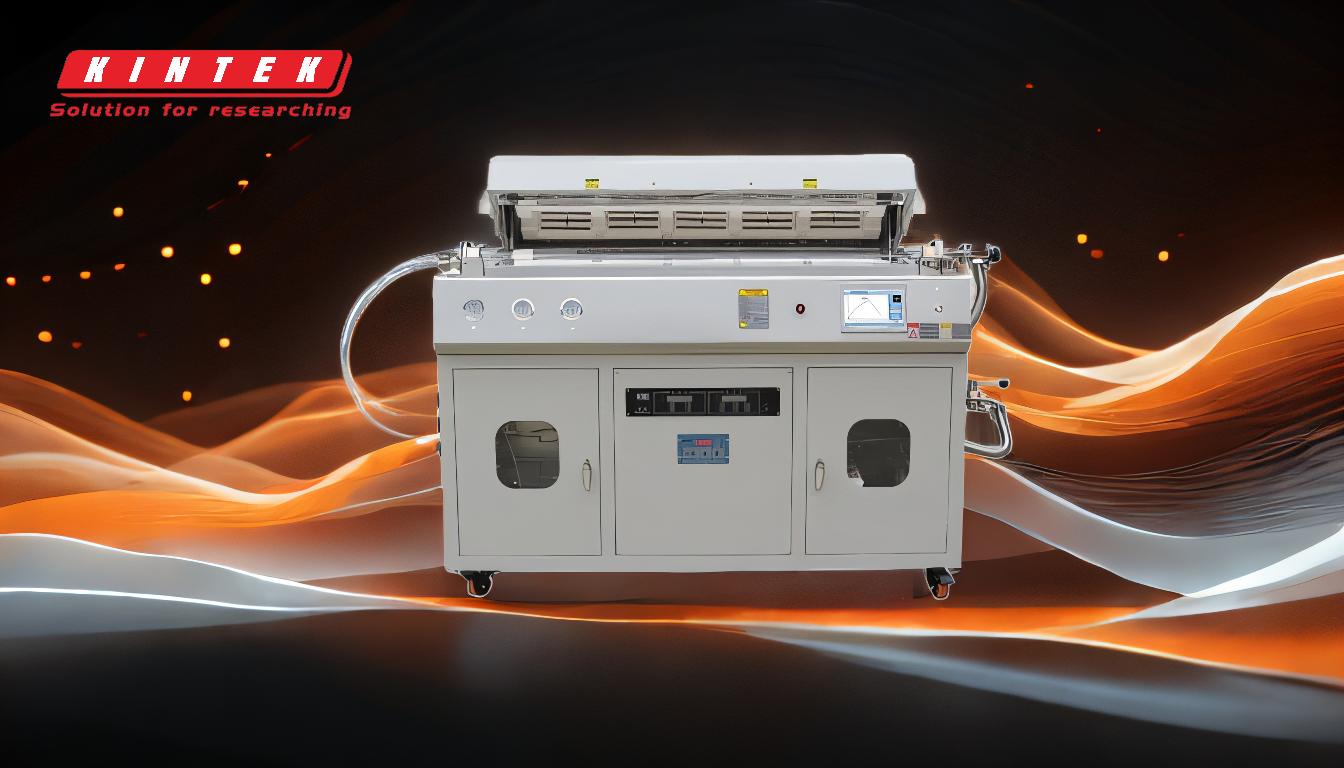
-
物理的気相成長法(PVD):
- 定義: PVDは、通常真空環境において、ソースから基板への材料の物理的な移動を伴う。
-
技術:
- 蒸発: 材料が気化するまで加熱し、基板上で凝縮させる。
- スパッタリング: 高エネルギーイオンの衝突により、固体ターゲット材料から原子が放出され、基板上に堆積する。
- 電子ビーム蒸発法: 電子ビームで原料を加熱・蒸発させる。
- 分子線エピタキシー(MBE): 高品質の結晶膜を成長させるために使用される高度に制御された蒸着法。
- 利点 高純度フィルム、良好な密着性、幅広い材料の成膜が可能。
- 用途 半導体デバイス、光学コーティング、装飾仕上げに使用される。
-
化学気相成長法(CVD):
- 定義: CVDとは、化学反応を利用して基板上に薄膜を形成することである。
-
手法
- 熱CVD: 化学反応を促進するために熱を使用する。
- プラズマエンハンスドCVD(PECVD): プラズマを使って化学反応を促進し、成膜温度を下げることができる。
- 原子層蒸着(ALD): CVDの一種で、一度に1原子層ずつ成膜するため、膜厚と均一性の制御に優れている。
- 利点 高品質で均一なフィルムで、複雑な形状にも優れた適合性を示します。
- 用途 半導体産業における高純度膜の製造や、耐摩耗性・耐腐食性コーティングの製造に広く使用されている。
-
原子層堆積法(ALD):
- 定義: ALDは、一度に1原子層ずつ成膜するCVDの特殊な形態である。
- プロセス 前駆体ガスのパルスを交互に照射し、各パルスで基板上に単一原子層を形成する。
- 利点 複雑な形状でも、膜厚と均一性の卓越した制御が可能。
- 用途 先端半導体デバイス、MEMS、ナノテクノロジーに使用される。
-
スプレー熱分解:
- 定義: 前駆体溶液を加熱した基板にスプレーし、溶媒を蒸発させて前駆体を分解させ、薄膜を形成する溶液ベースの方法。
- 利点 シンプルでコスト効率が高く、大面積蒸着に適している。
- 用途 太陽電池、透明導電性酸化物、その他の機能性コーティングの製造に使用される。
-
その他の蒸着法
- 電気めっき: 電流を利用して導電性基材上に金属の薄層を析出させる化学的方法。
- ゾル・ゲル: 溶液(ゾル)をゲルに変化させ、これを乾燥・焼結して薄膜を形成する化学プロセス。
- ディップコーティングとスピンコーティング: 基板を溶液に浸すか、溶液で回転させ、乾燥させて薄膜を形成する溶液ベースの方法。
- パルスレーザー堆積法(PLD): 高出力レーザーパルスを使用してターゲットから材料をアブレーションし、基板上に堆積させる物理的方法。
これらの方法にはそれぞれ利点と限界があり、用途によって適しているものが異なる。成膜技術の選択は、所望の膜特性、基板材料、特定のアプリケーション要件などの要因に依存する。
要約表
方法 | 主なテクニック | 利点 | 用途 |
---|---|---|---|
PVD | 蒸着、スパッタリング、電子ビーム蒸着、MBE | 高純度、密着性、広い材料範囲 | 半導体、光学コーティング、装飾仕上げ |
CVD | 熱CVD、PECVD、ALD | 高品質で均一な膜、優れた適合性 | 半導体、耐摩耗性コーティング、腐食保護 |
ALD | 原子層積層法 | 卓越した膜厚制御、複雑な形状での均一性 | 先端半導体、MEMS、ナノテクノロジー |
スプレー熱分解 | 加熱した基板に前駆体溶液を噴霧 | シンプル、コスト効率、大面積成膜に最適 | 太陽電池、透明導電性酸化物、機能性コーティング |
その他の方法 | 電気メッキ、ゾル-ゲル、ディップ/スピンコーティング、PLD | 方法による様々な利点 | エレクトロニクス、光学、コーティングを含む多様なアプリケーション |
お客様のニーズに合った理想的な薄膜形成方法を見つけてください。 今すぐ専門家にご相談ください !