粉末冶金は、複雑な形状と正確な寸法を持つ焼結部品を製造するために使用される汎用性の高い製造プロセスです。このプロセスには通常、粉末の選択、成形、焼結という3つの主要工程が含まれる。しかし、金属射出成形(MIM)、熱間静水圧プレス(HIP)、積層造形、スパークプラズマ焼結(SPS)などの高度な技術により、粉末冶金の能力は拡大している。これらの方法は、自動車、航空宇宙、切削工具などの産業向けの複雑な部品の製造を可能にする。どの方法を選択するかは、強度、硬度、寸法精度など、最終製品に求められる特性によって決まる。
キーポイントの説明
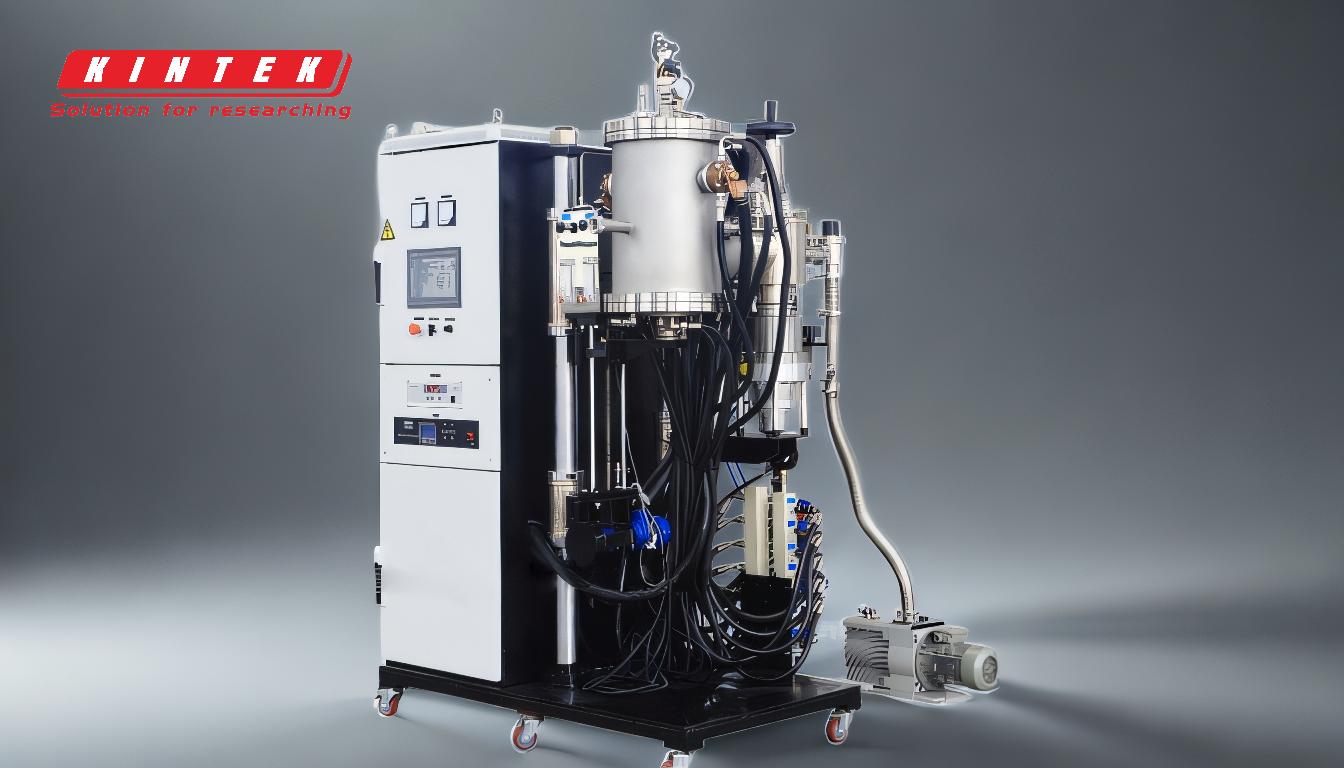
-
従来の粉末冶金(プレスと焼結)
- 粉末選択:このプロセスは、鉄、ニッケル、モリブデン、銅などの金属粉末を選択することから始まり、多くの場合、流動性と成形性を向上させるために潤滑剤と混合される。
- 成形:粉末を室温で金型に押し込み、初期強度のある部品を形成する。この工程で部品の形状と密度が決まる。
- 焼結:グリーン部分は、金属の融点ぎりぎりの温度で炉の中で加熱される。これにより粒子が結合し、材料を液化させることなく強度と硬度が向上する。酸化を防ぐために、制御された大気条件がしばしば使用される。
-
金属射出成形(MIM)
- 粉体混合:微細な金属粉末を熱可塑性バインダーと混合して原料を作る。
- 射出成形:原料を高圧で金型に注入し、グリーンパーツを形成する。
- 脱バインダー:バインダーは、熱または化学プロセスによって除去される。
- 焼結:部品は、完全な密度と機械的特性を達成するために焼結されます。MIMは、小型で複雑な部品を高精度で製造するのに理想的です。
-
熱間静水圧プレス(HIP)
- 粉末成形:金属粉末を金型に入れ、同時に高圧と高温にかける。
- 焼結:熱と圧力の組み合わせにより粉末を高密度化し、気孔率を最小限に抑えたニアネットシェイプ部品を実現します。HIPは、優れた機械的特性を必要とする高性能部品に使用されます。
-
積層造形(3Dプリンティング)
- パウダーベッドフュージョン:金属粉末をレーザーや電子ビームで選択的に溶かし、層ごとに部品を作る。
- バインダージェット:液体バインダーを粉末床に選択的に堆積させ、グリーンパーツを作成し、後に焼結する。
- 直接エネルギー蒸着:レーザーや電子ビームによって作られた溶融プールに金属粉末を投入することで、既存の部品を修復したり、材料を追加したりすることができる。積層造形は、試作品や複雑な形状の製造に最適です。
-
スパークプラズマ焼結 (SPS)
- 粉体調製:金属粉末を黒鉛製の金型に入れる。
- 焼結:パルス電流を流してプラズマを発生させ、粉体を急速に加熱する。同時に圧力を加えることで、高速で緻密化する。SPSは、低温で高密度を達成できるため、セラミックスや複合材料を含む先端材料に使用されている。
-
後処理プロセス
- 機械加工:焼結部品は、正確な寸法や表面仕上げを達成するために、追加の機械加工が必要になる場合があります。セラミックのような硬い材料には、ダイヤモンド工具や超音波加工がよく使用されます。
- 組立:セラミック部品の場合、部品の接合にはメタライゼーションとろう付けが用いられる。これは、導電性や気密封止を必要とする用途で一般的です。
- 熱処理:機械的特性を向上させるために、焼戻しや焼き入れなどの熱処理を施すこともある。
-
焼結部品の用途
- 自動車産業:焼結部品は、その強度と耐摩耗性から、ギア、カムシャフト、バルブシートなどに広く使用されています。
- 切削工具:超硬工具は、その硬度と耐久性で知られています。
- フィルター:焼結金属フィルターは、化学産業や製薬産業など、精密なろ過を必要とする用途で使用されています。
これらの方法を理解することで、メーカーは特定の性能要件とコスト考慮事項を満たす焼結部品を製造するための最も適切な技術を選択することができます。
要約表
方法 | 主な手順 | アプリケーション |
---|---|---|
従来の粉末冶金 | 粉末の選択、成形、焼結 | 自動車用ギア、カムシャフト、バルブシート |
金属射出成形(MIM) | 粉末混合、射出成形、脱バインダー、焼結 | 高精度の小型複雑部品 |
熱間静水圧プレス(HIP) | 粉末成形、高温高圧下での焼結 | 気孔率を最小限に抑えた高性能コンポーネント |
積層造形 | 粉末床溶融、バインダージェッティング、直接エネルギー堆積法 | プロトタイピング、複雑形状 |
スパークプラズマ焼結(SPS) | 粉末の調製、パルス電流と圧力による急速焼結 | セラミックスや複合材料などの先端材料 |
後処理プロセス | 機械加工、組立、熱処理 | 機械的特性と表面仕上げの向上 |
お客様のニーズに最適な粉末冶金ソリューションをご紹介します。 今すぐ専門家にお問い合わせください !