薄膜蒸着は、エレクトロニクス、光学、コーティングなど様々な産業において重要なプロセスである。しかし、最終製品の品質、性能、スケーラビリティに影響するいくつかの欠点や課題があります。これらの課題には、均一性、密着性、汚染、基板適合性、応力管理、純度、費用対効果に関する問題が含まれる。さらに、蒸着や冷却時の温度制約、一貫した厚みや純度を達成することの難しさも、プロセスをさらに複雑にしている。これらの欠点に対処するには、望ましい膜特性と性能を確保するための慎重な最適化と高度な技術が必要です。
キーポイントの説明
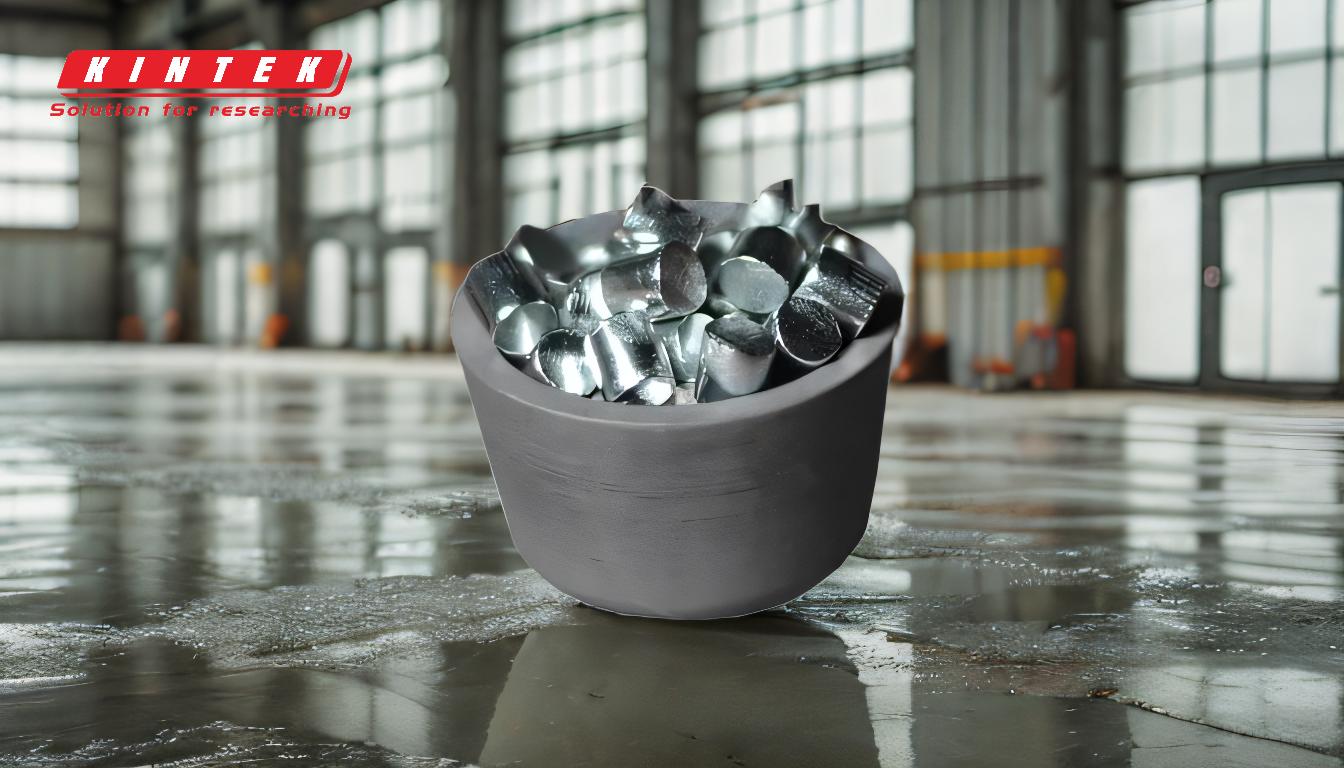
-
均一性と厚み制御:
- 基板全体で均一な膜厚を達成することは、薄膜蒸着における重要な課題である。不均一性は膜特性のばらつきにつながり、エレクトロニクスや光学などの用途における性能に影響を与える。
- 不均一性の要因には、蒸着速度の不均一、基板表面の凹凸、蒸着プロセス中の温度やガス流の変動などがある。
- 原子層堆積法(ALD)やプロセス制御の改善のような高度な技術は、これらの問題を軽減するのに役立つが、多くの場合、より高いコストがかかる。
-
接着と剥離:
- 薄膜と基材との適切な接着は、コーティングの耐久性と機能性にとって極めて重要である。密着性が悪いと、フィルムが基材から剥離するデラミネーションが発生します。
- 層間剥離は、熱膨張係数の不一致、表面汚染、不十分な表面処理によって引き起こされることが多い。
- 解決策としては、プラズマ洗浄や接着促進層の使用などの表面処理を行い、フィルムと基材との接着を強化する。
-
汚染と純度:
- 成膜プロセス中の汚染は、薄膜の品質を著しく低下させる。不純物は薄膜の電気的、光学的、機械的特性を変化させます。
- 汚染源としては、蒸着室内の残留ガス、基板からの粒子、蒸着材料中の不純物などがある。
- 汚染を最小限に抑えるためには、高い清浄度を維持し、超高純度材料を使用し、厳格な工程管理を実施することが不可欠である。
-
基板適合性:
- 成膜プロセスやフィルム材料との適合性が求められるため、基板材料の選択は非常に重要である。相性が悪いと、接着不良、応力誘起クラック、フィルムと基板間の化学反応などの問題を引き起こす可能性がある。
- 例えば、高温蒸着プロセスは、熱安定性の低い基板には適さない場合がある。
- 基板材料と成膜条件を注意深く選択することは、互換性を確保し、所望の膜特性を達成するために必要である。
-
ストレスと歪みの管理:
- 薄膜は、フィルムと基板間の熱膨張係数の違いや、成膜プロセス自体による内部応力がしばしば発生します。これらの応力は、フィルムのクラック、座屈、剥離につながる可能性があります。
- 応力管理技術には、温度や圧力などの蒸着パラメーターを最適化することや、応力緩和層やアニールプロセスを使用して残留応力を低減することなどが含まれる。
- しかし、これらの技術は成膜プロセスに複雑さとコストを加えることになる。
-
温度の制約:
- 多くの薄膜蒸着プロセスでは高温が要求されるため、基板材料の選択が制限され、熱損傷のリスクが高まる。
- 例えば、高温プロセスは、ポリマーやその他の温度に敏感な材料には適さない場合がある。
- プラズマエンハンスト化学気相成長法(PECVD)のような低温成膜技術も代替技術として使用できるが、膜質や成膜速度の点で限界がある。
-
冷却による応力:
- 成膜後の冷却段階で、薄膜と基板との熱収縮率の違いにより、薄膜に望ましくない応力が発生することがある。
- こうした応力は、亀裂や剥離といった欠陥につながり、フィルムの完全性を損なう。
- 段階的な冷却や成膜後のアニールは、これらの応力を緩和するのに役立つが、これらのステップはプロセスに時間と複雑さを加える。
-
コストとスケーラビリティ:
- 薄膜蒸着プロセスは、特に高度な技術や高純度材料が必要な場合、高価になることがある。装置、メンテナンス、プロセスの最適化にかかるコストは、特に大規模生産の場合、大きな障壁となりうる。
- 一貫した膜質を維持しながら蒸着プロセスをスケールアップすることは、もう一つの課題である。温度やガスフローなどの蒸着条件のばらつきは、スケールが大きくなるほど顕著になり、不均一性や欠陥につながる可能性がある。
- コストとスケーラビリティのバランスを取るには、成膜パラメータを慎重に最適化し、膜質を損なうことなくコスト効率の高い材料と技術を使用する必要がある。
結論として、薄膜蒸着は幅広い用途を持つ強力な技術であるが、課題がないわけではない。均一性、密着性、汚染、基板適合性、応力管理、費用対効果に関する問題に対処することは、最新のアプリケーションの要求を満たす高品質な膜を製造するために不可欠である。高度な技術と入念なプロセスの最適化は、これらの欠点を克服するのに役立ちますが、多くの場合、複雑さとコストの増加を伴います。
総括表:
チャレンジ | 説明 | ソリューション |
---|---|---|
均一性と厚み | 不均一な厚みはフィルムの性能に影響する。 | ALDや改善されたプロセス制御のような高度な技術を使用する。 |
接着と剥離 | 接着不良はフィルム剥がれの原因となる。 | 表面処理(プラズマ洗浄など)や接着促進層を施す。 |
汚染と純度 | 不純物はフィルムの品質を劣化させる。 | 清潔さを保ち、超高純度材料を使用し、厳格な管理を行う。 |
基板適合性 | 不適合な基材は、接着不良やクラックの原因となる。 | 適合する材料を選択し、蒸着条件を最適化する。 |
ストレスとひずみ | 内部応力は亀裂や剥離の原因となる。 | 蒸着パラメーターを最適化し、応力緩和層またはアニールを使用する。 |
温度の制約 | 高温のため、基板の選択肢が限られる。 | PECVDのような低温技術を使う。 |
冷却による応力 | 冷却中の応力は欠陥の原因となる。 | 徐冷または蒸着後アニールを実施する。 |
コストとスケーラビリティ | コスト高と規模拡大の課題は、大規模生産に影響する。 | パラメータを最適化し、品質に妥協することなく費用対効果の高い材料を使用する。 |
薄膜成膜の課題克服にお困りですか? 専門家にご相談ください オーダーメイドのソリューションのために!