サーマル・クラッキングは、石油産業で使用されるプロセスで、熱を加えることにより、大きな炭化水素分子をより小さく、より価値のあるものに分解する。このプロセスは、ガソリン、ディーゼル、その他の石油化学製品などの軽質留分を生産するために極めて重要である。熱分解の条件は、温度、圧力、滞留時間、原料の種類など、いくつかの要因に影響される。これらの条件を理解することは、プロセスを最適化し、望ましい製品収率を達成するために不可欠である。以下では、熱分解に影響を与える主な要因と、それらがどのように相互作用して望ましい結果を生み出すのかを探ります。
キーポイントの説明
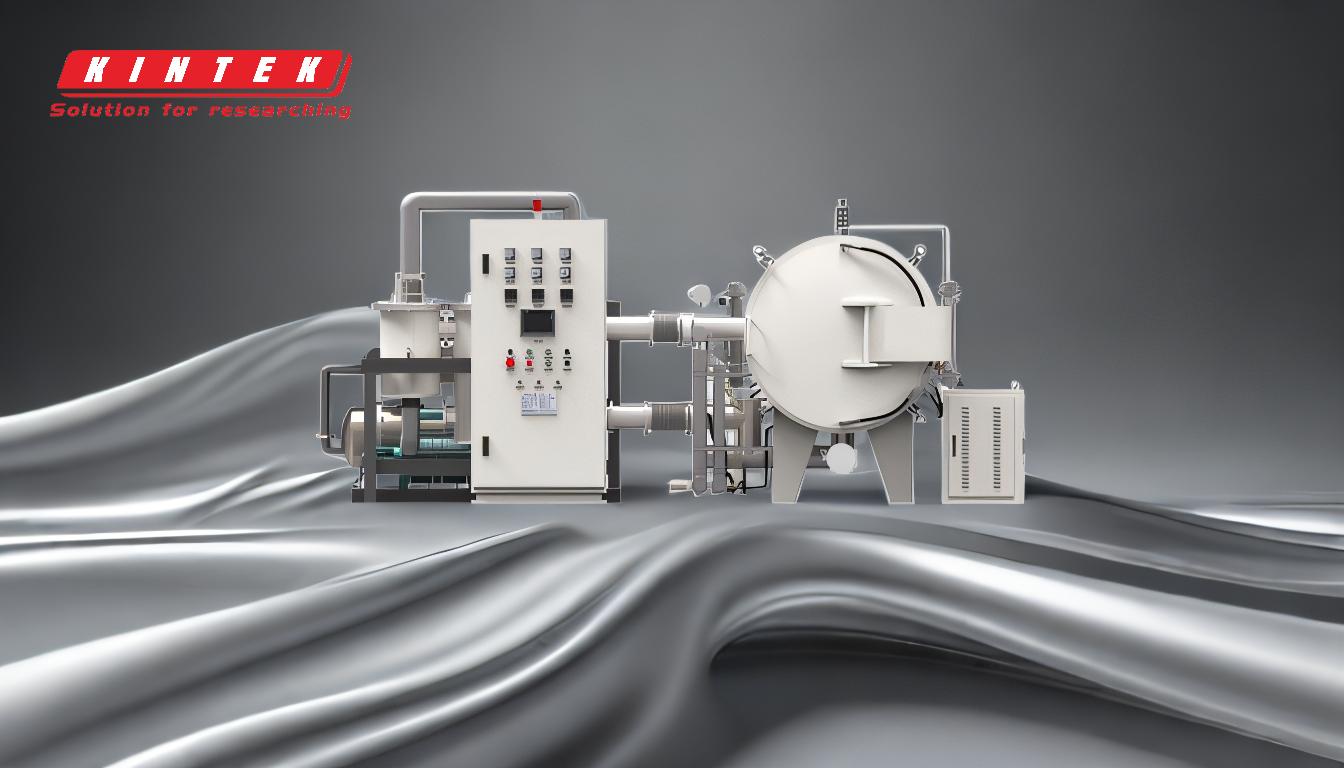
-
温度:
- 役割:温度は、熱分解における最も重要な要因のひとつである。より高い温度は、大きな炭化水素分子の化学結合を切断するのに必要なエネルギーを提供する。
- 最適範囲:通常、熱分解は450℃~750℃で起こる。正確な温度は、原料の種類と目的とする製品によって異なる。
- 影響:一般に、温度が高いほど分解率が高まり、より軽い炭化水素の生産につながる。しかし、過度に高温になると、コーキング(固形炭素の沈殿物の形成)など、望ましくない副反応を引き起こす可能性がある。
-
圧力:
- 役割:圧力は炭化水素の相と分解反応速度に影響する。圧力が低いとガス状生成物が生成されやすく、圧力が高いと液状生成物が多くなる。
- 最適範囲:熱分解は、通常1~10気圧の低~中程度の圧力で行われることが多い。圧力の選択は、所望の製品スレートと使用される特定のクラッキングプロセスに依存する。
- 影響:圧力が低いと軽い炭化水素の生成が促進されるが、コーキングのリスクも高まる。より高い圧力は、コーキングを抑えることができるが、より軽い製品の収率を低下させる可能性がある。
-
滞留時間:
- 役割:滞留時間とは、原料が分解条件にさらされる時間を指す。クラッキングの程度と生成物の分布を制御するために重要である。
- 最適範囲:滞留時間はプロセスによって大きく異なり、数秒から数分の幅がある。より短い滞留時間は、通常、水蒸気クラッキングのようなプロセスで使用され、より長い滞留時間は、遅延コークス化で使用される。
- 影響:滞留時間が長いと、より広範囲な分解が可能になり、軽量製品の収率が向上する。しかし、過剰な滞留時間は過剰分解につながり、不要な副産物を生成し、コーキングを増加させる。
-
原料組成:
- 役割:炭化水素原料の種類は分解プロセスに大きく影響する。原料が異なれば分子構造も異なり、クラッキング挙動に影響を与える。
- 原料の種類:一般的な原料には、ナフサ、軽油、残渣などがある。ナフサのような軽い原料はクラッキングが容易で、軽い製品の収率が高いが、残渣のような重い原料はより厳しい条件を必要とし、より多くの副産物を生産する。
- 影響:原料の選択は、最適な分解に必要な温度、圧力、滞留時間に影響する。より重い原料は、より高い温度とより長い滞留時間を必要とするが、コーキングのリスクを高め、より複雑な製品スレートが生成される可能性がある。
-
触媒(該当する場合):
- 役割:伝統的な熱分解では触媒を使用しないが、接触分解などの最新のプロセスでは、分解反応を促進するために触媒を使用するものもある。
- 影響:触媒は、分解に必要な活性化エネルギーを低下させ、より低い温度と圧力でプロセスを行うことを可能にする。これにより、分解プロセスの選択性が向上し、所望の生成物の収率が高まり、不要な副生成物が減少する。
-
リアクター設計:
- 役割:熱分解に使用される反応器の設計は、プロセスの効率と有効性に影響する。リアクターの設計は、熱伝導、混合、滞留時間の分布に影響する。
- リアクターの種類:一般的な反応器のタイプには、管状反応器、流動床反応器、遅延コークス化ドラムなどがある。各タイプには、熱伝達、滞留時間制御、運転のしやすさの点で長所と短所がある。
- インパクト:反応器設計の選択は、反応器内の温度と圧力プロファイルに影響を与え、クラッキングの程度と生成物の分布に影響を与える。適切な反応器設計は、最適な分解条件を達成し、不要な副反応を最小限に抑えるために不可欠である。
-
急冷:
- 役割:クエンチングとは、クラッキングした製品を急速に冷却し、それ以上のクラッキング反応を止めることである。これは、最終製品の分布を制御するために非常に重要である。
- 方法:急冷は、水、蒸気、その他の冷却媒体を用いて行うことができる。急冷の方法と速度は、具体的なプロセスと所望の製品スレートに依存する。
- 影響:効果的な焼き入れは、過度のクラッキングや不要な副生成物の生成を防ぎ、望ましい製品分布を維持するのに役立ちます。また、下流の装置におけるコーキングのリスクを低減するのにも役立つ。
要約すると、熱分解の条件は、温度、圧力、滞留時間、原料組成、および反応器の設計の組み合わせによって決定される。これらの各要因は、分解プロセスの効率と最終製品の品質を決定する上で重要な役割を果たす。これらの条件を注意深く制御することで、オペレーターは、不要な副生成物やコーキングなどの運転上の問題を最小限に抑えながら、軽質炭化水素の望ましい混合物を生産するために分解プロセスを最適化することができる。
要約表
ファクター | 役割 | 最適範囲 | 影響 |
---|---|---|---|
温度 | 炭化水素の結合を切断するエネルギーを与える | 450°C~750°C | より高い温度はクラッキングを増加させるが、コーキングを引き起こす可能性がある |
圧力 | クラッキング反応の相と速度に影響 | 1~10気圧 | 圧力が低いほど軽い炭化水素を好むが、コーキング・リスクが増加する可能性がある。 |
滞留時間 | クラッキングの程度と製品分布をコントロール | 数秒から数分 | 時間が長いほど軽量歩留まりは向上するが、過クラッキングのリスクがある。 |
原料 | 分子構造に基づく分解挙動への影響 | ナフサ、軽油、残渣 | 軽い原料は割れやすく、重い原料はより厳しい条件を必要とする。 |
リアクターの設計 | 伝熱、混合、滞留時間分布に影響 | 管状、流動床、遅延コークス化ドラム | 効率と製品分布に影響 |
急冷 | 製品を急速に冷却し、ひび割れを止める。 | 水、蒸気、その他の冷却媒体 | 製品分布を維持し、コーキングリスクを低減 |
専門家による指導で熱分解プロセスを最適化します。 今すぐご連絡ください !