焼結は金属製造における重要なプロセスであり、数多くの利点を提供するため、高性能部品の製造に適した方法となっている。粉末材料を融点以下に加熱して粒子を結合させ、材料特性と構造的完全性を向上させる。主な利点としては、強度の向上、気孔率の減少、電気および熱伝導率の改善、複雑な形状の製造能力などが挙げられます。焼結はまた、材料組成の調整、費用対効果、材料選択の多様性を可能にする。これらの利点により、焼結は金属部品の精度、耐久性、一貫性を必要とする産業において不可欠なものとなっています。
キーポイントの説明
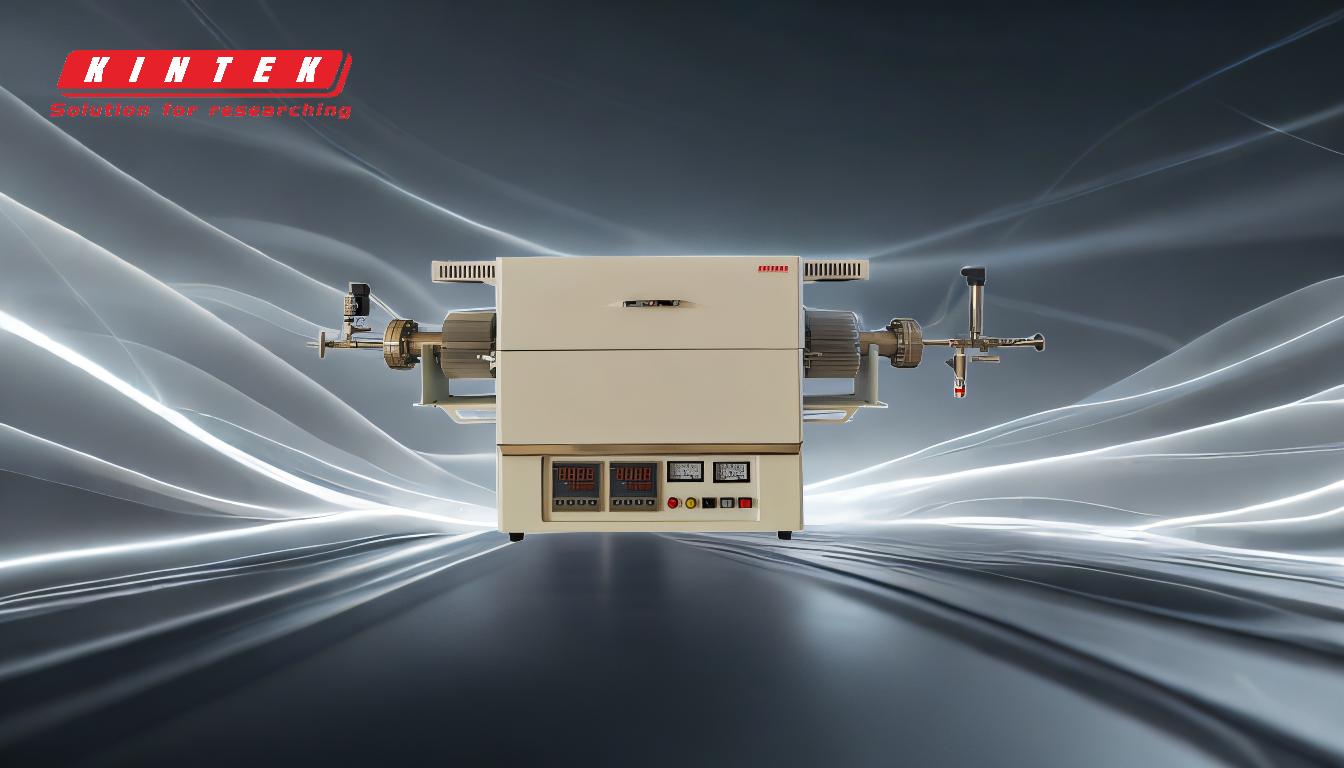
-
強化された素材特性:
- 強度と耐久性:焼結により粒子間に焼結ネックが形成され、気孔が減少し、材料全体の強度と耐久性が向上します。これは、高い応力や摩耗を受ける部品に特に有益です。
- 電気伝導率と熱伝導率:このプロセスは、気孔率を低減し、粒子の結合を強化することにより、電気および熱伝導性を向上させ、効率的な熱または電気の伝達を必要とする用途に最適です。
- 透光性と透明性:材料によっては、焼結によって半透明性や透明性を高めることができ、光学部品のような特殊な用途に役立ちます。
-
気孔率の低減:
- 焼結により気孔が効果的に減少し、より緻密で均一な材料が得られます。これは、フィルター、触媒、高圧部品など、構造的完全性と漏れ防止が不可欠な用途にとって極めて重要です。
-
複雑な形状の製造:
- このプロセスは、従来の製造方法では困難または不可能であった複雑なデザインや複雑な形状を持つ部品の製造を可能にする。これは、航空宇宙、自動車、医療機器などの業界で特に有利です。
-
オーダーメイドの材料組成:
- 焼結により、異なる元素(ニッケル、銅、グラファイトなど)を材料マトリックスに統合することが可能になり、耐摩耗性、熱安定性、電気的性能の向上など、カスタマイズされた特性を実現することができます。
-
費用対効果:
- 溶融の必要性をなくし、材料の無駄を減らすことで、焼結は費用対効果の高い製造方法です。また、潤滑剤の使用を最小限に抑え、表面酸素を減少させることで、製造コストをさらに下げることができます。
-
材料選択の多様性:
- 焼結は、高融点金属、セラミックス、複合材料など、幅広い材料に適用できる。この汎用性により、多様な産業や用途に適しています。
-
生産における一貫性とコントロール:
- 焼結プロセスでは、材料特性と寸法を正確に制御できるため、バッチ間で一貫した品質と性能を確保できます。これは、高い信頼性と精度を必要とする産業にとって非常に重要です。
-
特殊産業におけるアプリケーション:
- 焼結は、ベアリング、宝飾品、ヒートパイプ、散弾銃の砲弾など、さまざまな製品の製造に使用されている。フィルターや触媒の)ガス吸収性のような特定の特性を向上させる能力は、ニッチな用途において非常に貴重である。
要約すると、焼結は、コスト削減と設計の柔軟性を提供しながら、金属部品の特性を大幅に向上させる多用途で効率的なプロセスである。気孔率を減らし、強度を高め、複雑な形状を可能にするその能力により、焼結は現代の金属生産の要となっている。
総括表
主な利点 | 特徴 |
---|---|
強化された強度と耐久性 | 気孔を減らし、強度を高め、耐摩耗性を向上させます。 |
導電性の向上 | 電気伝導性と熱伝導性を高め、熱とエネルギーの効率的な伝達を実現。 |
気孔率の低減 | 高圧用途向けに、より高密度で気密性の高い材料を製造。 |
複雑形状の製造 | 特殊産業向けの複雑なデザインや形状を可能にします。 |
オーダーメイドの材料構成 | 耐摩耗性、熱安定性、電気的性能のカスタマイズが可能。 |
費用対効果 | 材料の無駄を省き、溶融をなくし、生産コストを下げる。 |
材料選択の多様性 | 金属、セラミック、複合材など、さまざまな業種に適しています。 |
安定した生産品質 | 高性能アプリケーションのための信頼できる正確な材料特性を保証します。 |
焼結が金属製造工程をどのように変えることができるかをご覧ください。 今すぐ専門家にお問い合わせください !