冷間加工と熱間加工は2つの基本的な金属成形プロセスで、それぞれに明確な利点と欠点がある。冷間加工では、金属を再結晶温度以下で成形するため、強度と硬度は向上するが、延性が低下する可能性がある。一方、熱間加工は再結晶温度以上で行われ、変形しやすく延性が向上するが、強度が低下することが多い。これらの方法のどちらを選択するかは、希望する材料特性、コスト、特定の用途によって決まる。以下では、熱間加工と比較した場合の冷間加工の主な利点と欠点について説明する。
主なポイントを説明します:
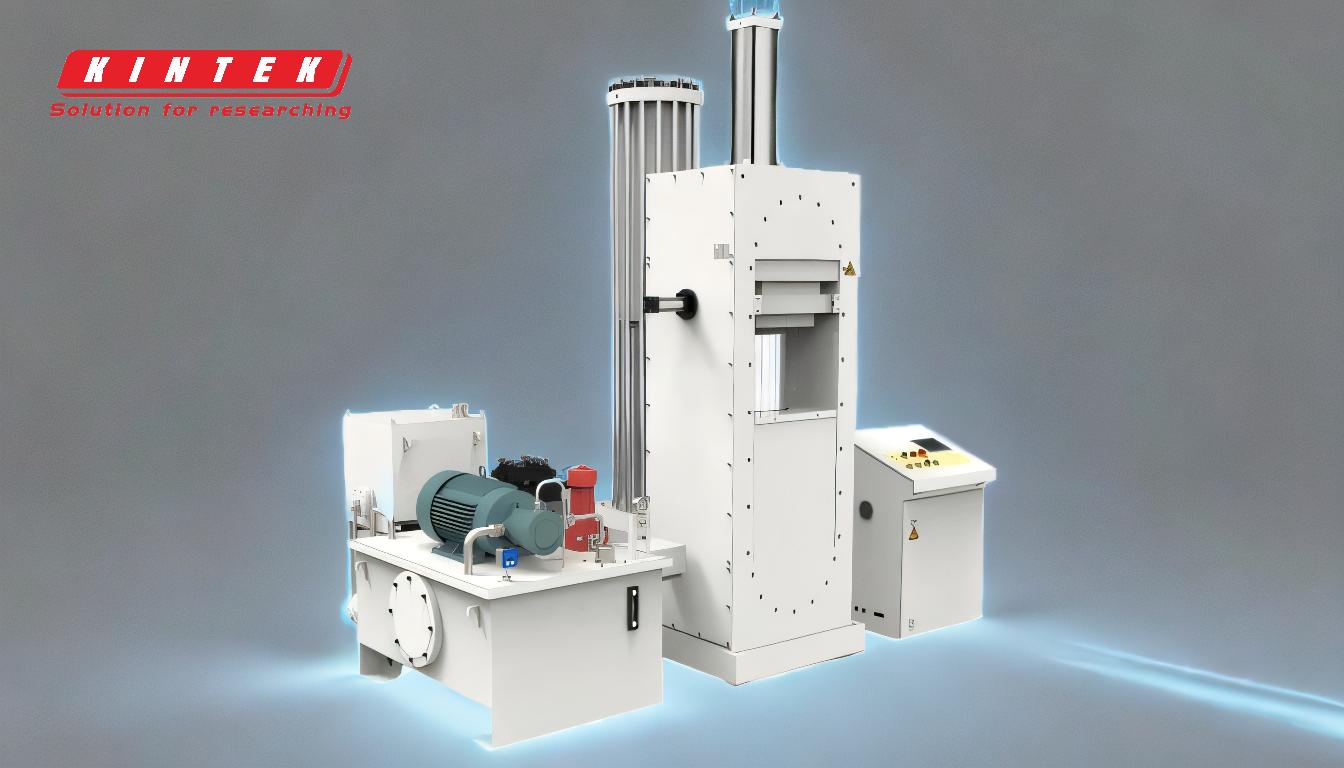
-
冷間加工の利点
-
機械的性質の向上:
- 冷間加工は、ひずみ硬化により金属の強度と硬度を向上させる。そのため、高い強度を必要とする用途に適しています。
-
より良い表面仕上げ:
- このプロセスにより、より滑らかで精密な表面仕上げが得られ、美観上または機能上望ましい場合が多い。
-
寸法精度:
- 冷間加工は、公差を厳しくし、寸法をより正確に制御できるため、高精度を必要とする用途に最適です。
-
加熱不要:
- 冷間加工は室温で行われるため、加熱の必要がなく、高温加工に伴うエネルギー消費とコストを削減できる。
-
機械的性質の向上:
-
冷間加工の欠点
-
延性の低下:
- このプロセスは金属の延性を著しく低下させるため、より脆くなり、応力下で割れやすくなる。
-
必要な力が大きい:
- 冷間加工は、熱間加工に比べ、金属を変形させるためにより大きな力とエネルギーを必要とする。
-
形状の複雑さに制限がある:
- 金属の延性が低下しているため、広範囲な変形が制限される。
-
残留応力:
- 冷間加工は、材料に残留応力をもたらし、時間の経過とともに歪みや破損につながる可能性がある。
-
延性の低下:
-
熱間加工の利点
-
延性の向上:
- 熱間加工は、金属をより容易に変形させることができるため、複雑な形状や大型部品の成形に適しています。
-
必要な力が小さい:
- 冷間加工に比べ少ない力で加工できるため、機械への負担が少なく、エネルギー消費も抑えられる。
-
結晶粒の微細化:
- 熱間加工は金属の結晶粒組織を微細化し、機械的特性と全体的な性能を向上させる。
-
残留応力の除去:
- 熱間加工に伴う高温が内部応力を緩和し、より 安定した均一な材料をもたらす。
-
延性の向上:
-
熱間加工の欠点
-
強度と硬度の低下:
- 熱間加工された金属は、一般的に冷間加工された金属に比べて強度と硬度が低い。
-
表面仕上げの悪さ:
- 高温により酸化やスケーリングが生じ、表面仕上げが粗くなり、追加加工が必要になる場合がある。
-
寸法の不正確さ:
- 熱間加工は精度が低いため、公差が広くなり、最終寸法の制御が難しくなることが多い。
-
エネルギー消費:
- 金属を高温に加熱する必要があるため、エネルギー消費と運用コストが増加する。
-
強度と硬度の低下:
-
アプリケーションの考慮事項
-
材料の選択:
- 冷間加工と熱間加工のどちらを選択するかは、材 料の特性と最終用途に求められる特性によって決まる。例えば、高強度用途には冷間加工が、複雑な形状には熱間加工が適している。
-
コストと効率:
- 小規模生産や高精度が要求される場合は、冷間加工の方がコスト効率に優れる場合があるが、大規模生産では熱間加工の方が効率的な場合が多い。
-
環境への影響:
- 冷間加工は高温加工がないため環境への影響が少なく、場合によってはより持続可能な選択肢となる。
-
材料の選択:
結論として、冷間加工と熱間加工にはそれぞれ独自の長所 と短所があり、どちらを選択するかは用途の具体的な要 件によって決まる。冷間加工は、強度、精度、表面仕上げを向上 させるが、その代償として延性が低下し、より大きな 力を必要とする。一方、熱間加工は、延性が向上し、変形しやすくなるが、強度が低下し、表面仕上げが粗くなる可能性がある。これらのトレードオフを理解することは、最も適切な金属成形プロセスを選択する上で極めて重要である。
総括表
側面 | 冷間加工 | 熱間加工 |
---|---|---|
強度と硬度 | ひずみ硬化により増加 | 一般的に低い |
延性 | 低下し、金属がより脆くなる | 強化:変形しやすくなる |
表面仕上げ | より滑らかで精密 | 酸化とスケーリングによる粗さ |
寸法精度 | より厳しい公差と優れた精度 | 精度が低く、公差が広い |
エネルギー消費 | 加熱が不要なため低い | 高温処理のため高い |
形状の複雑さ | 延性の低下による制限 | 複雑な形状に適している |
残留応力 | 残留応力の発生 | 残留応力を除去 |
適切な金属成形プロセスの選択にお困りですか? 当社の専門家に今すぐご連絡ください オーダーメイドのソリューションを