射出成形は、さまざまなプラスチック製品を製造するために使用される汎用性の高い製造プロセスです。射出成形は、溶融した材料を プレス金型 を使用し、高精度で再現性の高い部品を作ることができます。この方法は、効率性、拡張性、複雑な形状を最小限の無駄で製造できる能力により、大量生産に理想的である。一般的な用途としては、自動車部品、消費財、包装、医療機器などがある。射出成形を効果的に利用するには、プロセスを理解し、適切な材料を選択し、金型を設計し、生産パラメーターを最適化する必要があります。以下に、射出成形の主要な側面について詳しく説明する。
キーポイントの説明
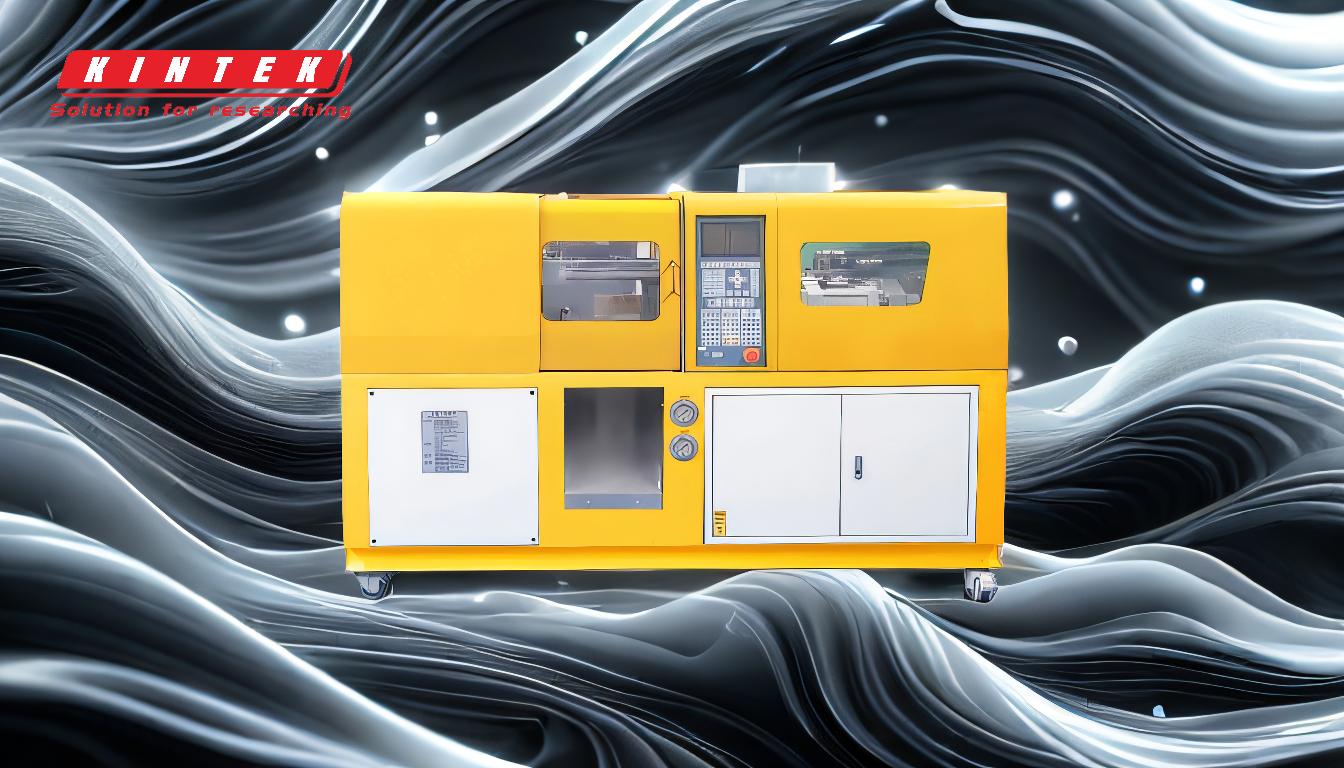
-
射出成形プロセスを理解する:
- 射出成形では、プラスチックのペレットを溶けるまで加熱し、溶けた材料を高圧で金型のキャビティに注入する。
- 材料は冷えて固まり、金型の形状になり、その後部品が射出される。
- この工程は高度に自動化されており、大量生産に適している。
-
射出成形の用途:
- 自動車部品:ダッシュボード、バンパー、内装トリムなどの部品は、その耐久性と精度の高さから射出成形が一般的である。
- 消費財:玩具、ボトルキャップ、保存容器などがこの方法で大量生産されている。
- 医療機器:注射器、点滴部品、手術器具は、射出成形の無菌性と精度の恩恵を受けています。
- パッケージング:薄肉容器、キャップ、クロージャーを効率的に生産することができます。
-
材料の選択:
- 熱可塑性プラスチック:一般的に使用される素材には、ポリエチレン(PE)、ポリプロピレン(PP)、ポリスチレン(PS)、アクリロニトリル・ブタジエン・スチレン(ABS)などがある。これらの材料は、汎用性、強度、コストパフォーマンスの高さから選ばれている。
- エンジニアリングプラスチック:高性能の用途には、耐熱性や機械的特性からポリカーボネート(PC)やナイロンなどの素材が使用される。
- 添加剤:充填剤、着色剤、強化剤は、強度、柔軟性、外観などの材料特性を向上させるために添加することができます。
-
金型の設計と製造:
- 金型設計:金型は、希望する部品の形状に合わせて精密に設計されなければならない。ゲートの位置、冷却チャンネル、排出機構などの要素は非常に重要です。
- 金型材料:金型は通常、生産量と部品の複雑さに応じて、スチールまたはアルミニウムから作られます。
- 金型費用:初期の金型設計と製造にはコストがかかるが、生産量が多く、単位あたりのコストが低いため、そのコストは相殺される。
-
生産の最適化:
- サイクルタイム:効率を上げるためには、サイクルタイムの短縮が不可欠です。これには、冷却時間、射出速度、金型設計の最適化が含まれる。
- 品質管理:部品の品質を一定に保つには、温度、圧力、材料の流れなどのパラメータを監視する必要があります。
- オートメーション:ロボットや自動化システムを取り入れることで、生産スピードと一貫性をさらに高めることができます。
-
射出成形の利点:
- 高効率:このプロセスは高速でスケーラブルであるため、大量生産に最適である。
- 複雑な形状:射出成形は、高精度で複雑な形状を作ることができます。
- 材料の多様性:幅広い材料が使用でき、部品特性のカスタマイズが可能。
- 低廃棄物:余分な材料はリサイクルできることが多く、廃棄物を減らすことができる。
-
課題と考察:
- 高いイニシャルコスト:金型の設計と製造にかかるコストは、少量生産の場合、法外なものになる可能性がある。
- 設計上の制限:部品は成形性を考慮して設計する必要があり、特定の形状が制限されることがある。
- 材料の制限:すべての材料が射出成形に適しているわけではなく、特殊な設備が必要な場合もあります。
-
射出成形の今後の動向:
- サステイナブル素材:環境負荷を低減するため、生分解性素材やリサイクル素材の使用を増やす。
- 先端技術:リアルタイムモニタリングとプロセス最適化のためのIoTとAIの統合。
- マイクロモールド:医療用や電子機器用の極めて小さく精密な部品を製造する技術の開発。
これらのポイントを理解することで、射出成形を消費財から工業部品まで幅広い用途に効果的に活用することができる。このプロセスには数多くの利点があるが、その課題を克服し、可能性を最大限に引き出すためには、入念な計画と最適化が不可欠である。
総括表
側面 | 主な内容 |
---|---|
工程 | プラスチックペレットを加熱し、金型に溶融材料を注入し、部品を射出する。 |
用途 | 自動車部品、消費財、医療機器、包装。 |
素材 | 熱可塑性プラスチック(PE、PP、PS、ABS)およびエンジニアリングプラスチック(PC、ナイロン)。 |
金型設計 | 精密な形状、ゲートの位置、冷却チャンネル、排出機構。 |
利点 | 高効率、複雑な形状、材料の多様性、廃棄物の少なさ。 |
課題 | 初期コストの高さ、設計上の制限、材料の制約。 |
今後のトレンド | 持続可能な材料、IoT/AI統合、マイクロ成形。 |
射出成形で生産を最適化する準備はできていますか? 今すぐご連絡ください までご連絡ください!