蒸着プロセス、特に化学蒸着(CVD)は、基板上に材料の薄膜を蒸着させるのに用いられる高度な製造技術である。このプロセスには、基板表面へのガス状反応物質の輸送、これらの反応物質の吸着、膜形成につながる化学反応、副生成物の除去など、いくつかの重要なステップが含まれる。CVDは、物理的プロセスではなく化学反応に依存する点で、物理的蒸着(PVD)と区別される。電子機器から保護膜に至るまで、高品質で耐久性のあるコーティングやフィルムを作るために、様々な産業で広く使用されています。
キーポイントの説明
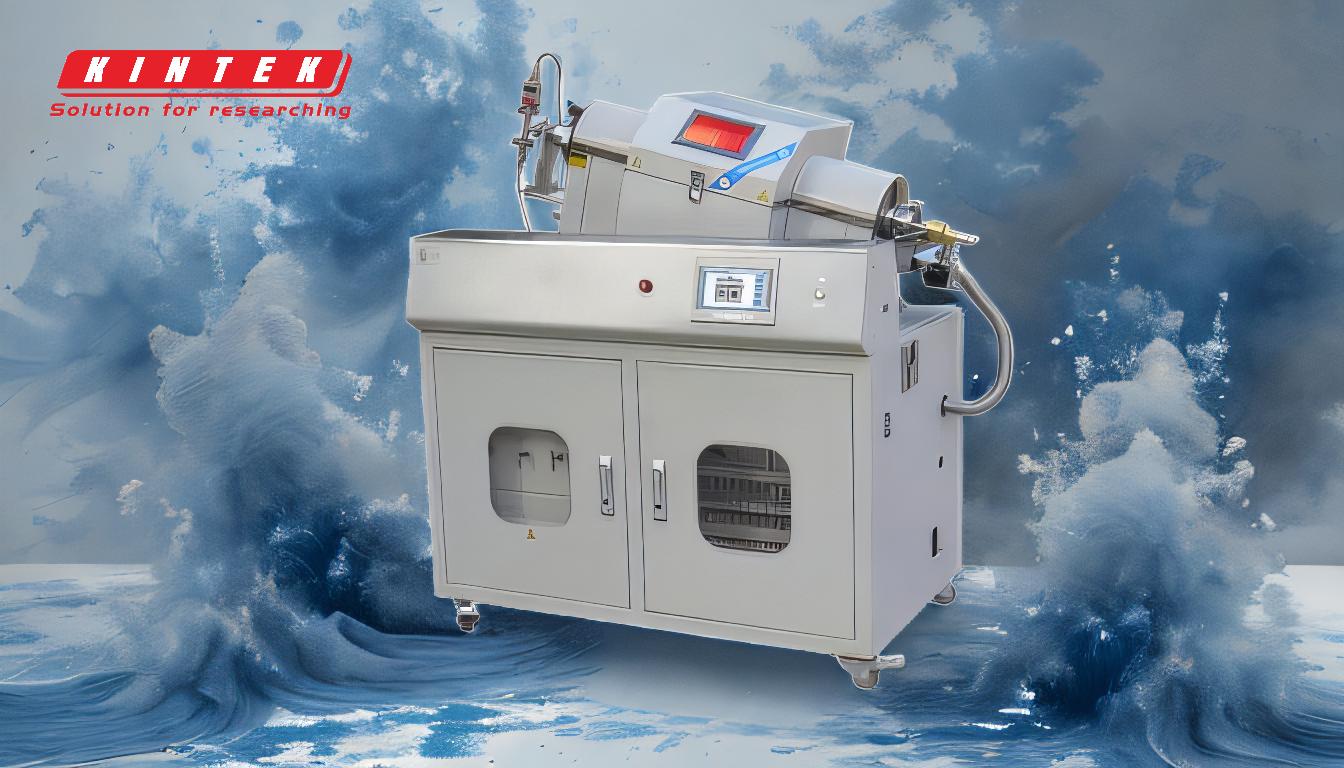
-
化学気相成長(CVD)の定義:
- CVDは、加熱された基板上に、気相中の化学反応によって固体膜を形成する薄膜堆積プロセスである。このプロセスでは通常、原子、分子、またはその両方の組み合わせが基板表面で反応し、薄い固体膜を形成する。蒸発やスパッタリングなどの物理的プロセスに依存する物理的気相成長(PVD)とは異なり、CVDは表面を介した化学反応が特徴である。
-
CVDのステップ:
- 反応ガス種の輸送:このプロセスは、ガス状の反応物を基材表面に輸送することから始まる。これらの反応物質は通常、容易に気化する揮発性化合物である。
- 表面への吸着:気体種が基質に到達すると、その表面に吸着する。このステップは、その後の化学反応のための反応物を準備するため、非常に重要である。
- 表面触媒反応:吸着種は基材表面で化学反応を起こし、多くの場合、表面そのものが触媒となる。これらの反応により、目的の固体膜が形成される。
- 成長部位への表面拡散:反応した化学種は表面を拡散し、膜の核となる特定の成長部位に到達する。
- 膜の核生成と成長:成長部位で、膜は核生成と成長を開始し、基板上に連続層を形成する。
- 副生成物の脱着:最後に、反応中に形成されたガス状の副生成物は表面から脱離し、堆積膜を残して輸送される。
-
CVDの応用:
- CVDは、二酸化ケイ素、窒化ケイ素、各種金属などの薄膜を成膜するために、半導体産業で広く使用されている。また、保護膜や光学膜の製造、さらには複雑なナノ構造の作成にも利用されている。
-
CVDの利点:
- 高品質フィルム:CVDは、均一性、純度、基板への密着性に優れた膜を作ることができる。
- 汎用性:金属、セラミック、ポリマーなど、さまざまな材料を蒸着できる。
- 複雑な形状:CVDは、複雑な形状や入り組んだ形状のコーティングが可能で、様々な用途に適しています。
-
物理蒸着法(PVD)との比較:
- 薄膜の成膜にはCVDとPVDの両方が用いられるが、そのメカニズムは根本的に異なる。PVDは蒸発やスパッタリングのような物理的プロセスに依存するのに対し、CVDは化学反応を伴う。この違いにより、CVDはフィルムの組成や特性を精密に制御する必要がある用途に特に適している。
-
CVDによる重合:
- CVDは、基板上で材料を直接重合させるのにも使用できる。例えば、ポリパラキシリレンを真空チャンバー内でCVD成膜すると、モノマーが基板に接触して重合し、薄いポリマー膜が形成される。
-
環境と安全への配慮:
- CVDプロセスでは、危険な化学物質や高温を使用することが多いため、厳格な安全プロトコルが必要となる。適切な換気、廃棄物管理、個人用保護具は、安全な操業を保証するために不可欠である。
まとめると、化学気相成長プロセスは、高い精度と品質で薄膜を蒸着するための、多用途で強力な技術である。化学反応に依存することで、オーダーメイドの特性を持つ膜を作ることができ、現代の製造や技術に欠かせないものとなっている。このトピックの詳細については 化学蒸着 プロセス。
総括表:
アスペクト | 詳細 |
---|---|
定義 | CVDは、気相での化学反応によって薄膜を堆積させる。 |
主なステップ | 1.気体の輸送 2.吸着 3.表面反応 4.薄膜成長 |
応用分野 | 半導体、保護膜、光学フィルム、ナノ構造体 |
利点 | 高品質フィルム、汎用性、複雑な形状のコーティングが可能。 |
PVDとの比較 | CVDは化学反応を利用するが、PVDは物理的プロセスに依存する。 |
安全性への配慮 | 危険な化学物質や高温の取り扱いが必要です。 |
CVDがお客様の製造工程をどのように向上させるかをご覧ください。 今すぐご連絡ください までご連絡ください!