物理蒸着技術は、化学反応を伴わずに、材料をソースから基板に物理的に移動させることによって、基板上に薄膜やコーティングを作成するために使用される方法である。これらの技術は、機械的、電気機械的、または熱力学的プロセスに依存しており、通常、材料が均一かつ正確に蒸着されるように真空環境を必要とする。最も一般的な物理蒸着法には、蒸着とスパッタリングがあり、それぞれに真空熱蒸着、電子ビーム蒸着、カソードアーク蒸着などのさまざまなサブテクニックがある。これらの方法は、その精度と高品質の薄膜を製造する能力により、エレクトロニクス、光学、製造などの産業で広く使用されています。
キーポイントの説明
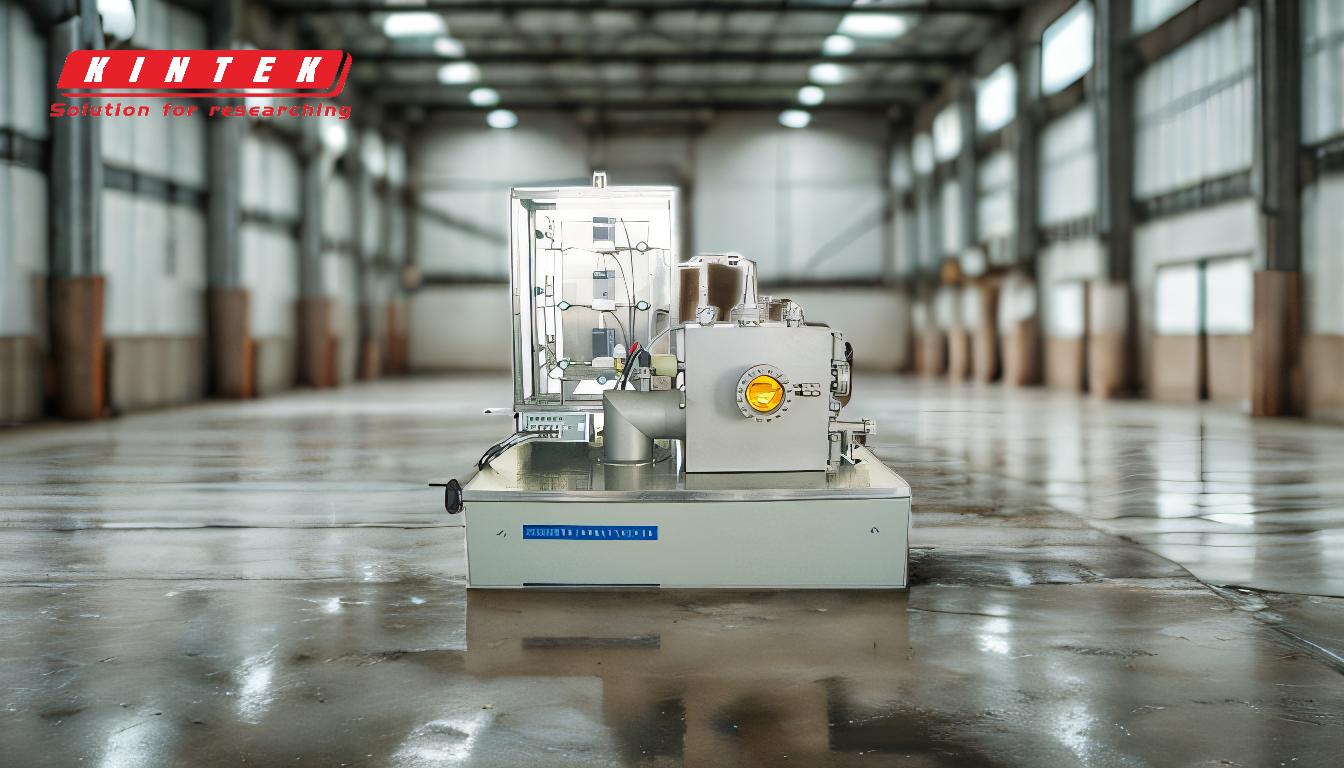
-
物理蒸着技術の定義:
- 物理蒸着法は、機械的、電気機械的、または熱力学的な方法を用いて、材料を供給源から基板に移動させる。
- 化学蒸着とは異なり、物理蒸着は薄膜を形成するための化学反応に依存しない。
- これらの技術は、材料が汚染されることなく均一に蒸着されることを確実にするため、通常真空環境で行われる。
-
物理蒸着法の主な構成要素:
- 真空チャンバー:材料粒子が自由に移動し、基板上に均一に堆積できるような低圧環境を作り出すために不可欠。
- ソース材料:蒸着される材料で、最初は固体または液体の状態であることが多い。
- 基板:薄膜が蒸着される表面で、通常、成膜を容易にするためにソース材料よりも低温になっている。
-
一般的な物理蒸着法:
-
蒸発:
- 蒸発または昇華して気体状態になるまで原料を加熱する。
- その後、気体状の材料は冷却された基板上で凝縮し、薄膜を形成する。
-
サブテクニックには以下が含まれる:
- 真空サーマルエバポレーション:真空中で熱を利用して材料を蒸発させる。
- 電子ビーム蒸発:電子ビームで材料を加熱・蒸発させる。
- レーザービーム蒸発:レーザーを使用して材料をアブレーションし、蒸発させる。
- アーク蒸発:電気アークを使用して材料を蒸発させる。
- 分子線エピタキシー(MBE):結晶層を成長させるために使用される高度に制御された蒸発形態。
- イオンプレーティング蒸発法:蒸着とイオン照射を組み合わせ、膜の密着性と密度を高める。
-
スパッタリング:
- 高エネルギーのイオンまたはプラズマをソース材料(ターゲット)に照射し、ターゲットから原子を放出させる。
- 放出された原子は基板上に堆積し、薄膜を形成する。
- スパッタリングは、半導体や光学コーティングの製造に広く用いられている。
-
蒸発:
-
物理蒸着技術の利点:
- 高精度:非常に薄く均一な膜の成膜が可能で、多くの場合ナノメータースケールである。
- 材料の多様性:金属、セラミックス、半導体を含む幅広い材料に使用可能。
- 管理された環境:真空環境はコンタミネーションを最小限に抑え、蒸着パラメーターの精密な制御を可能にする。
- 接着と密度:イオンプレーティングやスパッタリングなどの技術は、優れた密着性と密度を持つ膜を作ることができる。
-
物理蒸着技術の応用:
- エレクトロニクス:半導体、集積回路、微小電気機械システム(MEMS)の製造における薄膜の成膜に使用される。
- 光学:反射防止コーティング、ミラー、光学フィルターの製造に使用。
- 製造:工具用硬質皮膜、装飾皮膜、耐食性皮膜の製造に応用。
-
化学蒸着技術との比較:
- 物理蒸着 (PVD):物理的プロセスに依存し、化学反応を伴わない。一般的に真空中で行われ、幅広い材料に適している。
- 化学蒸着(CVD):薄膜を形成するための化学反応を伴う。大気圧または真空中で行うことができ、酸化物や窒化物のような複雑な材料の蒸着によく用いられる。
-
物理蒸着技術の例:
- アーク-PVD (カソードアーク蒸着):電気アークを使用してカソードから材料を蒸発させ、基板上に堆積させる。
- パルスレーザー蒸着(PLD):高出力レーザーを使用してターゲットから材料をアブレーションし、基板上に堆積させる。
- スパッタリング:磁場を利用してスパッタリングプロセスの効率を高めるマグネトロンスパッタリングなどの技術が含まれる。
- 熱蒸発:特に金属や単純な化合物に対して、最もシンプルで広く使われている物理蒸着法のひとつ。
要約すると、物理蒸着法は様々な産業において高品質の薄膜を作るために不可欠な技術である。蒸着プロセスを正確に制御でき、優れた特性を持つ膜を作ることができるため、多くの用途で好まれている。
総括表
アスペクト | 詳細 |
---|---|
定義 | 化学反応なしに物質を物理的に移動させる技術。 |
主な構成要素 | 真空チャンバー、ソース材料、基板。 |
一般的な方法 | 蒸着(熱、電子ビーム、レーザー)およびスパッタリング。 |
利点 | 高精度、材料の多様性、管理された環境、強力な接着力。 |
用途 | エレクトロニクス(半導体)、光学(ミラー)、製造(コーティング)。 |
CVDとの比較 | PVD:化学反応なし、真空ベース。CVD:化学反応、大気圧または真空。 |
お客様の用途に合った高品質の薄膜にご興味がおありですか? 当社の専門家に今すぐご連絡ください までご連絡ください!