スパッタリングと化学的気相成長法(CVD)は、さまざまな産業で使用されている2つの異なる薄膜蒸着技術であり、それぞれに独自のプロセス、利点、用途がある。スパッタリングは物理的気相成長法(PVD)で、高エネルギーイオンを用いて固体ターゲット材料から原子を放出させ、基板上に堆積させる。このプロセスは熱に依存しないため、プラスチックや有機物のような温度に敏感な材料に適している。一方、CVDは化学的なプロセスで、ガス状の前駆体が基板上で反応し、固体の薄膜を形成する。より高い温度で作動し、視線を必要とせず、複雑な形状でも均一なコーティングが可能です。スパッタリングは膜特性の精密な制御が必要な用途に最適ですが、CVDは半導体や光学用途の高品質で均一な膜の形成に優れています。
ポイントを解説
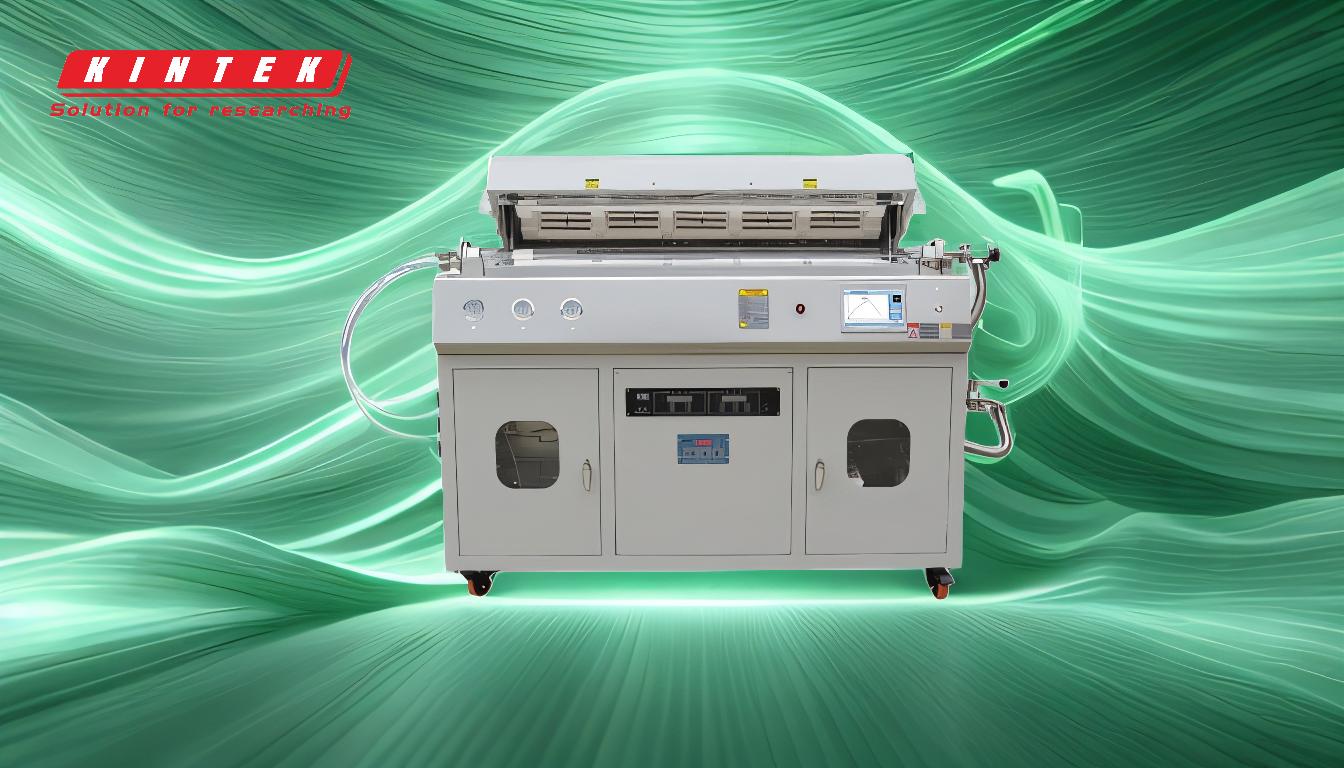
-
プロセスのメカニズム:
- スパッタリング:高エネルギーイオンをターゲット材料に照射し、原子を移動させて基板上に堆積させる物理的プロセス。この方法は熱に依存しないため、温度に敏感な材料に適している。
- CVD:ガス状の前駆体が基板表面で反応し、固体の薄膜を形成する化学プロセス。このプロセスは通常、高温を必要とし、化学反応を伴う。
-
必要な温度:
- スパッタリング:低温で動作するため、プラスチック、有機物、ガラスなどのコーティングに最適。
- CVD:より高い温度を必要とするため、温度に敏感な材料への使用は制限されるが、高品質で均一な膜の形成が可能。
-
蒸着速度:
- スパッタリング:一般に、熱蒸発法に比べて成膜速度は低いが、膜特性を精密に制御できる。
- CVD:特に熱CVDのようなプロセスでは、より高い成膜速度を達成できるが、化学反応を伴うため、運転時間が長くなる可能性がある。
-
視線と均一性:
- スパッタリング:ターゲットと基板の間に視線を必要とするため、複雑な形状を均一にコーティングする能力が制限されることがある。
- CVD:視線を必要としないため、複雑な形状や複数の部品に同時に均一なコーティングが可能。
-
用途:
- スパッタリング:光学コーティング、装飾仕上げ、エレクトロニクスの機能層などによく使われる。
- CVD:集積回路用の多結晶シリコン膜の製造など、半導体製造や光学・機械用途の高性能コーティングの製造に広く使用されている。
-
材料の利用と効率:
- スパッタリング:特に電子ビーム物理蒸着(EBPVD)のような技術では、高い材料利用効率を提供する。
- CVD:効率的な反面、腐食性の副生成物が発生したり、フィルムに不純物が残ったりすることがあり、慎重な取り扱いと後処理が必要。
-
利点と限界:
-
スパッタリング:
- 利点低温プロセス、フィルム特性の正確な制御、温度に敏感な材料に適している。
- 制限事項成膜速度が低い、見通しが必要、単純な形状に限定される。
-
CVD:
- 利点複雑な形状への均一なコーティング、高品質のフィルム、視線を必要としない。
- 制限事項より高い温度、腐食性副生成物の可能性、より長い処理時間。
-
スパッタリング:
これらの重要な違いを理解することで、装置や消耗品の購入者は、特定のアプリケーションのニーズに最も適した成膜方法を、十分な情報を得た上で決定することができる。
要約表
側面 | スパッタリング | CVD |
---|---|---|
プロセスメカニズム | 物理蒸着法、熱は不要 | 化学プロセス、高温が必要 |
温度 | 低め、デリケートな素材に適している | 高い、デリケートな材料での使用は制限される |
蒸着速度 | フィルム特性をより低く、正確に制御 | 高いが、運転時間が長い |
視線 | 必要、複雑な形状の制限 | 不要、複雑な形状を均一にコーティング |
用途 | 光学コーティング, エレクトロニクス, 装飾 | 半導体, 光学, メカニカルコーティング |
材料効率 | 特にEBPVDでは高い利用率 | 効率的だが、腐食性の副生成物が発生する可能性あり |
利点 | 低温、精密制御 | 均一なコーティング、高品質のフィルム |
制限事項 | レートが低い、見通しが必要 | 高温、不純物の可能性 |
適切な薄膜蒸着法の選択にお困りですか? 当社の専門家に今すぐご連絡ください にお問い合わせください!